Használati útmutató Generac QT08054GVAX
Generac
nincs kategorizálva
QT08054GVAX
Olvassa el alább 📖 a magyar nyelvű használati útmutatót Generac QT08054GVAX (120 oldal) a nincs kategorizálva kategóriában. Ezt az útmutatót 5 ember találta hasznosnak és 2 felhasználó értékelte átlagosan 4.5 csillagra
Oldal 1/120
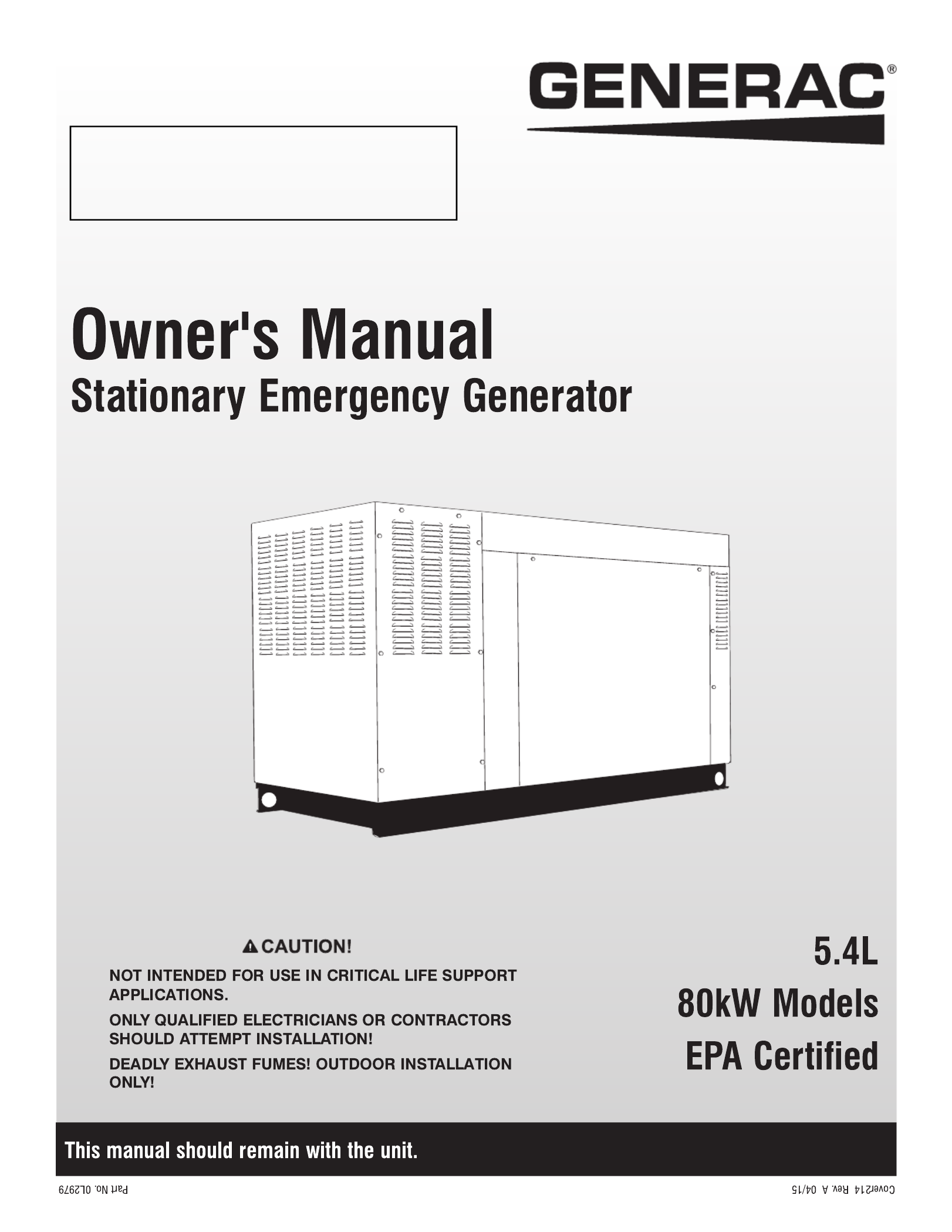
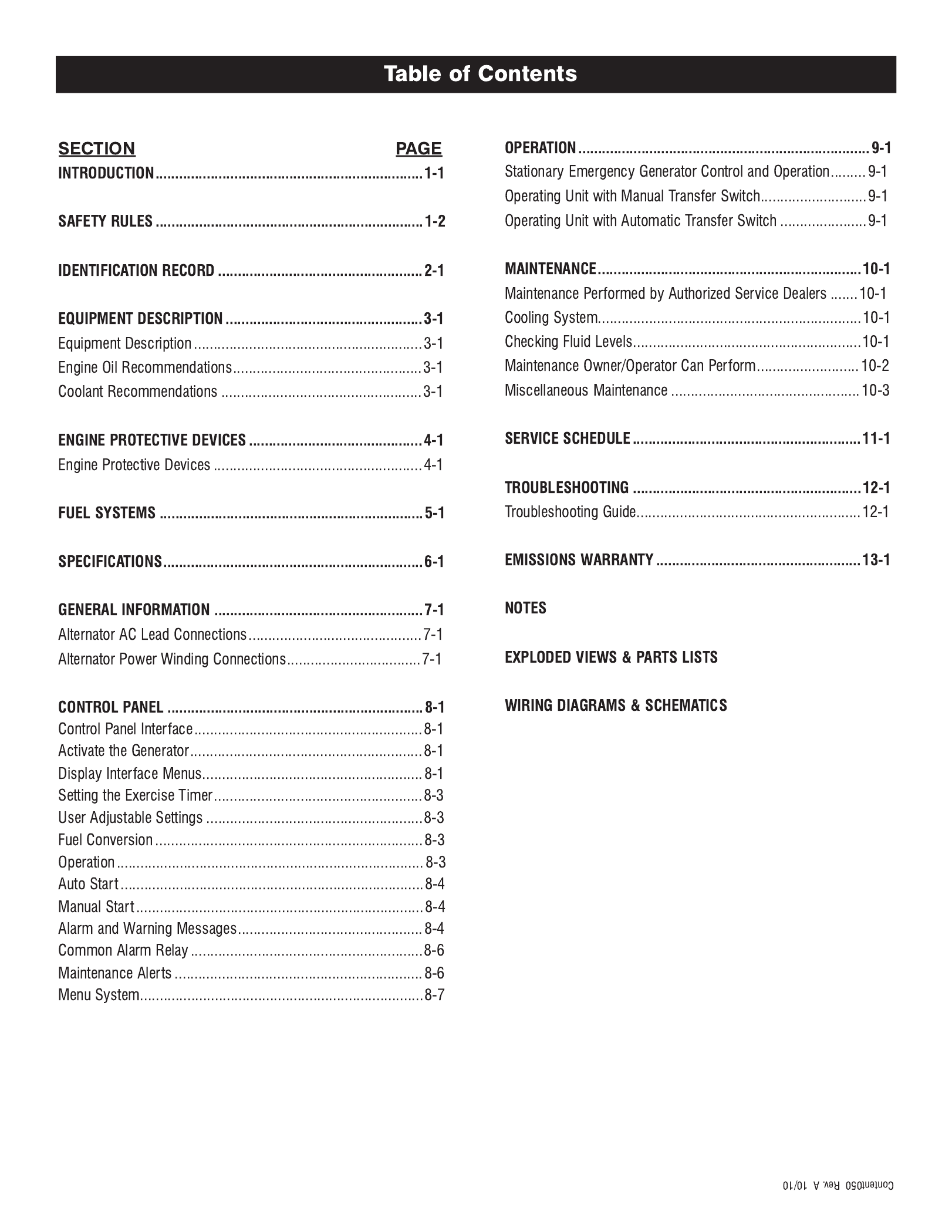
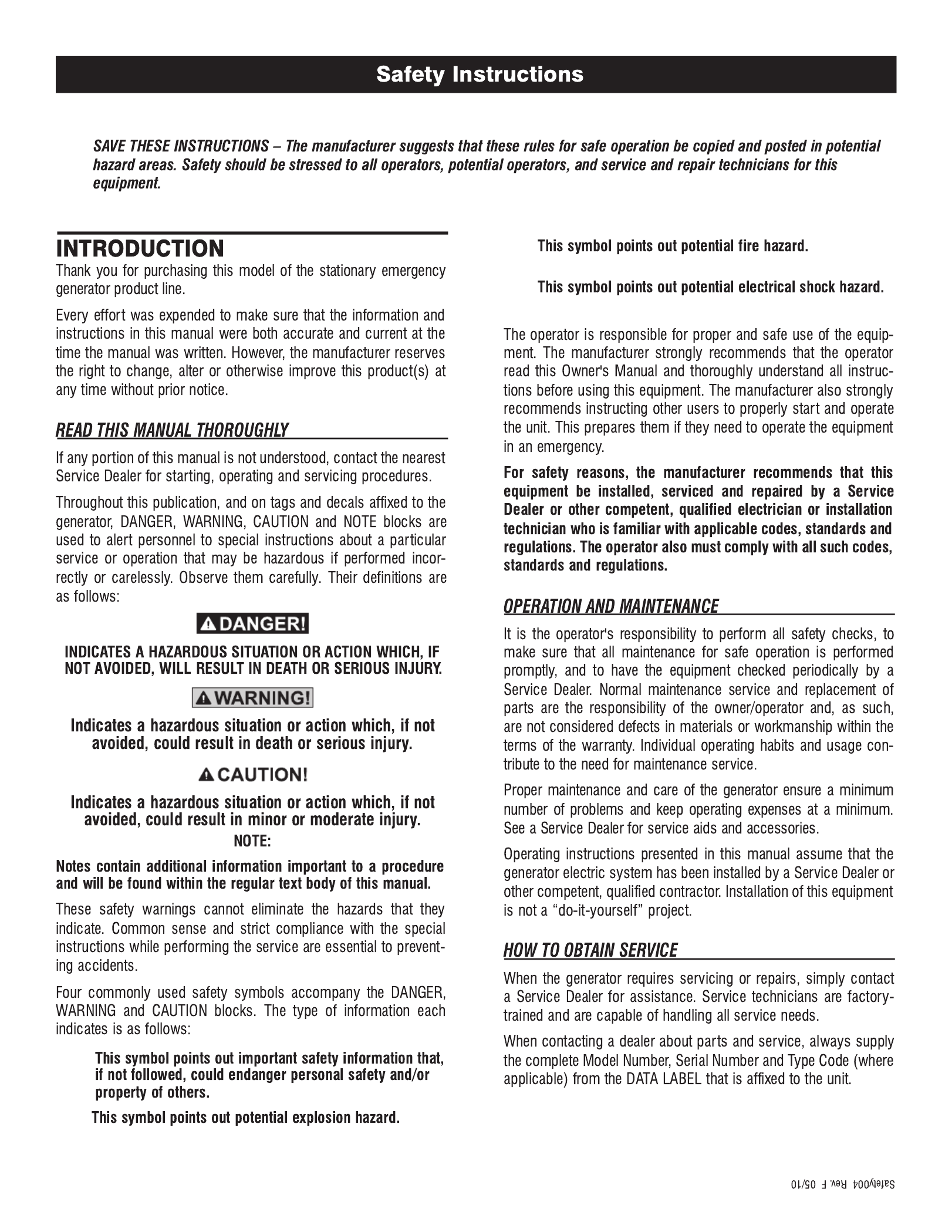
n
1-1
n
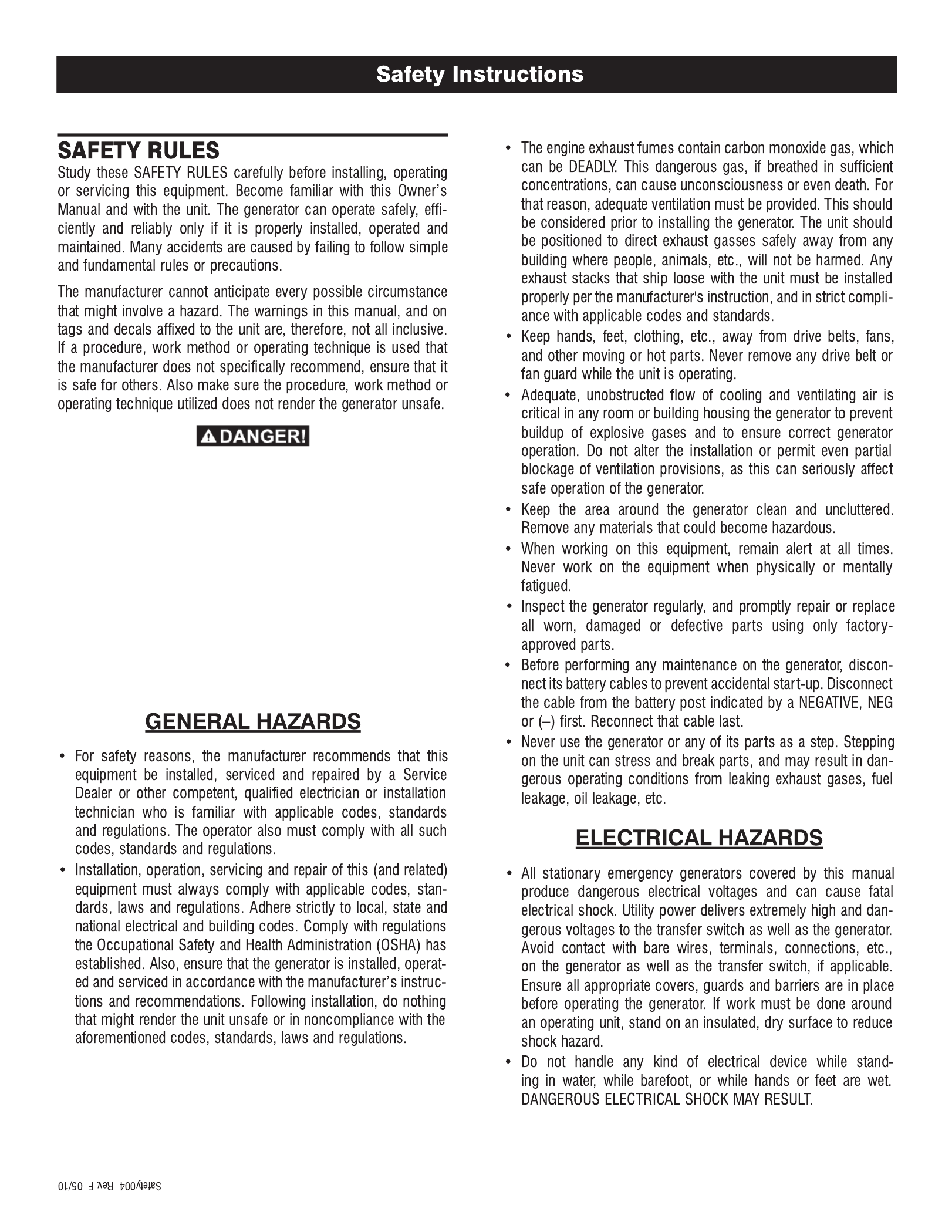
n
Despite the safe design of this generator,
operating this equipment imprudently, neglect-
ing its maintenance or being careless can cause
possible injury or death. Permit only respon-
sible and capable persons to install, operate or
maintain this equipment.
Potentially lethal voltages are generated by
these machines. Ensure all steps are taken to
render the machine safe before attempting to
work on the generator.
n
Parts of the generator are rotating and/or hot
during operation. Exercise care near running
generators.
1-2
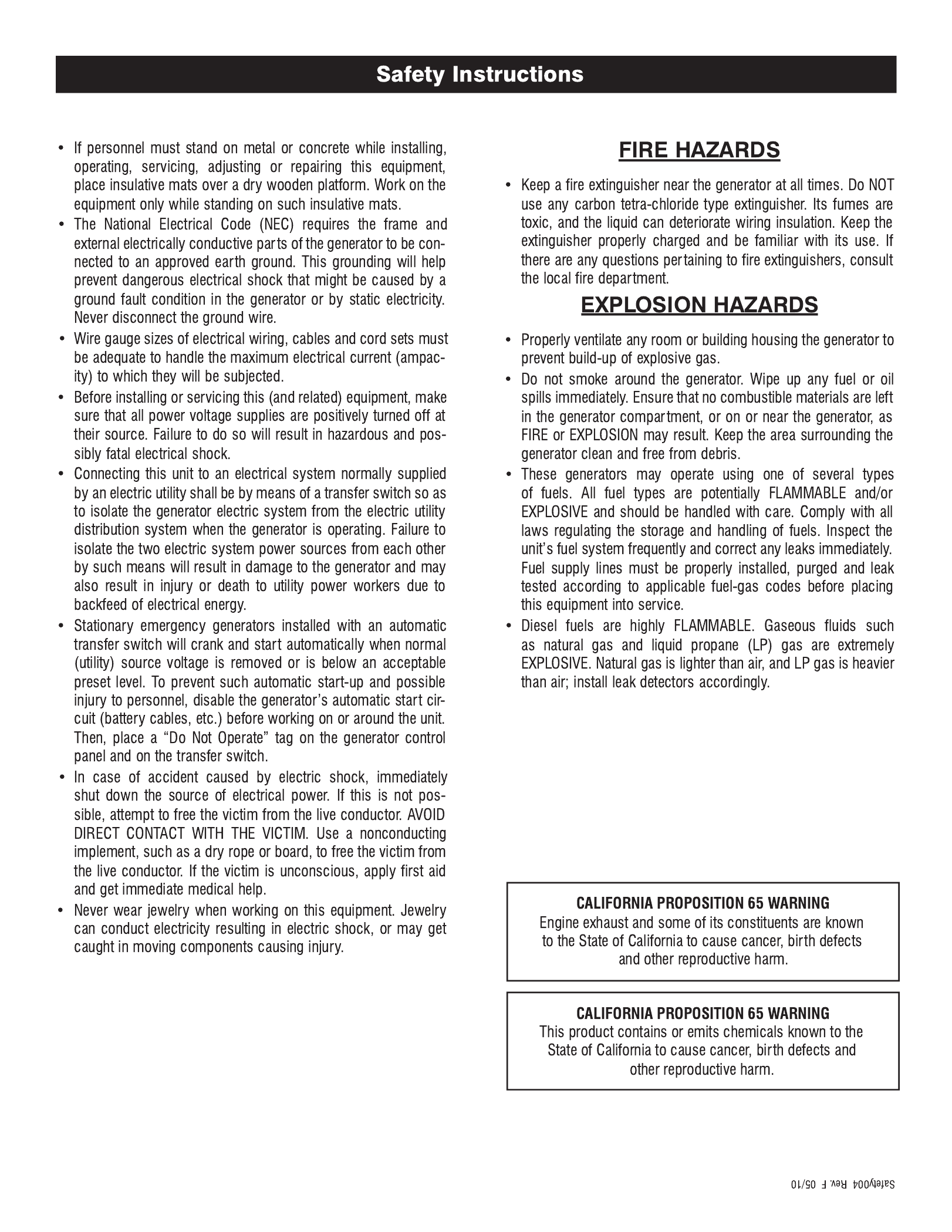
1-3
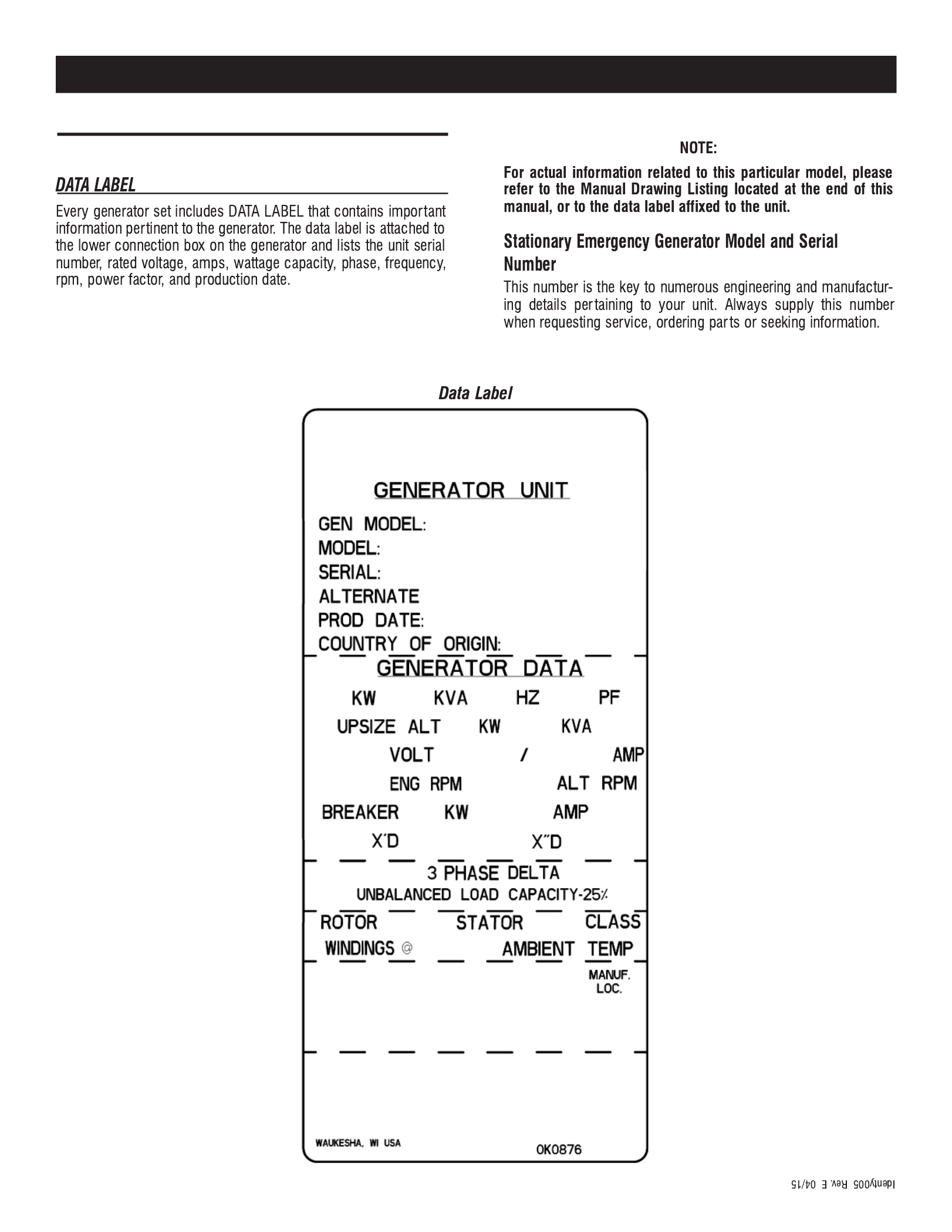
IDENTIFICATION RECORD
2-1
General Information
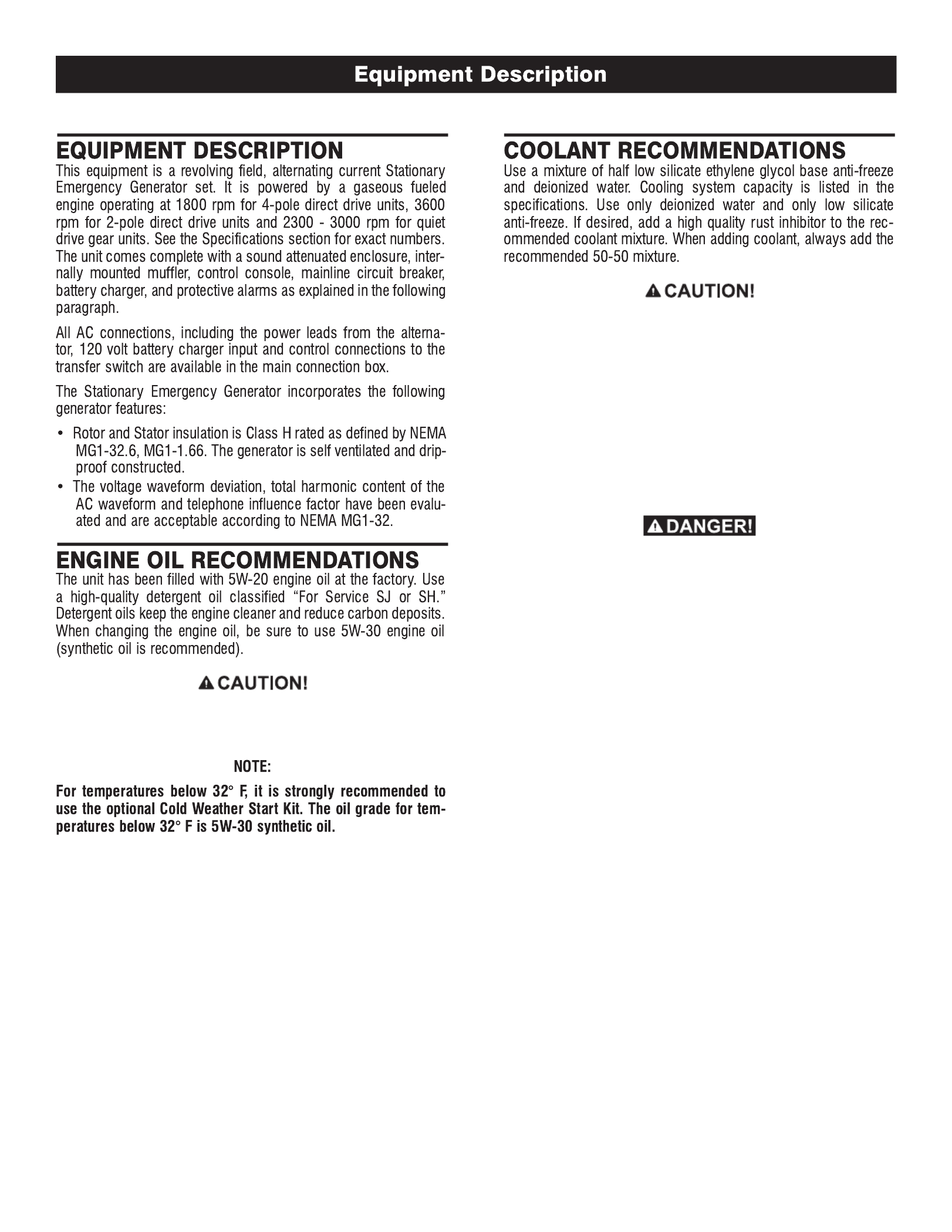
Any attempt to crank or start the engine before
it has been properly serviced with the recom-
mended oil may result in an engine failure.
Do not use any chromate base rust inhibitor
with ethylene glycol base anti-freeze or chro-
mium hydroxide (“green slime”) forms and will
cause overheating. Engines that have been
operated with a chromate base rust inhibitor
must be chemically cleaned before adding eth-
ylene glycol base anti-freeze. Using any high
silicate anti-freeze boosters or additives will
also cause overheating. The manufacturer also
recommends that any soluble oil inhibitor is
NOT used for this equipment.
Do not remove the radiator pressure cap while
the engine is hot or serious burns from boiling
liquid or steam could result.
Ethylene glycol base antifreeze is poisonous.
Do not use mouth to siphon coolant from the
radiator, recovery bottle or any container. Wash
hands thoroughly after handling. Never store
used antifreeze in an open container because
animals are attracted to the smell and taste of
antifreeze even though it is poisonous to them.
3-1
Equip010 Rev. D 07/11
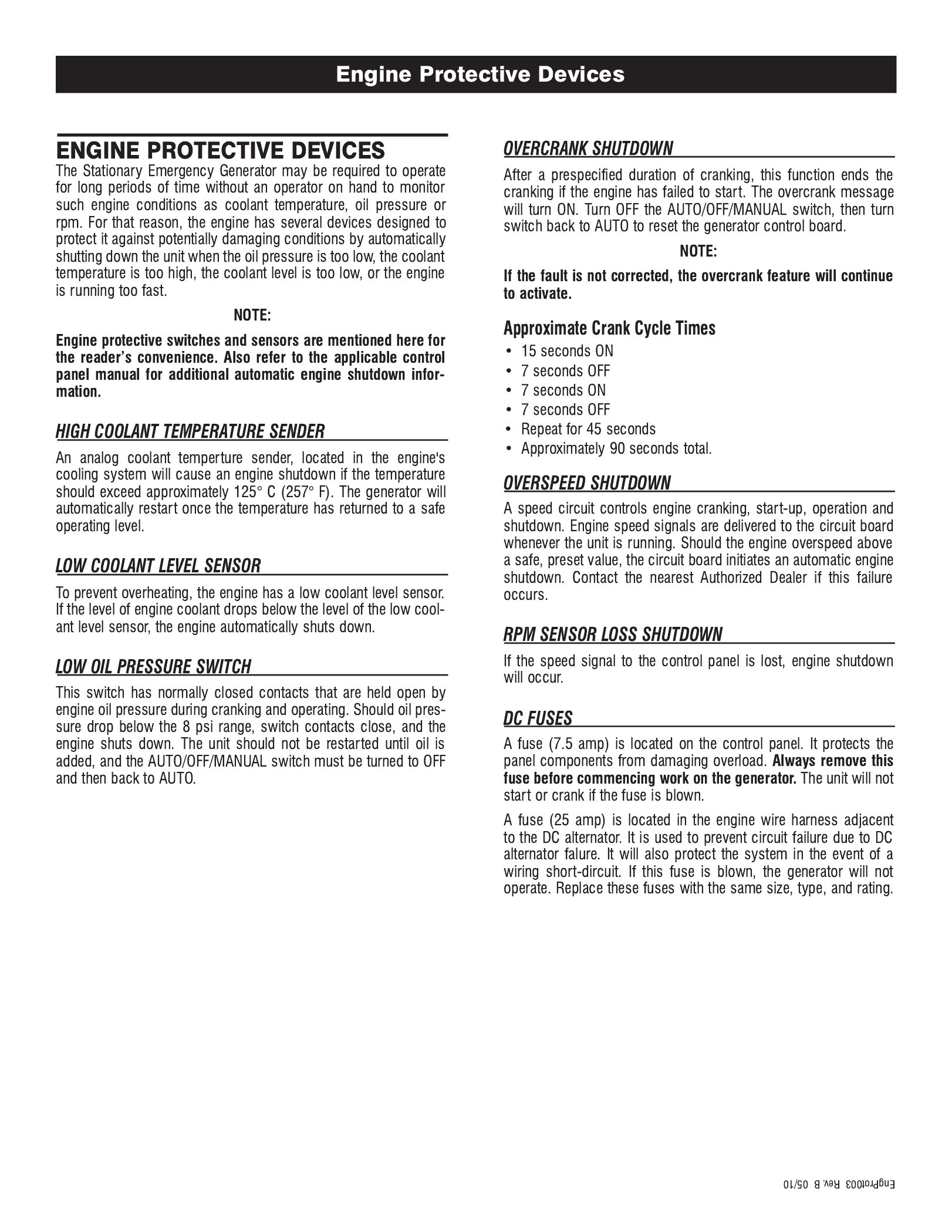
4-1
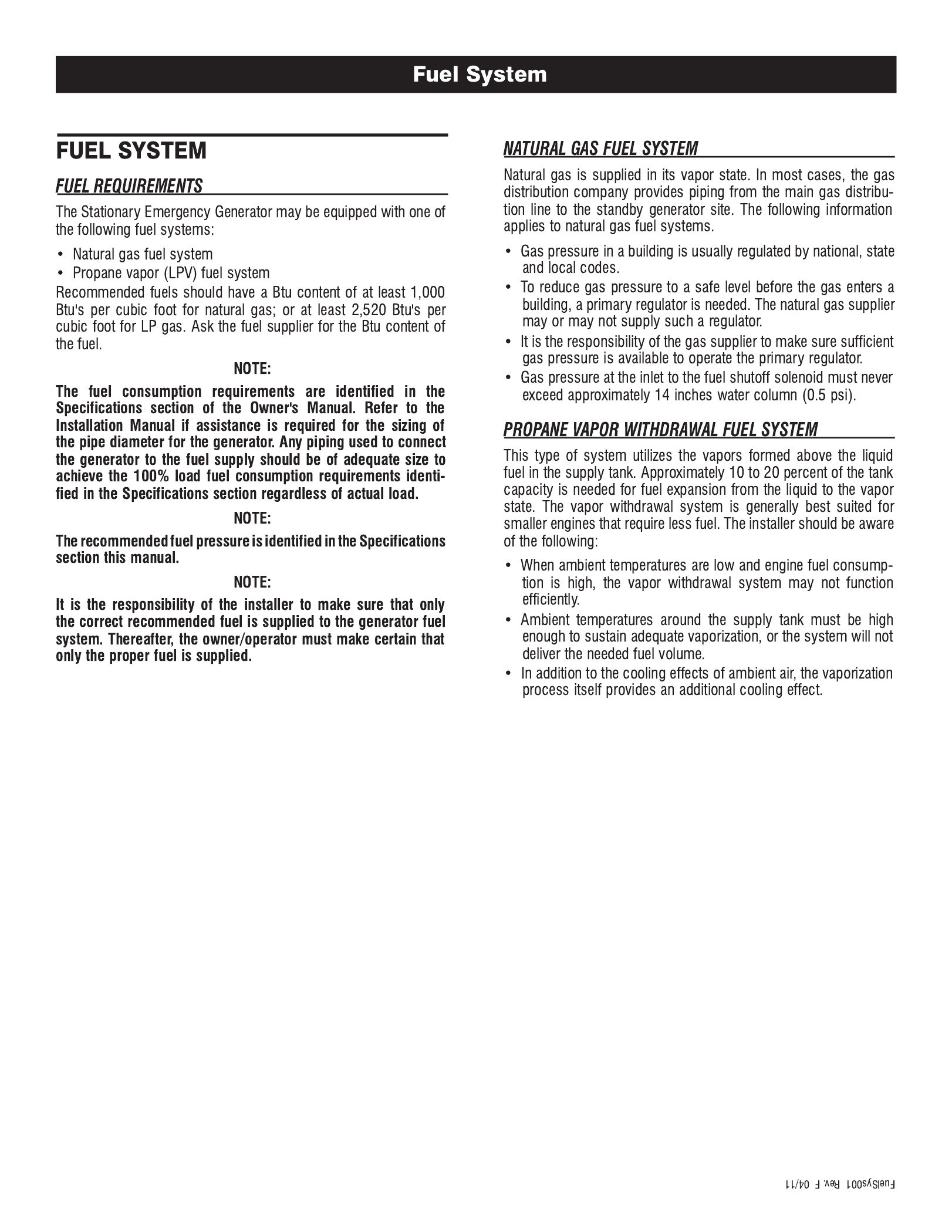
5-1
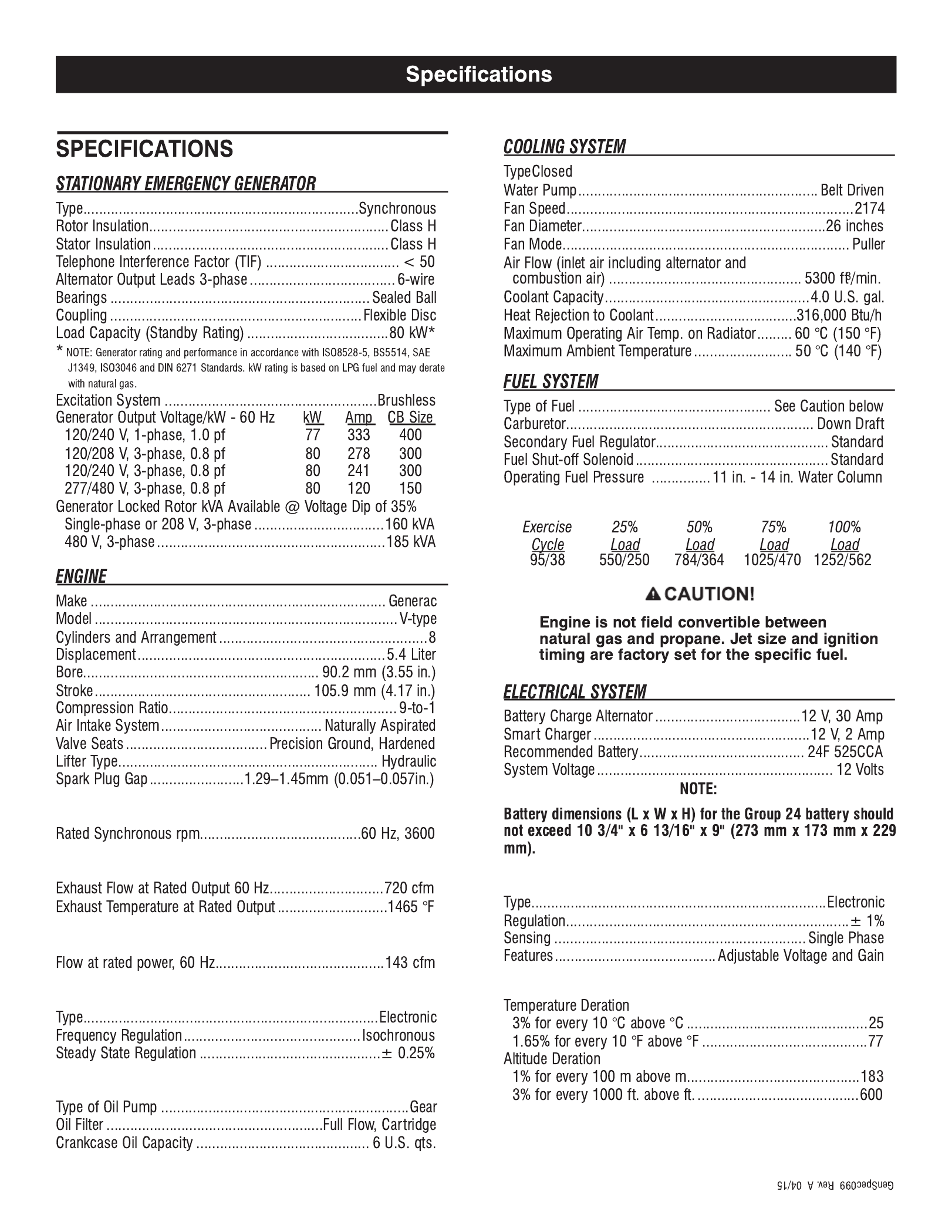
Engine Parameters
Exhaust System
Combustion Air Requirements (Natural Gas)
Governor
Engine Lubrication System
Fuel Consumption - ft3/hr (Natural Gas/LPV)
Voltage Regulator
Power Adjustment for Ambient Conditions
Controller Nexus ..................................................................
6-1

6-2
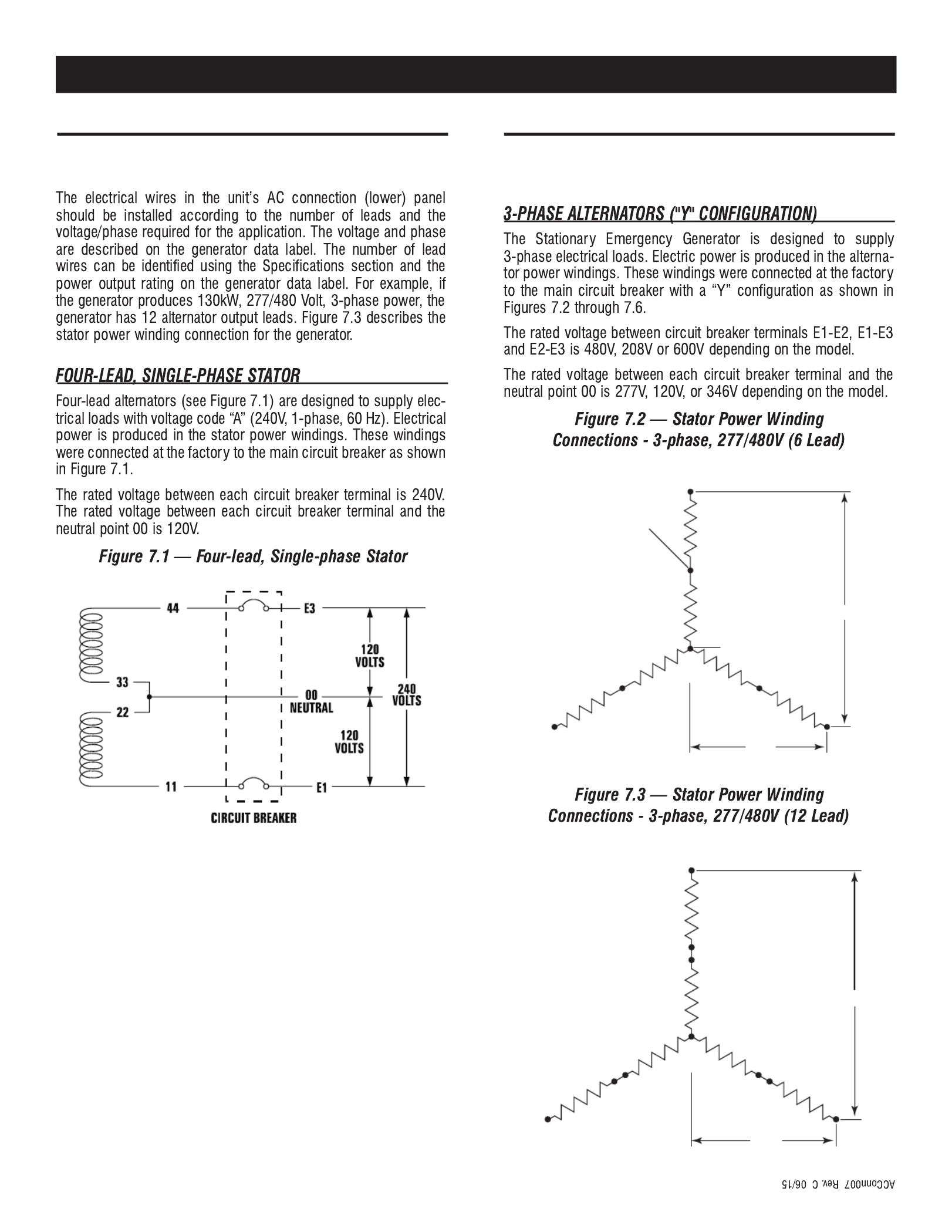
ALTERNATOR AC LEAD
CONNECTIONS
ALTERNATOR POWER WINDING
CONNECTIONS
E1
S1
S6
S5
S4
S2
E2
S3
E3 L - N
L - L
INTERNAL
CONNECTIONS
00 (NEUTRAL)
E1
S1
S4
S7
S12
S11
S10
S8
S5
S2
E2
S9
S6
S3
E3 L - N
L - L
7-1
General Information
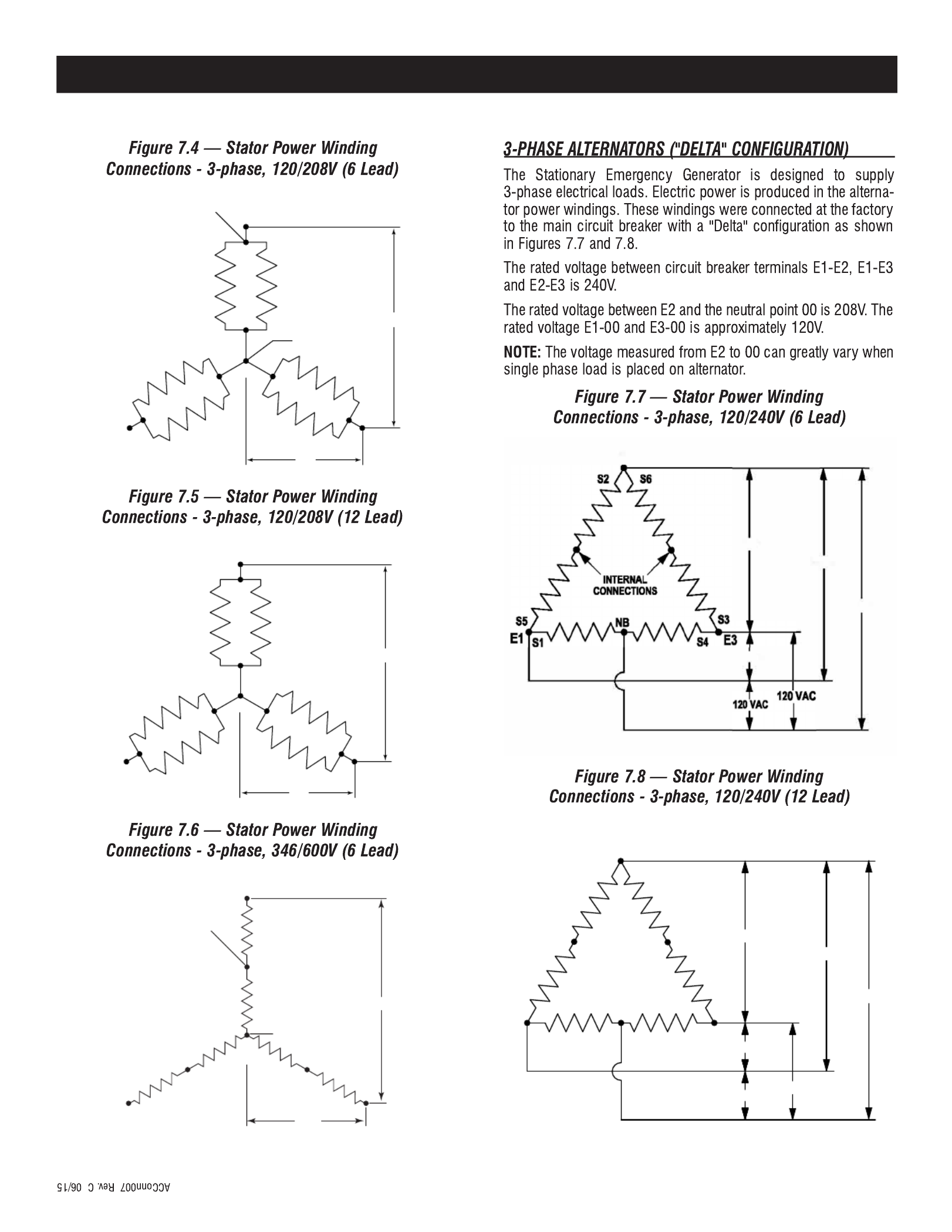
E3 E2
00 (NEUTRAL)
INTERNAL CONNECTIONS E1
L-L
L-N
S1 S1
S4 S4
S6
S6
S3
S3
S5
S5 S2
S2
E3 E2
E1
L-L
L-N
S7 S1
S10 S4
S12
S6
S9
S3
S5
S11 S2
S8
E1
S1
S6
S5
S4
S2
E2
S3
E3 L - N
L - L
INTERNAL
CONNECTIONS
00 (NEUTRAL)
E2
0VAC
2VAC
208C
240C
240 VAC
120 VAC 120 VAC
240 VAC
240 VAC
S2 S12
S11
S1
NB
S10
S3
E1 E3
E2
S5
S8
S9
S6
208 VAC
7-2
General Information
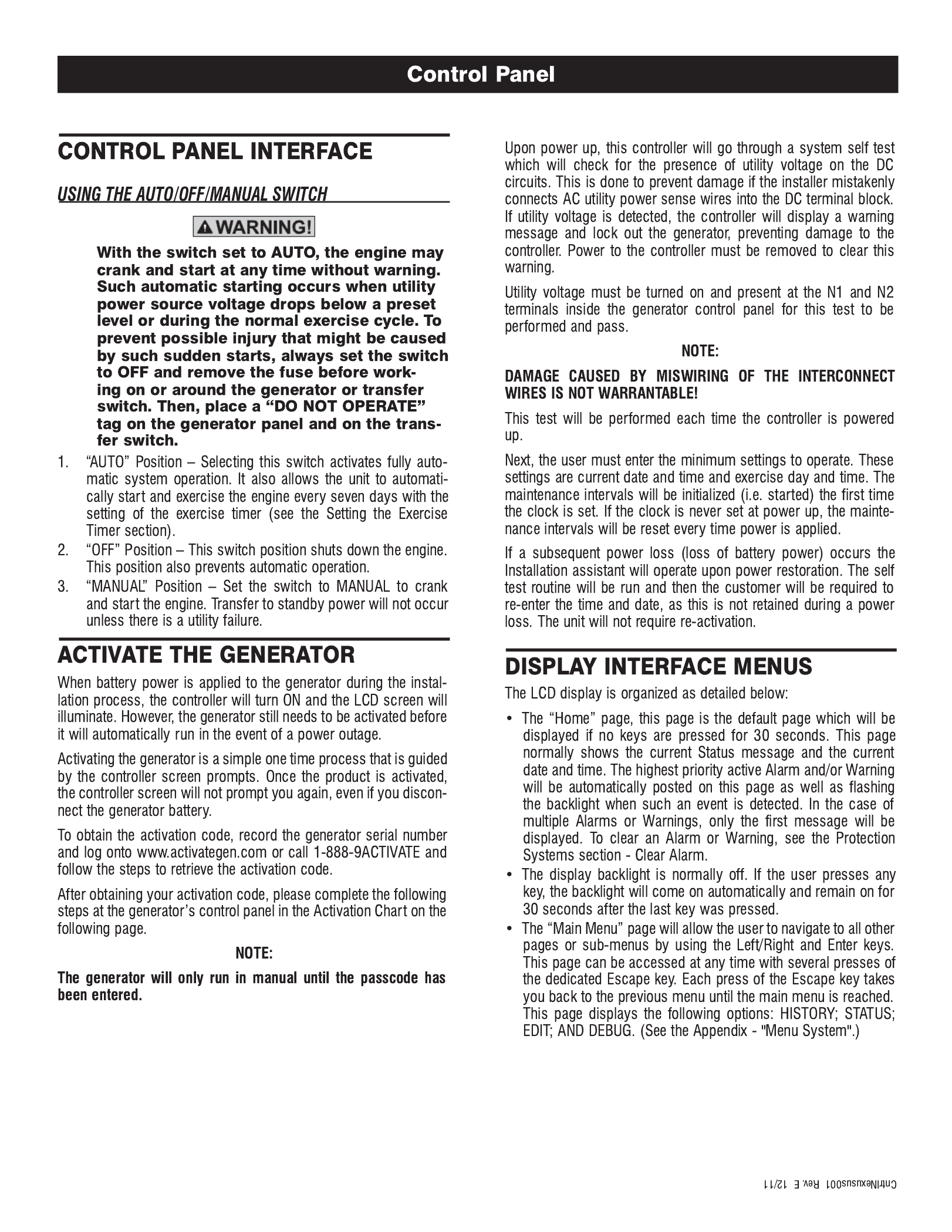
8-1
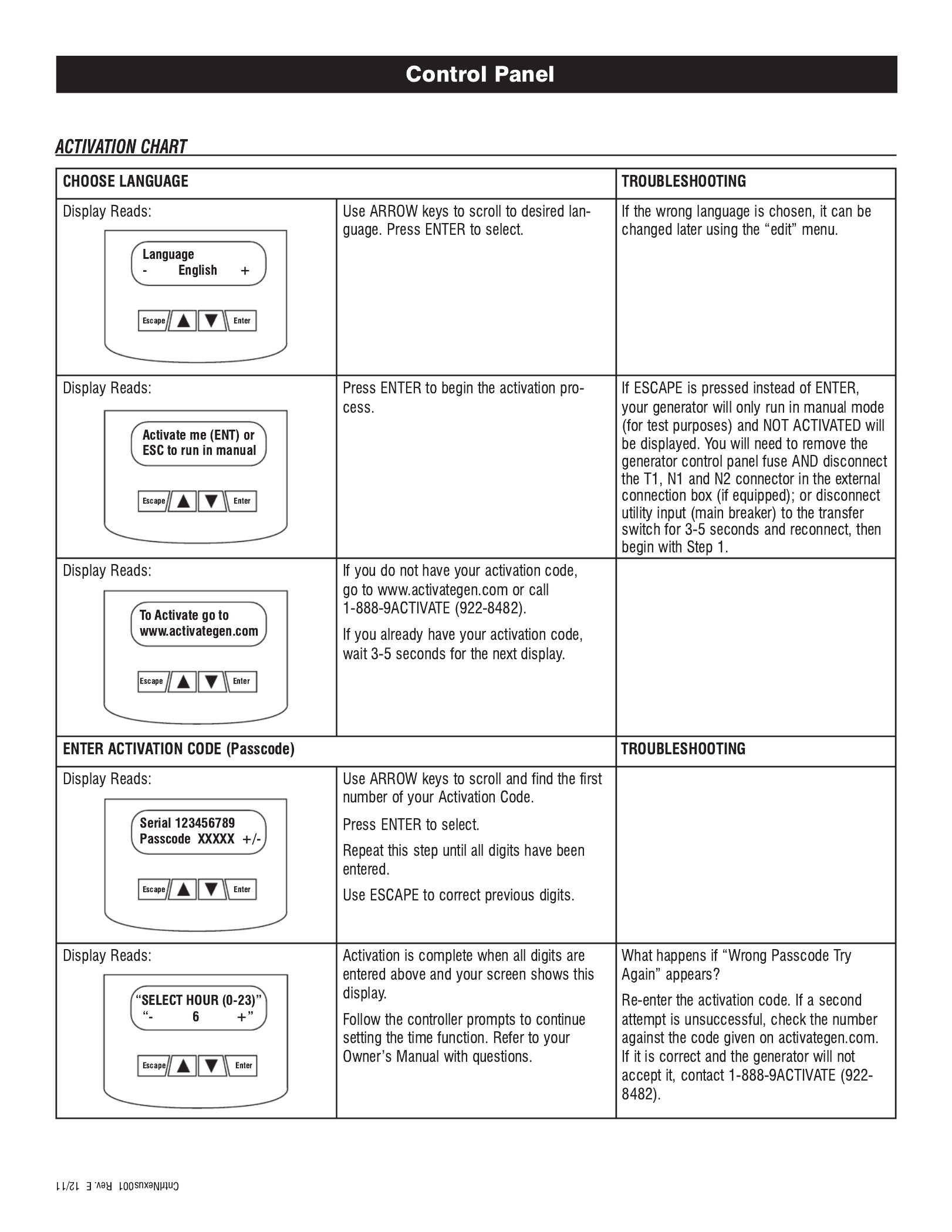
8-2
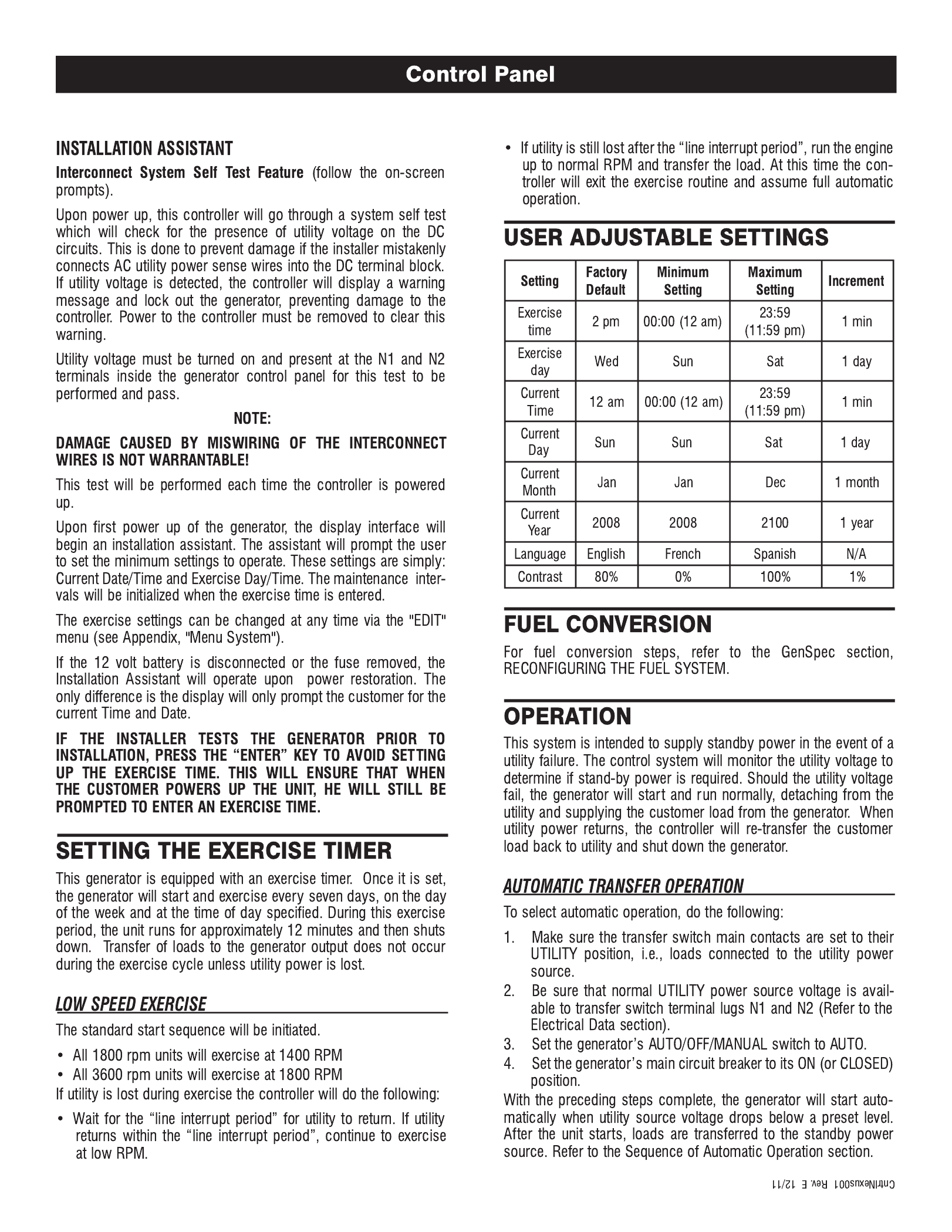
8-3
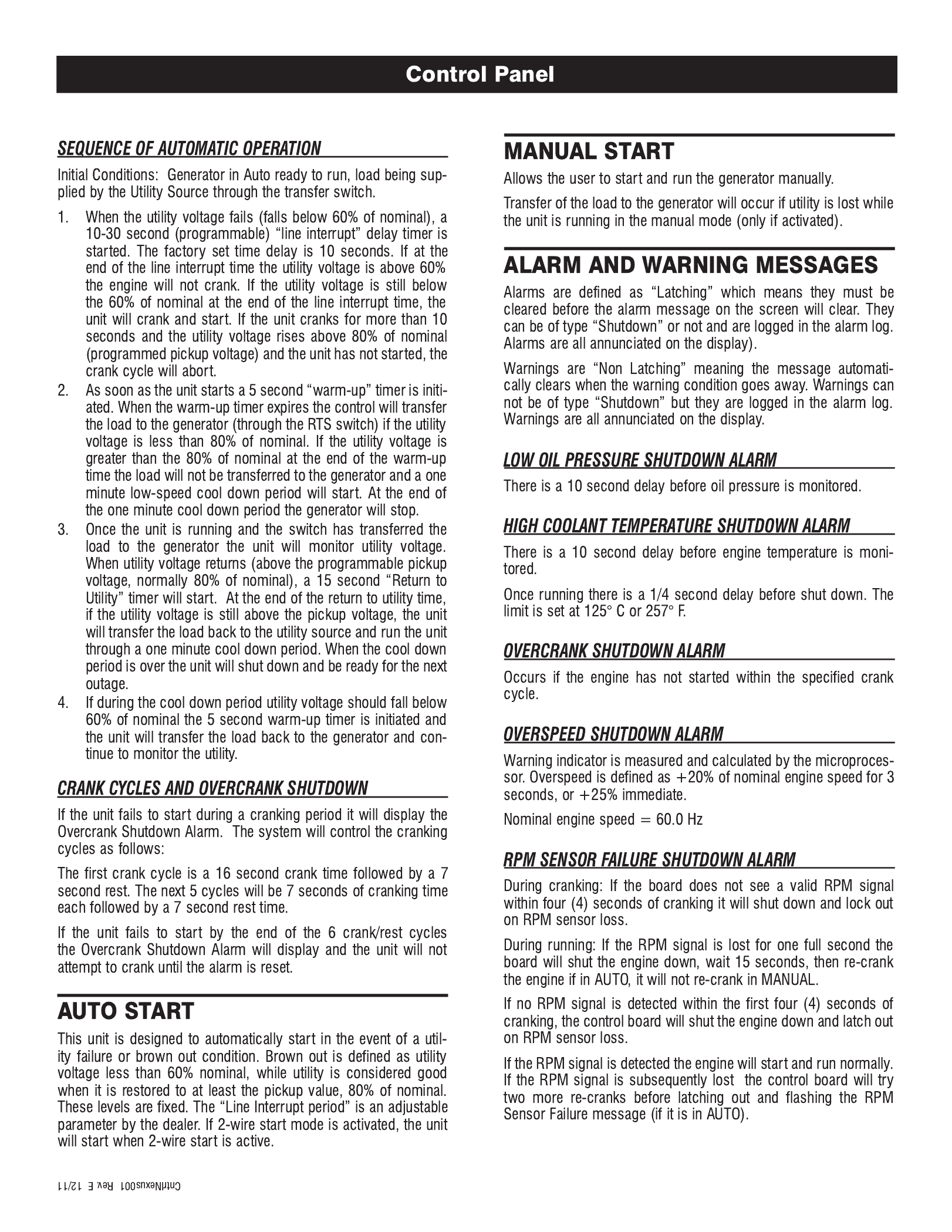
8-4
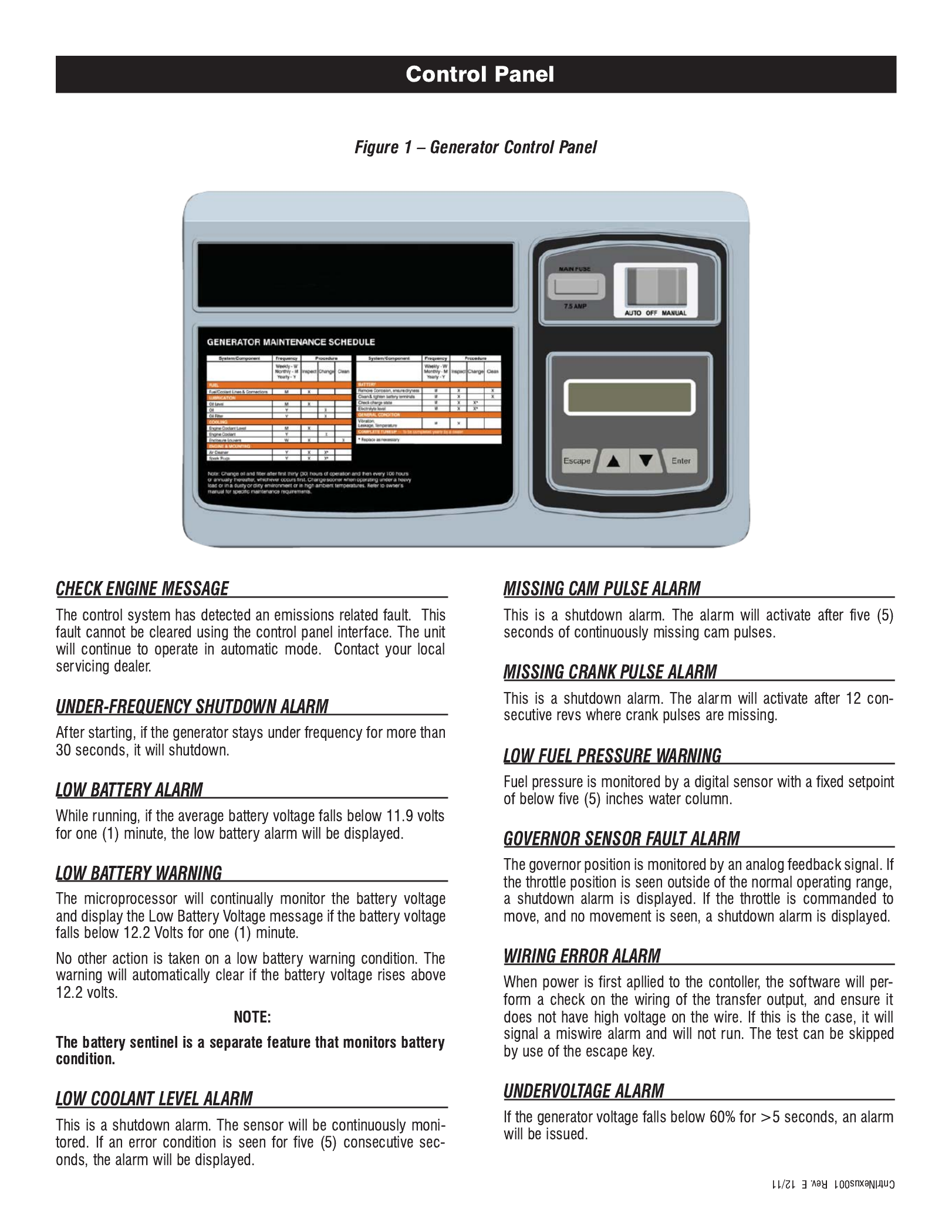
8-5
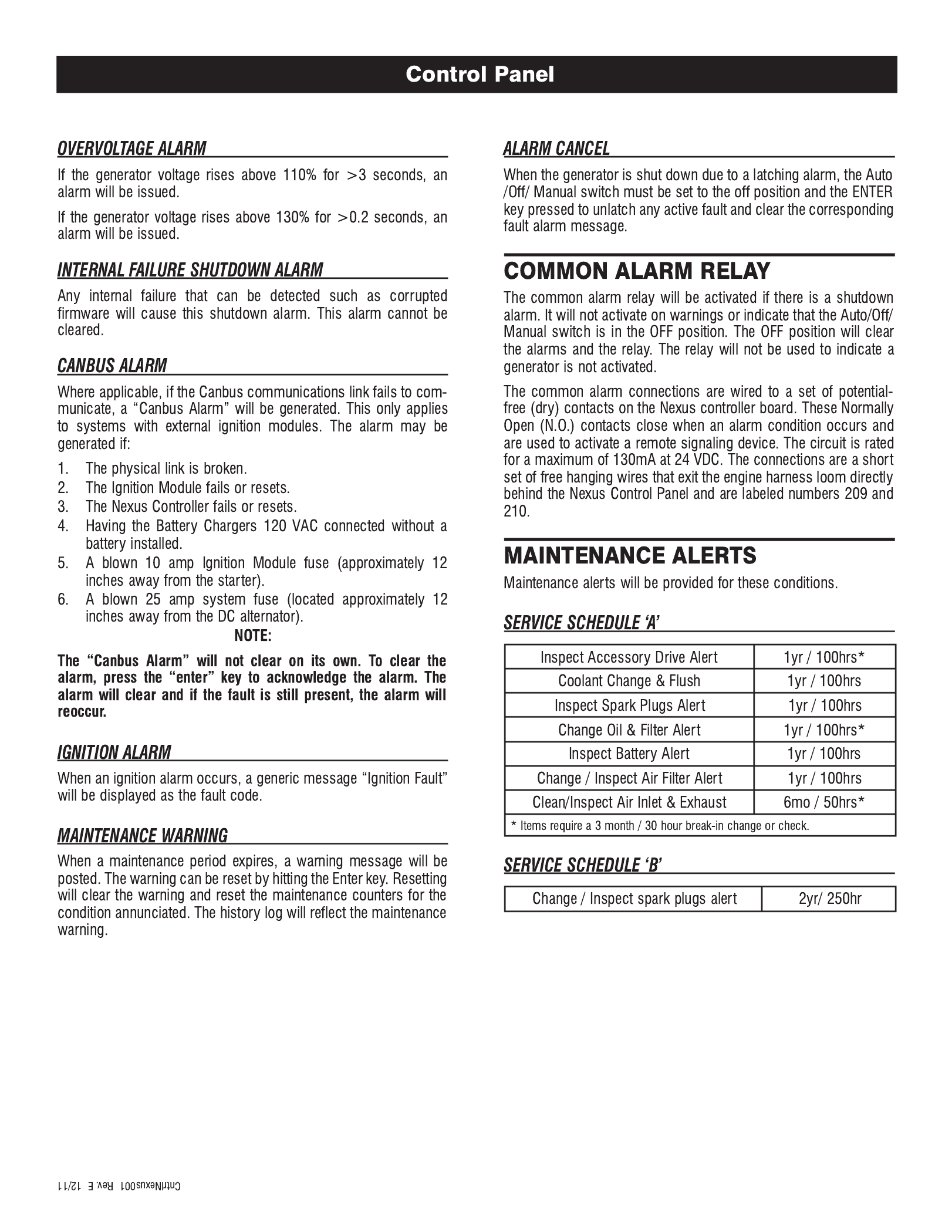
8-6
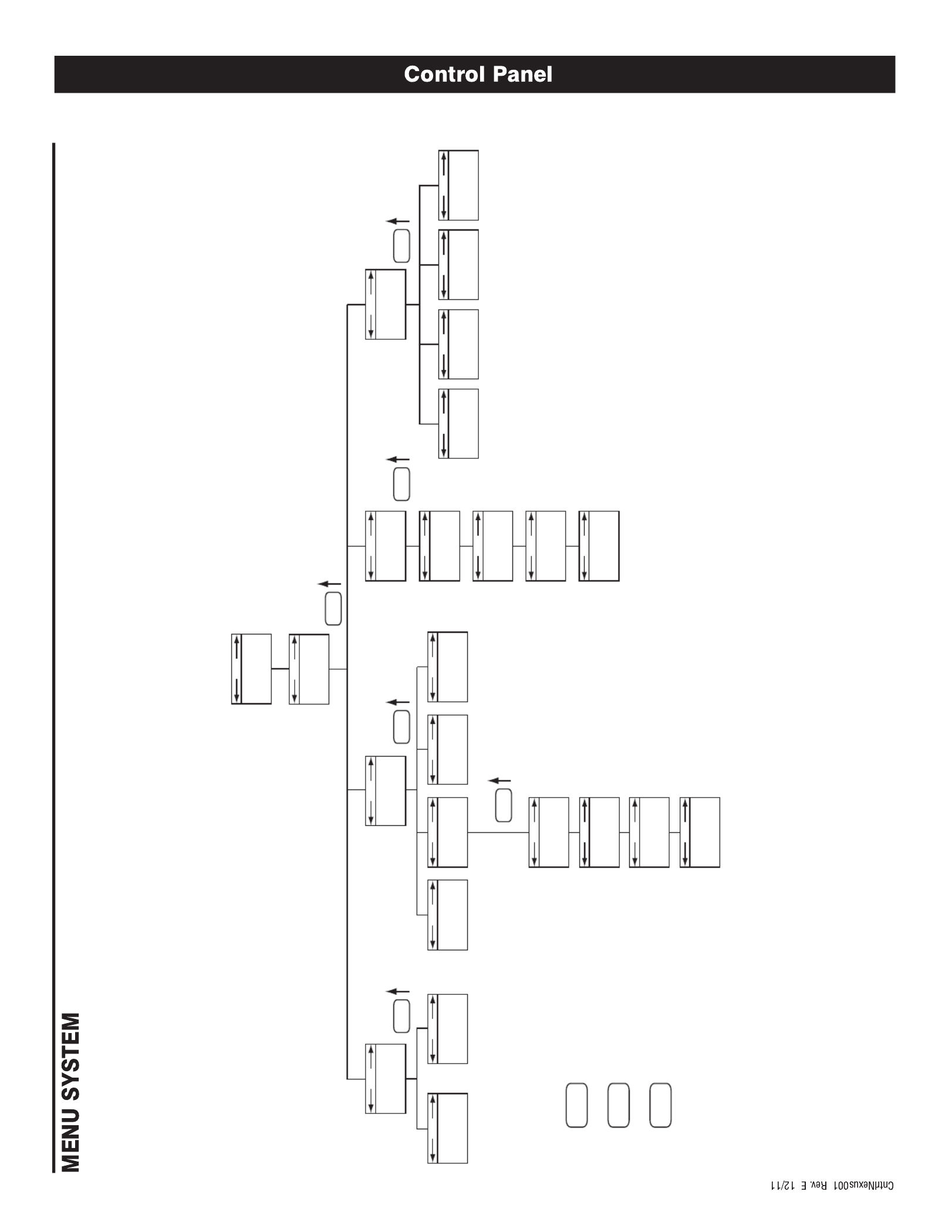
8-7
ACTIVATION
RUN LOGALARM LOG
HISTORY STATUS
COMMANDSTATE VERSIONSDISPLAY
GENERATOR
FREQUENCY
ENGINE
HOURS
ENGINE
RPM
BATTERY
VOLTAGE
DEBUG
INPUTS OUTPUTS DISPLAYS
EDIT
LANGUAGE
TIME/DATE
EXERCISE
TIME/SPEED
ESC Press the “ESCAPE” key
to jump back up through
the menu levels.
+ / - Use the “+/-” key
to navigate through
the menu.
ENTER Use the “ENTER” key
to select items or
enter data.
ESC
ESC
ESC
ESC
ESC ESC
RESET
MAINTENANCE
QT TEST
MAIN MENU
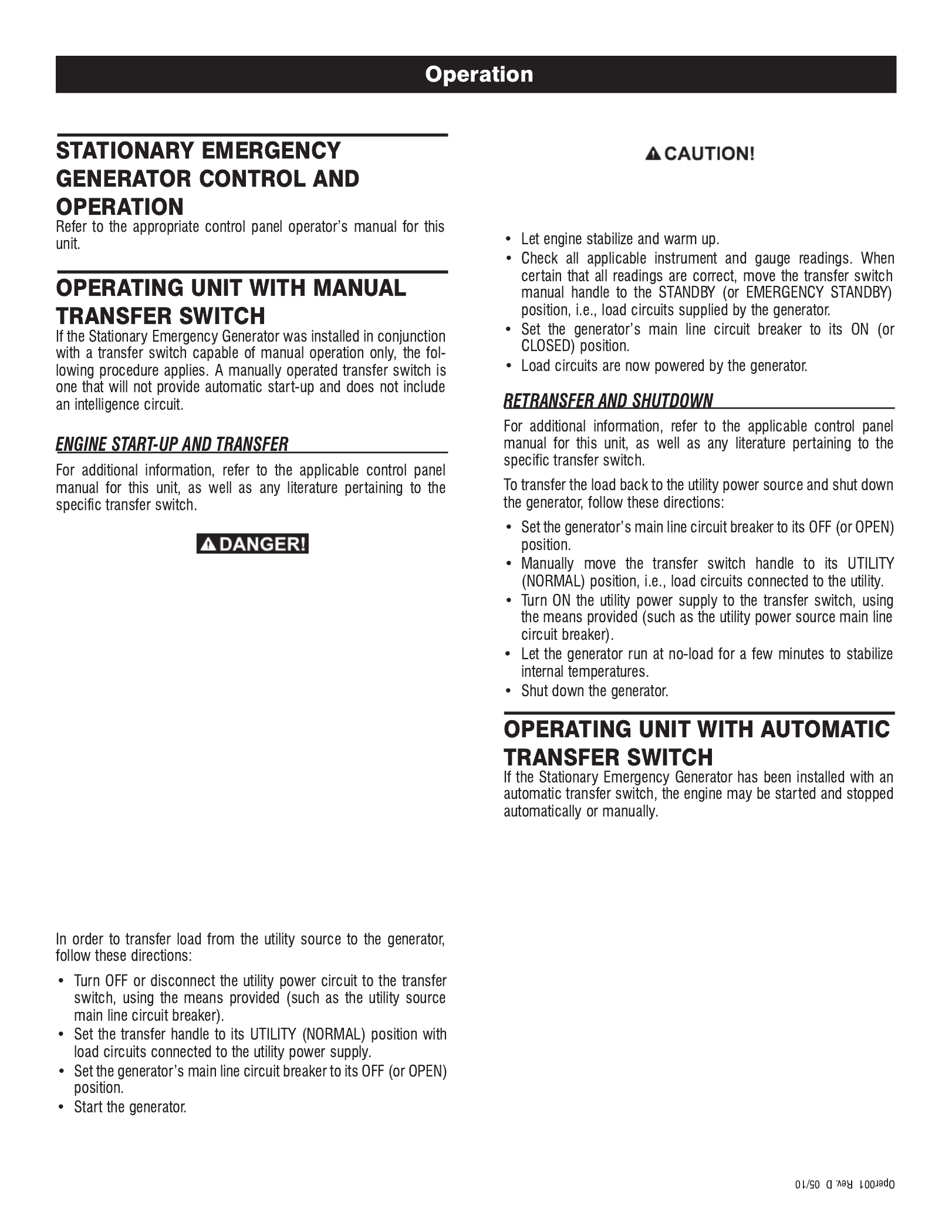
n
The Maintenance Disconnect Switch and the
AUTO/OFF/MANUAL switches (if so equipped)
must be set properly, or the generator will
crank and start as soon as the utility power to
the transfer switch is turned off. Refer to appli-
cable control panel and transfer switch manuals
for more information.
n
Do not proceed until certain that utility source
voltage is available to the transfer switch and
the transfer switch main contacts are set to
UTILITY.
Do not attempt manual operation until all
power supplies to the transfer switch have been
positively turned off, or extremely dangerous -
possibly lethal - electrical shock will result.
Transfer switch enclosure doors should be kept
closed and locked. Only authorized personnel
should be allowed access to the transfer switch
interior. Extremely high and dangerous voltages
are present in the transfer switch.
n Do not crank the engine continuously for lon-
ger than 30 seconds, or the heat may
damage the starter motor.
NOTE:
Refer to the applicable manual for your transfer switch and to
“Transfer Switch Start Signal Connections”. In addition, please
note the dangers under “Engine Start-up and Transfer.”
9-1
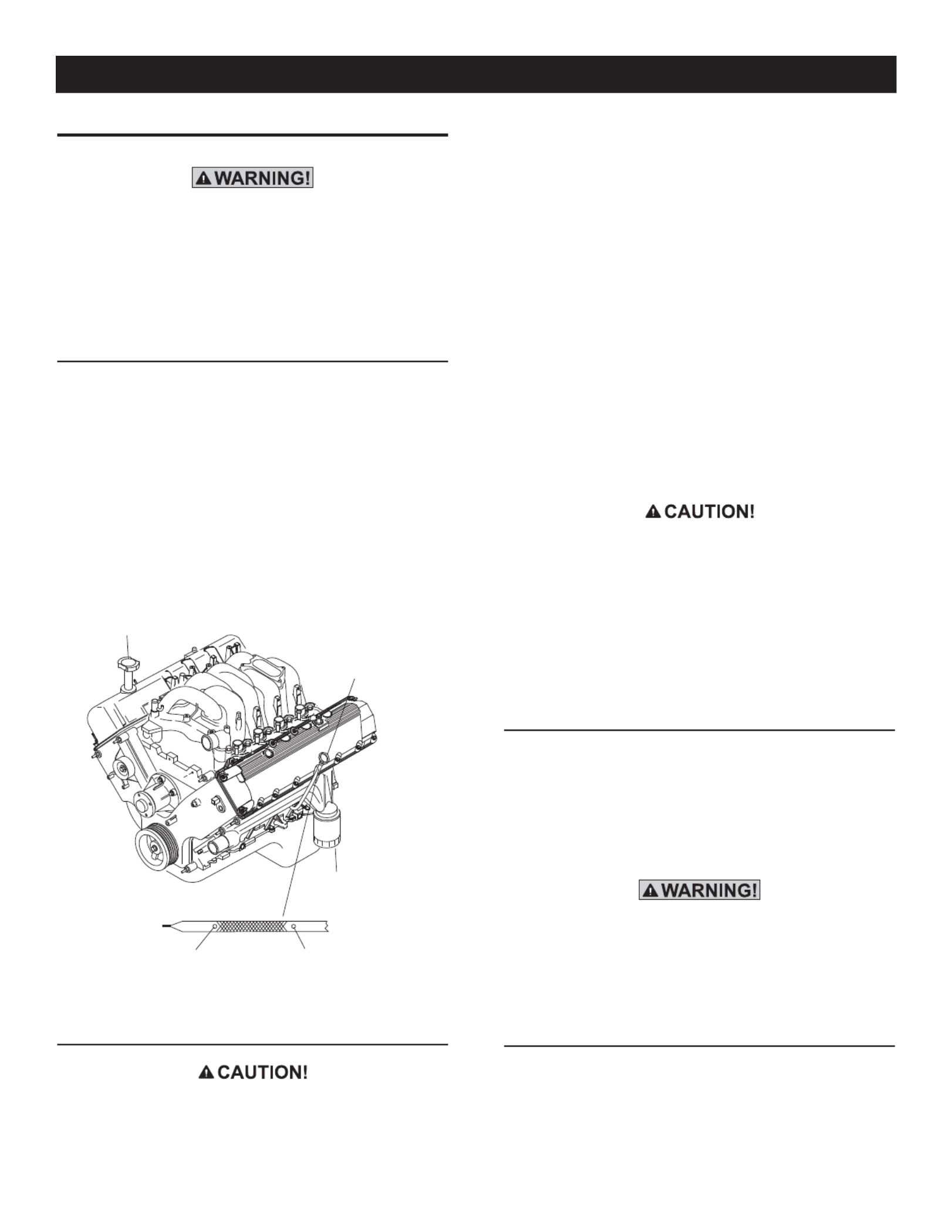
GENERAL MAINTENANCE
Before working on the Stationary Emergency
Generator, ensure the following:
• The AUTO/OFF/MANUAL switch is in the OFF position.
• The control panel fuse has been removed from the control
box.
• The 120VAC supply to the battery charger is switched OFF.
• The negative battery cable has been removed.
CHECK ENGINE OIL
Check engine crankcase oil level (Figure 10.1) according to the
Service Schedule.
• Remove oil dipstick and wipe dry with a clean, lint-free cloth.
• Install oil dipstick, wait approximately 10 seconds, then remove
again.
• Oil should be between FULL and ADD marks.
• If oil level is below the dipstick ADD mark, remove oil fill cap-.
Add the recommended oil to bring oil level up to the FULL
mark. DO NOT FILL ABOVE THE “FULL” MARK. See “Engine Oil
Recommendations” for recommended oils.
Figure 10.1 - Oil Dipstick and Oil Fill Cap
Oil Filter
Oil Fill Oil
Dipstick
Add Oil
Level Mark
Full Oil
Level Mark
CHANGING ENGINE OIL
Hot oil may cause burns. Allow engine to cool
before draining oil. Avoid prolonged or repeat-
ed skin exposure with used oil. Thoroughly
wash exposed areas with soap.
Refer to the Service Schedule for engine oil and filter change fre-
quencies.
Drain the oil while the engine is still warm from running. This
means warm up the engine, shut it down and drain immediately
as follows:
1. Remove the drain hose from its retaining clip or cut the zip-tie
securing the oil drain hose.
2. Loosen and remove OIL DRAIN HOSE CAP. Drain oil com-
pletely into suitable container.
3. When all oil has drained, install and tighten OIL DRAIN HOSE
CAP and secure drain hose with a new zip-tie, or place the
hose in its retaining clip.
4. Turn OIL FILTER (Figure 10.1) counterclockwise and remove.
Properly dispose of old filter.
5. Apply light coating of new engine oil to seal of new oil fil-
ter. Install FILTER and tighten by hand only. DO NOT OVER
TIGHTEN.
6. Remove OIL FILL CAP and add recommended oil. Crankcase
oil capacity is listed in the "Specifications" section.
After refilling the crankcase with oil, always
check oil level on dipstick. NEVER OPERATE
ENGINE WITH OIL BELOW THE DIPSTICK “ADD”
MARK.
7. Start engine and check for oil leaks.
8. Shut OFF engine and wait 10 minutes for the oil to settle down
into the oil pan. Recheck oil level on dipstick. DO NOT fill
above the dipstick "FULL" mark.
9. Dispose of used oil at a proper collection center.
COOLING INTAKE/OUTLET
Air intake and outlet openings in the generator compartment must
be open and unobstructed for continued proper operation. This
includes such obstructions as high grass, weeds, brush, leaves
and snow.
Without sufficient cooling and ventilating air flow, the engine/gen-
erator quickly overheats, which causes it to shut down. (See the
installation diagram.)
The exhaust system parts from this product get
extremely hot and remains hot after shutdown.
High grass, weeds, brush, leaves, etc. must
remain clear of the exhaust. Such materials may
ignite and burn from the heat of the exhaust
system.
INSPECT COOLING SYSTEM
• Inspect engine cooling system. See the Service Schedule.
• Check hoses for damage, deterioration, leaks, etc. Correct any
discrepancies found.
• Check hose clamps for tightness.
10-1
Maint032 Rev. A 12/11
Maintenance
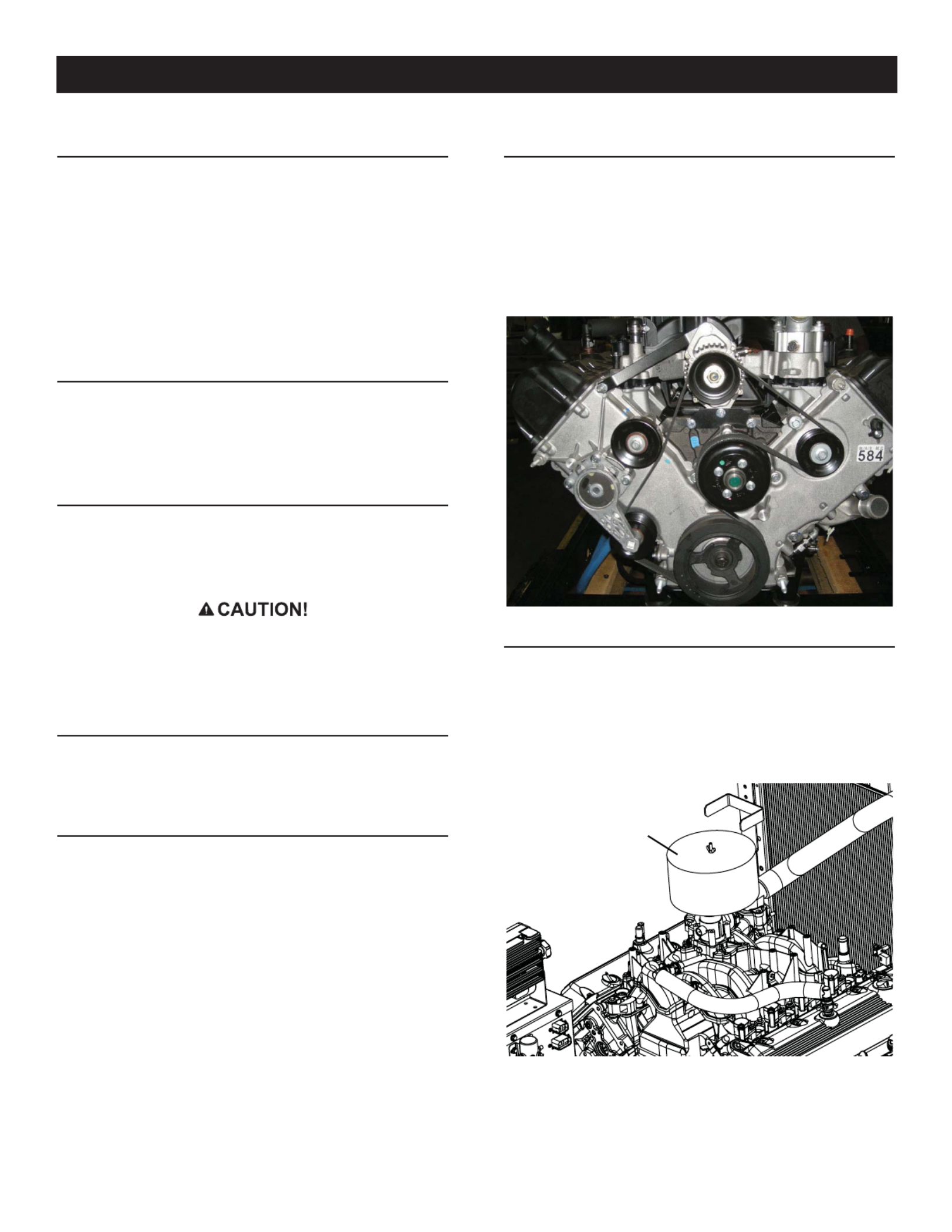
ENGINE COOLANT
Check coolant level in coolant recovery bottle. See the Specifications
and Service Schedule sections.
• Add recommended coolant mixture as necessary.
• Periodically remove radiator pressure cap (only when engine
has cooled down) to make sure the coolant recovery system
is functioning properly. Coolant should be at bottom of radia-
tor filler neck. If coolant level is low, inspect gasket in radiator
pressure cap. Replace cap, if necessary. To have pressure cap
tested, contact a Service Facility. Inspect cooling system and
coolant recovery system for leaks.
COOLANT CHANGE
Every year, have a service dealer drain, flush and refill the cooling
system. See the Specifications and Service Schedule for cooling
system recommendations.
OVERLOAD PROTECTION FOR ENGINE DC ELECTRICAL
SYSTEM
Engine cranking, start up and running are controlled by a solid
state Engine Controller circuit board. Battery voltage is delivered
to that circuit board via the control panel fuse. This overcurrent
protection device will open if the circuit is overloaded.
If a circuit breaker opens or a fuse element
melts, find the cause of the overload before
resetting the circuit breaker or replacing the
fuse.
PERFORM VISUAL INSPECTION
Complete a thorough visual inspection of the entire engine-genera-
tor monthly. Look for obvious damage, loose, missing or corroded
nuts, bolts and other fasteners. Look for fuel, oil or coolant leaks.
INSPECT EXHAUST SYSTEM
Inspect the exhaust system at least once every year. Check all
exhaust system pipes, mufflers, clamps, etc. for condition, tight-
ness, leaks, security, damage.
CHECK FAN BELT
• Inspect fan belts every year. Replace any damaged, deterio-
rated, worn or otherwise defective belt.
• Check fan belt tension. Thumb pressure, exerted midway
between pulleys, should deflect about 3/8 to 5/8 of an inch.
This system uses an automatic belt tensioner and cannot be
adjusted.
Figure 10.2 – Fan Belts
CHANGING THE ENGINE AIR FILTER
To replace the engine air filter, remove the air filter cover and
replace the air filter making sure it is positioned properly before
reattaching the cover (Figure 10.3).
See the Service Schedule for air filter maintenance.
Figure 10.3 – Engine Air Filter
Air Filter
10-2
Maint032 Rev. A 12/11
Maintenance
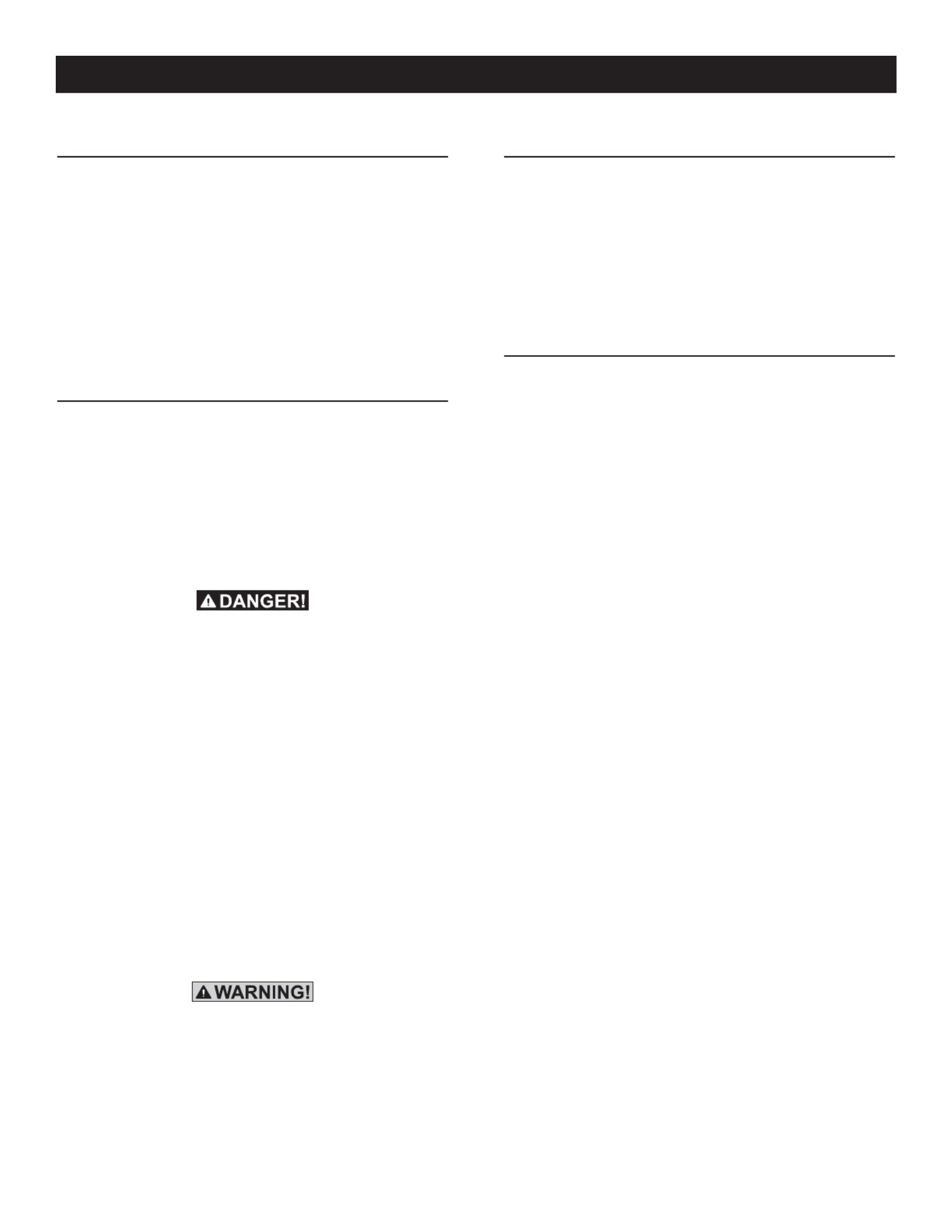
SPARK PLUGS
Reset the spark plug gap or replace the spark plugs as neces-
sary.
1. Clean the area around the base of the spark plugs to keep dirt
and debris out of the engine. Clean by scraping or washing
using a wire brush and commercial solvent. Do not blast the
spark plugs to clean.
2. Remove the spark plugs and check the condition. Replace
the spark plugs if worn or if reuse is questionable. See the
“Service Schedule” section for recommended inspection.
3. Check the spark plug gap using a wire feeler gauge. See the
Specifications section for the required spark plug gap.
BATTERY MAINTENANCE
The battery should be inspected per the Service Schedule section.
The following procedure should be followed for inspection:
1. Inspect the battery posts and cables for tightness and corro-
sion. Tighten and clean as necessary.
2. Check the battery fluid level of unsealed batteries and, if
necessary, fill with DISTILLED WATER ONLY. DO NOT USE TAP
WATER IN BATTERIES.
3. Have the state of charge and condition checked. This should
be done with an automotive-type battery hydrometer.
Storage batteries give off explosive hydrogen
gas. This gas can form an explosive mixture
around the battery for several hours after
charging. The slightest spark can ignite the gas
and cause an explosion. Such an explosion can
shatter the battery and cause blindness or other
injury. Any area that houses a storage battery
must be properly ventilated. Do not allow smok-
ing, open flame, sparks or any spark producing
tools or equipment near the battery.
Battery electrolyte fluid is an extremely corro-
sive sulfuric acid solution that can cause severe
burns. Do not permit fluid to contact eyes, skin,
clothing, painted surfaces, etc. Wear protective
goggles, protective clothing and gloves when
handling a battery. If fluid is spilled, flush the
affected area immediately with clear water.
Do not use any jumper cables or booster bat-
tery to crank and start the generator engine. If
the battery has completely discharged, remove
it from the generator for recharging.
Be sure the AUTO/OFF/MANUAL switch is set
to the OFF position, before connecting the
battery cables. If the switch is set to AUTO or
MANUAL, the generator can crank and start as
soon as the battery cables are connected.
Be sure the 120VAC power supply to the battery
is turned OFF, or sparking may occur at the bat-
tery posts as the cables are attached and cause
an explosion.
BATTERY REPLACEMENT
NOTE:
Unit DOES NOT include battery.
When supplying or replacing the battery, the recommended num-
ber and type of battery is listed in the Specifications Section.
NOTE:
The BCI number should be located directly on the battery.
CLEANING THE STATIONARY EMERGENCY GENERATOR
Keep the generator as clean and as dry as possible. Dirt and
moisture that accumulates on internal generator windings have an
adverse effect on insulation resistance.
Periodically clean generator exterior surfaces. A soft brush may be
used to loosen caked on dirt. Use a vacuum system or dry, low
pressure air to remove any accumulations of dirt. The generator is
housed inside an all-weather enclosure, clean the enclosure with a
soft, damp cloth or sponge and water.
Once each year have the generator cleaned and inspected by a
Service Dealer. That dealer will use dry, low pressure air to clean
internal windings.
Finally, have the insulation resistance of stator and rotor windings
checked. If insulation resistances are excessively low, the genera-
tor may require drying.
10-3
Maint032 Rev. A 12/11
Maintenance
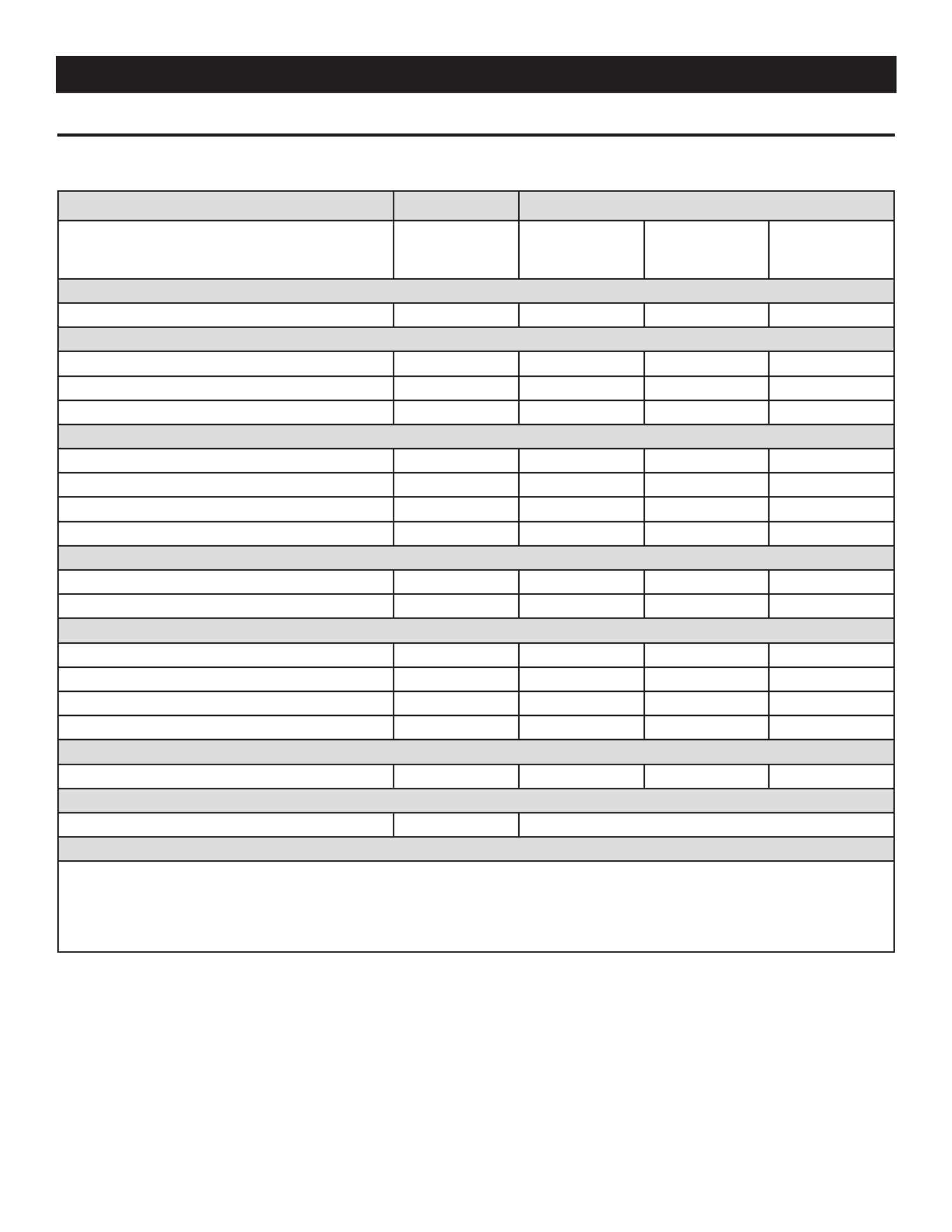
SERVICE SCHEDULE
System / Component Frequency Procedure
Weekly - W
Monthly - M
Yearly - Y
Inspect Change Clean
Fuel
Fuel Lines & Connections M X
Lubrication
Oil Level M X*
Oil Y X**
Oil Filter Y X**
Cooling
Engine Coolant Lines & Connections M X
Engine Coolant Level M X
Engine Coolant Y X
Enclosure Louvers W X X
Engine
Air Cleaner Y X X***
Spark Plugs Y X X***
Battery
Remove Corrosion, Ensure Dryness M X X
Clean & Tighten Battery Terminals M X X
Check Charge State M X X***
Check Electrolyte Level M X X***
General Condition
Vibration, Noise, Leakage, Temperature M X
Generator System
Complete Tune-up and System Inspection Y To be completed by an Authorized Service Dealer.
Footnotes
* Inspect the oil level monthly or every 12 hours during continuous operation.
** Change oil and oil filter after the first 30 hours of operation and then every 100 hours or annually thereafter, whichever occurs first.
Change sooner when operating under heavy load or in a dusty or dirty environment or in high ambient temperatures.
*** Replace as necessary.
11-1
SrvSchd004 Rev. B 05/10
Service Schedule
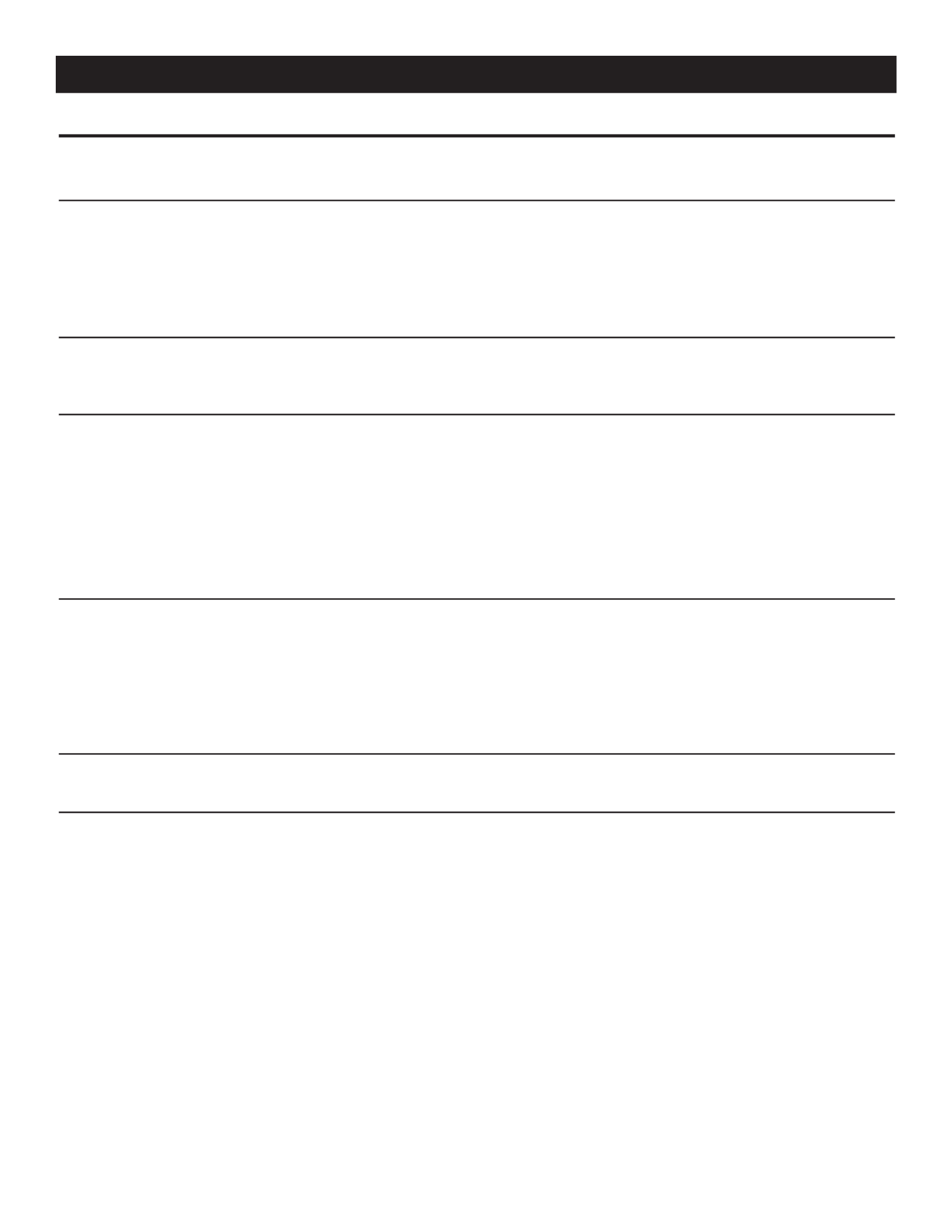
Troubleshooting
TROUBLESHOOTING GUIDE
PROBLEM CAUSE CORRECTION
Engine won’t crank. 1. Control panel 7.5 amp fuse blown. 1. Replace fuse.*
2. Loose or corroded or defective 2. Tighten, clean or replace
battery cables. battery cables as necessary.*
3. Defective starter contactor. 3. Replace contactor.*
4. Defective starter motor. 4. Replace starter motor.*
5. Dead or Defective Battery. 5. Remove, change or replace battery.*
Engine cranks but won't start. 1. Out of fuel. 1. Replenish fuel/turn on fuel valve.
2. Fuel solenoid (FS) is defective 2. Replace solenoid.*
3. Spark plugs defective. 3. Clean, regap or replace plugs.
Engine starts hard, runs rough. 1. Air cleaner plugged or damaged. 1. Clean or replace as needed.
2. Defective spark plugs. 2. Clean, regap or replace plugs.
3. Fuel pressure incorrect. 3. Confirm fuel pressure to regulator is as
recommended in SPECIFICATIONS.*
4. Insufficient fuel supply. 4. Confirm fuel pressure to regualtor is as
recommended in SPECIFICATIONS.*
5. Fuel system set to wrong fuel type. 5. Reconfigure the fuel system. (See
RECONFIGURING THE FUEL SYSTEM in
manual.*
Engine starts then shuts down. 1. Engine oil level is low. 1. Check oil and add oil as needed.
2. Engine is overheated. 2. Check cooling system for leaks.
3. Defective Low Oil Pressure Switch 3. Replace switch.*
4. Defective Coolant Temperature Switch 4. Replace switch.*
5. Defective Control Module circuit board. 5. Replace board.*
6. Coolant Level is Low. 6. Repair leak - Add coolant.
7. Defective Low Coolant Level Switch 7. Replace Switch.*
AUTO/OFF/MANUAL Switch at OFF, 1. Defective AUTO/OFF/MANUAL switch 1. Replace board.*
engine continues to run. 2. Defective Control Module circuit board 2. Replace board.*
No AC output from generator. 1. Main line circuit breaker is tripped/open. 1. Reset to ON/CLOSED.
2. Generator internal failure. 2. *
3. Thermal circuit breaker open. 3. Auto-reset - Wait 5 min. and attempt restart.
*Contact the nearest Dealer for assistance.
12-1
Trblsht003 Rev. B 05/10

United States Environmental Protection Agency Warranty Statement
(Stationary Emergency Spark-Ignited Generators)
Warranty Rights, Obligations and Coverage
The United States Environmental Protection Agency (EPA) and Generac Power Systems, Inc. (Generac) are pleased to explain the Emission
Control System Warranty on your new stationary emergency engine. If during the warranty period, any emission control system or compo-
nent on your engine is found defective in materials or workmanship, Generac will repair your engine at no cost to you for diagnosis, replace-
ment parts and labor provided it be done by a Generac Authorized Warranty Service Facility. Your emission control system may include parts
such as the fuel metering, ignition, and exhaust systems and other related emission related components listed below. Generac will warrant
the emissions control systems on your 2009 and later model year engines provided there has been no abuse, neglect, unapproved modifica-
tion, or improper maintenance of your engine. For engines less than 130 HP the warranty period is two years from the date of sale to the ulti-
mate purchaser. For engines greater than or equal to 130 HP the warranty period is three years or 2500 hours of operation, whichever
comes first, from the date of the engine being placed into service. For high-cost warranted components, the Emission Control System war-
ranty is valid for 5 years or 3500 hours of operation, whichever comes first.
Purchaser's/Owner's Warranty Responsibilities
As the engine purchaser/owner you are responsible for the following: 1) The engine must be installed and configured in accordance to Gen-
erac's installation specifications. 2) The completion of all maintenance requirements listed in your Owner's Manual. 3) Any engine setting
adjustment must be done in accordance and consistent with the instructions in the Owner's Manual. 4) Any emission control system or com-
ponent must be maintained and operated appropriately in order to ensure proper operation of the engine and control system to minimize
emissions at all times.
Generac may deny any/or all Emission Control System Warranty coverage or responsibility of the engine, or an emission control system or
component on your engine thereof, if it has failed due to abuse, neglect, unapproved modification or improper maintenance, or the use of
counterfeit and/or “gray market” parts not made, supplied or approved by Generac. Warranty service can be arranged by contacting either
your selling dealer or a Generac Authorized Warranty Service dealer, 1-800-333-1322 for the dealer nearest you. The purchaser/owner shall
be responsible for any expenses or other charges incurred for service calls and/or tr spection or ansportation of the product to/from the in
repair facilities. The purchaser/owner shall be responsible for any and/or all damages or losses incurred while the engine is being trans-
ported/shipped for inspection or warranty repairs. Contact Generac Power Systems Inc. for additional Emission Control System Warranty
related information, Generac Power Systems, Inc., PO. Box 8, Waukesha, WI 53187, or call 1-800-333-1322 or www.generac.com.
Important Note
This warranty statement explains your rights and obligations under the Emission Control System Warranty, which is provided to you by Gen-
erac pursuant to federal law. Note that this warranty shall not apply to any incidental, consequential, or indirect damages caused by defects
in materials or workmanship or any delay in repair or replacement of the defective part(s). This warranty is in place of all other warranties,
expressed or implied. Specifically, Generac makes no other warranties as to the merchantability or fitness for a particular purpose. Any
implied warranties which are allowed by law, shall be limited in duration to the terms of the express warranty provided herein. Some states
do not allow limitations on how long an implied warranty lasts, so the above limitation may not apply to you.
Emission Related Parts Include the Following (if so equipped)
*High-Cost Warranted Component
EmsnWrnty001 Revision F (04/15)
1) Fuel Metering System
1.1) Gasoline Carburetor Assembly and Internal Components
A) Fuel Filter, B) Carburetor, C) Fuel Pump
1.2) Carburetion Assembly and Its Components
A) Fuel Controller, B) Carburetor and Its Gaskets,
C) Mixer and Its Gaskets, D) Primary Gas Regulator,
E) Liquid Vaporizer
1.3) Fuel Regulator
2) Air Induction System Including A) Intake Pipe/Manifold,
B) Air Cleaner
3) Ignition System Including A) Spark Plug, B) Ignition Module,
C) Ignition Coil, D) Spark Plug Wires
4) Exhaust System
A) Catalyst Assembly*, B) Exhaust Manifold, C) Muffler,
D) Exhaust Pipe, E) Muffler Gasket
5) Crankcase Breather Assembly Including
A) Breather Connection Tube, B) PCV Valve
6) Oxygen Sensor
7) Diagnostic Emission-Control System
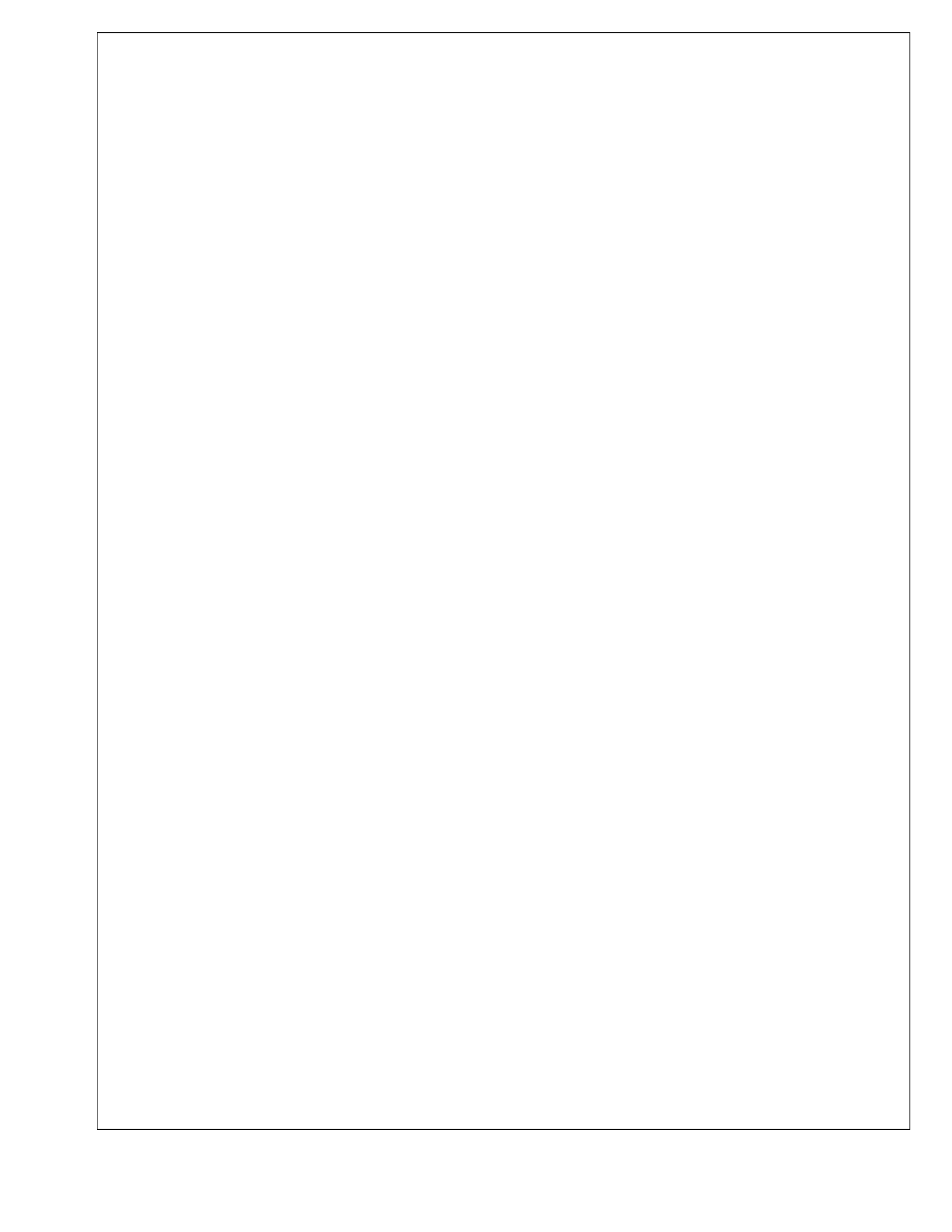
United States Environmental Protection Agency Compliance Requirements
(Stationary Emergency Spark-Ignited Generators)
Purchaser's/Owner's Record Keeping Responsibilities
The United States Environmental Protection Agency (EPA) and Generac Power Systems, Inc. (Generac) are pleased to explain your record
keeping requirements for compliance with Subpart JJJJ- Standards of Performance for Stationary Spark Ignition Internal Combustion
Engines as listed in the Electronic Code of Federal Regulations Title 40 Part 60. As the engine purchaser/owner who operates and maintains
their certified emergency stationary engine and emission control system according to applicable emission related guidelines as specified in
this Owner's Manual, you are required to meet the following notification and record keeping requirements to demonstrate compliance: 1)
Maintain documentation that the engine is certified to meet emission standards. 2) Record keeping of maintenance conducted. 3) Record
keeping of the provision allowing natural gas engines to operate using propane for a maximum of 100 hours per year as an alternate fuel
solely during emergency operations provided the engine is not certified to operate on propane. 4) Meet all compliance notifications submitted
to the purchaser/owner and maintain all supporting documentation. 5) Record keeping of hours of operation, including what classified the
operation as emergency and how many hours are spent for non-emergency operation. For emergency engines greater than or equal to 130
HP, record keeping of hours of operation begins January 1, 2011. For emergency engines less than 130 HP, record keeping of hours of oper-
ation begins January 1, 2009; engines are equipped with non-resettable hour meters to facilitate record keeping.
Specific Air Quality Management or Air Pollution Control Districts may have different and additional record keeping/reporting requirements.
Your permit to construct and/or operate the engine may be contingent upon compliance with those requirements. Check with your local Air
Quality Management or Air Pollution Control District for specific requirements.
Emergency stationary internal combustion engines (ICE) may be operated for the purpose of maintenance checks and readiness testing,
provided that the tests are recommended by Federal, State or local government, Generac, or the insurance company associated with the
engine. Maintenance checks and readiness testing of such units is limited to 100 hours per year. There is no time limit on the use of emer-
gency stationary ICE in emergency situations. The purchaser/owner may petition the Administrator for approval of additional hours to be
used for maintenance checks and readiness testing, but a petition t Federal, is not required if the owner maintains records indicating tha
State, or local standards require maintenance and testing of emergency ICE beyond 100 hours per year. Emergency stationary ICE may
operate up to 50 hours per year in non emergency situations, but those 50 hours are counted towards the 100 hours per year provided for
maintenance and testing.
The 50 hours per year for non-emergency situations cannot be used for peak shaving or to generate income for a facility to supply power to
an electric grid or otherwise supply power as part of a financial arrangement with another entity. For purchaser/owner of emergency engines,
any operation other than emergency operation, maintenance and testing, and operation in non-emergency situations for 50 hours per year,
as permitted in this section is prohibited.
If you operate and maintain your certified emergency stationary SI internal combustion engine and emissions control systems in accordance
to the specifications and guidelines in this Owner’s Manual, EPA will not require engine performance testing. If not, your engine will be con-
sidered non-certified and you must demonstrate compliance according to Subpart JJJJ - Standards of Performance for Stationary Spark Igni-
tion Internal Combustion Engines as listed in the Electronic Code of Federal Regulations Title 40 Part 60.
Emission-Related Installation Instructions
Your certified emergency stationary engine has pre-set emission control systems or components that require no adjustment. Inspection and
replacement of an emissions related component is required to be done so in accordance with the requirements cited in the United States
Environmental Protection Agency Warranty Statement or can be arranged by contacting either your selling dealer or a Generac Authorized
Warranty Service dealer, 1-800-333-1322 for the dealer nearest you. Failing to follow t ified engine in a hese instructions when installing a cert
piece of non-road equipment violates federal law 40 CFR 1068.105 (b), subject to fines or penalties as described in the Clean Air Act.
EmsnWrnty001 Revision F (04/15)
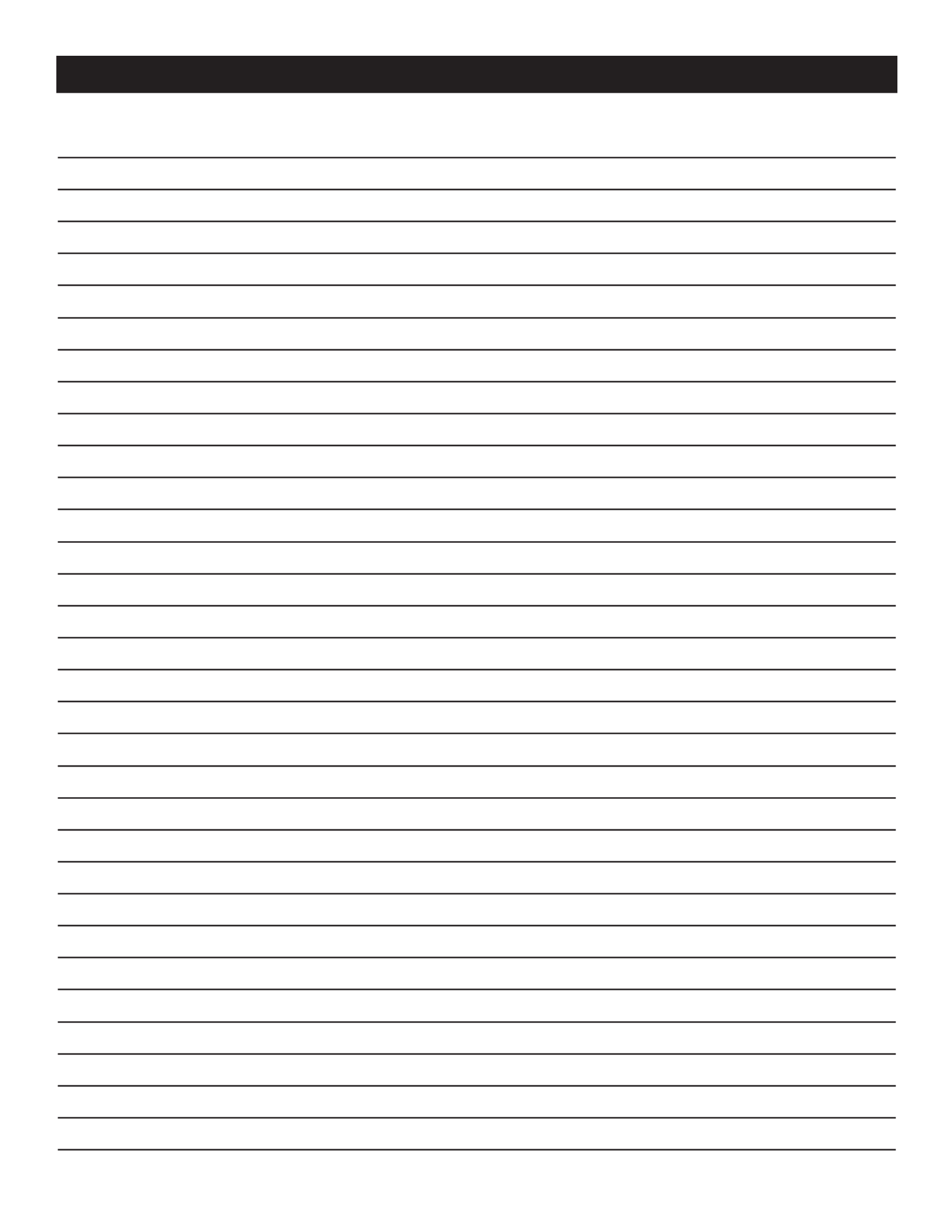
Notes
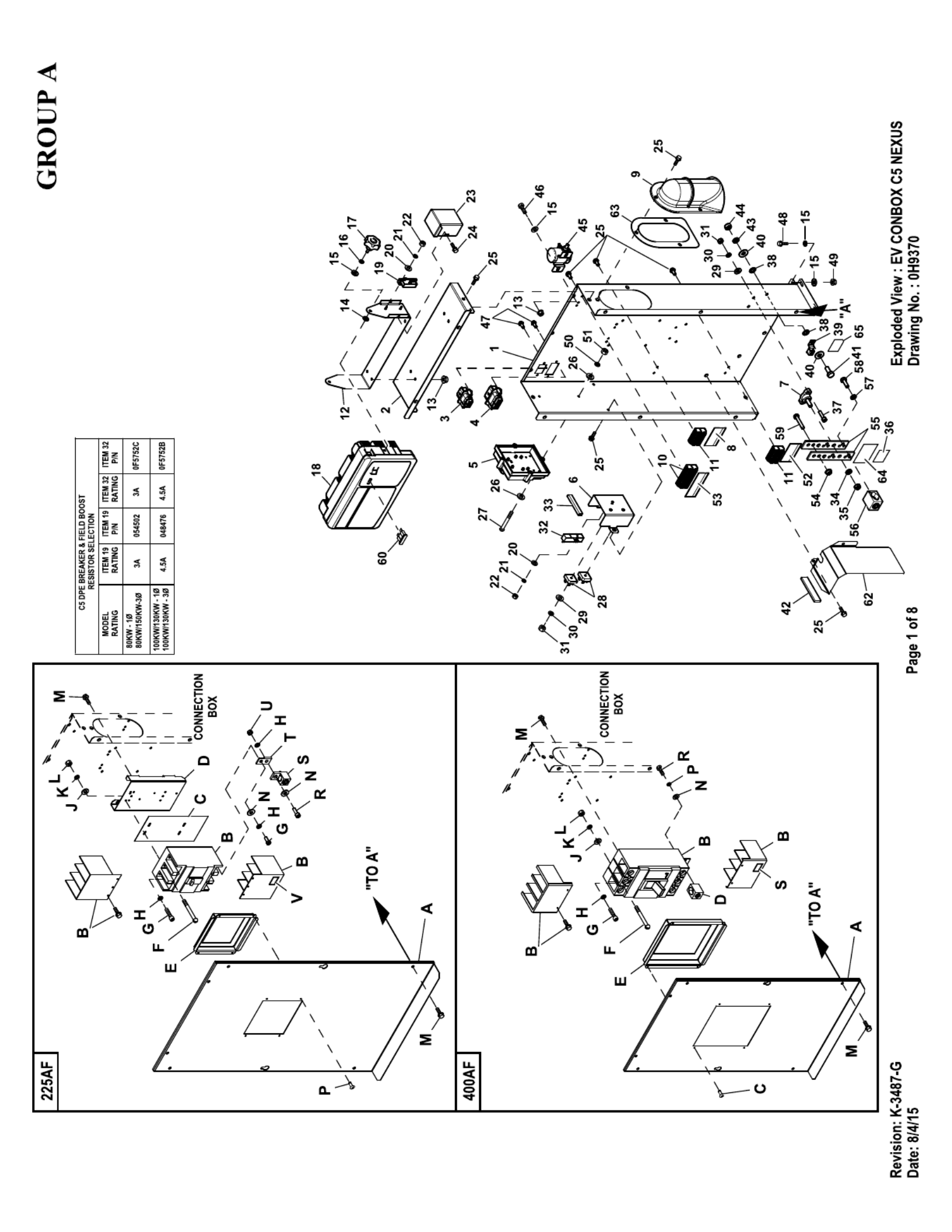
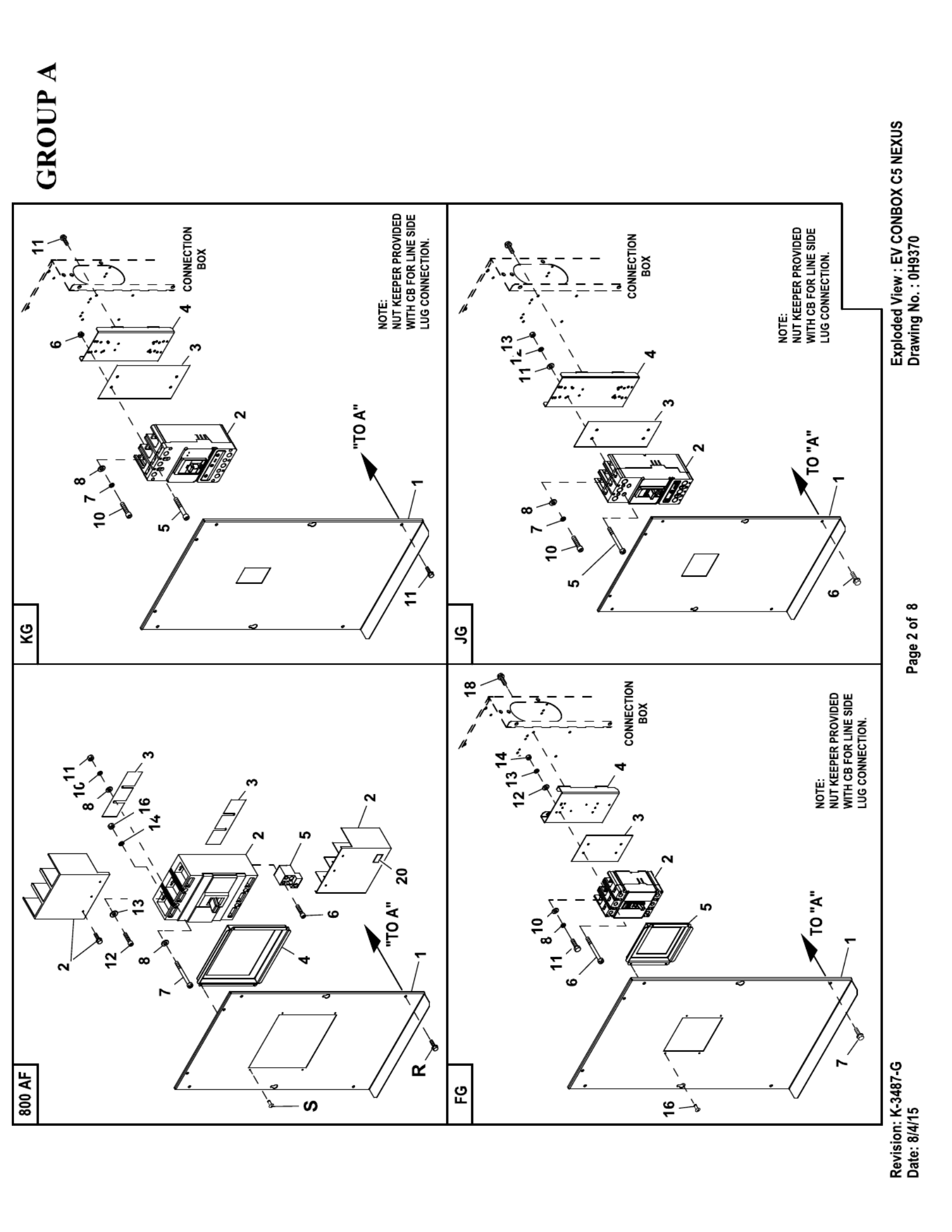
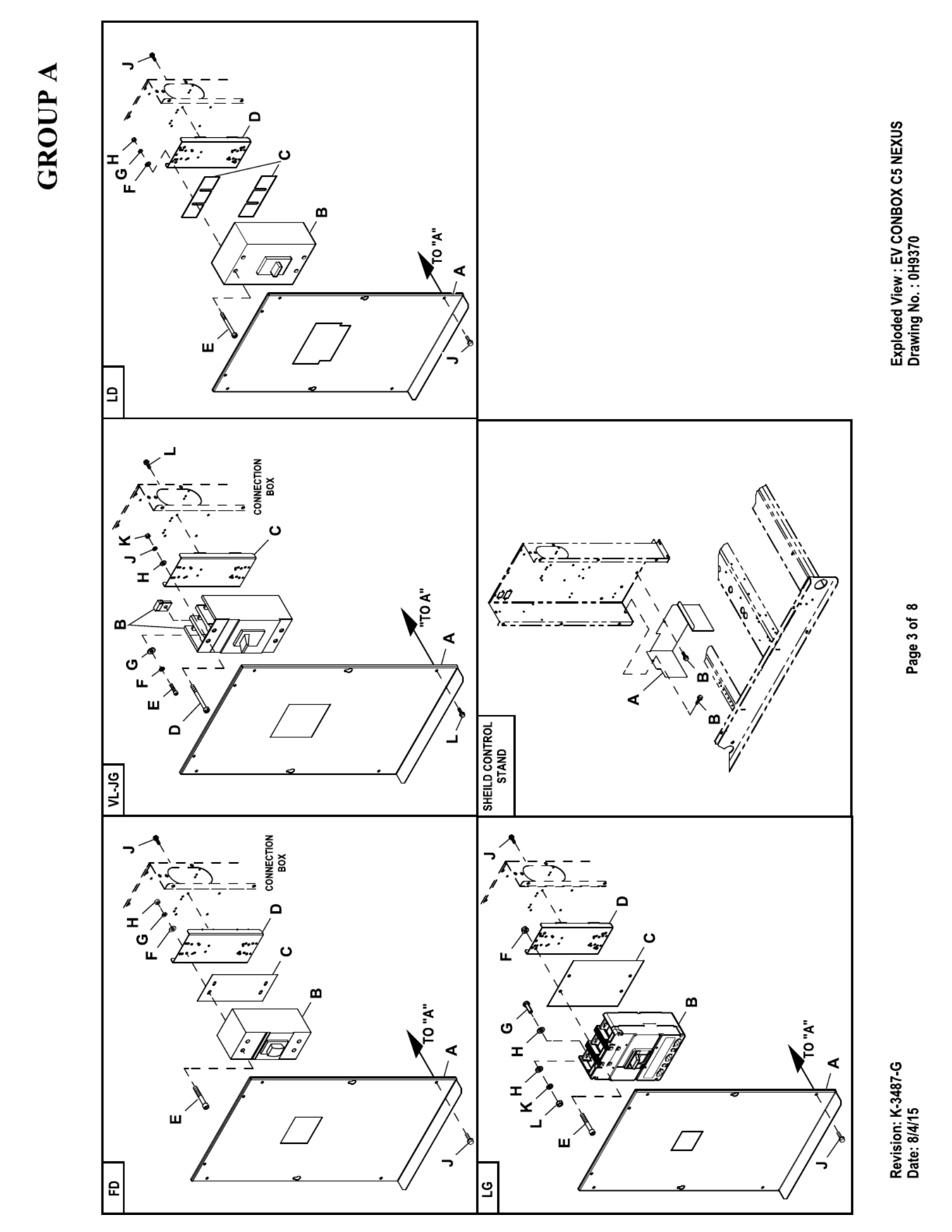
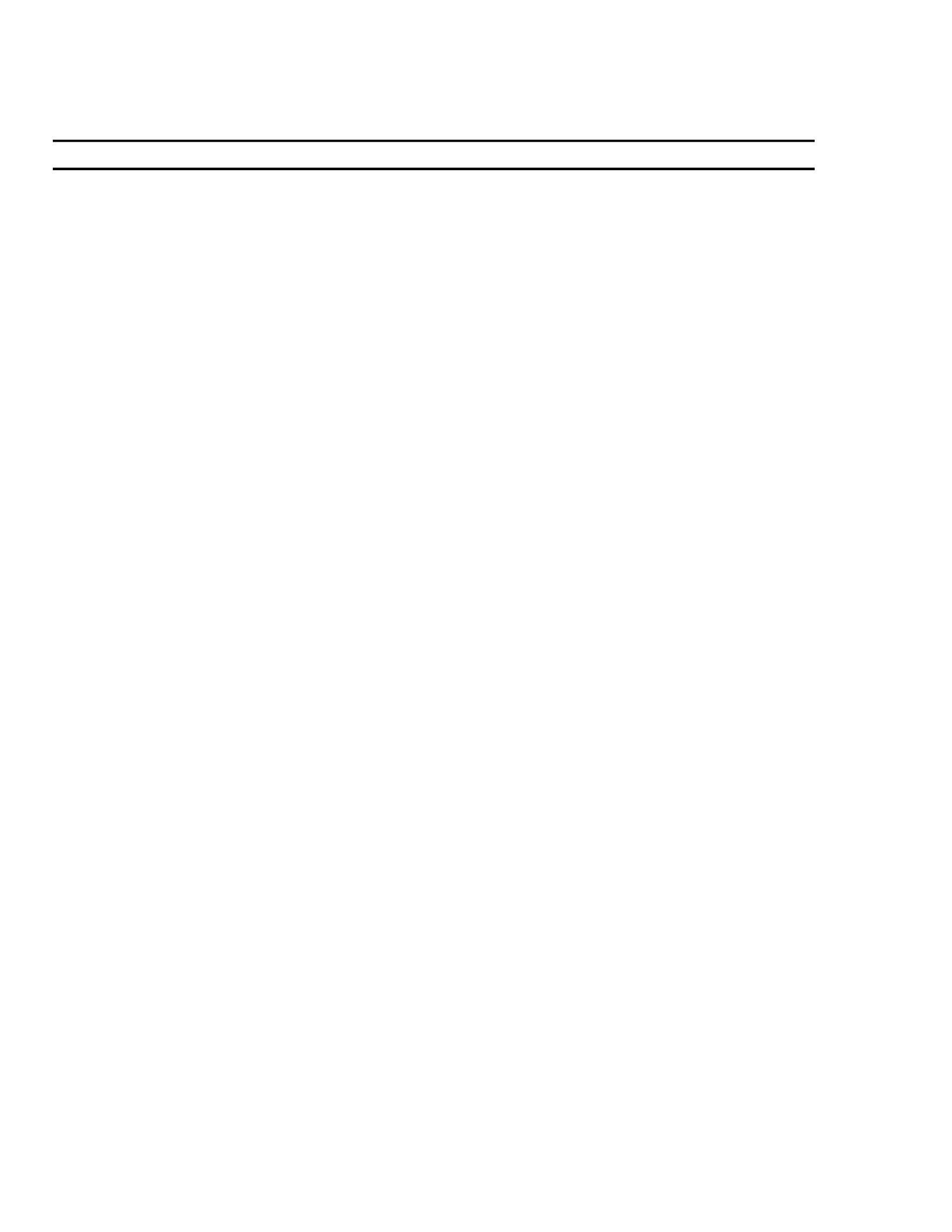
EXPLODED VIEW: EV CONBOX C5 NEXUS
DRAWING #: 0H9370
GROUP A
APPLICABLE TO:
REVISION: K-3487-G Page 4 of 8
DATE: 8/4/15
ITEM PART# QTY. DESCRIPTION
PAGE 1
1 0H9221 1 BACK PANEL CONNBOX SUPPORT C5
2 0H6265 1 TOP PANEL CONNBOX SUPPORT C2
(1)3 0F5376S0AR 1 MX150L SLRRMNT 22-18 8P W/O GA
(1)4 0F5396S0AR 1 MX150L SLRRMNT 22-18 12P W/OGA
5 0H6169D 1 ASSY PROG 2010 IGN MOD 10CYL
0H6169C 1 ASSY PROG 2010 IGN MOD 8 CYL
6 0H6267 1 COVER VOLTAGE SHIELD
7 057073 2 JUNCTION BLOCK 3/8-16
8 0J0489 1 DECAL CUSTOMER POWER CONNECT
9 0H6160 1 COVER WIRE ENTRY CONNBOX
(1)10 0D7393T 2 TERM BLOCK 3P UL 12-20AWG
(1)11 0D7393U 2 TERM BLOCK 4P UL 12-20AWG
(5)12 0H67330ST0R 1 BRACKET GIMBAL CONTROL PNL
13 0D3700 6 NUT FLANGE M6-1.0 NYLOK
14 0A2115 2 WASHER NYLON .257
15 022473 12 WASHER FLAT 1/4-M6 ZINC
16 022097 2 WASHER LOCK M6-1/4
17 0H7115 2 KNOB M6-1.0 CONTROL PANEL
18 REF 1 ASSY CTRL PROGRAMMED
(3)19 -- 1 SEE “C5 DPE BRKR & FIELD BOOST” CHART
20 052777 3 WASHER FLAT M3
21 043182 3 WASHER LOCK M3
22 051714 3 NUT HEX M3-0.5 G8 CLEAR ZINC
(5)23 0H81040AS0R 1 COVER DPE BREAKER NEXUS RAW
24 045764 2 SCREW HHTT M4-0.7 X 8 ZP
25 0C2454 10 SCREW HWHT M6-1 X 16 N WA Z/JS
26 023897 4 WASHER FLAT #10 ZINC
27 036943 2 SCREW PPHM #10-32 X 2
28 0D7177V 2 DIODE BRIDGE 1P 35A 1000V
29 051713 6 WASHER FLAT M5
30 049226 6 WASHER LOCK M5
31 051716 6 NUT HEX M5-0.8 G8 CLEAR ZINC
(3)32 -- 1 SEE “C5 DPE BRKR & FIELD BOOST” CHART
33 056326 1 TRIM VINYL BLACK 1/8GP (63“LG)
34 022237 2 WASHER LOCK 3/8
35 022241 2 NUT HEX 3/8-16 STEEL
36 0H8006 1 DECAL CAUTION ELEC SHOCK SM
37 0D3580 4 SCREW SHC M5-0.8 X 20 C12.9
38 025507 2 WASHER LOCK EXT 7/16 STL
39 061383 1 LUG SLDLSS 3/0-#4 X 13/32 CU
40 022131 2 WASHER FLAT 3/8-M10 ZINC
41 049814 1 SCREW HHC M10-1.5 X 25 C8.8
42 029289 1 TAPE ELEC 1/2 FOAM
43 046526 1 WASHER LOCK M10
44 045772 1 NUT HEX M10-1.5 G8 YEL CHR
45 056739 1 RELAY SOLENOID 12VDC PNL MNT
46 042568 2 SCREW HHC M6-1.0 X 20 C8.8
47 0F5458 12 SCREW HHSP #10 X 3/8 HI-LOW
48 0D6029 4 SCREW HHTT M6-1.0 X 16 ZYC
49 052857 4 NUT TOP LOCK FL M6-1.0
50 022152 2 WASHER LOCK #10
51 022158 2 NUT HEX #10-32 STEEL
52 0H7292 1 DECAL CUSTOMER CONTROL CONNECT
53 0H7293 1 DECAL CONBOX TB1 CONNECTIONS
(2)54 067989 1 NUT HEX FL WHIZ M8-1.25
(2)55 0D5466 2 BUSBAR NEUTRAL BLOCK 390
(2)56 0A7822 1 LUG SLDLSS 600/250-1/0X1/4-28
(2)57 083896 2 WASHER LOCK 1/4-M6 SS
(2)58 045335 2 SCREW HHC 1/4-28 X 3/4 G5
(2)59 039287 1 SCREW HHC M8-1.25 X 45 C8.8
60 0D7178T 1 FUSE ATO TYPE 7.5AMP (BROWN)
61 0J1618 1 HARN EXCITATION NEXUS C3/C5 (NOT SHOWN)
62 0H97300ST0R 1 SHIELD HIGH/LOW C5 RAW
63 0J3060 1 GASKET WIRE ENTRY COVER
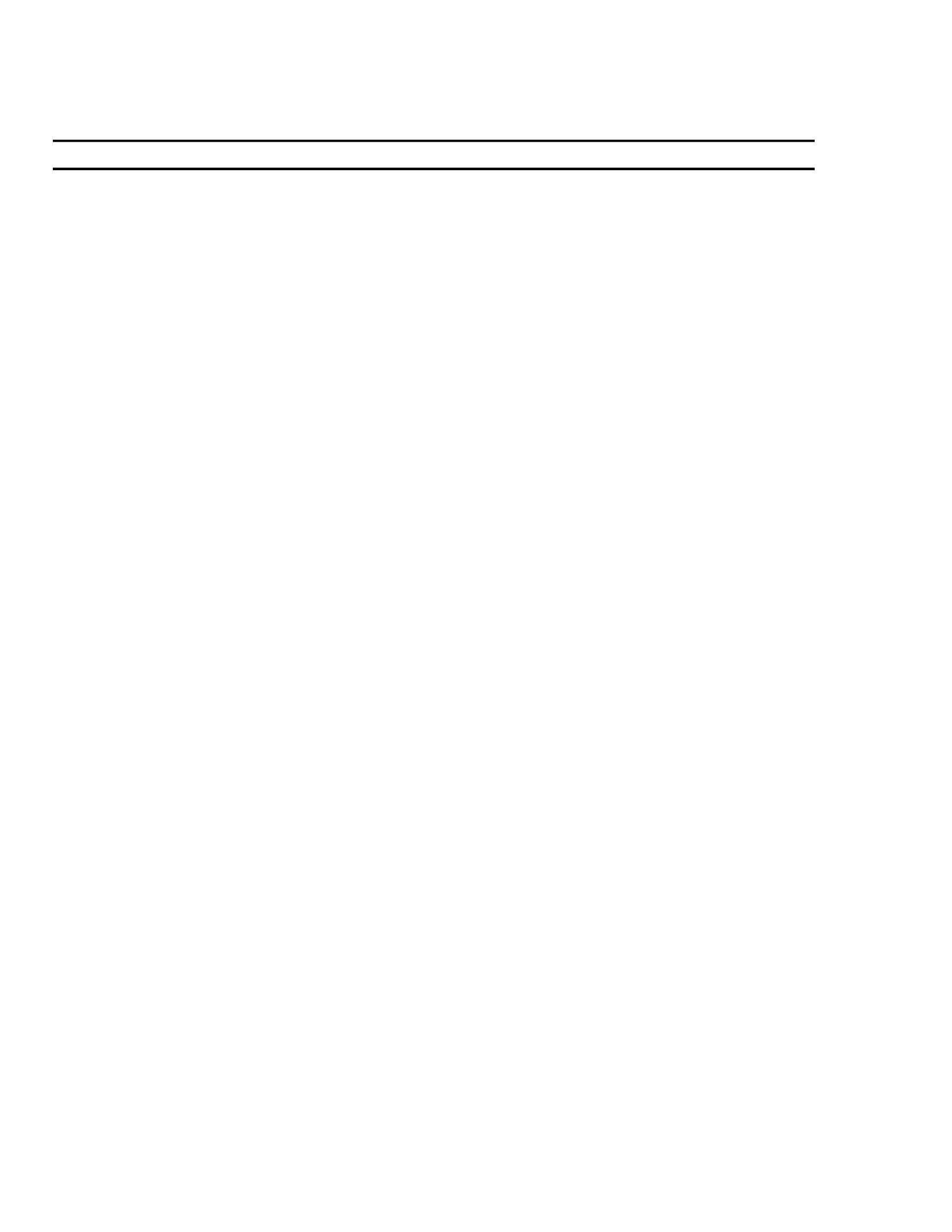
EXPLODED VIEW: EV CONBOX C5 NEXUS
DRAWING #: 0H9370
GROUP A
APPLICABLE TO:
REVISION: K-3487-G Page 5 of 8
DATE: 8/4/15
ITEM PART# QTY. DESCRIPTION
64 0A9457 1 DECAL NEUTRAL
65 067210A 1 DECAL GROUND LUG
UL CIRCUIT BREAKER (225AF)
A 0J0662 1 COVER CB G 225AF C5
B 0F4149 1 CB 0150A 3P 480V G 225AF
0F4150 1 CB 0175A 3P 480V G 225AF
C 0F8432 1 INSUL CB 225AF
D 0H7311 1 STANDOFF CB BOX CONBOX
E 0F4186 1 COVER CB DISH 3P G 225AF
F 053640 4 SCREW RHM #8-32 X 3-1/4
G 049897 6 SCREW SHC M8-1.25 X 20 G8
H 022129 9 WASHER LOCK M8-5/16
J 038150 4 WASHER FLAT #8 ZINC
K 022264 4 WASHER LOCK #8-M4
L 022471 4 NUT HEX #8-32 STEEL
M 0C2454 12 SCREW HWHT M6-1 X 16 N WA Z/JS
N 022145 6 WASHER FLAT 5/16-M8 ZINC
P 036261 4 RIVET POP .125 X .275 SS
R 058306 3 SCREW SHC M8-1.25 X 25 C12.9
S 0F8451 3 LUG SLDLSS 300 MCM-6 AL/CU
T 0F8843 3 BUS BAR 200A LUG ADAPTOR
U 045771 3 NUT HEX M8-1.25 G8 CLEAR ZINC
V 0G3257 1 DECAL TERMINAL SHOCK HZD BI
UL CIRCUIT BREAKER (400AF)
A 0H9220 1 COVER CB G 400AF C5
B 0F4153 1 CB 0250A 3P 480V G 400AF
C 036261 4 RIVET POP .125 X .275 SS
(4)D 0A7822 2/3 LUG SLDLSS 600/250-1/0X1/4-28
E 0H9270 1 COVER CB DISH G 400AF C5
F 042419 4 SCREW RHM 10-32 X 4
(4)G 052647 2/3 SCREW SHC M10-1.5 X 25 C12.9
(4)H 046526 2/3 WASHER LOCK M10
J 023897 4 WASHER FLAT #10 ZINC
K 022152 4 WASHER LOCK #10
L 022158 4 NUT HEX #10-32 STEEL
M 0C2454 8 SCREW HWHT M6-1 X 16 N WA Z/JS
(4)N 022473 4/6 WASHER FLAT 1/4-M6 ZINC
(4)P 022097 4/6 WASHER LOCK M6-1/4
(4)R 023334 4/6 SCREW HHC 1/4-28 X 1/2 G5
S 0G3257 1 DECAL TERMINAL SHOCK HZD BI
PAGE 2
UL CIRCUIT BREAKER (800AF)
A 0H9271 1 COVER CB G 800AF C5
B 0F8185 1 CB 0630A 2P 480V G 800AF
0F8189 1 CB 0630A 3P 480V G 800AF
C 0F8433 2 INSUL CB 800AF
D 0H9272 1 COVER CB DISH G 800AF C5
(4)E 0F9721 2/3 LUG SLDLSS 3/0-400X3 MCM AL/CU
(4)F 0D2157 4/6 SCREW SHC M6-1.0 X 50 C8.8
G 069232 4 SCREW RHM #10-32 X 3-3/4
H 023897 8 WASHER FLAT #10 ZINC
J 022152 4 WASHER LOCK #10
K 022158 4 NUT HEX #10-32 STEEL
(4)L 052647 2/3 SCREW SHC M10-1.5 X 25 C12.9
(4)M 022131 2/3 WASHER FLAT 3/8-M10 ZINC
(4)N 022237 2/3 WASHER LOCK 3/8
(4)P 045772 2/3 NUT HEX M10-1.5 G8 YEL CHR
R 0C2454 8 SCREW HWHT M6-1 X 16 N WA Z/JS
S 036261 4 RIVET POP .125 X .275 SS
T 0G3257 1 DECAL TERMINAL SHOCK HZD BI
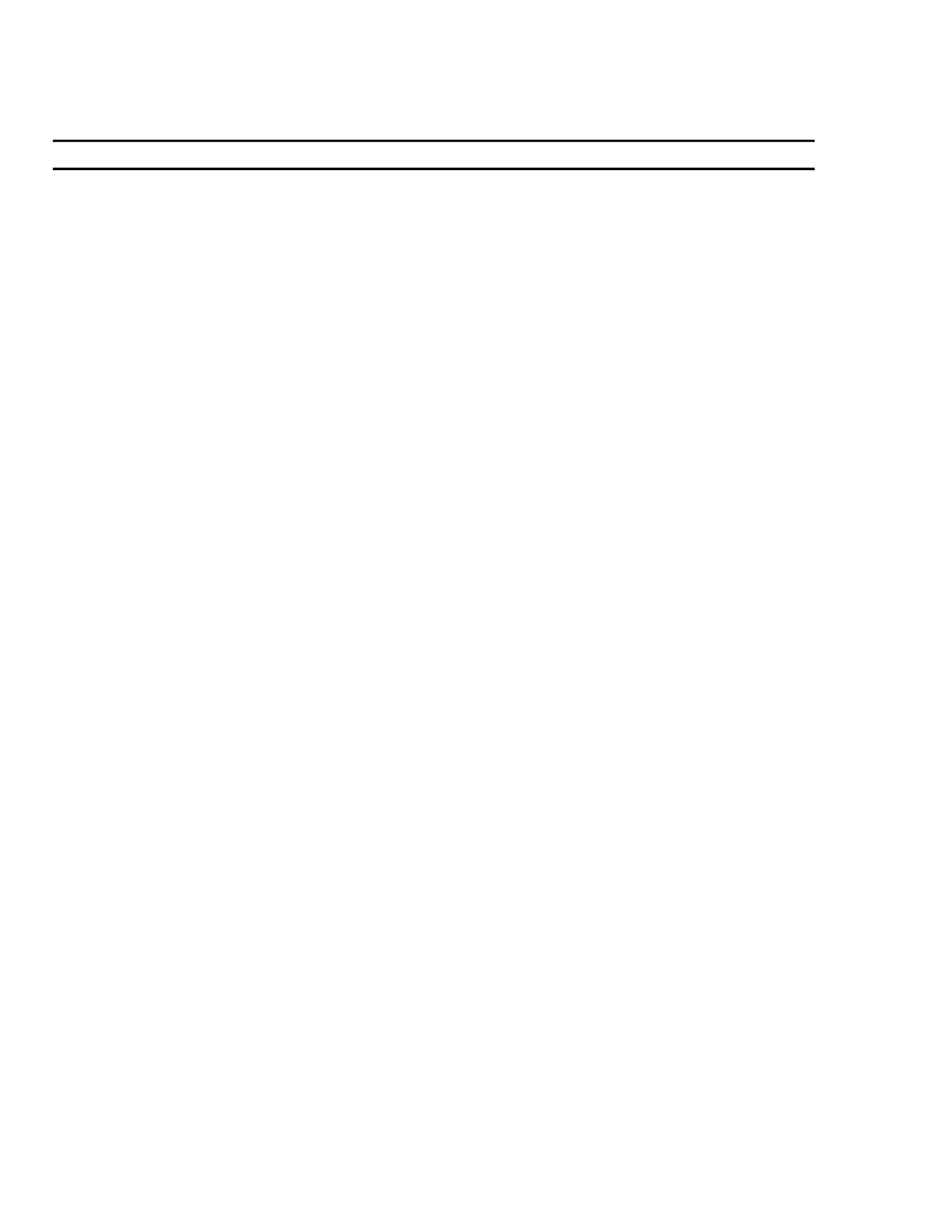
EXPLODED VIEW: EV CONBOX C5 NEXUS
DRAWING #: 0H9370
GROUP A
APPLICABLE TO:
REVISION: K-3487-G Page 6 of 8
DATE: 8/4/15
ITEM PART# QTY. DESCRIPTION
UL CIRCUIT BREAKER (KG)
A 0H9375 1 COVER CB 3P E KG C5
B 0H5582 1 CB 0300 3P 600V E KG LL
C 0H5581A 1 INSULATOR CB E 3P KG
D 0H6734 1 STANDOFF CB MOUNT CONBOX
E 0D2157 4 SCREW SHC M6-1.0 X 50 C8.8
F 0D3700 4 NUT FLANGE M6-1.0 NYLOK
G 022129 3 WASHER LOCK M8-5/16
H 022145 3 WASHER FLAT 5/16-M8 ZINC
J 049821 3 SCREW SHC M8-1.25 X 30 C12.9
K 0C2454 12 SCREW HWHT M6-1 X 16 N WA Z/JS
UL CIRCUIT BREAKER (FG)
A 0H9373 1 COVER CB 3P E FG C5
B 0H5486 1 CB 0060 3P 600V E FG LL
C 0H4698A 1 INSULATOR CB 3P E TYPE CC/FG
D 0H7311 1 STANDOFF CB BOX CONBOX
E 0H7434 1 COVER CB DISH 3P E FG
F 0H5721 4 SCREW PPHM #8-32 X 1-3/4 ZINC
G 0C2454 12 SCREW HWHT M6-1 X 16 N WA Z/JS
H 049226 3 WASHER LOCK M5
J 023897 3 WASHER FLAT #10 ZINC
K 052619 3 SCREW HHC M5-0.8 X 20 G8.8
L 038150 4 WASHER FLAT #8 ZINC
M 022264 4 WASHER LOCK #8-M4
N 022471 4 NUT HEX #8-32 STEEL
P 036261 4 RIVET POP .125 X .275 SS
UL CIRCUIT BREAKER (JG)
A 0H9374 1 COVER CB 3P E JG C5
B 0H5580 1 CB 0250 3P 600V E JG LL
C 0H5576A 1 INSULATOR CB E 3P JG
D 0H6734 1 STANDOFF CB MOUNT CONBOX
E 022770 4 SCREW RHM 1/4-20 X 3
F 0C2454 12 SCREW HWHT M6-1 X 16 N WA Z/JS
G 022129 3 WASHER LOCK M8-5/16
H 022145 3 WASHER FLAT 5/16-M8 ZINC
J 049897 3 SCREW SHC M8-1.25 X 20 G8
K 022473 4 WASHER FLAT 1/4-M6 ZINC
L 022097 4 WASHER LOCK M6-1/4
M 022127 4 NUT HEX 1/4-20 STEEL
PAGE 3
UL CIRCUIT BREAKER (FD)
A 0H9372 1 COVER CB 3P S FD6 C5
B 0D5572 1 CB 0150A 3P 600V S FD6 LL
C 0F0199 1 INSULATOR CB FD FRAME 30MIL
D 0H6734 1 STANDOFF CB MOUNT CONBOX
E 081320 4 SCREW SHC 1/4-20 X 4.5 G8.8 NZ
F 022473 4 WASHER FLAT 1/4-M6 ZINC
G 022097 4 WASHER LOCK M6-1/4
H 022127 4 NUT HEX 1/4-20 STEEL
J 0C2454 12 SCREW HWHT M6-1 X 16 N WA Z/JS
UL CIRCUIT BREAKER (VL-JG)
A 0H9376 1 COVER CB 3P S VL C5
B 0H7519 1 CB 0300A 3P 600V S JG-VL LL
C 0H6734 1 STANDOFF CB MOUNT CONBOX
D 042419 4 SCREW RHM 10-32 X 4
E 040976 3 SCREW SHC M8-1.25 X 20 C12.9
F 022129 3 WASHER LOCK M8-5/16
G 022145 3 WASHER FLAT 5/16-M8 ZINC
H 023897 4 WASHER FLAT #10 ZINC
J 022152 4 WASHER LOCK #10
K 022158 4 NUT HEX #10-32 STEEL
L 0C2454 12 SCREW HWHT M6-1 X 16 N WA Z/JS
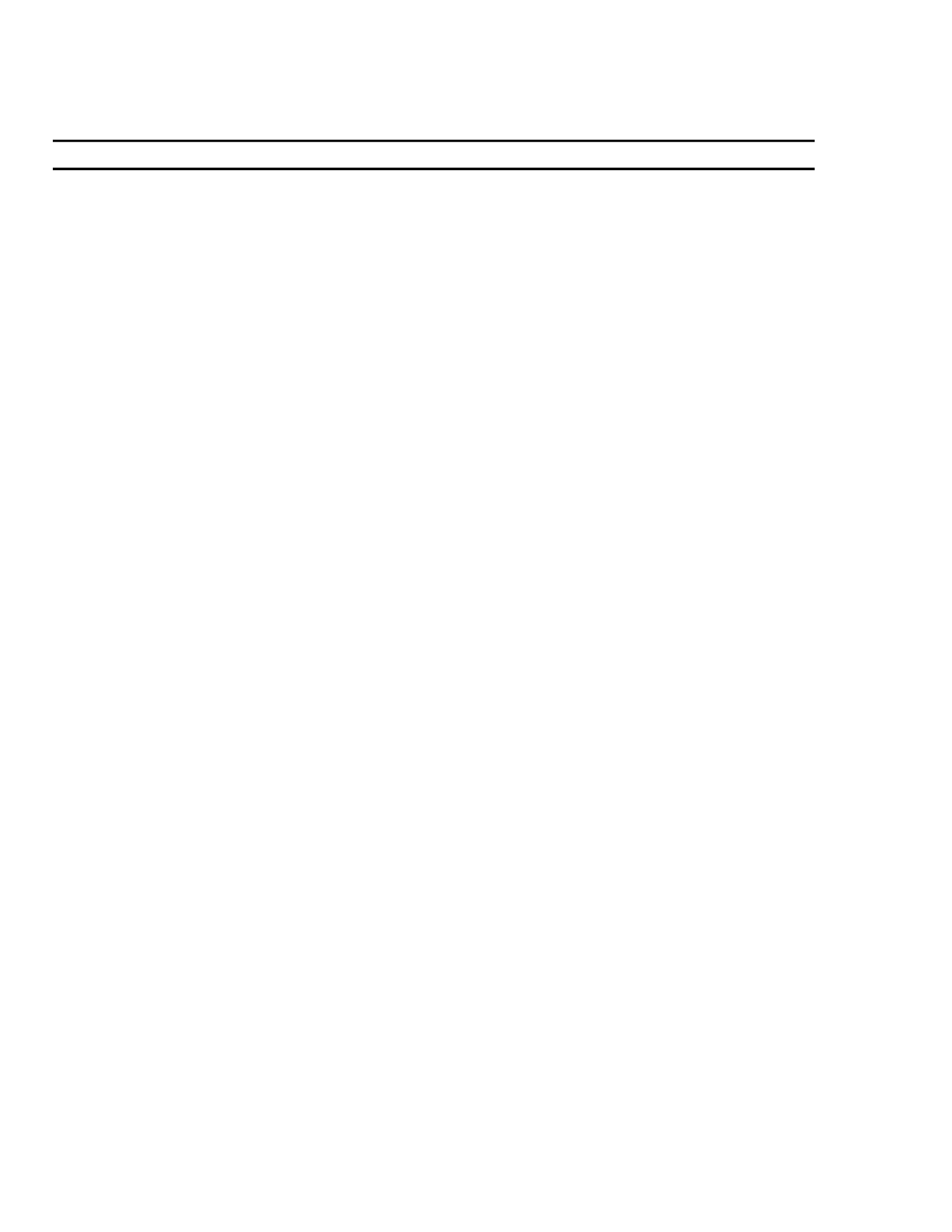
EXPLODED VIEW: EV CONBOX C5 NEXUS
DRAWING #: 0H9370
GROUP A
APPLICABLE TO:
REVISION: K-3487-G Page 7 of 8
DATE: 8/4/15
ITEM PART# QTY. DESCRIPTION
UL CIRCUIT BREAKER (LD)
A 0J2468 1 COVER CB 2P S LD6 C5
B 0D5580 1 CB 0500A 3P 600V S LD6
C 0F2353 2 INSUL CIRCUIT BREAKER JD/LD
D 0H6734 1 STANDOFF CB MOUNT CONBOX
E 022770 4 SCREW RHM 1/4-20 X 3
F 022473 4 WASHER FLAT 1/4-M6 ZINC
G 022097 4 WASHER LOCK M6-1/4
H 022127 4 NUT HEX 1/4-20 STEEL
J 0C2454 12 SCREW HWHT M6-1 X 16 N WA Z/JS
UL CIRCUIT BREAKER (LG)
A 0J2405 1 COVER CB 2P E LG C5
B 0H5674 1 CB 0500A 3P 600V E LG LL
C 0H5672A 1 INSULATOR CB E 3P LG
D 0H6734 1 STANDOFF CB MOUNT CONBOX
E 0D2157 4 SCREW SHC M6-1.0 X 50 C8.8
F 0D3700 4 NUT FLANGE M6-1.0 NYLOK
G 043107 3 SCREW HHC M8-1.25 X 25 C8.8
H 022145 6 WASHER FLAT 5/16-M8 ZINC
J 0C2454 12 SCREW HWHT M6-1 X 16 N WA Z/JS
K 022129 3 WASHER LOCK M8-5/16
L 045771 3 NUT HEX M8-1.25 G8 CLEAR ZINC
SHIELD CONTROL STAND
A
0H9612 1 SHIELD WIRING CHUTE 150KW
0J0036 1 SHIELD WIRING CHUTE 100/130 C5
0J0037 1 SHIELD WIRING CHUTE 80KW C5
B 0C2454 2 SCREW HWHT M6-1 X 16 N WA Z/JS
(1)ITEMS INCLUDED WITH HARNESS P/N 0J0372
(2)ITEMS INCLUDED WITH NEUTRAL BLOCK P/N 0D5464B
(3)SEE “C5 DPE BREAKER & FIELD BOOST RESISTOR SELECTION” TABLE
(4)QTY. REQ’D. FOR 2 POLE BREAKER/QTY. REQ’D. FOR 3 POLE BREAKER
(5) SHEET METAL PARTS LISTED IN THE BOM TABLE ARE REPRESENTING GENERIC PARTS (NO COLOR)
• MANUFACTURING: FOR CORRECT MATERIAL AND COLOR REFER TO AS400 BOM.
• CUSTOMER: WHEN ORDERING REPLACEMENT PARTS ENTER BASE NUMBER (FIRST 6 DIGITS ONLY) IN THE SYSTEM FOR
CORRECT MATERIAL AND COLOR (FOR REFERENCE SEE GUIDELINE 0H7169).
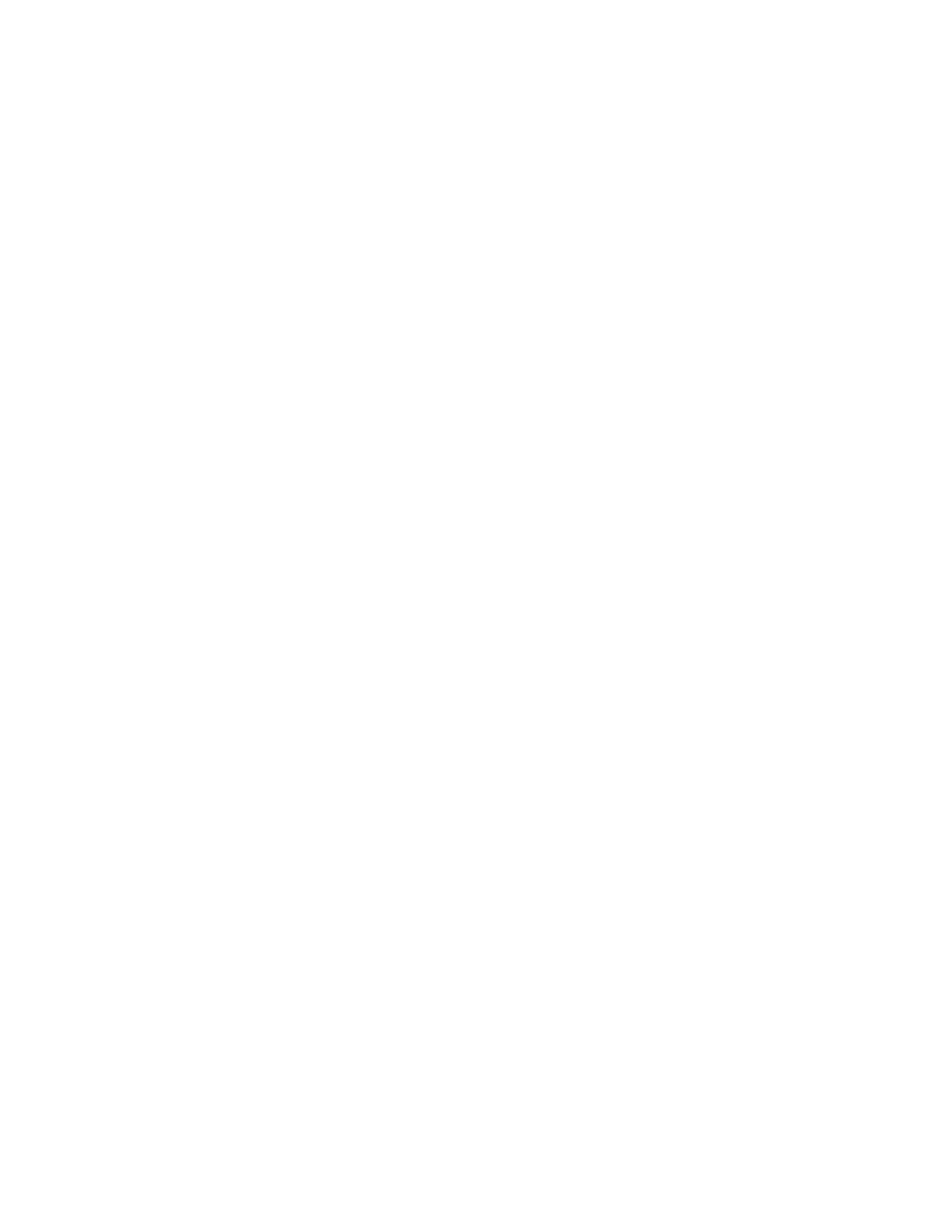
EXPLODED VIEW: EV CONBOX C5 NEXUS
DRAWING #: 0H9370
GROUP A
APPLICABLE TO:
REVISION: K-3487-G Page 8 of 8
DATE: 8/4/15
THIS PAGE LEFT INTENTIONALLY BLANK
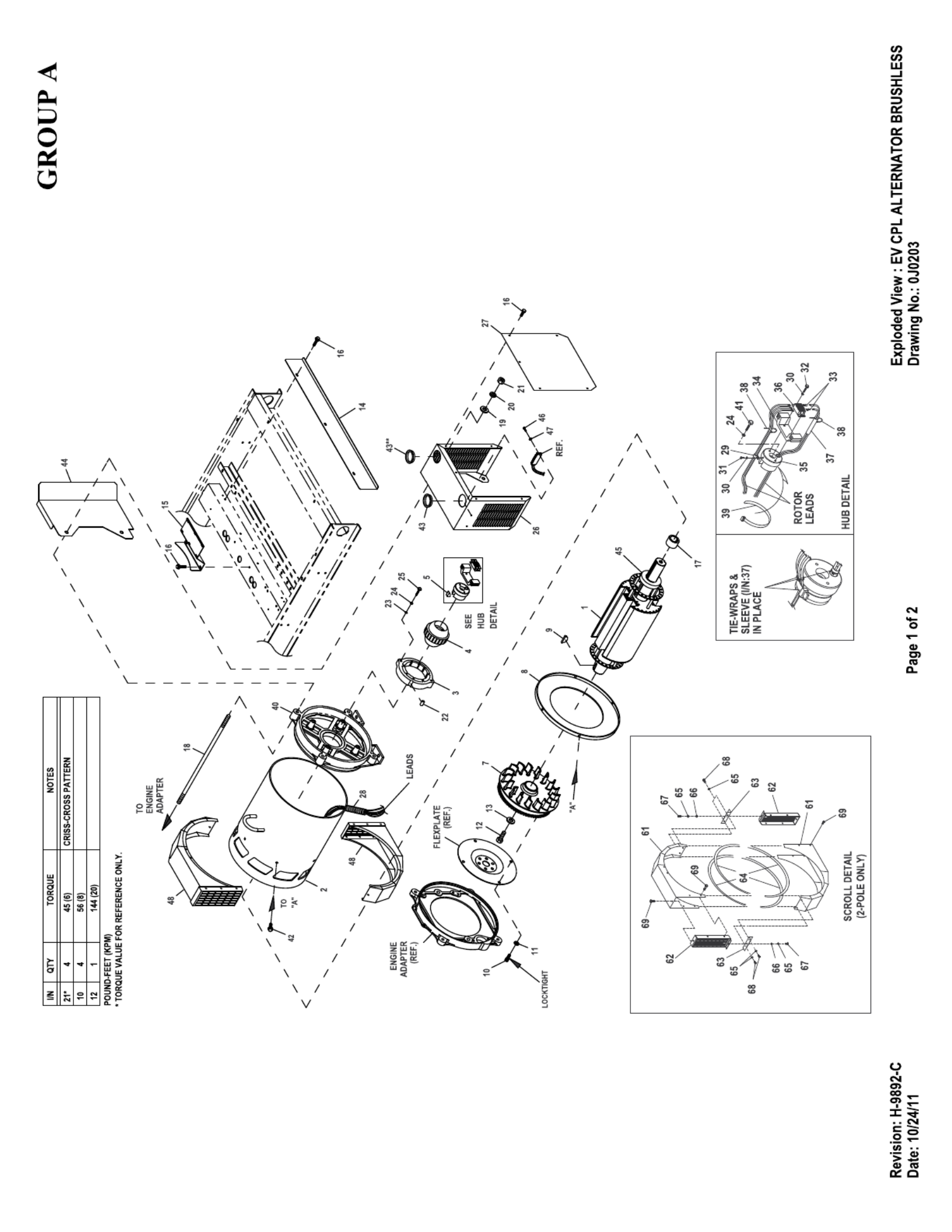
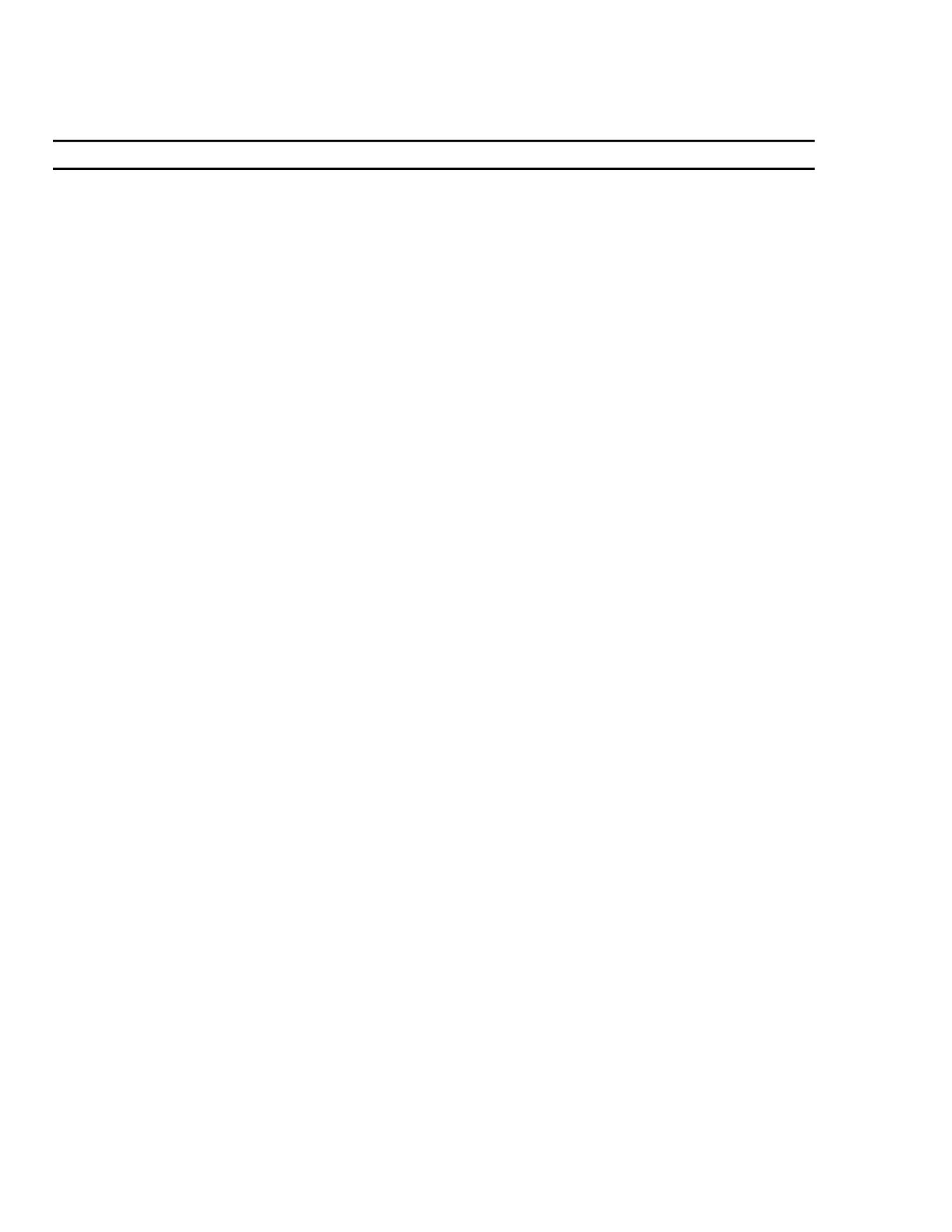
EXPLODED VIEW: EV CPL ALTERNATOR BRUSHLESS
DRAWING #: 0J0203
GROUP A
APPLICABLE TO:
REVISION: H-9892-C Page 2 of 2
DATE: 10/24/11
ITEM PART# QTY. DESCRIPTION
1 0F9952 1 ASSY ROTOR 2390 80KB3 CPL
0F2984 1 ASSY ROTOR 390 2P 150K BRSHLS
2 0F9949 1 ASSY STATOR 80KW 1PH 2P BRSHLS
0F2985 1 ASSY STATOR 390 2P 150K BRSHLS UL
0F9950 1 STATOR 2390 80 GB3 CPL
0F9951 1 STATOR 2390 80 KB3 CPL
0G6319 1 STR 2390 80 JB3 CPL
0F6184 1 ASSY STR 390 150KW 2P 3PH 208V
0F6212 1 ASSY STR 150KW 1PH 2P BRSHLS
0G2023 1 ASSY STR 390 150KW 2P 3PH 240V
3 068405C 1 EXITER FIELD 2" LG SPD CONN
4 0F3013 1 ASSY EXCITER 2.0" STACK 2P
5 072878 1 KEY SQ 3/8 X 3-1/4 STEEL
6 0C9708 REF HYPOT TEST PROCEDURE (NOT SHOWN)
7 0F3726B 1 ASSY FLYWHEEL CPL
8 0F2689 1 RING PRESSURE 390 STATOR CAN
9 023454 1 KEY WOODRUFF #E
10 059980 4 SCREW HHC M10-1.5 X 25 C10.9
11 046526 4 WASHER LOCK M10
12 0A2601 1 SCREW HHC M16-2.0 X 45 G8.8
13 072879 1 SPACER .69 X 2.75 X .37 ST/ZNC
14 0F7029 1 SHROUD LOWER ALTERNATOR EXCITR
(2)15 0J232100ST0R 1 SHIELD CENTER ALT EXCITER
16 0C2454 9 SCREW THF M6-1 X 16 N WA Z/JS
17 092950 1 COLLAR SLIP FIT 390 MM
18 04576100CF 4 STUD M14-2.0 X 760 G5 ZINC
19 052646 4 WASHER FLAT M14
20 043123 4 WASHER LOCK M14
21 051779 4 NUT HEX M14-2.0 G8 YEL CHR
22 022392 2 PIN DOWEL 1/2 X 1-1/4
23 052259 2 WASHER FLAT M12
24 051769 3 WASHER LOCK M12
25 0E7230 3 SCREW HHC M12-1.75 X 80 G10.9
26 0F9492 1 SHIELD ALT EXCITER 5.4/6.8 (1 PHASE)
27 0F2722 1 COVER EXCITER SHIELD
28 077043F 1 CONDUIT FLEX 1.25” ID
29 020151 1 CLAMP VINYL .312 X .203 Z
30 023365 3 WASHER SHAKEPROOF INT #8
31 033133 1 SCREW HHM #8-32 X 3/8
32 033143 2 SCREW HHM #8-32 X 7/8
33 086032 2 LUG RT-ANG #10/10-12
34 090063 1 BRIDGE SUPPORT DIODE 15"
35 090064 1 CAP END ROTOR 390MM
36 090152 1 ASSY BRIDGE RECTIFIER
37 022661L 1 SLEEVING UL #0 .330 ID (3” LG)
38 028739A 2 TIE WRAP UL 3.9" X .10" BLK
39 085662D 1 TIE WRAP UL 17.7 X .35 BLK HT
40 068113 1 REAR BEARING CARRIER
41 068406 1 SCREW HHC M12-1.75 X 60 G10.9
42 0F7272 6 SCREW 1/4-20 X 5/8" TAPTITE SS
43 023484N 1 BUSHING SNAP SB-2.5-31
023484N 2 BUSHING SNAP SB-2.5-31 (FOR 5.4/6.8 1 PHASE)
44 0F7030 1 SHROUD UPPER ALTERNATOR EXCITR
(1)45 052624 1 BEARING BALL 6212 SEALED
46 0C2428 2 SCREW PHTT #6-32 X 1/2 ZYC
47 022155 2 WASHER LOCK #6
48 0F3834 1 ASSY SCROLL 390 X 60MM CPL
KIT PARTS (I/N’S: 61 THRU 69)
61 0F3846B 2 SHROUD ALT SHEET METAL CPL 2P
62 0F3892 2 SCREEN, 390 SAE ALT 60MM WIDE
63 0A2496A 2 BRACKET SAE SCROLL TENSIONER
64 056326 8.4 FT. VINYL TRIM 1/8” GAP
65 022097 6 WASHER, SPLIT 1/4”-M6
66 022473 6 WASHER FLAT 1/4 ZINC
67 045757 2 SCREW HHC M6-1.0 x 25 LONG
68 047411 4 SCREW HHC M6-1.0 X 16 G8.8
69 0A2110 12 SCREW SWAGE 1/4-20 X 1/2 Z/YC
(1) ROTOR REPLACEMENT PARTS.
(2) SHEET METAL PARTS LISTED IN THE BOM TABLE ARE REPRESENTING GENERIC PARTS (NO COLOR).
•
MANUFACTURING: FOR CORRECT MATERIAL AND COLOR REFER TO AS400 BOM.
•
CUSTOMER: FOR CORRECT MATERIAL AND COLOR OF REPLACEMENT PARTS REFER TO “REPLACEMENT SHEET METAL PARTS
ORDERING GUIDE- ” INCLUDED IN THE MANUAL OR AVAILABLE ON THE GENERAC WEBSITE. 0H7169
NOTE: 1 PHASE UNITS REQUIRE SEPERATION OF LEADS.
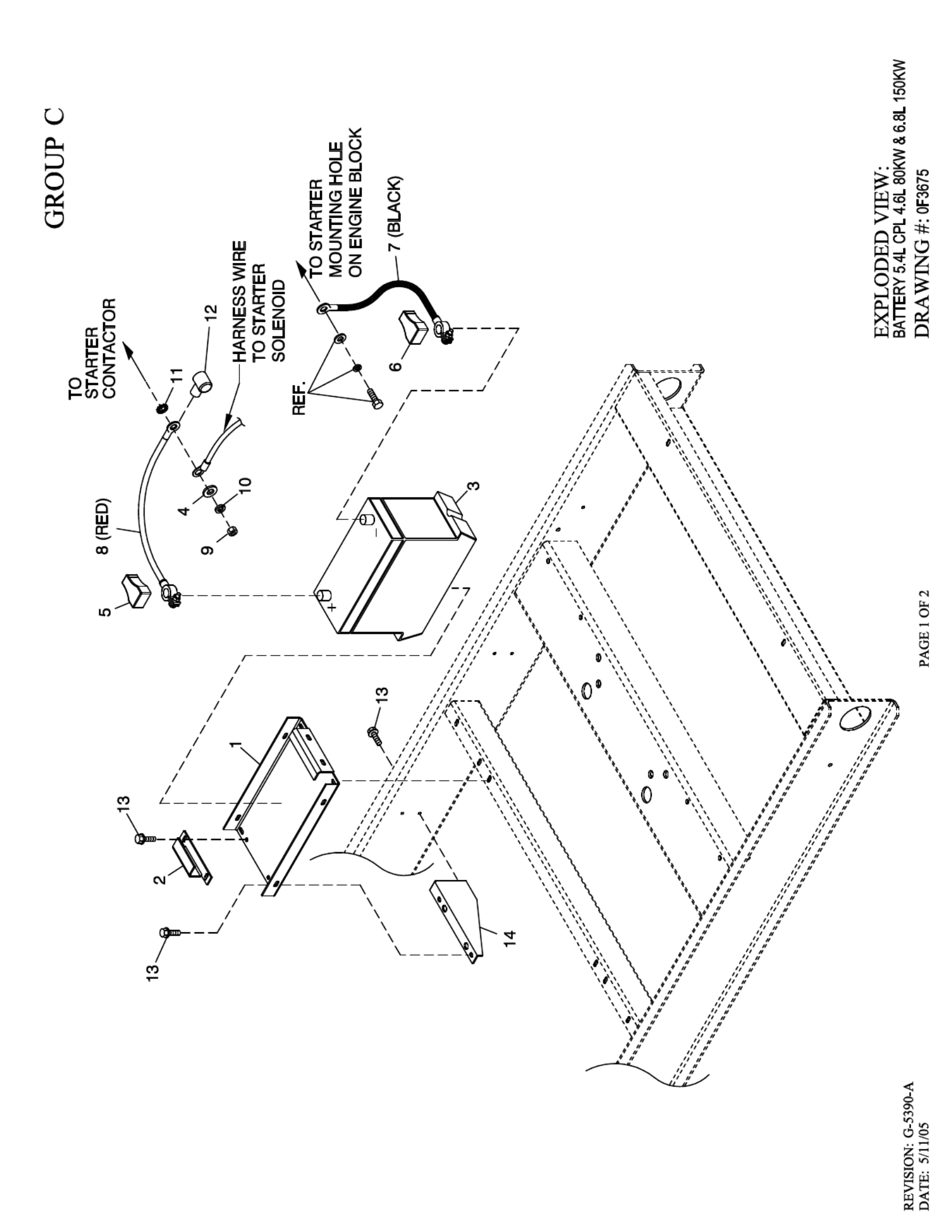
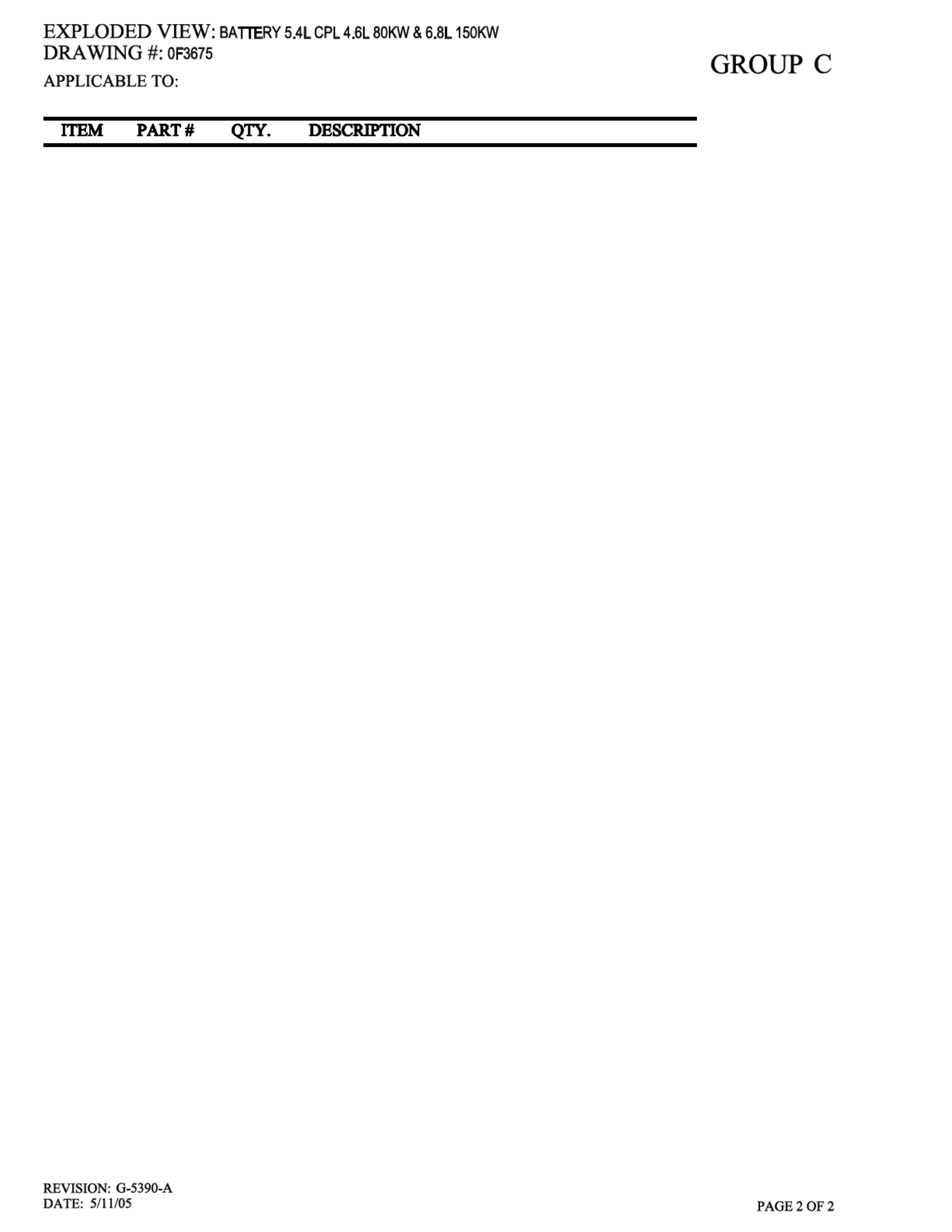
1 0F3408 1 TRAY BATTERY
2 0F3411 1 STRAP BATTERY RETAINMENT
3 058208 1 BATT 12VDC 24F 625
4 022131 1 WASHER FLAT 3/8-M10 ZINC
5 050331A 1 BATT POST COVER RED +
6 050331 1 BATT POST COVER BLK -
7 038805U 1 CABLE BATT BLK #1 X 18.00
8 038804U 1 CABLE BATT RED #1 X 28.00
9 045771 1 NUT HEX M8-1.25 G8 YEL CHR
10 022129 1 WASHER LOCK M8-5/16
11 027482 1 WASHER SHAKEPROOF EXT 5/16 STL
12 075763 1 BOOT BATTERY CABLE
13 0C2454 8 SCREW THF M6-1X16 N WA Z/JS
14 0F3409 1 SUPPORT BATTERY TRAY
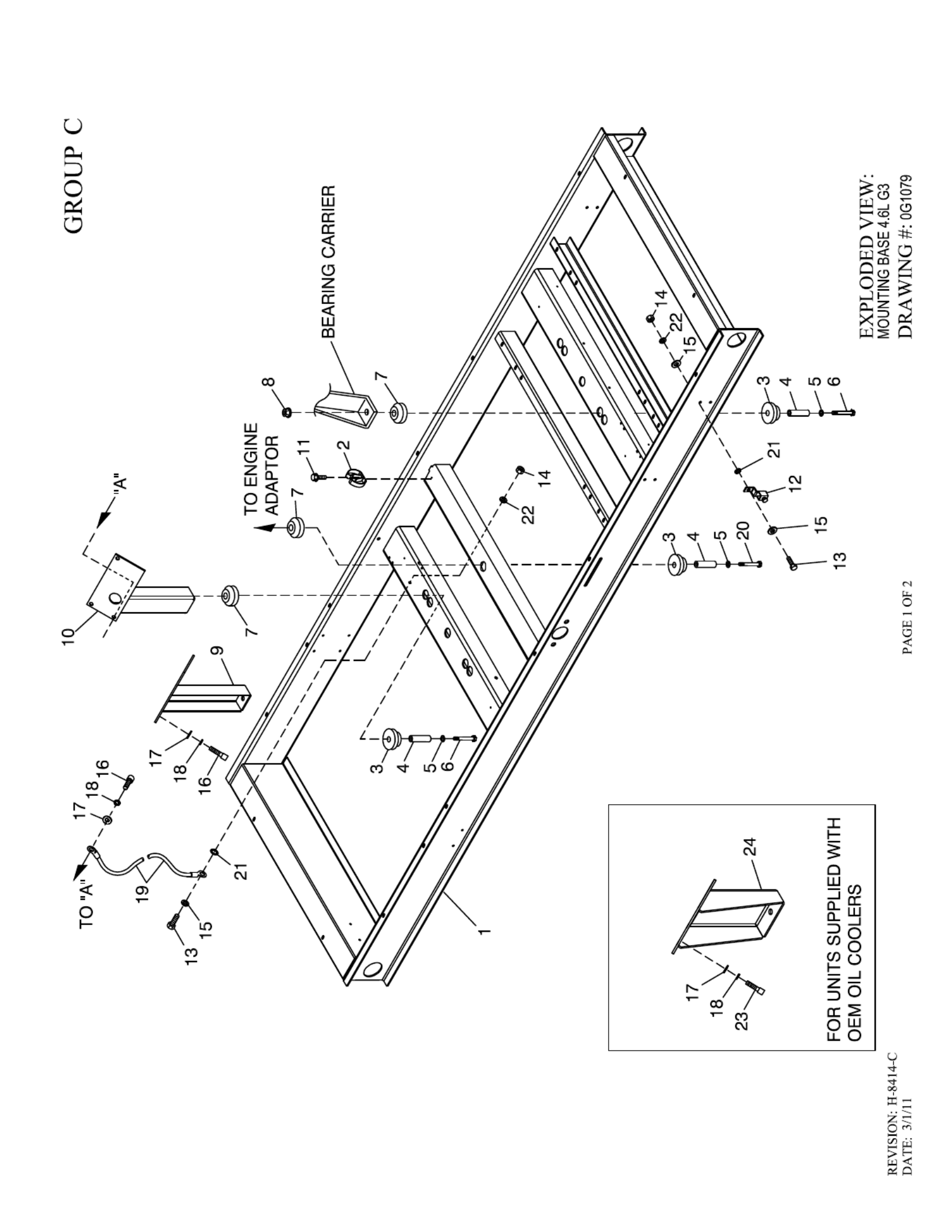
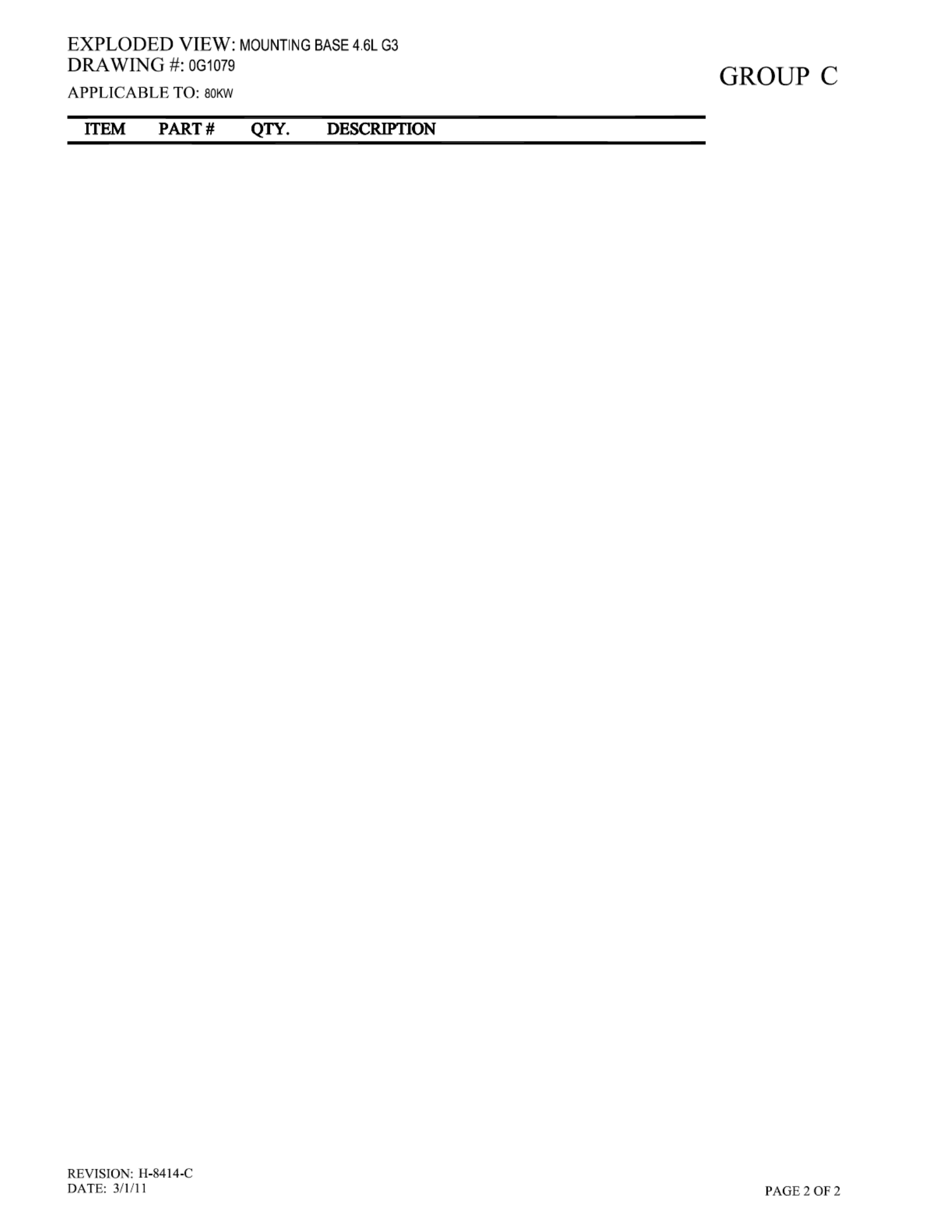
1 0F30990ST03 1 MTG BASE C5 4.6/80KW 5.4/100KW
2 065852 1 SPRING CLIP HOLDER .37-.62
3 052252 5 DAMPENER VIBRATION
4 052257 5 SPACER .49 X .62 X 1.87 PWDR/ZINC
5 052259 5 WASHER FLAT M12
6 055597 4 SCREW HHC M12-1.75 X 85 G8.8
7 052251A 5 DAMPENER VIBRATION 50 WHITE
8 052860 4 NUT LOCKING M12-1.75
9 0F8864 1 SUPPORT ENG 4.6L LH
10 0F8865 1 SUPPORT ENG 4.6L RH
11 045764 1 SCREW HHTT M4-0.7 X 8 BP
12 061383 1 LUG SOLDERLESS 3/0-#4 X 13/32 CU
13 045757 2 SCREW HHC M6-1.0 X 25 G8.8
14 049813 2 NUT HEX M6 X 1.0 G8 YEL CHR
15 022473 3 WASHER FLAT 1/4-M6 ZINC
16 057192 6 SCREW SHC M10-1.5 X 30 G12.9
17 022131 6 WASHER FLAT 3/8-M10 ZINC
18 046526 6 WASHER LOCK M10
19 0536210410 1 ASSY WIRE 14.00”
20 0E7230 1 SCREW HHC M12-1.75 X 80 G10.9
21 027482 2 WASHER SHAKEPROOF EXT 5/16 STL
22 022097 2 WASHER LOCK M6-1/4
23 090502 3 SCREW SHC M10-1.5 X 60 C12.9
24 0J45320ST03 1 SUPPORT ENGINE LH
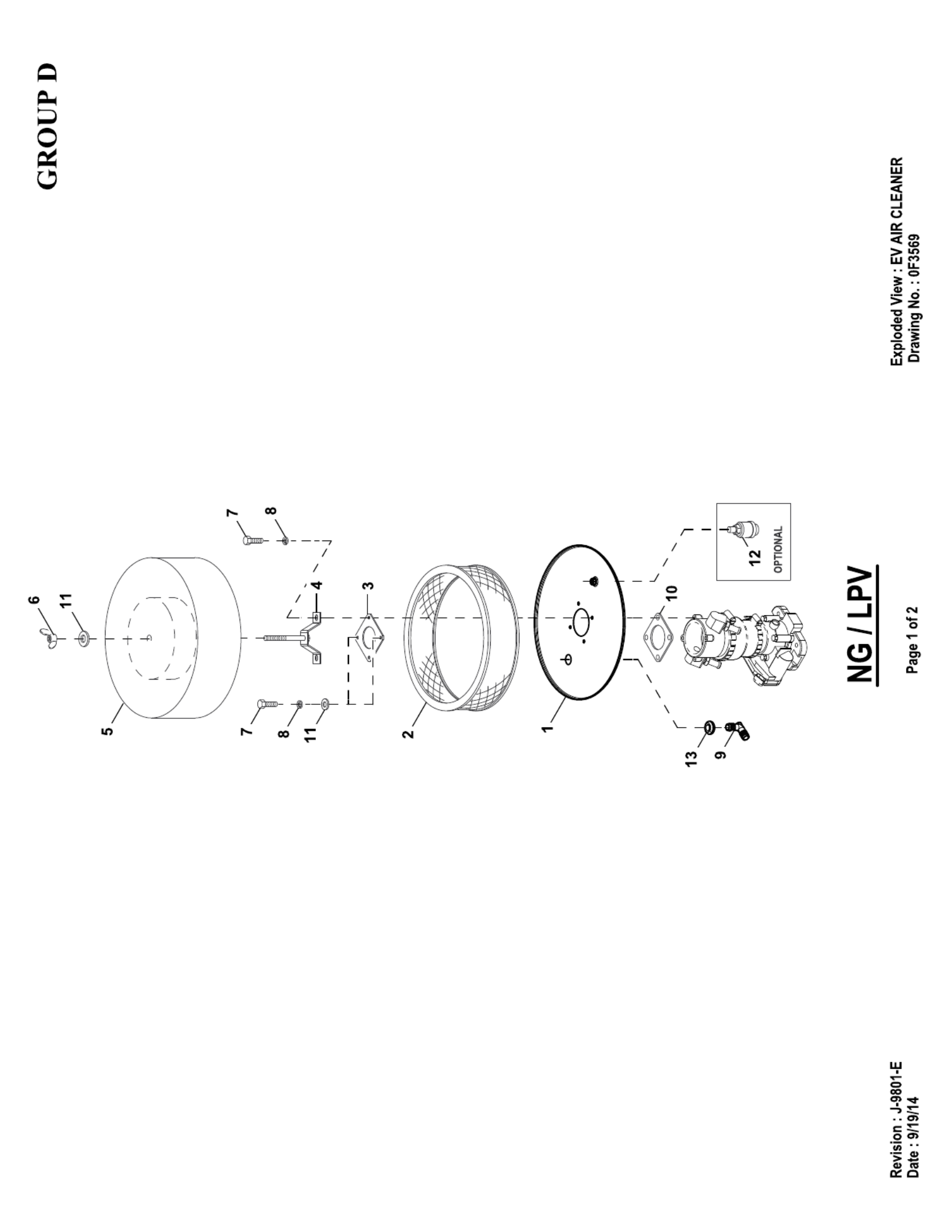
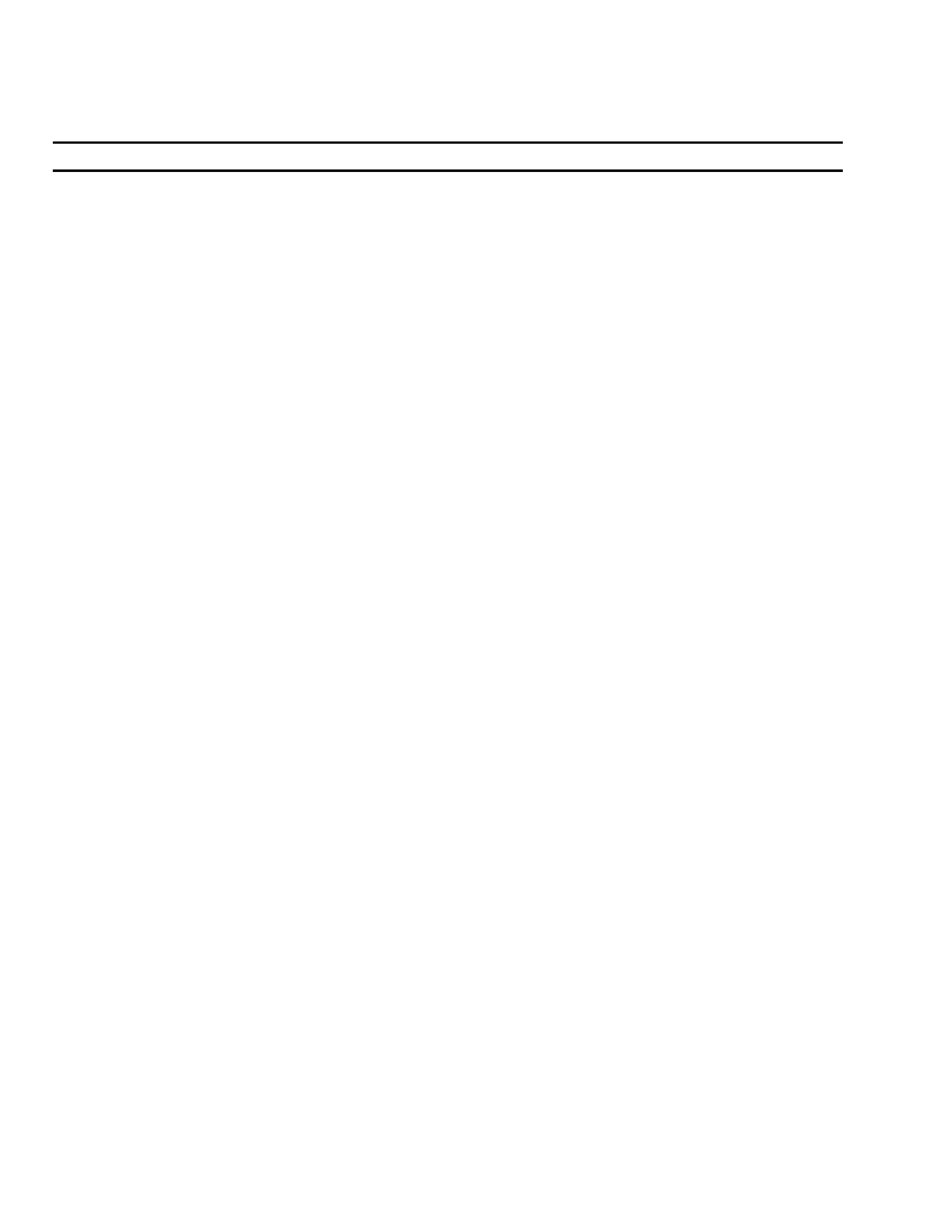
EXPLODED VIEW: EV AIR CLEANER
DRAWING #: 0F3569
GROUP D
ITEM PART# QTY. DESCRIPTION
REVISION: J-9801-E Page 2 of 2
DATE: 9/19/14
1 0D2513D 1 AIR CLNR BTM PLT W/CPLR 8.1L
0D2513E 1 PLATE AIR CLEANER W/COUPLER
2 0F5419 1 ELEMENT AIR FILTER
3 0F4268 1 TOP PLATE VENTURI
4 0F4270A 1 HOLD DOWN AIR CLEANER PLATED
5 0F6977 1 PLATE AIR CLEAN TOP 5.4L/6.8L
6 037561 1 NUT WING 1/4-20 NYLK
7 047411 4 SCREW HHC M6-1.0 X 16 G8.8
8 022097 4 WASHER LOCK M6-1/4
9 057795B 1 BARBED EL 90 5/8 PLASTIC
10 0F4269 1 GASKET MIXER BODY
11 022473 3 WASHER FLAT 1/4-M6 ZINC
12 0A4256 1 INDICATOR FILTER MINDER (USE WITH ITEM #1 P/N 0D2513E)
13 0G5954 1 GROMMET .625 X 1.25 X .433
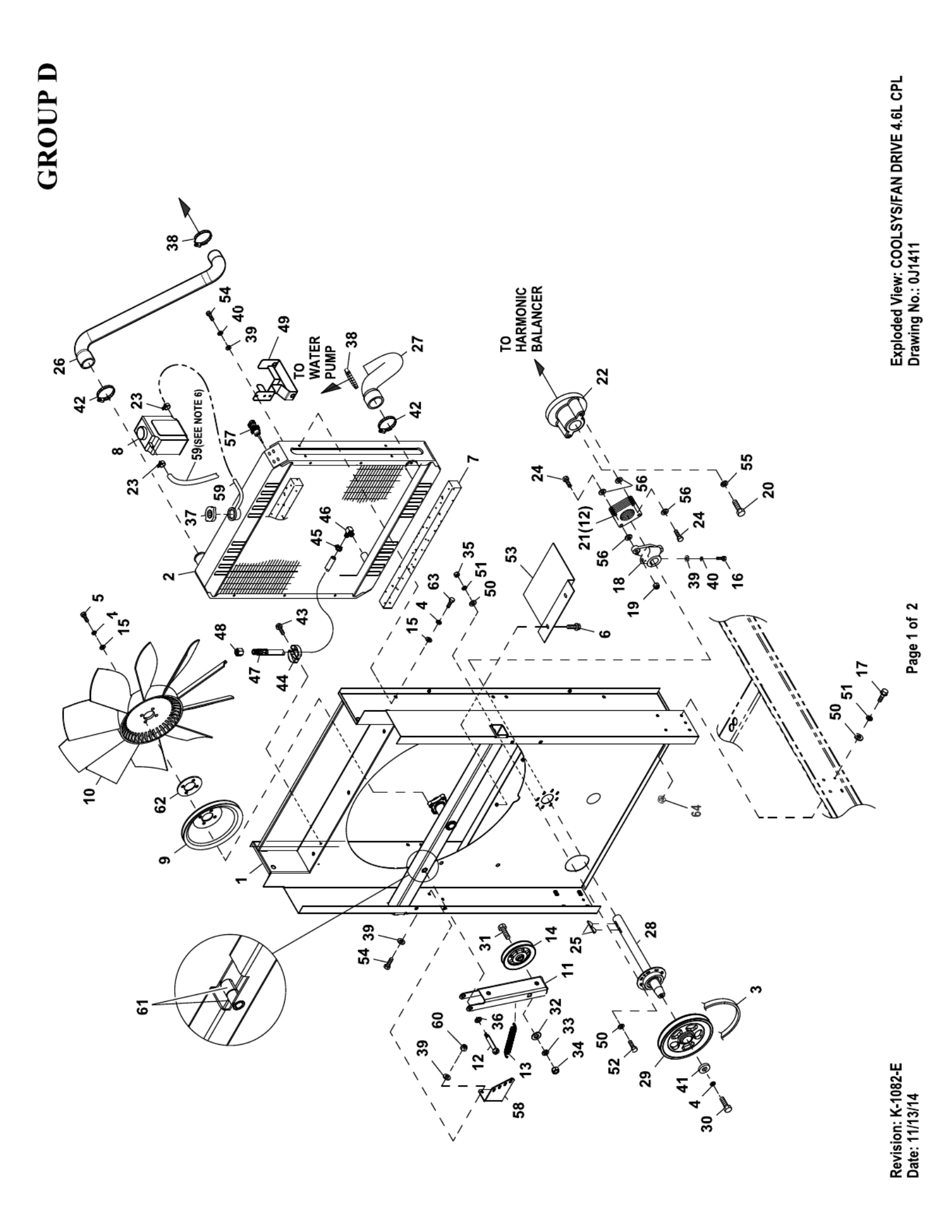
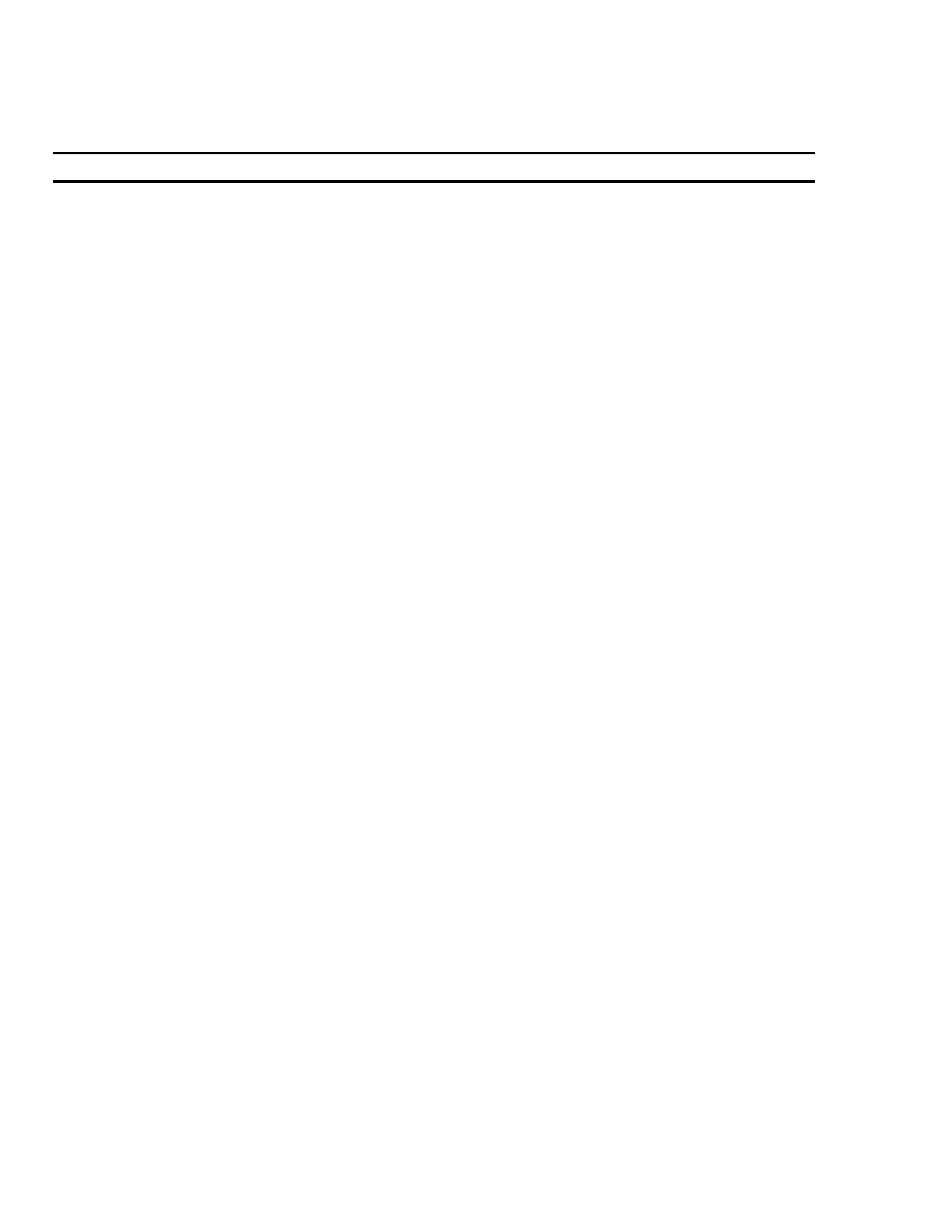
EXPLODED VIEW: COOLSYS/FAN DRIVE 4.6L CP
DRAWING #: 0J1411
GROUP D
APPLICABLE TO:
ITEM PART# QTY. DESCRIPTION
REVISION: K-1082-E Page 2 of 2
DATE: 11/13/14
(4)1 0J01150ST0R 1 WELDMENT RADIATOR SUPPORT C5
2 0F2611 1 RADIATOR 680 X 680 X 70 CPL
3 0F5254 1 V-BELT 31/64" X 62-3/8"
4 046526 9 WASHER LOCK M10
(2)5 059981 4 SCREW HHC M10-1.5 X 30 C10.9
6 0C2454 2 SCREW THF M6-1 X 16 N WA Z/JS
7 052250 2 TAPE FOAM 1 X 1 (26.75” LG)
8 076749 1 TANK COOLANT RECOVERY
9 0F2573 1 PULLEY FAN V-GROOVE 9"
10 0F2610 1 FAN 26" LH ROTATION
(4)11 0H20620ST0R 1 ARM BELT TENSIONER
(2)12 0H2051 1 SHOULDER BOLT 1/2 X 2-1/4"
13 0F2862 1 SPRING TENSION CPL
14 0F2560 1 PULLEY V-BELT 4" FLANGED
15 022131 8 WASHER FLAT 3/8-M10 ZINC
(2)16 039287 1 SCREW HHC M8-1.25 X 45 C8.8
17 0C8566 8 SCREW HHFC M6-1.0 X 20 G8.8
18 0F2561 1 HUB FLEX PLATE
19 0C8165 2 NUT HEX LOCK 5/16-24 NY INS
(2)20 0D6795 1 SCREW HHC M12-1.5 X 60 G8.8
21 0C7043 12 DISK FLEX
22 0H5380 1 COUPLING FLEX HUB MACHINED
23 048031C 2 CLAMP HOSE BAND 1/4
(2)24 0C8146 4 SCREW HHC 5/16-24 X 1.124
25 082774 2 KEY WOODRUFF 4 X 19D
26 0H3909 1 HOSE RADIATOR UPPER C5 CPL
(5) 0F2686 1 HOSE, RADIATOR UPPER, CPL
27 0H3908 1 HOSE RADIATOR LOWER C5 CPL
(5) 0F5463 1 HOSE LOWER RAD CPL C5 6.8L
28 0F8695 1 ASSY BRG/SHAFT CPL FANDRIVE
29 0F4032 1 PULLEY 5.5" DIA MACHINED
(2)30 042911 1 SCREW HHC M10-1.5 X 30 G8.8
31 0F2872 1 SCREW HHC 1/2-13 X 2" G8
32 022304 1 WASHER FLAT 1/2 ZINC
33 022195 1 WASHER LOCK 1/2
34 022196 1 NUT HEX 1/2-13 STEEL
35 049813 8 NUT HEX M6 X 1.0 G8 YEL CHR
36 052677 1 WASHER NYLON .50 X .87 X .06
37 090283 1 CAP RADIATOR 13 PSI
38 099502 2 CLAMP HOSE #24 B1.06-2.00
39 022145 4 WASHER FLAT 5/16-M8 ZINC
40 022129 2 WASHER LOCK M8-5/16
41 052644 1 SPACER .5 X 1.5 X .25 STL/ZINC
42 035685 2 CLAMP HOSE #28 1.32-2.25
43 045764 1 SCREW HHTT M4-0.7 X 8 BP
44 065852 1 SPRING CLIP HOLDER .37-.62
45 0C7649 1 CLAMP HOSE .38-.87
46 043790 1 BARBED EL 90 3/8 NPT X 3/8
47 069860E 1 HOSE DRAIN ASSY 28"
(1)48 069811 REF CAP HEX 1/4 NPT BRASS
49 0L01050ST0R 1 BRACKET COOLANT TANK
50 022473 24 WASHER FLAT 1/4-M6 ZINC
51 022097 16 WASHER LOCK M6-1/4
52 042568 8 SCREW HHC M6-1.0 X 20 G8.8
53 0F5050B 1 SHIELD RADIATOR
54 039253 3 SCREW HHC M8-1.25 X 20 G8.8
55 051769 1 WASHER LOCK M12
56 0C8145 8 WASHER FLEX (THIN)
57 0H1827 1 PROBE COOLANT LEVEL 3/8-18NPTF
(4)58 0H23980ST0R 1 BRACKET TENSIONER SPRING
59 029032 2 HOSE 9/32 ID (43”LG)
60 049820 2 NUT HEX LOCK M8-1.25 NY INS
(3)61 0H2844 2 (REF) BEARING SLEEVE 1/2/ X 3/4 X 1
(4)62 0G53150AL0R 1 SPACER CPL COOLING FAN 1/8"
63 051756 4 SCREW HHC M10-1.5 X 20 C8.8
64 0D3700 8 NUT FLANGE M6-1.0 NYLOK
65 085662 3 TIE WRAP UL 14.6 X .14 BLK (NOT SHOWN)
(1) ITEM 48 IS INCLUDED WITH 47.
(2) APPLY MEDIUM STRENGTH BLUE THREAD LOCKING FLUID TO THREADS.
(3) ITEM 61 IS INCLUDED WITH ITEM 1.
NOTES (UNLESS OTHERWISE SPECIFIED):
(1) SHEET METAL PARTS LISTED IN THE BOM TABLE ARE REPRESENTING GENERIC PARTS (NO COLOR)
• MANUFACTURING: FOR CORRECT MATERIAL AND COLOR REFER TO XA BOM.
• CUSTOMER: WHEN ORDERING REPLACEMENT PARTS ENTER BASE NUMBER (FIRST 6 DIGITS ONLY) IN THE SYSTEM FOR
CORRECT MATERIAL AND COLOR (FOR REFERENCE SEE GUIDELINE 0H7169).
(5) USED ONLY ON ENGINES WITH OEM OIL COOLER.
(6) FASTEN HOSE TO RADIATOR SUPPORT USING TIE WRAP I/N 65. DIRECT HOSE TOWARD BASE OF UNIT AND AWAY FROM
EXHAUST COMPONENTS.
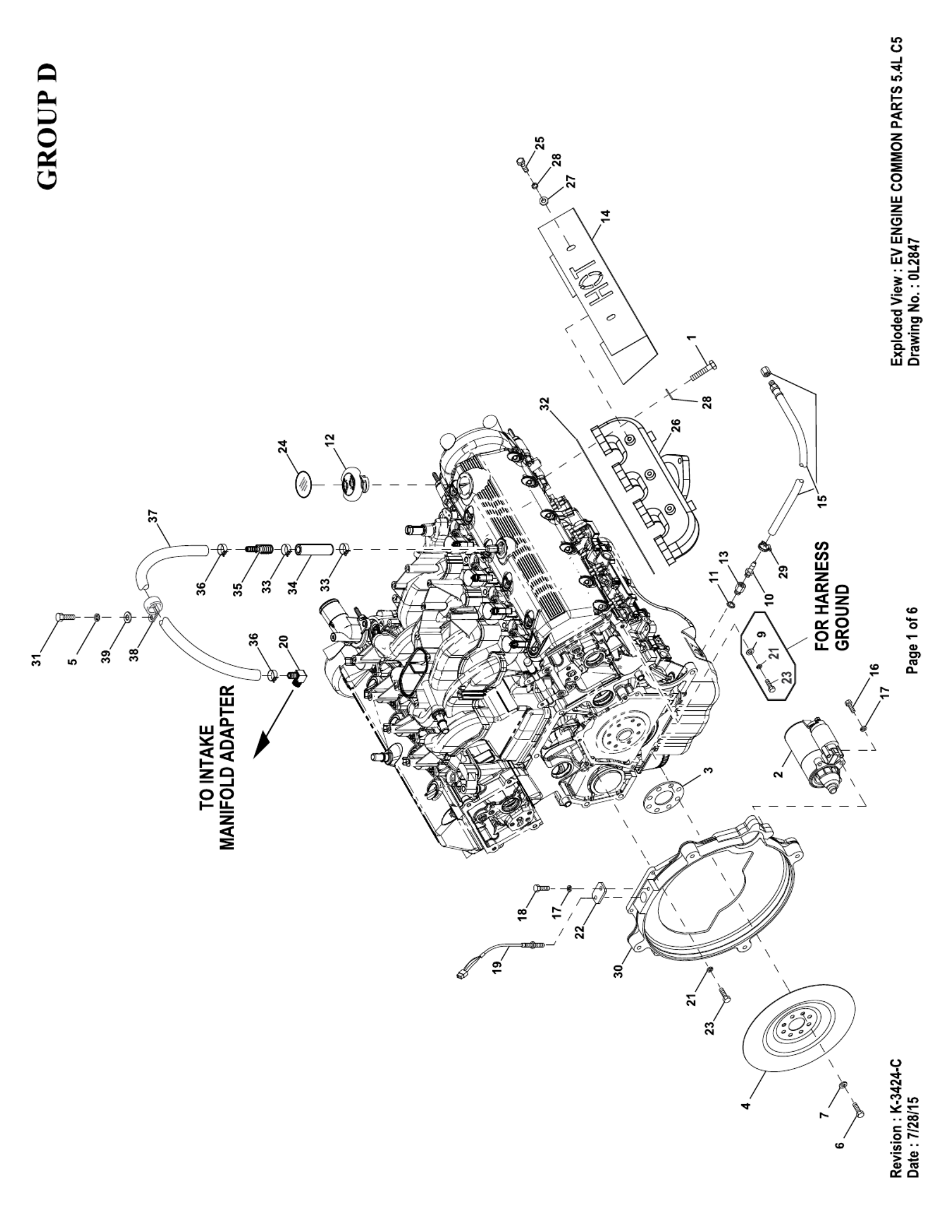
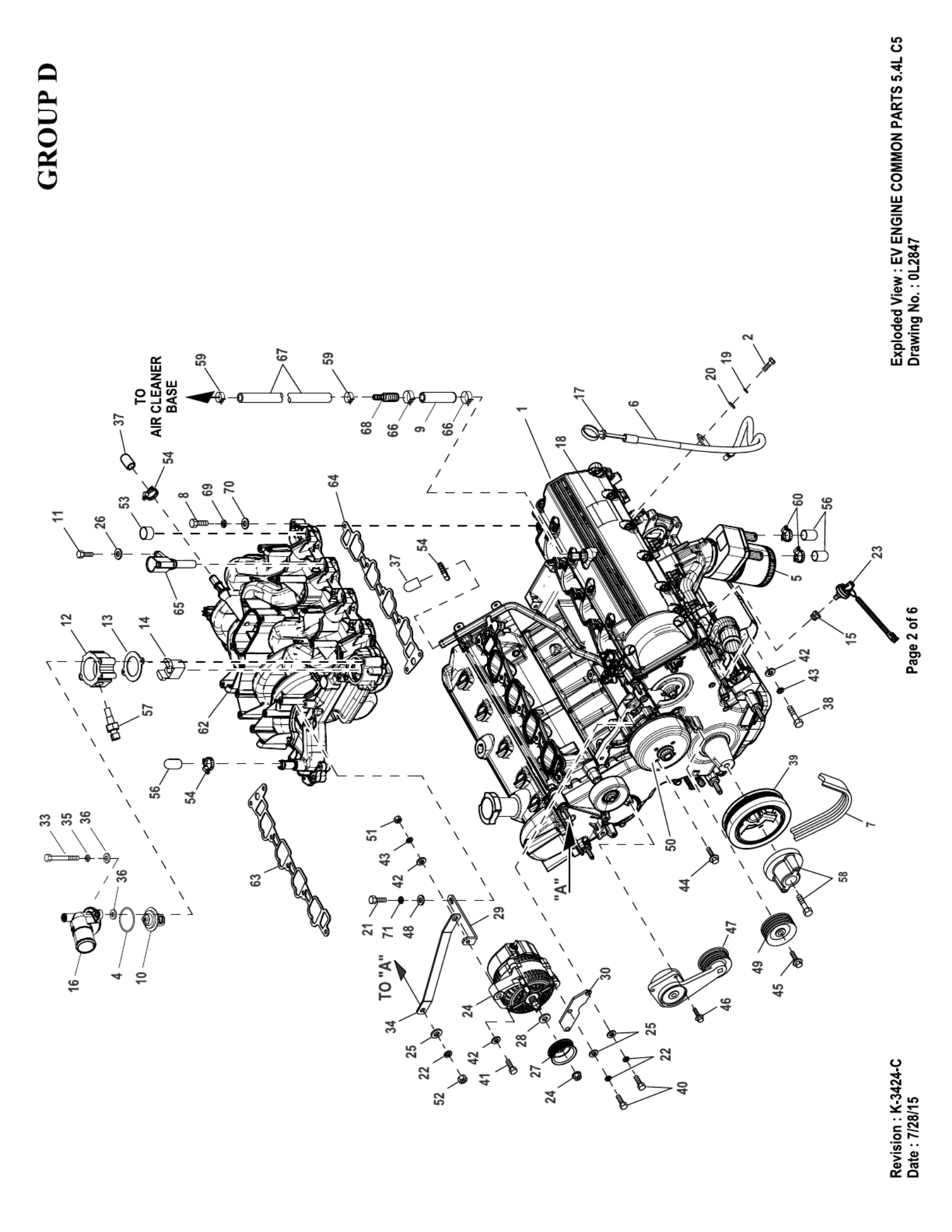
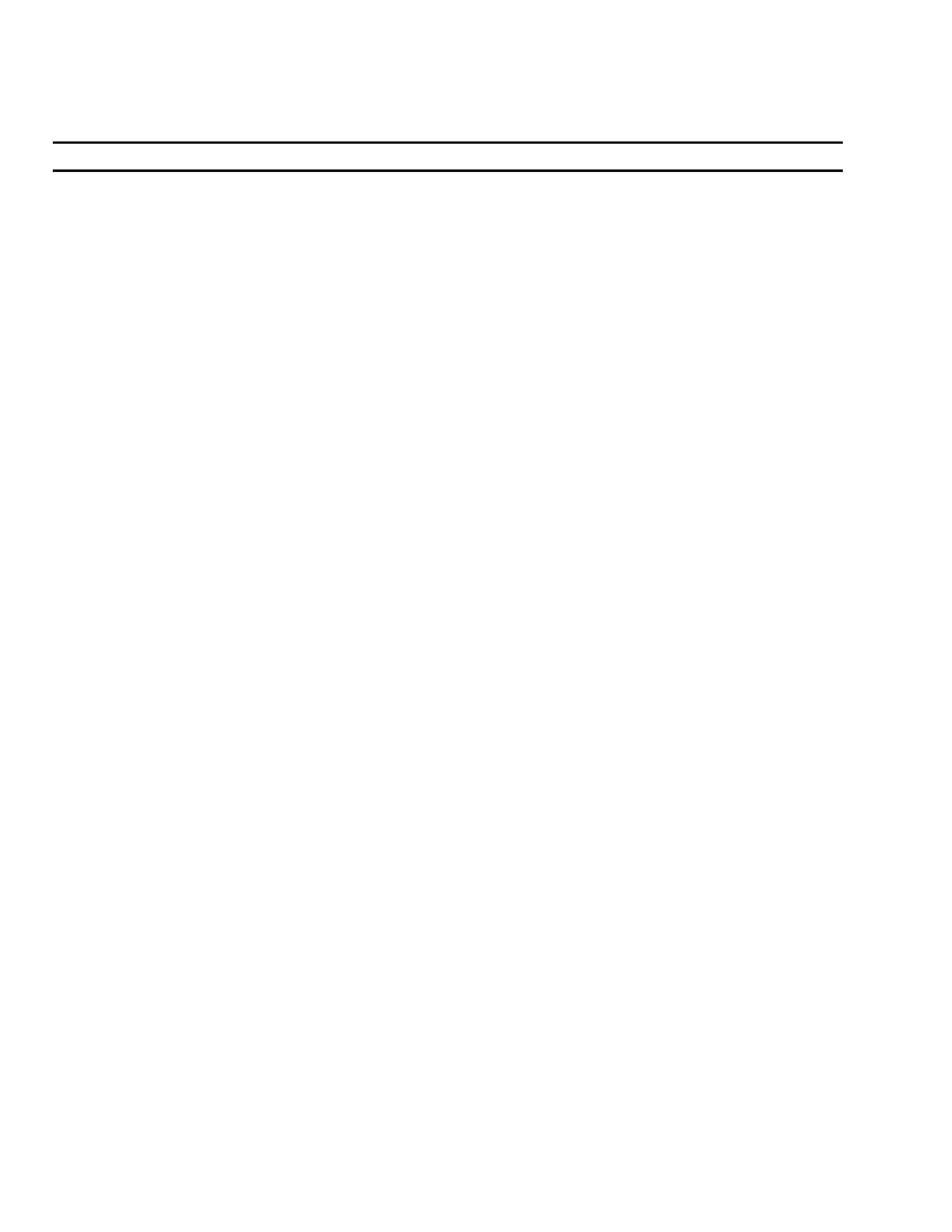
EXPLODED VIEW: EV ENGINE COMMON PARTS 5.4L C5
DRAWING #: 0L2847
GROUP D
ITEM PART# QTY. DESCRIPTION
REVISION: K-3424-C Page 3 of 6
DATE: 7/28/15
PAGE 1
1 0D9913 16 SCREW SHC M8-1.25 X 35 SS
2 0G7461 1 STARTER MOTOR 12V
3 0F3514 1 SPACER FLEXPLATE 5.4L/6.8L
4 0F9965C 2 FLEX PLATE 2 POLE 5.4L/6.8L
5 022097 1 WASHER LOCK M6-1/4
6 0D5417 8 SCREW HHC M10-1.0 X 25 G10.9
7 0A5768 8 WASHER FLAT M10 HEAVY DUTY
8 029333A 1 TIE WRAP UL 7.4" X .19" BLK (NOT SHOWN)
9 022131 1 WASHER FLAT 3/8-M10 ZINC
10 055596 1 BARBED STR 3/8 NPT X 3/8
11 057772 1 WASHER NYLON .565
12 0F7316C150 1 CAP, OIL FILLER
13 057765 1 ADAPTER M14-1.50 X 3/8 NPTA
14 0F3534 2 HEAT SHLD EXHAUST MANIFOLD
15 069860E 1 HOSE DRAIN ASSY 28"
16 049821 2 SCREW SHC M8-1.25 X 30 G12.9
17 022129 4 WASHER LOCK M8-5/16
18 039253 1 SCREW HHC M8-1.25 X 20 G8.8
19 0D2244M 1 ASSY MAGPICKUP(3/8-24 MALE)
20 049340 1 BARBED EL 90 1/4NPT X 3/8
21 046526 6 WASHER LOCK M10
22 0F5454 1 PLATE MAG PICK-UP ADAPTOR
23 071623 4 SCREW SHC M10-1.5 X 55 G12.9
24 0F5114 1 DECAL REFER TO OWNERS MANUAL
25 0D2608 8 SCREW HHC 5/16-18 X 1/2 SSTL
26 0F1820 2 MACHINED MANIFOLD EXHAUST 5.4L
27 070008 8 WASHER FLAT M8 SS
28 070006 24 WASHER LOCK M8 SSTL
29 0C7649 1 CLAMP HOSE .38-.87
30 0F2929 1 ENGINE ADAPTER 5.4L/6.8L
31 047411 1 SCREW HHC M6-1.0 X 16 C8.8
32 0F5755 2 GASKET, EXHAUST MANIFOLD
33 048031P 2 CLAMP HOSE BAND .88"
34 0G0321 1 HOSE COOL 5/8"ID 250#WP (2” LG)
35 0G1462 1 HOSE BARB REDUCER 5/8"-3/8"ID
36 048031J 2 CLAMP HOSE BAND .63
37 047290 1 HOSE 3/8 ID SINGLE BRAID (15” LG)
38 055934M 1 CLAMP STL/VNL .75 X .343 Z
39 022473 1 WASHER FLAT 1/4-M6 ZINC
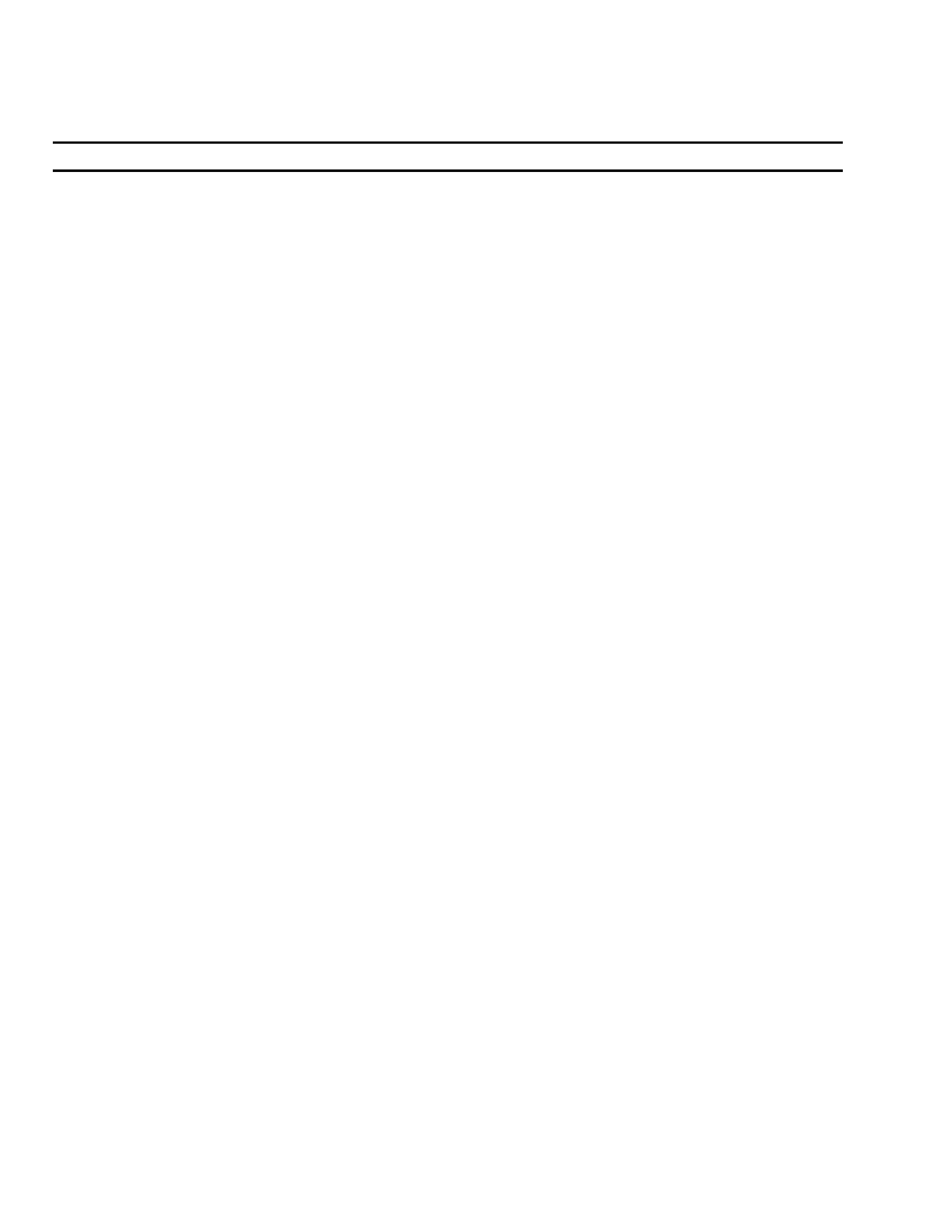
EXPLODED VIEW: EV ENGINE COMMON PARTS 5.4L C5
DRAWING #: 0L2847
GROUP D
ITEM PART# QTY. DESCRIPTION
REVISION: K-3424-C Page 4 of 6
DATE: 7/28/15
PAGE 2
1 0J6240 1 5.4L G3 - LONG BLOCK
2 042568 1 SCREW HHC M6-1.0 X 20 C8.8
4 0F2843 1 GASKET THERMOSTAT HOUSING
5 0D5419 REF OIL FILTER V-10 ENGINE
6 0J7906 1 DIPSTICK G5.4L G3
7 0D3488K 1 BELT SERPENTINE 68.3"
8 051731 9 SCREW HHC M8-1.25 X 50 C8.8
9 0G0321 1 HOSE COOL 5/8"ID 250#WP (2” LG)
10 0J6240E 1 5.4L G3 - THERMOSTAT
11 055440 8 SCREW HHC M5-0.8 X 25 C8.8 BLK
12 0G5515B 1 ADAPTER THERMOSTAT 4.6L G3
13 0G5511 1 GASKET THERMOSTAT 4.2L
14 0H3920 1 SPACER COOLANT BYPASS
15 035579 1 BSHG RDCR HEX 1/4 TO 1/8
16 0J6240F 1 5.4L G3 - THERMOSTAT OUTLET
17 0F7316C160 1 DIPSTICK
18 0H0550 1 DECAL EPA STATIONARY EMERGENCY
19 022097 1 WASHER LOCK M6-1/4
20 022473 1 WASHER FLAT 1/4-M6 ZINC
21 042568 1 SCREW HHC M6-1.0 X 20 C8.8
22 022129 5 WASHER LOCK M8-5/16
23 0H7435 1 HARN LOW OIL PRESS SWITCH ASSY
24 0E9868A 1 ALTERNATOR DC W/OUT PULLEY
25 022145 5 WASHER FLAT 5/16 ZINC
26 051713 8 WASHER FLAT M5
27 0F3216D 1 PULLEY 160 OD DC ALTERNATOR (3600 RPM)
28 0F3217 1 SPACER DC ALTERNATOR PULLEY
29 0F3287 1 BRKT DC ALTERNATOR UPPER
30 0F3017 1 BRKT DC ALTERNATOR LOWER
(1)31 0L3020 1 HARN ENG G5.4L G3 NEXUS
33 0G5148 2 SCREW HHC M8-1.25 X 140 G8.8
34 0F4308 1 BRACKET DC ALT STABILIZER
35 022129 2 WASHER LOCK M8-5/16
36 022145 4 WASHER FLAT 5/16-M8 ZINC
37 077996 2 CAP ANTIFREEZE 5/8"ID X 1.2"LG
38 052243 1 SCREW HHC M10-1.5 X 60 C8.8
39 0H5406A 1 REWORK HARMONIC BALANCER 5.4L
40 039253 3 SCREW HHC M8-1.25 X 20 G8.8
41 064416 1 SCREW HHC M10-1.5 X 45 G8.8 FT
42 022131 3 WASHER FLAT 3/8-M10 ZINC
43 046526 2 WASHER LOCK M10
44 0D8027 4 SCREW WP PULLEY M8-1.25 X 19
45 0D8025 1 BOLT HEX FL HD M8-1.25 X 28
46 0D8026 3 BOLT HEX FL HD M8-1.25 X 31
47 0D8030 1 TENSIONER ENG. AUTOMATIC BELT
48 022473 1 WASHER FLAT 1/4-M6 ZINC
49 0D8028 1 PULLEY GROOVED ENGINE IDLER
50 0F2846 1 PULLEY WATER PUMP G3
51 045772 1 NUT HEX M10-1.5 G8 YEL CHR
52 045771 1 NUT HEX M8-1.25 G8 YEL CHR
53 0E0992A 8 PLUG EXPANSION 14 OD
54 057823 3 CLAMP HOSE #10 .56-1.06
(1)55 029333A 2 TIE WRAP UL 7.4" X .19" BLK
(1)56 0F6151 3 CAP RUBBER
57 0E0502 1 TEMPERATURE SENDER, DELPHI
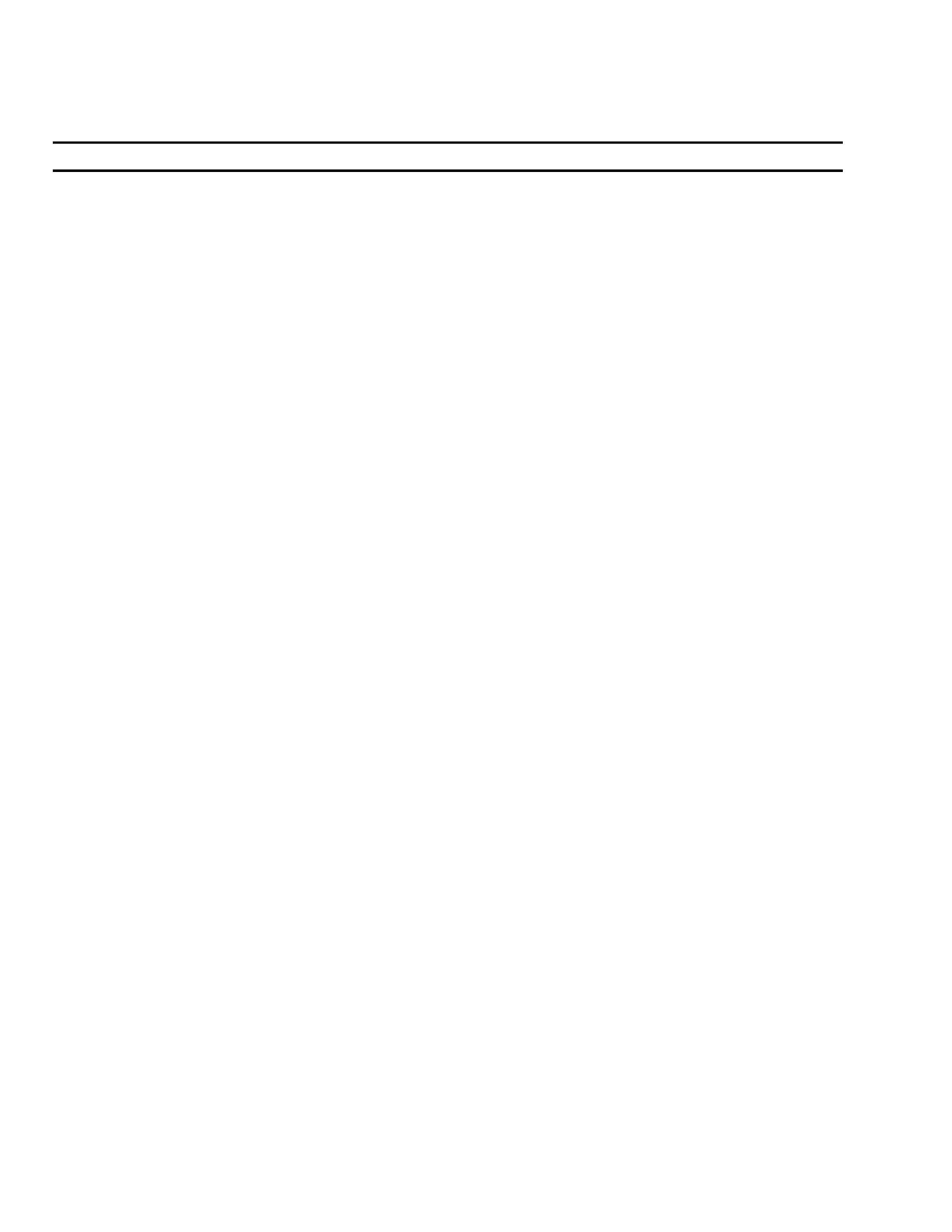
EXPLODED VIEW: EV ENGINE COMMON PARTS 5.4L C5
DRAWING #: 0L2847
GROUP D
ITEM PART# QTY. DESCRIPTION
REVISION: K-3424-C Page 5 of 6
DATE: 7/28/15
58 REF 1 COUPLING FLEX HUB MACH
59 048031J 2 CLAMP HOSE BAND .63
60 035473 2 CLAMP HOSE #12 .50-1.25
62 0J6240B 1 5.4L G3 - INTAKE MANIFOLD
63 0J6240C 1 5.4L G3 - INTAKE GASKET RH
64 0J6240D 1 5.4L G3 - INTAKE GASKET LH
65 0F2842 8 COIL & BOOT ASY-IGNITION
66 048031P 2 CLAMP HOSE BAND .88"
67 047290 1 HOSE 3/8 ID SINGLE BRAID (14.75” LG)
68 0G1462 1 HOSE BARB REDUCER 5/8"-3/8"ID
69 022129 9 WASHER LOCK M8-5/16
70 022145 9 WASHER FLAT 5/16 ZINC
71 022097 1 WASHER LOCK M6-1/4
(1) NOT SHOWN
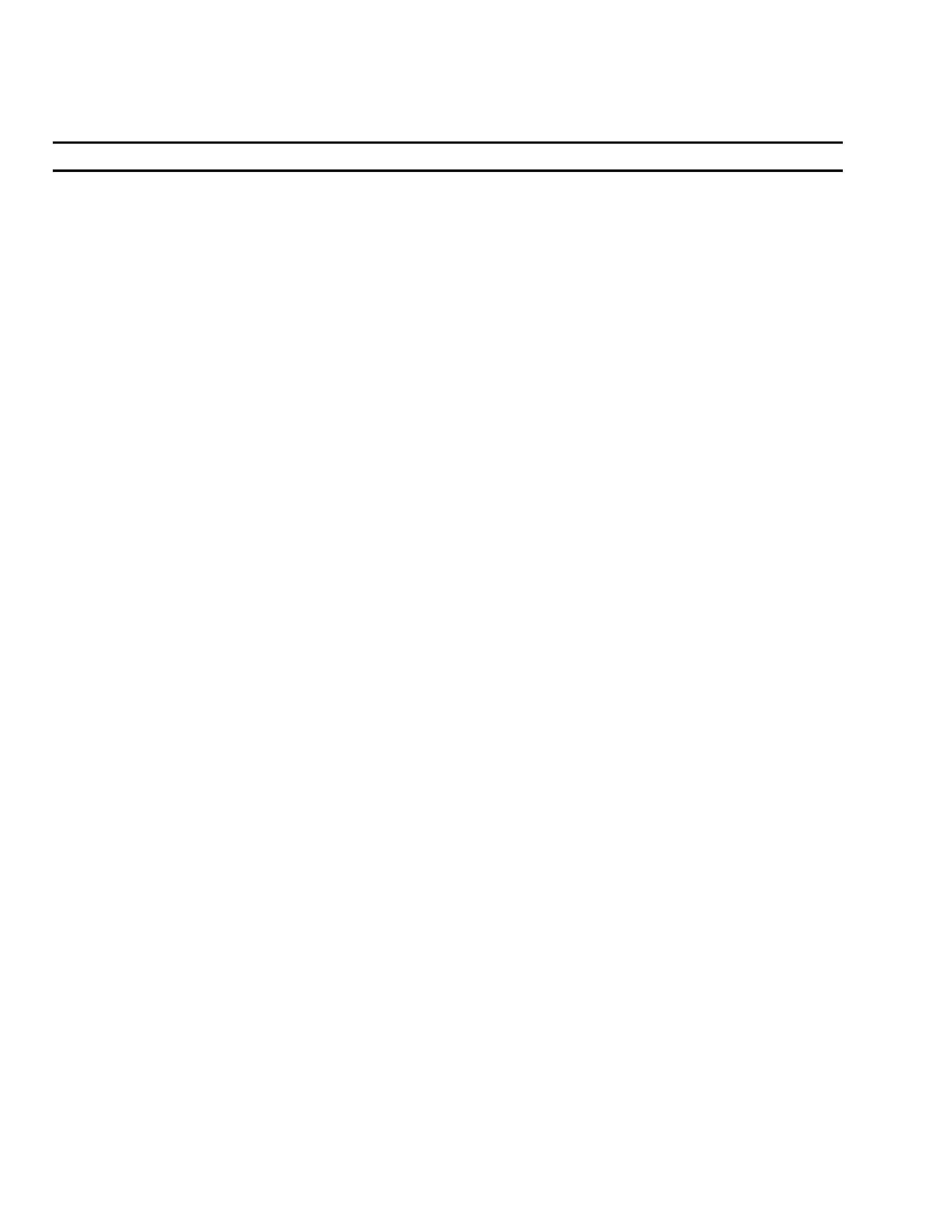
EXPLODED VIEW: EV ENGINE COMMON PARTS 5.4L C5
DRAWING #: 0L2847
GROUP D
ITEM PART# QTY. DESCRIPTION
REVISION: K-3424-C Page 6 of 6
DATE: 7/28/15
This page left blank intentionally
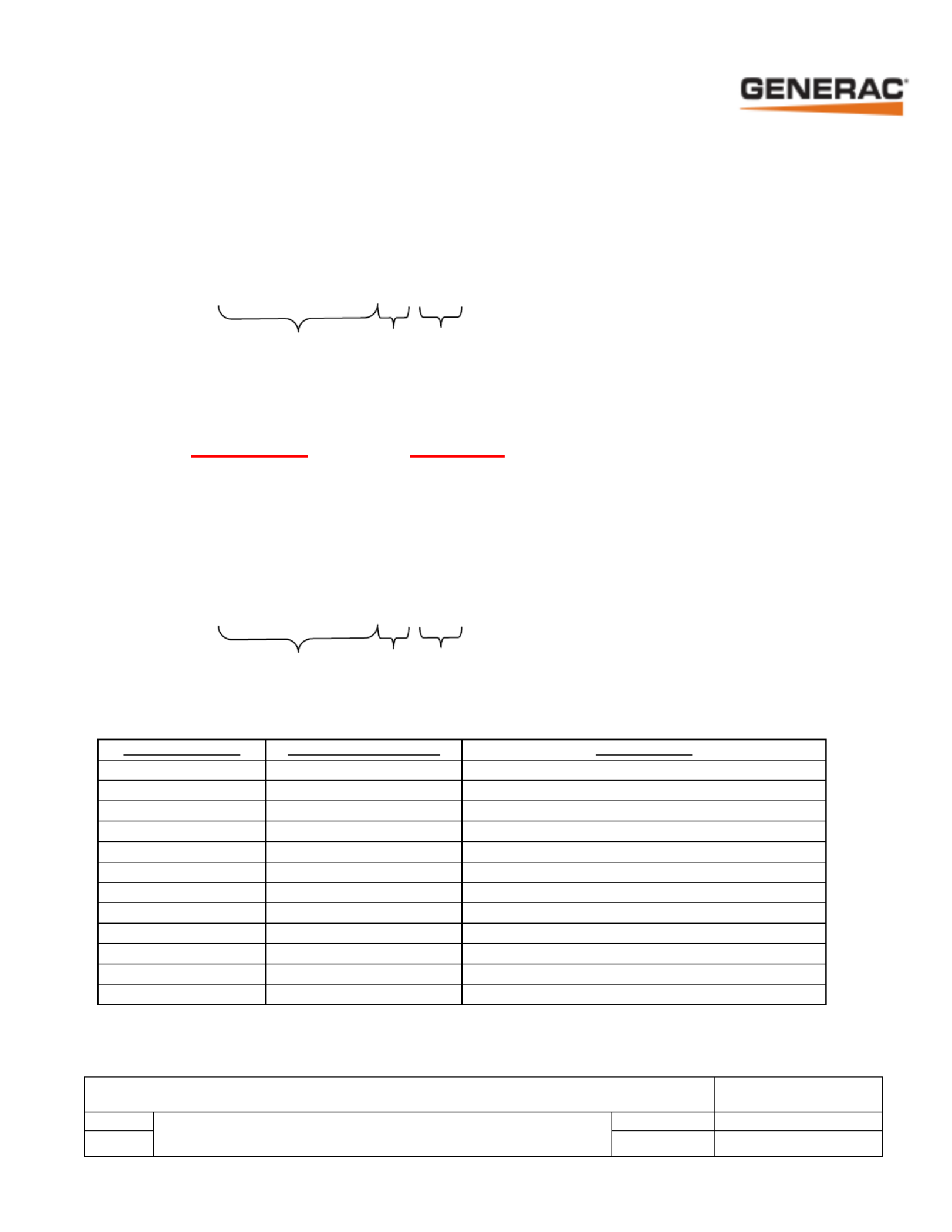
REPLACEMENT SHEET METAL PARTS ORDERING GUIDE
Parts listed in the manual Bill of Material on the EV drawings/Manuals are listed in the unfinished form with the default
material – usually steel or plain six or seven digit number.
0XXXXXX or 0XXXXX ST0R X
Base number Suffix1 Raw
After entering serial number or model number of the unit to search/order replacement sheet metal parts follow steps below
to identify/verify correct part number:
1. Obtain Unfinished Part number from the EV drawing in the manual or Generac Website
2. Enter
base number
in the system –
first 6 digit
. Press enter.
3. The full part number of the finished/painted part will show. (example 0H5522A or 0H0103A ) ST19 ST16
Verify that the material and color matches the unit/ replaced part per reference information below:
REFERENCE INFORMATION:
Starting in 2009 Generac Power Systems uses following part number structuring for parts with secondary finish – painted or
plated.
0XXXXXX YYZZ
Base number Suffix1 Suffix2
Suffix 1 - represent material part is made of – aluminum, steel or stainless steel
Suffix 2 - represents color or plating
Suffix 1 - Material Suffix 2 – Color/plating Color Used on
AL – Aluminum 0R – Raw (unfinished) DO NOT ORDER (default parts on drawings)
ST – Steel 01 – Tan Genset enclosures parts until 2009
SS – Stainless 03 – Black Frames, Tanks and misc. internal parts
VR – Variable Material 05 – White Industrial products parts
11 – Yellow Zinc Plating Miscellaneous internal parts
13 – Bisque Genset enclosures parts since 2008
14 – Grey Gen and TSW enclosures parts since 2009
15 – Orange Textured Portable Generator parts since 2009
16 – XP Gray Portable Generator parts since 2009
17 – Orange Gloss Portable Generator parts since 2009
18 – Special/Customer Colors per customer request (Special)
19 – Dark Grey Industrial products parts since 2010
GENERAC POWER SYSTEMS OWNS THE COPYRIGHT OF THIS SPECIFICATION WHICH IS SUPPLIED IN CONFIDENCE AND MUST NOT BE
COPIED OR TRANSMITTED TO OTHERS WITHOUT THE EXPRESS WRITTEN CONSENT OF GENERAC POWER SYSTEMS
Page 1 of 1
REV DATE NUMBER
B
REPLACEMENT SHEET METAL PARTS ORDERING
GUIDE
12/20/10 0H7169
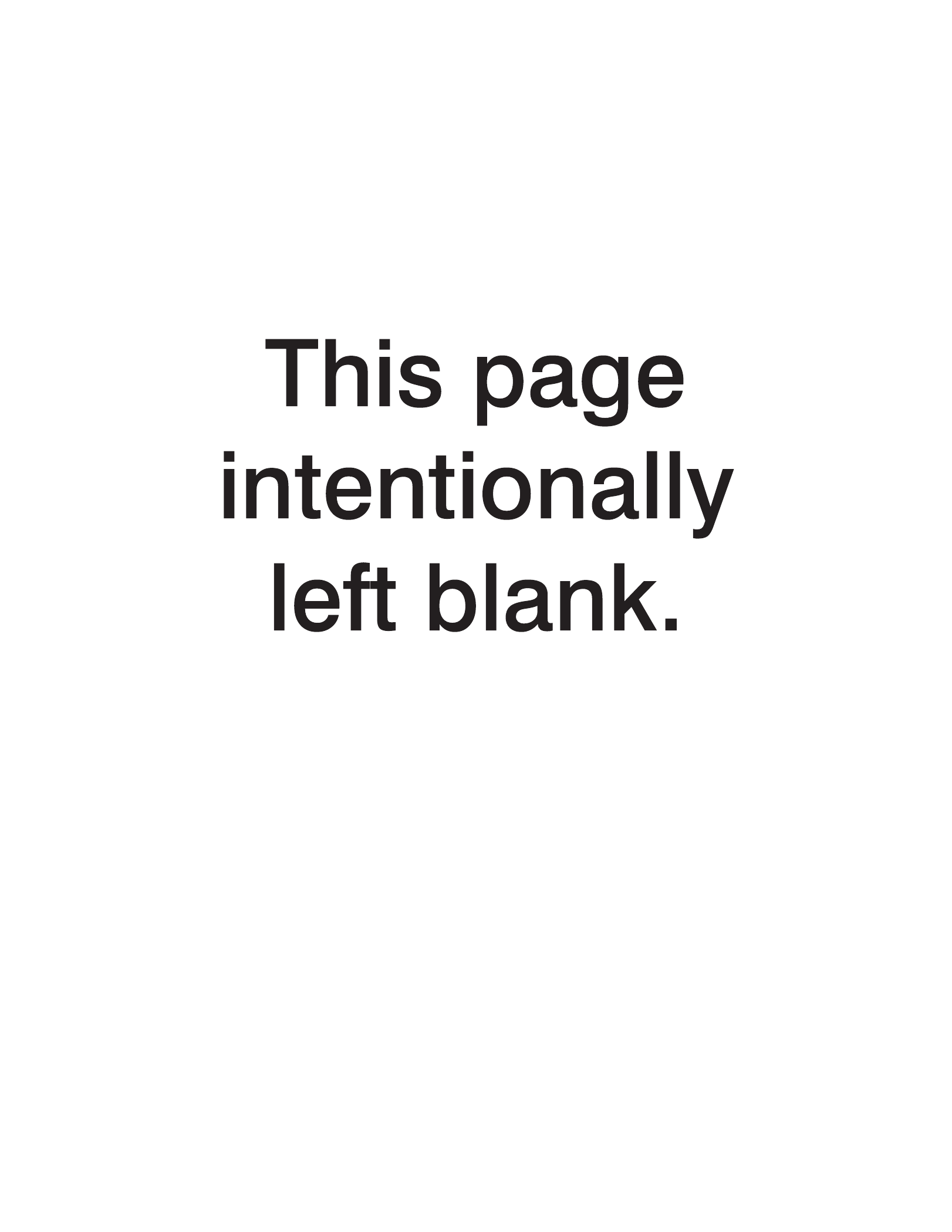
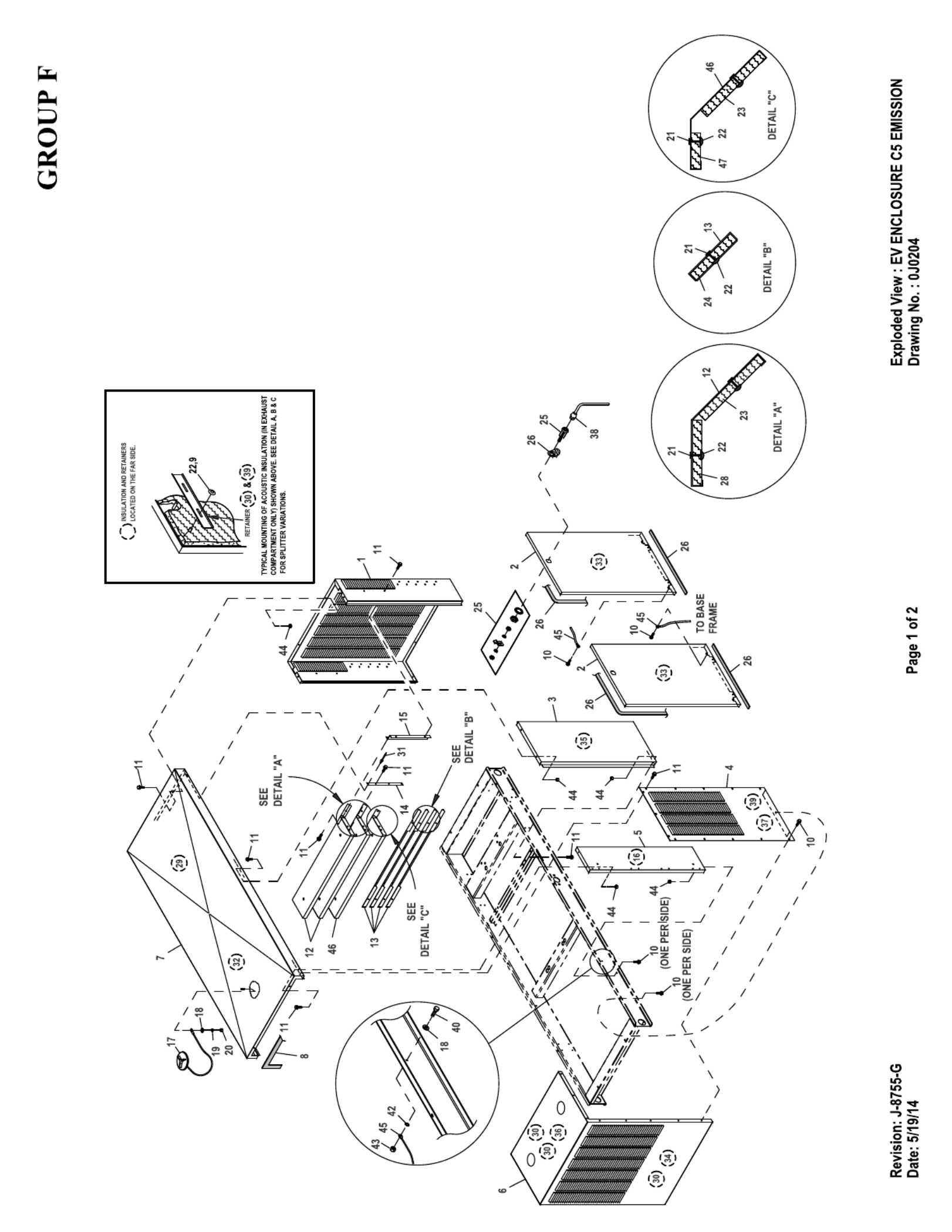
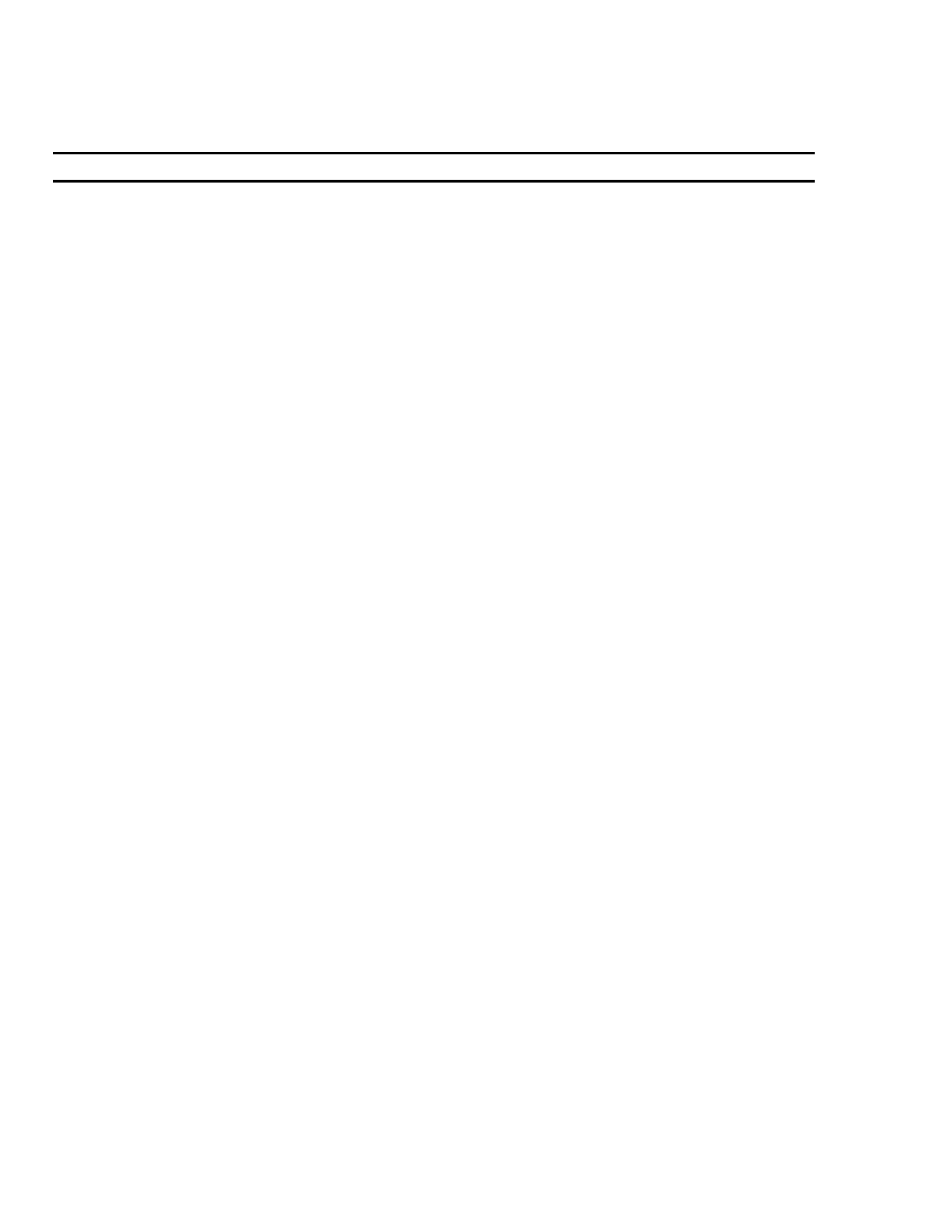
EXPLODED VIEW: EV ENCLOSURE C5 EMISSION
DRAWING #: 0J0204
GROUP F
APPLICABLE TO:
ITEM PART# QTY. DESCRIPTION
REVISION: J-8755-G PAGE 2 OF 2
DATE: 5/19/14
(2) 1 0F58730AL0R 1 REAR WRAP C5
(2) 2 0F5868AAL0R 4 DOOR C5
(2) 3 0F5872AAL0R 2 CENTER SUPPORT C5
(2) 4 0F58710AL0R 2 DISCHARGE DUCT LH & RH SIDE C5
(2) 5 0F5869AAL0R 2 FRONT CORNERS C5
(2) 6 0K88730AL0R 1 DUCT CENTER DISCHARGE RAW
(2) 7 0F58670AL0R 1 ROOF C5 ALUM
8 066760 1 STRIP SEALANT 1/8 X 1 (44.5”LG)
9 078115A 12 WASHER SELF LOCKING DOME #8-32
(1)10 0E3257 16 SCREW TH-FRM M6 W/CAP SHKPRF W
(1)11 0C2454 76 SCREW THF M6-1 X 16 N WA Z/JS
12 0F2766 2 SPLITTER
13 0F3181 4 SPLITTER SHORT
14 0F3185 2 STRINGER SPLITTER C3
15 0F3416 2 SUPPORT SPLITTER C5 130KW
16 0J0336 2 INSUL CORNER POST
17 0F4487A 1 ASSY ACCESS COVER
18 022473 5 WASHER FLAT 1/4-M6 ZINC
19 022097 1 WASHER LOCK M6-1/4
20 022127 1 NUT HEX 1/4-20 STEEL
21 0F3072 20 INSULATION RETAINMENT HANGER
22 078115 30 WASHER SELF LOCKING DOME #4-40
23 0J0336B 3 INSUL SPLITTER
24 0J0336A 4 INSUL SHORT LOUVER
25 0F5048D 4 VISE-ACTION LATCH SLOTTED CIR
26 0E5968 1 GASKET EXTRUDED TRIM (566” LG)
27 0F5049B 2 PULL TAB DOOR LOCK SS
28 0J0336G 2 INSUL SPLITTER SML
29 0J2624B 1 INSUL ROOF TOP REAR
30 0F3890A 3 RETAINER INSULATION (740)
31 087233 2 RIVET POP .1875 X .450 SS
32 0J0336C 1 INSUL ROOF TOP FRT
33 0J0336D 4 INSUL DOOR
34 0F3949G 1 INSUL DISCHARGE DUCT
35 0J0336F 2 INSUL CENTER SUPPORT
36 0F3949K 1 INSUL DISCHARGE DUCT TOP
37 0F3949F 2 INSUL INNER DUCT SIDE
38 0F8869D 1 KEY VISE-ACTION LATCH SLOT CIR
39 0F3890 2 RETAINER INSULATION (450)
40 042568 4 SCREW HHC M6-1.0 X 20 G8.8
42 022447 4 WASHER SHAKEPROOF INT 1/4
43 049813 4 NUT HEX M6 X 1.0 G8 YEL CHR
(1) 44 077992 28 NUT HEX LOCK M6-1.0 SS NY INS
45 0912970090 4 ASSY WIRE 14AWG GRN/YEL
46 0F2766A 1 SPLITTER C5
47 0J0336H 1 INSUL SPLITTER SHRT MPS
(1)ENCLOSURE NOTE: ALL PANELS THAT FASTEN TO THE BASEFRAME MUST BE SECURED USING I/N 10 & 11 (THREAD FORMING FASTENERS) AND I/N
44 (LOCK NUT). LOCK NUT IS TO BE INSTALLED AFTER THREAD FORMING FASTENER HAS PENETRATED THROUGH EXTRUSIONS IN ENCLOSURE
PANELS. ALL PANEL TO PANEL CONNECTIONS TO INCLUDE AT LEAST ONE CONNECTION POINT USING I/N 10 (THREAD FORMING FASTENER).
(2) SHEET METAL PARTS LISTED IN THE BOM TABLE ARE REPRESENTING GENERIC PARTS (NO COLOR)
• MANUFACTURING: FOR CORRECT MATERIAL AND COLOR REFER TO AS400 BOM.
• CUSTOMER: WHEN ORDERING REPLACEMENT PARTS ENTER BASE NUMBER (FIRST 6 DIGITS ONLY) IN THE SYSTEM FOR CORRECT
MATERIAL AND COLOR (FOR REFERENCE SEE GUIDELINE 0H7169).
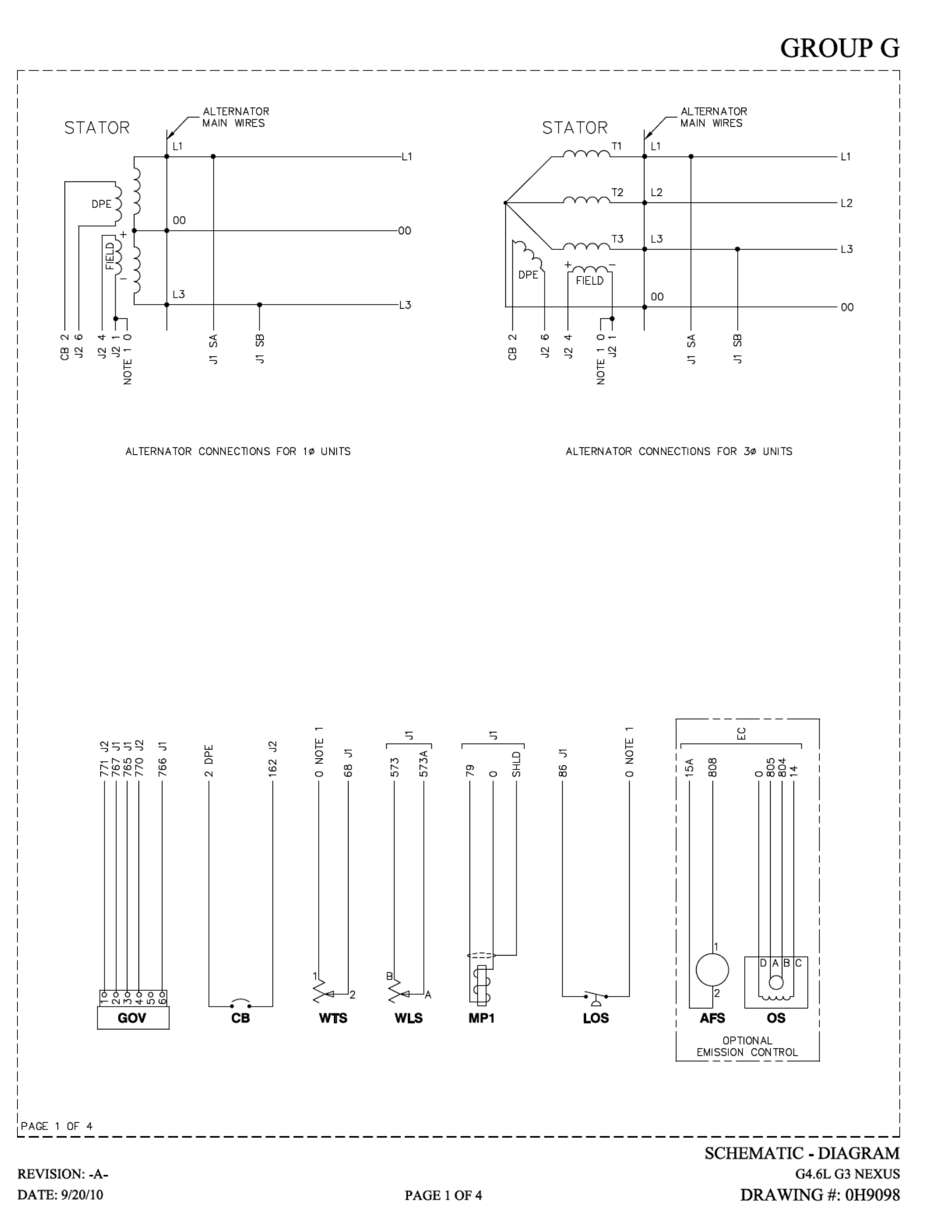
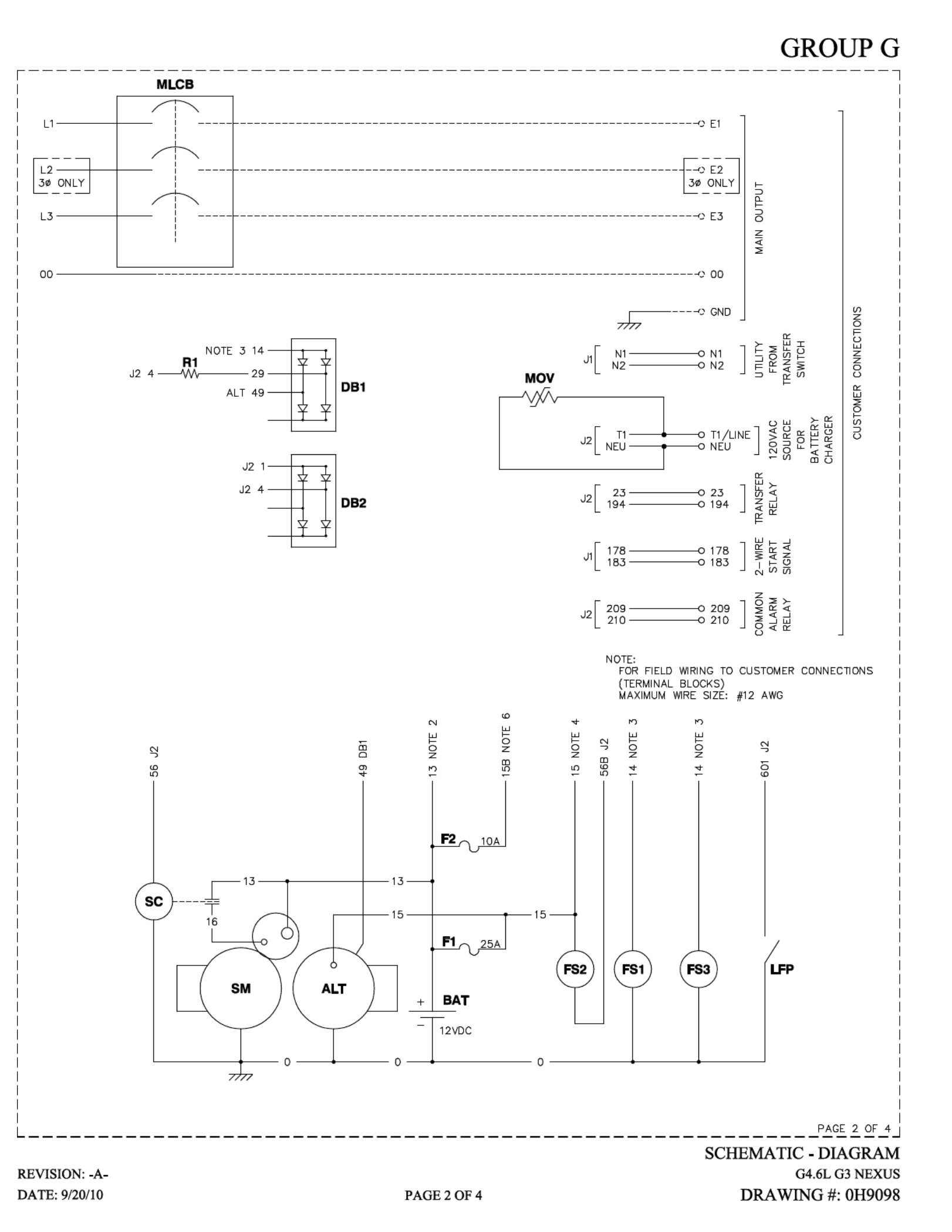
Termékspecifikációk
Márka: | Generac |
Kategória: | nincs kategorizálva |
Modell: | QT08054GVAX |
Szüksége van segítségre?
Ha segítségre van szüksége Generac QT08054GVAX, tegyen fel kérdést alább, és más felhasználók válaszolnak Önnek
Útmutatók nincs kategorizálva Generac

12 Január 2025

12 Január 2025

4 Szeptember 2024

4 Szeptember 2024

4 Szeptember 2024

16 Augusztus 2024

15 Augusztus 2024

15 Augusztus 2024

15 Augusztus 2024

15 Augusztus 2024
Útmutatók nincs kategorizálva
- nincs kategorizálva Mestic
- nincs kategorizálva Ikea
- nincs kategorizálva Phoenix Gold
- nincs kategorizálva Samsung
- nincs kategorizálva BaByliss
- nincs kategorizálva Grace Design
- nincs kategorizálva PeakTech
- nincs kategorizálva Sony
- nincs kategorizálva August
- nincs kategorizálva Braun
- nincs kategorizálva Yamaha
- nincs kategorizálva National Geographic
- nincs kategorizálva Beko
- nincs kategorizálva Fujitsu
- nincs kategorizálva Hoshizaki
- nincs kategorizálva Microchip
- nincs kategorizálva Dometic
- nincs kategorizálva Electrolux
- nincs kategorizálva Acer
- nincs kategorizálva Moulinex
- nincs kategorizálva Sharkoon
- nincs kategorizálva Whirlpool
- nincs kategorizálva Nedis
- nincs kategorizálva Applico
- nincs kategorizálva Milwaukee
- nincs kategorizálva Amazfit
- nincs kategorizálva LG
- nincs kategorizálva Grundig
- nincs kategorizálva Ariston Thermo
- nincs kategorizálva Husqvarna
- nincs kategorizálva Dolmar
- nincs kategorizálva Realme
- nincs kategorizálva Tommee Tippee
- nincs kategorizálva Parkside
- nincs kategorizálva DeepCool
- nincs kategorizálva Peugeot
- nincs kategorizálva Maglite
- nincs kategorizálva Marantz
- nincs kategorizálva Candy
- nincs kategorizálva Gem Toys
- nincs kategorizálva Worx
- nincs kategorizálva Philips
- nincs kategorizálva Gorenje
- nincs kategorizálva Pioneer
- nincs kategorizálva Kärcher
- nincs kategorizálva Reolink
- nincs kategorizálva Olympus
- nincs kategorizálva Adler
- nincs kategorizálva Princess
- nincs kategorizálva Oregon Scientific
- nincs kategorizálva SilverCrest
- nincs kategorizálva Garmin
- nincs kategorizálva RCF
- nincs kategorizálva Bosch
- nincs kategorizálva Indesit
- nincs kategorizálva Nivona
- nincs kategorizálva TC Electronic
- nincs kategorizálva Singer
- nincs kategorizálva Honda
- nincs kategorizálva Theben
- nincs kategorizálva Panasonic
- nincs kategorizálva Canon
- nincs kategorizálva Zanussi
- nincs kategorizálva JVC
- nincs kategorizálva Lego
- nincs kategorizálva Conair
- nincs kategorizálva MPM
- nincs kategorizálva AEG
- nincs kategorizálva Doepke
- nincs kategorizálva Emerio
- nincs kategorizálva Volvo
- nincs kategorizálva StarTech.com
- nincs kategorizálva Ultimate Speed
- nincs kategorizálva Mega
- nincs kategorizálva Tunturi
- nincs kategorizálva Paidi
- nincs kategorizálva Sharp
- nincs kategorizálva Einhell
- nincs kategorizálva Livarno Lux
- nincs kategorizálva Harman Kardon
- nincs kategorizálva Florabest
- nincs kategorizálva Nokia
- nincs kategorizálva Stihl
- nincs kategorizálva Lenovo
- nincs kategorizálva Teka
- nincs kategorizálva Yard Force
- nincs kategorizálva Hoover
- nincs kategorizálva Evolveo
- nincs kategorizálva Neff
- nincs kategorizálva HyperX
- nincs kategorizálva Casio
- nincs kategorizálva Toshiba
- nincs kategorizálva Sven
- nincs kategorizálva Neumann
- nincs kategorizálva Oppo
- nincs kategorizálva Bluetti
- nincs kategorizálva Ozito
- nincs kategorizálva Omron
- nincs kategorizálva Bartscher
- nincs kategorizálva Gamdias
- nincs kategorizálva Maxwell
- nincs kategorizálva HP
- nincs kategorizálva Makita
- nincs kategorizálva Hyundai
- nincs kategorizálva Hisense
- nincs kategorizálva Gastronoma
- nincs kategorizálva BenQ
- nincs kategorizálva Sandisk
- nincs kategorizálva Scarlett
- nincs kategorizálva Tefal
- nincs kategorizálva Auriol
- nincs kategorizálva Apple
- nincs kategorizálva HQ
- nincs kategorizálva Ubiquiti Networks
- nincs kategorizálva Bestway
- nincs kategorizálva Saramonic
- nincs kategorizálva SunBriteTV
- nincs kategorizálva Siemens
- nincs kategorizálva TP-Link
- nincs kategorizálva Fellowes
- nincs kategorizálva Emos
- nincs kategorizálva Hifonics
- nincs kategorizálva Voltcraft
- nincs kategorizálva Medion
- nincs kategorizálva Onkyo
- nincs kategorizálva MyPhone
- nincs kategorizálva Motorola
- nincs kategorizálva Geemarc
- nincs kategorizálva Vimar
- nincs kategorizálva LogiLink
- nincs kategorizálva Sena
- nincs kategorizálva Exquisit
- nincs kategorizálva Alcatel
- nincs kategorizálva SBS
- nincs kategorizálva Corbero
- nincs kategorizálva Miele
- nincs kategorizálva Technics
- nincs kategorizálva Fuxtec
- nincs kategorizálva Roland
- nincs kategorizálva JBL
- nincs kategorizálva Camry
- nincs kategorizálva Suzuki
- nincs kategorizálva TCL
- nincs kategorizálva DAP-Audio
- nincs kategorizálva Hunter
- nincs kategorizálva Rocstor
- nincs kategorizálva Digitus
- nincs kategorizálva Zebra
- nincs kategorizálva Viessmann
- nincs kategorizálva My Wall
- nincs kategorizálva Xiaomi
- nincs kategorizálva TRENDnet
- nincs kategorizálva V-Zug
- nincs kategorizálva GoGen
- nincs kategorizálva Flex
- nincs kategorizálva Danby
- nincs kategorizálva DeLonghi
- nincs kategorizálva Clean Air Optima
- nincs kategorizálva Mercusys
- nincs kategorizálva AVM
- nincs kategorizálva Futaba
- nincs kategorizálva Enhanced Flight
- nincs kategorizálva Insignia
- nincs kategorizálva Krups
- nincs kategorizálva Vertiv
- nincs kategorizálva Fujifilm
- nincs kategorizálva Hecht
- nincs kategorizálva AL-KO
- nincs kategorizálva Crimson
- nincs kategorizálva Liebherr
- nincs kategorizálva Martin Logan
- nincs kategorizálva EA Elektro Automatik
- nincs kategorizálva Crivit
- nincs kategorizálva LC-Power
- nincs kategorizálva EZVIZ
- nincs kategorizálva Heinner
- nincs kategorizálva Infiniton
- nincs kategorizálva Ford
- nincs kategorizálva Sunbeam
- nincs kategorizálva Dell
- nincs kategorizálva Beurer
- nincs kategorizálva Boss
- nincs kategorizálva Crestron
- nincs kategorizálva Lancom
- nincs kategorizálva Cramer
- nincs kategorizálva ORNO
- nincs kategorizálva Strong
- nincs kategorizálva Ariete
- nincs kategorizálva Wilfa
- nincs kategorizálva Klarstein
- nincs kategorizálva Amica
- nincs kategorizálva Medisana
- nincs kategorizálva Lincoln Electric
- nincs kategorizálva Cyrus
- nincs kategorizálva Keurig
- nincs kategorizálva VOX
- nincs kategorizálva Scheppach
- nincs kategorizálva Dreame
- nincs kategorizálva Instant
- nincs kategorizálva Cybex
- nincs kategorizálva Be Cool
- nincs kategorizálva Gourmetmaxx
- nincs kategorizálva Gigabyte
- nincs kategorizálva Tripp Lite
- nincs kategorizálva Ergotools Pattfield
- nincs kategorizálva Vivax
- nincs kategorizálva Volkswagen
- nincs kategorizálva MEE Audio
- nincs kategorizálva Prixton
- nincs kategorizálva Primera
- nincs kategorizálva Omega
- nincs kategorizálva Conceptronic
- nincs kategorizálva Datalogic
- nincs kategorizálva Allen & Heath
- nincs kategorizálva Thomson
- nincs kategorizálva Intex
- nincs kategorizálva Esperanza
- nincs kategorizálva Juniper
- nincs kategorizálva Smeg
- nincs kategorizálva Polaroid
- nincs kategorizálva Fagor
- nincs kategorizálva BDI
- nincs kategorizálva Unold
- nincs kategorizálva DPM
- nincs kategorizálva Vileda
- nincs kategorizálva SHX
- nincs kategorizálva Jura
- nincs kategorizálva Sage
- nincs kategorizálva Kyocera
- nincs kategorizálva Klipsch
- nincs kategorizálva Hegel
- nincs kategorizálva Melitta
- nincs kategorizálva CMI
- nincs kategorizálva Brentwood
- nincs kategorizálva Bifinett
- nincs kategorizálva Scala
- nincs kategorizálva Technaxx
- nincs kategorizálva Ardes
- nincs kategorizálva Aiwa
- nincs kategorizálva Hammersmith
- nincs kategorizálva Roidmi
- nincs kategorizálva Phanteks
- nincs kategorizálva Cuisinart
- nincs kategorizálva Suevia
- nincs kategorizálva Joie
- nincs kategorizálva GoPro
- nincs kategorizálva Speco Technologies
- nincs kategorizálva Blackmagic Design
- nincs kategorizálva Orima
- nincs kategorizálva Ricoh
- nincs kategorizálva Eden
- nincs kategorizálva GW Instek
- nincs kategorizálva Interphone
- nincs kategorizálva Rommelsbacher
- nincs kategorizálva Hikvision
- nincs kategorizálva United Office
- nincs kategorizálva Rapid
- nincs kategorizálva Kenwood
- nincs kategorizálva Eurolite
- nincs kategorizálva Owon
- nincs kategorizálva Epson
- nincs kategorizálva Cateye
- nincs kategorizálva Cleanmaxx
- nincs kategorizálva WiiM
- nincs kategorizálva Rega
- nincs kategorizálva Vivanco
- nincs kategorizálva Jocel
- nincs kategorizálva Duronic
- nincs kategorizálva Subaru
- nincs kategorizálva Bimar
- nincs kategorizálva Netgear
- nincs kategorizálva Etna
- nincs kategorizálva Solis
- nincs kategorizálva V7
- nincs kategorizálva Huawei
- nincs kategorizálva Dehner
- nincs kategorizálva EGO
- nincs kategorizálva Aim TTi
- nincs kategorizálva Café
- nincs kategorizálva Microsoft
- nincs kategorizálva Asus
- nincs kategorizálva Segway
- nincs kategorizálva Jabra
- nincs kategorizálva Starlyf
- nincs kategorizálva Vtech
- nincs kategorizálva Clatronic
- nincs kategorizálva Arturia
- nincs kategorizálva Rollei
- nincs kategorizálva Rain Bird
- nincs kategorizálva Bomann
- nincs kategorizálva Mafell
- nincs kategorizálva Bauknecht
- nincs kategorizálva Hama
- nincs kategorizálva Amana
- nincs kategorizálva ELAC
- nincs kategorizálva Bugaboo
- nincs kategorizálva Dyson
- nincs kategorizálva JIMMY
- nincs kategorizálva Hauck
- nincs kategorizálva Zoom
- nincs kategorizálva Renkforce
- nincs kategorizálva Korg
- nincs kategorizálva Ambiano
- nincs kategorizálva Toorx
- nincs kategorizálva Kugoo
- nincs kategorizálva Ninja
- nincs kategorizálva Agfa
- nincs kategorizálva Hotpoint
- nincs kategorizálva Midland
- nincs kategorizálva Haier
- nincs kategorizálva Frigidaire
- nincs kategorizálva Mitsubishi
- nincs kategorizálva Gossen Metrawatt
- nincs kategorizálva Cecotec
- nincs kategorizálva Dacor
- nincs kategorizálva Lamax
- nincs kategorizálva Britax-Römer
- nincs kategorizálva Lezyne
- nincs kategorizálva Sanitas
- nincs kategorizálva Synology
- nincs kategorizálva Godex
- nincs kategorizálva Navitel
- nincs kategorizálva Sencor
- nincs kategorizálva Pelgrim
- nincs kategorizálva GPX
- nincs kategorizálva Proaim
- nincs kategorizálva Hori
- nincs kategorizálva Techno Line
- nincs kategorizálva Focusrite
- nincs kategorizálva Knog
- nincs kategorizálva Polsen
- nincs kategorizálva Draytek
- nincs kategorizálva Privileg
- nincs kategorizálva Benavent
- nincs kategorizálva Supermicro
- nincs kategorizálva Baxi
- nincs kategorizálva Küppersbusch
- nincs kategorizálva Pfaff
- nincs kategorizálva CATA
- nincs kategorizálva Genesis
- nincs kategorizálva Innoliving
- nincs kategorizálva Bose
- nincs kategorizálva Avidsen
- nincs kategorizálva M-Audio
- nincs kategorizálva Brother
- nincs kategorizálva Raymarine
- nincs kategorizálva AOC
- nincs kategorizálva Summit
- nincs kategorizálva Thrustmaster
- nincs kategorizálva Lowrance
- nincs kategorizálva Iogear
- nincs kategorizálva Rowenta
- nincs kategorizálva Lastolite
- nincs kategorizálva Polisport
- nincs kategorizálva Westinghouse
- nincs kategorizálva Thomas
- nincs kategorizálva Güde
- nincs kategorizálva Hitachi
- nincs kategorizálva Inventum
- nincs kategorizálva BabyZen
- nincs kategorizálva Xblitz
- nincs kategorizálva BeamZ
- nincs kategorizálva Mercury
- nincs kategorizálva Hasbro
- nincs kategorizálva IRobot
- nincs kategorizálva Wolf Garten
- nincs kategorizálva Kospel
- nincs kategorizálva Peg Perego
- nincs kategorizálva Ctek
- nincs kategorizálva Rexel
- nincs kategorizálva Lagrange
- nincs kategorizálva DSC
- nincs kategorizálva PATLITE
- nincs kategorizálva BLUEPALM
- nincs kategorizálva Reebok
- nincs kategorizálva Continental Edison
- nincs kategorizálva Biostar
- nincs kategorizálva Eta
- nincs kategorizálva Atag
- nincs kategorizálva Izzy
- nincs kategorizálva Remington
- nincs kategorizálva Mikrotik
- nincs kategorizálva Blackstar
- nincs kategorizálva Telefunken
- nincs kategorizálva Asrock
- nincs kategorizálva Nevir
- nincs kategorizálva Microboards
- nincs kategorizálva Kodak
- nincs kategorizálva Sennheiser
- nincs kategorizálva Tractive
- nincs kategorizálva JANDY
- nincs kategorizálva ResMed
- nincs kategorizálva Ring
- nincs kategorizálva V-TAC
- nincs kategorizálva Piko
- nincs kategorizálva Cambridge
- nincs kategorizálva Kanto
- nincs kategorizálva Doro
- nincs kategorizálva Nikon
- nincs kategorizálva Domo
- nincs kategorizálva Russell Hobbs
- nincs kategorizálva Monster
- nincs kategorizálva Alpine
- nincs kategorizálva Acoustic Solutions
- nincs kategorizálva Roadinger
- nincs kategorizálva Silk'n
- nincs kategorizálva Roadstar
- nincs kategorizálva Zepter
- nincs kategorizálva 4ms
- nincs kategorizálva Optoma
- nincs kategorizálva COLBOR
- nincs kategorizálva Thor
- nincs kategorizálva Emilia
- nincs kategorizálva Caso
- nincs kategorizálva Tempo
- nincs kategorizálva Eastron
- nincs kategorizálva Kiloview
- nincs kategorizálva Omnitronic
- nincs kategorizálva Toolcraft
- nincs kategorizálva ZyXEL
- nincs kategorizálva Logitech
- nincs kategorizálva Solac
- nincs kategorizálva Amiko
- nincs kategorizálva Proviel
- nincs kategorizálva SPL
- nincs kategorizálva Bresser
- nincs kategorizálva JennAir
- nincs kategorizálva Bahr
- nincs kategorizálva Pro-Ject
- nincs kategorizálva Coyote
- nincs kategorizálva Smart
- nincs kategorizálva TOA
- nincs kategorizálva Klein Tools
- nincs kategorizálva Parrot
- nincs kategorizálva Chauvin Arnoux
- nincs kategorizálva Carson
- nincs kategorizálva Kindercraft
- nincs kategorizálva Chicco
- nincs kategorizálva Stiebel Eltron
- nincs kategorizálva Create
- nincs kategorizálva Dahua Technology
- nincs kategorizálva Withings
- nincs kategorizálva Edesa
- nincs kategorizálva Viewsonic
- nincs kategorizálva Wagner
- nincs kategorizálva SVS
- nincs kategorizálva Cobra
- nincs kategorizálva Microlife
- nincs kategorizálva Nextbase
- nincs kategorizálva American DJ
- nincs kategorizálva Scosche
- nincs kategorizálva Crane
- nincs kategorizálva Hilti
- nincs kategorizálva Crunch
- nincs kategorizálva NordicTrack
- nincs kategorizálva Denver
- nincs kategorizálva Dynaudio
- nincs kategorizálva Smart-AVI
- nincs kategorizálva Empress Effects
- nincs kategorizálva Naim
- nincs kategorizálva First Alert
- nincs kategorizálva Bush
- nincs kategorizálva Power Dynamics
- nincs kategorizálva Black & Decker
- nincs kategorizálva Workzone
- nincs kategorizálva Fibaro
- nincs kategorizálva G3 Ferrari
- nincs kategorizálva Stages
- nincs kategorizálva Ravensburger
- nincs kategorizálva Zoofari
- nincs kategorizálva IPGARD
- nincs kategorizálva Dynacord
- nincs kategorizálva Minox
- nincs kategorizálva Trevi
- nincs kategorizálva Hoymiles
- nincs kategorizálva Devolo
- nincs kategorizálva Gardena
- nincs kategorizálva EchoMaster
- nincs kategorizálva Memphis Audio
- nincs kategorizálva RCBS
- nincs kategorizálva Hamilton Beach
- nincs kategorizálva Global
- nincs kategorizálva Fitbit
- nincs kategorizálva DiO
- nincs kategorizálva Planet
- nincs kategorizálva Ewent
- nincs kategorizálva Wood's
- nincs kategorizálva Burg Wächter
- nincs kategorizálva Turmix
- nincs kategorizálva Beha-Amprobe
- nincs kategorizálva Evenflo
- nincs kategorizálva Elta
- nincs kategorizálva Ernitec
- nincs kategorizálva Tenda
- nincs kategorizálva Waterco
- nincs kategorizálva Severin
- nincs kategorizálva Vaillant
- nincs kategorizálva Fieldmann
- nincs kategorizálva DJI
- nincs kategorizálva BT
- nincs kategorizálva Bryton
- nincs kategorizálva Albrecht
- nincs kategorizálva X4 Tech
- nincs kategorizálva Lionelo
- nincs kategorizálva Livington
- nincs kategorizálva Black Box
- nincs kategorizálva Mattel
- nincs kategorizálva Ground Zero
- nincs kategorizálva Autel
- nincs kategorizálva EZ Dupe
- nincs kategorizálva Aluratek
- nincs kategorizálva Audio-Technica
- nincs kategorizálva Gustavsberg
- nincs kategorizálva Amazon
- nincs kategorizálva Orbegozo
- nincs kategorizálva NGS
- nincs kategorizálva BRITA
- nincs kategorizálva HDFury
- nincs kategorizálva Hanseatic
- nincs kategorizálva Joy-It
- nincs kategorizálva MSI
- nincs kategorizálva Konig & Meyer
- nincs kategorizálva Daewoo
- nincs kategorizálva Fisher Price
- nincs kategorizálva Lenoxx
- nincs kategorizálva GYS
- nincs kategorizálva Juki
- nincs kategorizálva Dali
- nincs kategorizálva Mount-It!
- nincs kategorizálva Livoo
- nincs kategorizálva Tesla
- nincs kategorizálva Viking
- nincs kategorizálva Kali Audio
- nincs kategorizálva Godox
- nincs kategorizálva SodaStream
- nincs kategorizálva Antec
- nincs kategorizálva Dash
- nincs kategorizálva Eberle
- nincs kategorizálva Gram
- nincs kategorizálva Extech
- nincs kategorizálva Gembird
- nincs kategorizálva Cisco
- nincs kategorizálva Elica
- nincs kategorizálva PowerPlus
- nincs kategorizálva Denon
- nincs kategorizálva Victor Technology
- nincs kategorizálva Body Sculpture
- nincs kategorizálva Balay
- nincs kategorizálva Silverlit
- nincs kategorizálva Sungrow
- nincs kategorizálva Hotpoint Ariston
- nincs kategorizálva ATen
- nincs kategorizálva XGIMI
- nincs kategorizálva Muse
- nincs kategorizálva Energy Sistem
- nincs kategorizálva Native Instruments
- nincs kategorizálva OK
- nincs kategorizálva Horizon Fitness
- nincs kategorizálva GE
- nincs kategorizálva Playtive
- nincs kategorizálva Guzzanti
- nincs kategorizálva Google
- nincs kategorizálva Honor
- nincs kategorizálva Xtorm
- nincs kategorizálva Electro-Voice
- nincs kategorizálva Concept
- nincs kategorizálva DCS
- nincs kategorizálva DEDRA
- nincs kategorizálva SVAN
- nincs kategorizálva Niceboy
- nincs kategorizálva JL Audio
- nincs kategorizálva On Air
- nincs kategorizálva Dymo
- nincs kategorizálva NightStick
- nincs kategorizálva Metabo
- nincs kategorizálva Dorma
- nincs kategorizálva TrueLife
- nincs kategorizálva Turbo Air
- nincs kategorizálva Newline
- nincs kategorizálva SPC
- nincs kategorizálva Sanus
- nincs kategorizálva Bellini
- nincs kategorizálva Maxi-Cosi
- nincs kategorizálva BabyBjörn
- nincs kategorizálva Osram
- nincs kategorizálva Baby Lock
- nincs kategorizálva Maximum
- nincs kategorizálva Bialetti
- nincs kategorizálva Testo
- nincs kategorizálva Ledlenser
- nincs kategorizálva BOYA
- nincs kategorizálva Speed-Link
- nincs kategorizálva Caple
- nincs kategorizálva Kingston
- nincs kategorizálva Hartke
- nincs kategorizálva Weller
- nincs kategorizálva Nobo
- nincs kategorizálva Steelplay
- nincs kategorizálva Auna
- nincs kategorizálva Akasa
- nincs kategorizálva Simpson
- nincs kategorizálva Hitec
- nincs kategorizálva Polti
- nincs kategorizálva Accu-Chek
- nincs kategorizálva Stokke
- nincs kategorizálva CDA
- nincs kategorizálva KitchenAid
- nincs kategorizálva Unify
- nincs kategorizálva Mac Audio
- nincs kategorizálva Asko
- nincs kategorizálva Rosieres
- nincs kategorizálva Consul
- nincs kategorizálva Growatt
- nincs kategorizálva OBH Nordica
- nincs kategorizálva Bissell
- nincs kategorizálva Behringer
- nincs kategorizálva Nexa
- nincs kategorizálva Bea-fon
- nincs kategorizálva Powerfix
- nincs kategorizálva TriStar
- nincs kategorizálva Biltema
- nincs kategorizálva Hoberg
- nincs kategorizálva Zelmer
- nincs kategorizálva Scotsman
- nincs kategorizálva Rocktrail
- nincs kategorizálva Suunto
- nincs kategorizálva Novy
- nincs kategorizálva Mooer
- nincs kategorizálva Suntec
- nincs kategorizálva ZTE
- nincs kategorizálva BaseTech
- nincs kategorizálva Edimax
- nincs kategorizálva Loewe
- nincs kategorizálva REL Acoustics
- nincs kategorizálva Chamberlain
- nincs kategorizálva Chord
- nincs kategorizálva SABO
- nincs kategorizálva Bavaria
- nincs kategorizálva Eufy
- nincs kategorizálva APC
- nincs kategorizálva CyberPower
- nincs kategorizálva Zodiac
- nincs kategorizálva Bogen
- nincs kategorizálva Tanita
- nincs kategorizálva Showtec
- nincs kategorizálva Pulsar
- nincs kategorizálva Jane
- nincs kategorizálva IMC Toys
- nincs kategorizálva RYOBI
- nincs kategorizálva ProfiCare
- nincs kategorizálva Stiga
- nincs kategorizálva Thule
- nincs kategorizálva Rommer
- nincs kategorizálva Atlantic
- nincs kategorizálva KRK
- nincs kategorizálva SolarEdge
- nincs kategorizálva Tower
- nincs kategorizálva Keter
- nincs kategorizálva Futurelight
- nincs kategorizálva ModeCom
- nincs kategorizálva Avaya
- nincs kategorizálva Ei Electronics
- nincs kategorizálva Fantini Cosmi
- nincs kategorizálva ADATA
- nincs kategorizálva Cooler Master
- nincs kategorizálva Babymoov
- nincs kategorizálva Hobart
- nincs kategorizálva Hammer
- nincs kategorizálva Solo
- nincs kategorizálva Terratec
- nincs kategorizálva Carel
- nincs kategorizálva Koenic
- nincs kategorizálva Chauvet
- nincs kategorizálva ICE Watch
- nincs kategorizálva ADDAC System
- nincs kategorizálva Pentair
- nincs kategorizálva DreamGEAR
- nincs kategorizálva Lorelli
- nincs kategorizálva Nodor
- nincs kategorizálva Grohe
- nincs kategorizálva Electro Harmonix
- nincs kategorizálva Syma
- nincs kategorizálva Levenhuk
- nincs kategorizálva Daikin
- nincs kategorizálva Shure
- nincs kategorizálva Renegade
- nincs kategorizálva Konica Minolta
- nincs kategorizálva Aprilia
- nincs kategorizálva PreSonus
- nincs kategorizálva Mamiya
- nincs kategorizálva REV
- nincs kategorizálva Overmax
- nincs kategorizálva Artusi
- nincs kategorizálva SuperTooth
- nincs kategorizálva Midea
- nincs kategorizálva American International
- nincs kategorizálva Hamax
- nincs kategorizálva Adidas
- nincs kategorizálva Steba
- nincs kategorizálva Revel
- nincs kategorizálva OnePlus
- nincs kategorizálva Flycam
- nincs kategorizálva Winix
- nincs kategorizálva Proxxon
- nincs kategorizálva Archos
- nincs kategorizálva HiKOKI
- nincs kategorizálva Deltaco
- nincs kategorizálva Lorex
- nincs kategorizálva Foscam
- nincs kategorizálva Trisa
- nincs kategorizálva Steelseries
- nincs kategorizálva Oliveri
- nincs kategorizálva Polar
- nincs kategorizálva Intertechno
- nincs kategorizálva MaxCom
- nincs kategorizálva SEH
- nincs kategorizálva Heller
- nincs kategorizálva Milan
- nincs kategorizálva Manhattan
- nincs kategorizálva BeSafe
- nincs kategorizálva Spektrum
- nincs kategorizálva Carlo Gavazzi
- nincs kategorizálva Tannoy
- nincs kategorizálva Plantronics
- nincs kategorizálva SkyRC
- nincs kategorizálva Peavey
- nincs kategorizálva BENNING
- nincs kategorizálva Orbit
- nincs kategorizálva PurAthletics
- nincs kategorizálva Blomberg
- nincs kategorizálva Progress
- nincs kategorizálva ISi
- nincs kategorizálva Kogan
- nincs kategorizálva Profilo
- nincs kategorizálva Texas
- nincs kategorizálva Horizon
- nincs kategorizálva Alecto
- nincs kategorizálva Core SWX
- nincs kategorizálva Grizzly
- nincs kategorizálva Festool
- nincs kategorizálva Falmec
- nincs kategorizálva Honeywell
- nincs kategorizálva Truma
- nincs kategorizálva Broan
- nincs kategorizálva Sodapop
- nincs kategorizálva PKM
- nincs kategorizálva EnGenius
- nincs kategorizálva McCulloch
- nincs kategorizálva Fontastic
- nincs kategorizálva Greenworks
- nincs kategorizálva Intenso
- nincs kategorizálva MantelMount
- nincs kategorizálva Stirling
- nincs kategorizálva Adder
- nincs kategorizálva SMART Technologies
- nincs kategorizálva Yato
- nincs kategorizálva Mesko
- nincs kategorizálva Marshall
- nincs kategorizálva Acme
- nincs kategorizálva Levoit
- nincs kategorizálva Sigma
- nincs kategorizálva PowerXL
- nincs kategorizálva Kindermann
- nincs kategorizálva Juwel
- nincs kategorizálva Furrion
- nincs kategorizálva Ultimate
- nincs kategorizálva Gardenline
- nincs kategorizálva Pentax
- nincs kategorizálva Alesis
- nincs kategorizálva Velleman
- nincs kategorizálva Prestigio
- nincs kategorizálva Universal Audio
- nincs kategorizálva Western Digital
- nincs kategorizálva AEA
- nincs kategorizálva Morel
- nincs kategorizálva Geuther
- nincs kategorizálva Terraillon
- nincs kategorizálva Russound
- nincs kategorizálva GLORIA
- nincs kategorizálva Dimplex
- nincs kategorizálva FireAngel
- nincs kategorizálva Grandstream
- nincs kategorizálva Teac
- nincs kategorizálva Master
- nincs kategorizálva D-Link
- nincs kategorizálva Clarion
- nincs kategorizálva Fischer
- nincs kategorizálva Baumr-AG
- nincs kategorizálva Aspes
- nincs kategorizálva Shindaiwa
- nincs kategorizálva Media-Tech
- nincs kategorizálva Avanti
- nincs kategorizálva OKAY
- nincs kategorizálva Scott
- nincs kategorizálva Blustream
- nincs kategorizálva ProfiCook
- nincs kategorizálva E-ast
- nincs kategorizálva Humminbird
- nincs kategorizálva Grillmeister
- nincs kategorizálva TC Helicon
- nincs kategorizálva Saturn
- nincs kategorizálva Milesight
- nincs kategorizálva EQ-3
- nincs kategorizálva Forza
- nincs kategorizálva Fisher & Paykel
- nincs kategorizálva Kenmore
- nincs kategorizálva Metra
- nincs kategorizálva Røde
- nincs kategorizálva TFA
- nincs kategorizálva Monacor
- nincs kategorizálva Cylinda
- nincs kategorizálva Shimano
- nincs kategorizálva Weston
- nincs kategorizálva Huion
- nincs kategorizálva MXL
- nincs kategorizálva Thermex
- nincs kategorizálva IDIS
- nincs kategorizálva Hayward
- nincs kategorizálva Epiphan
- nincs kategorizálva DCG
- nincs kategorizálva Hestan
- nincs kategorizálva Lanaform
- nincs kategorizálva Boneco
- nincs kategorizálva Tesy
- nincs kategorizálva Scanstrut
- nincs kategorizálva TOGU
- nincs kategorizálva S.M.S.L
- nincs kategorizálva Leifheit
- nincs kategorizálva Melissa
- nincs kategorizálva Anthem
- nincs kategorizálva Janitza
- nincs kategorizálva Sheeran Looper
- nincs kategorizálva Zephyr
- nincs kategorizálva One For All
- nincs kategorizálva IK Multimedia
- nincs kategorizálva Zhiyun
- nincs kategorizálva Trotec
- nincs kategorizálva McIntosh
- nincs kategorizálva Sauter
- nincs kategorizálva ION
- nincs kategorizálva Efbe-Schott
- nincs kategorizálva LD Systems
- nincs kategorizálva Nilfisk
- nincs kategorizálva Eurochron
- nincs kategorizálva Manta
- nincs kategorizálva Proel
- nincs kategorizálva Jamo
- nincs kategorizálva Blaupunkt
- nincs kategorizálva U-Line
- nincs kategorizálva Deaf Bonce
- nincs kategorizálva Oricom
- nincs kategorizálva EcoFlow
- nincs kategorizálva NZXT
- nincs kategorizálva Veripart
- nincs kategorizálva NAD
- nincs kategorizálva Ilve
- nincs kategorizálva Viper
- nincs kategorizálva Apricorn
- nincs kategorizálva Gre
- nincs kategorizálva Pancontrol
- nincs kategorizálva Mio
- nincs kategorizálva Witt
- nincs kategorizálva AstralPool
- nincs kategorizálva Easy Home
- nincs kategorizálva Yealink
- nincs kategorizálva TSC
- nincs kategorizálva Korona
- nincs kategorizálva Hozelock
- nincs kategorizálva Chacon
- nincs kategorizálva Stadler Form
- nincs kategorizálva Minn Kota
- nincs kategorizálva Elro
- nincs kategorizálva Crofton
- nincs kategorizálva InfiRay
- nincs kategorizálva Bertazzoni
- nincs kategorizálva Fluke
- nincs kategorizálva Mobicool
- nincs kategorizálva Moxa
- nincs kategorizálva Foster
- nincs kategorizálva Thomann
- nincs kategorizálva DOD
- nincs kategorizálva Datapath
- nincs kategorizálva Sagem
- nincs kategorizálva Hammond
- nincs kategorizálva Princeton Tec
- nincs kategorizálva Pro-User
- nincs kategorizálva Inglesina
- nincs kategorizálva Hansa
- nincs kategorizálva Thetford
- nincs kategorizálva Perixx
- nincs kategorizálva Uni-T
- nincs kategorizálva Razer
- nincs kategorizálva T-Rex
- nincs kategorizálva Taurus
- nincs kategorizálva Comfee
- nincs kategorizálva Cosori
- nincs kategorizálva Samson
- nincs kategorizálva Leitz
- nincs kategorizálva Be Quiet!
- nincs kategorizálva Signature
- nincs kategorizálva Delta
- nincs kategorizálva Zipper
- nincs kategorizálva Cayin
- nincs kategorizálva Bebe Confort
- nincs kategorizálva Gosund
- nincs kategorizálva TomTom
- nincs kategorizálva Jay-Tech
- nincs kategorizálva Busch-Jaeger
- nincs kategorizálva Olympia
- nincs kategorizálva Logik
- nincs kategorizálva Tineco
- nincs kategorizálva NEO Tools
- nincs kategorizálva Domyos
- nincs kategorizálva Millenium
- nincs kategorizálva Bavaria By Einhell
- nincs kategorizálva Mackie
- nincs kategorizálva Soundcraft
- nincs kategorizálva Vonyx
- nincs kategorizálva Rossmax
- nincs kategorizálva Fiap
- nincs kategorizálva Tronic
- nincs kategorizálva Alto
- nincs kategorizálva Metrix
- nincs kategorizálva Delta Dore
- nincs kategorizálva Posiflex
- nincs kategorizálva Hendi
- nincs kategorizálva Peerless-AV
- nincs kategorizálva ZKTeco
- nincs kategorizálva Abus
- nincs kategorizálva Maytag
- nincs kategorizálva La Crosse Technology
- nincs kategorizálva SureFire
- nincs kategorizálva Vivotek
- nincs kategorizálva AG Neovo
- nincs kategorizálva AFK
- nincs kategorizálva Polaris
- nincs kategorizálva KKT Kolbe
- nincs kategorizálva Gree
- nincs kategorizálva Infinity
- nincs kategorizálva Fulgor Milano
- nincs kategorizálva Rovo Kids
- nincs kategorizálva Walrus Audio
- nincs kategorizálva BEEM
- nincs kategorizálva Barazza
- nincs kategorizálva Arlo
- nincs kategorizálva Magnat
- nincs kategorizálva Bang & Olufsen
- nincs kategorizálva Trust
- nincs kategorizálva Herkules
- nincs kategorizálva UDG Gear
- nincs kategorizálva GAO
- nincs kategorizálva Iiyama
- nincs kategorizálva Yukon
- nincs kategorizálva Chief
- nincs kategorizálva AKAI
- nincs kategorizálva Porter-Cable
- nincs kategorizálva Tiptel
- nincs kategorizálva Finder
- nincs kategorizálva Konig
- nincs kategorizálva Marmitek
- nincs kategorizálva H.Koenig
- nincs kategorizálva Stabo
- nincs kategorizálva TechniSat
- nincs kategorizálva Seiki
- nincs kategorizálva Chipolino
- nincs kategorizálva 3M
- nincs kategorizálva ARRI
- nincs kategorizálva Tanaka
- nincs kategorizálva GlobalTronics
- nincs kategorizálva Gtech
- nincs kategorizálva TDE Instruments
- nincs kategorizálva Line 6
- nincs kategorizálva Crelando
- nincs kategorizálva Jensen
- nincs kategorizálva Megger
- nincs kategorizálva Polyend
- nincs kategorizálva Pyle
- nincs kategorizálva Emerson
- nincs kategorizálva Shark
- nincs kategorizálva Computherm
- nincs kategorizálva MuxLab
- nincs kategorizálva Lumens
- nincs kategorizálva Audioengine
- nincs kategorizálva Testboy
- nincs kategorizálva AVer
- nincs kategorizálva Everdure
- nincs kategorizálva Veritas
- nincs kategorizálva Sôlt
- nincs kategorizálva DeWalt
- nincs kategorizálva AVMATRIX
- nincs kategorizálva Kalorik
- nincs kategorizálva Morphy Richards
- nincs kategorizálva Sanyo
- nincs kategorizálva Steinel
- nincs kategorizálva Hacienda
- nincs kategorizálva Kemo
- nincs kategorizálva Constructa
- nincs kategorizálva Rolls
- nincs kategorizálva Frilec
- nincs kategorizálva Laica
- nincs kategorizálva Salora
- nincs kategorizálva Sunding
- nincs kategorizálva IFM
- nincs kategorizálva Healthy Choice
- nincs kategorizálva Musical Fidelity
- nincs kategorizálva Rangemaster
- nincs kategorizálva DataVideo
- nincs kategorizálva Waldbeck
- nincs kategorizálva Eheim
- nincs kategorizálva Telestar
- nincs kategorizálva A-NeuVideo
- nincs kategorizálva Lenco
- nincs kategorizálva Wachendorff
- nincs kategorizálva Greisinger
- nincs kategorizálva Sonel
- nincs kategorizálva Dangerous Music
- nincs kategorizálva Wiha
- nincs kategorizálva CRUX
- nincs kategorizálva Roccat
- nincs kategorizálva Maxell
- nincs kategorizálva Solplanet
- nincs kategorizálva Junkers
- nincs kategorizálva JMAZ Lighting
- nincs kategorizálva Sanitaire
- nincs kategorizálva Alpina
- nincs kategorizálva Stinger
- nincs kategorizálva GA.MA
- nincs kategorizálva Atlona
- nincs kategorizálva Statron
- nincs kategorizálva Watson
- nincs kategorizálva Corsair
- nincs kategorizálva Schneider
- nincs kategorizálva Corel
- nincs kategorizálva Gastroback
- nincs kategorizálva Kyoritsu
- nincs kategorizálva Bernina
- nincs kategorizálva AJA
- nincs kategorizálva LEDs-ON
- nincs kategorizálva Lindy
- nincs kategorizálva Infantino
- nincs kategorizálva Cudy
- nincs kategorizálva Philco
- nincs kategorizálva JYSK
- nincs kategorizálva Brandson
- nincs kategorizálva ECG
- nincs kategorizálva Foppapedretti
- nincs kategorizálva Audiotec Fischer
- nincs kategorizálva Stanley
- nincs kategorizálva NACON
- nincs kategorizálva Danfoss
- nincs kategorizálva Uniden
- nincs kategorizálva JLab
- nincs kategorizálva Victrola
- nincs kategorizálva Hurricane
- nincs kategorizálva Busch + Müller
- nincs kategorizálva LiftMaster
- nincs kategorizálva Fender
- nincs kategorizálva Vorago
- nincs kategorizálva Gaggenau
- nincs kategorizálva Technika
- nincs kategorizálva Arctic Cooling
- nincs kategorizálva Majority
- nincs kategorizálva Areca
- nincs kategorizálva Rotel
- nincs kategorizálva Hertz
- nincs kategorizálva Impact
- nincs kategorizálva Leica
- nincs kategorizálva Azden
- nincs kategorizálva Bowers & Wilkins
- nincs kategorizálva Barco
- nincs kategorizálva Thinkware
- nincs kategorizálva QNAP
- nincs kategorizálva Franklin
- nincs kategorizálva Quantum
- nincs kategorizálva Mean Well
- nincs kategorizálva FBT
- nincs kategorizálva Vemer
- nincs kategorizálva Zenec
- nincs kategorizálva Vornado
- nincs kategorizálva Emko
- nincs kategorizálva Interstuhl
- nincs kategorizálva KEF
- nincs kategorizálva Newland
- nincs kategorizálva Kaiser
- nincs kategorizálva Burris
- nincs kategorizálva Esatto
- nincs kategorizálva Grässlin
- nincs kategorizálva MDT
- nincs kategorizálva Franke
- nincs kategorizálva NEC
- nincs kategorizálva Audiolab
- nincs kategorizálva Ufesa
- nincs kategorizálva Sekonic
- nincs kategorizálva Meireles
- nincs kategorizálva Capital Sports
- nincs kategorizálva Texas Instruments
- nincs kategorizálva Atlas Sound
- nincs kategorizálva Proctor Silex
- nincs kategorizálva Ernesto
- nincs kategorizálva Silverline
- nincs kategorizálva AKG
- nincs kategorizálva Vonroc
- nincs kategorizálva Marshall Electronics
- nincs kategorizálva Trebs
- nincs kategorizálva Galanz
- nincs kategorizálva Taylor
- nincs kategorizálva Ashly
- nincs kategorizálva AudioControl
- nincs kategorizálva Rigol
- nincs kategorizálva CM Storm
- nincs kategorizálva Graco
- nincs kategorizálva Fanvil
- nincs kategorizálva Scandomestic
- nincs kategorizálva Soundmaster
- nincs kategorizálva New Pol
- nincs kategorizálva Crock-Pot
- nincs kategorizálva Neutrik
- nincs kategorizálva Nitecore
- nincs kategorizálva Audioline
- nincs kategorizálva Monitor Audio
- nincs kategorizálva DMT
- nincs kategorizálva Rinnai
- nincs kategorizálva Steinberg
- nincs kategorizálva Dormakaba
- nincs kategorizálva Cameo
- nincs kategorizálva Cotech
- nincs kategorizálva Audac
- nincs kategorizálva Traxxas
- nincs kategorizálva Fresh 'n Rebel
- nincs kategorizálva Technical Pro
- nincs kategorizálva Martin
- nincs kategorizálva Alphatronics
- nincs kategorizálva AYA
- nincs kategorizálva Siig
- nincs kategorizálva Yorkville
- nincs kategorizálva Stabila
- nincs kategorizálva MBM
- nincs kategorizálva Recaro
- nincs kategorizálva GoClever
- nincs kategorizálva WMF
- nincs kategorizálva Wolf
- nincs kategorizálva Rockford Fosgate
- nincs kategorizálva Sensiplast
- nincs kategorizálva Krüger&Matz
- nincs kategorizálva Salus
- nincs kategorizálva Dual
- nincs kategorizálva Elo
- nincs kategorizálva Inter-Tech
- nincs kategorizálva Ebro
- nincs kategorizálva Getac
- nincs kategorizálva ICOM
- nincs kategorizálva Velbus
- nincs kategorizálva Eaton
- nincs kategorizálva Projecta
- nincs kategorizálva Brandt
- nincs kategorizálva Novation
- nincs kategorizálva Artecta
- nincs kategorizálva Noctua
- nincs kategorizálva Gefen
- nincs kategorizálva Graef
- nincs kategorizálva Ambient Weather
- nincs kategorizálva Warm Audio
- nincs kategorizálva Dirt Devil
- nincs kategorizálva Edilkamin
- nincs kategorizálva Kubota
- nincs kategorizálva Wharfedale
- nincs kategorizálva Edge
- nincs kategorizálva M-e
- nincs kategorizálva Cardo
- nincs kategorizálva Kathrein
- nincs kategorizálva Avenview
- nincs kategorizálva Homematic IP
- nincs kategorizálva IStarUSA
- nincs kategorizálva Oase
- nincs kategorizálva Lantronix
- nincs kategorizálva Adobe
- nincs kategorizálva Yaesu
- nincs kategorizálva WAGAN
- nincs kategorizálva Ketron
- nincs kategorizálva Panduit
- nincs kategorizálva HQ Power
- nincs kategorizálva Elation
- nincs kategorizálva RCA
- nincs kategorizálva Arendo
- nincs kategorizálva Somfy
- nincs kategorizálva Vocopro
- nincs kategorizálva Outwell
- nincs kategorizálva Axis
- nincs kategorizálva Nintendo
- nincs kategorizálva BBB
- nincs kategorizálva SunPower
- nincs kategorizálva Biohort
- nincs kategorizálva Beper
- nincs kategorizálva Insta360
- nincs kategorizálva Optex
- nincs kategorizálva Bestron
- nincs kategorizálva Vacmaster
- nincs kategorizálva HTC
- nincs kategorizálva Breville
- nincs kategorizálva TAURUS Titanium
- nincs kategorizálva Postium
- nincs kategorizálva Magnus
- nincs kategorizálva Thermaltake
- nincs kategorizálva Orion
- nincs kategorizálva Melinera
- nincs kategorizálva Blizzard
- nincs kategorizálva Medeli
- nincs kategorizálva Varta
- nincs kategorizálva Technicolor
- nincs kategorizálva Palmer
- nincs kategorizálva Tiptop Audio
- nincs kategorizálva Antari
- nincs kategorizálva Altronix
- nincs kategorizálva Marvel
- nincs kategorizálva Imperial
- nincs kategorizálva Soler & Palau
- nincs kategorizálva Hover-1
- nincs kategorizálva Kicker
- nincs kategorizálva Alpha Tools
- nincs kategorizálva Creative
- nincs kategorizálva Pattfield
- nincs kategorizálva EverFocus
- nincs kategorizálva Elektron
- nincs kategorizálva SereneLife
- nincs kategorizálva Ravanson
- nincs kategorizálva BLANCO
- nincs kategorizálva Multimetrix
- nincs kategorizálva NOCO
- nincs kategorizálva DBX
- nincs kategorizálva Teesa
- nincs kategorizálva Sangean
- nincs kategorizálva Carrier
- nincs kategorizálva Joby
- nincs kategorizálva Pontec
- nincs kategorizálva Schuberth
- nincs kategorizálva JAYS
- nincs kategorizálva Salter
- nincs kategorizálva Equip
- nincs kategorizálva Deltaco Gaming
- nincs kategorizálva Luxor
- nincs kategorizálva ECS
- nincs kategorizálva Flavel
- nincs kategorizálva Metz
- nincs kategorizálva Deye
- nincs kategorizálva Genius
- nincs kategorizálva Emeril Lagasse
- nincs kategorizálva Camille Bauer
- nincs kategorizálva Ipevo
- nincs kategorizálva Valueline
- nincs kategorizálva Scancool
- nincs kategorizálva Becken
- nincs kategorizálva Swann
- nincs kategorizálva Heckler Design
- nincs kategorizálva Brevi
- nincs kategorizálva Olight
- nincs kategorizálva Best Service
- nincs kategorizálva Kino Flo
- nincs kategorizálva Holzmann
- nincs kategorizálva Fein
- nincs kategorizálva Elvid
- nincs kategorizálva InfaSecure
- nincs kategorizálva PowerBass
- nincs kategorizálva Sirius
- nincs kategorizálva Gamber-Johnson
- nincs kategorizálva Challenge Xtreme
- nincs kategorizálva Arris
- nincs kategorizálva Definitive Technology
- nincs kategorizálva Focal
- nincs kategorizálva Adj
- nincs kategorizálva Revlon
- nincs kategorizálva Anker
- nincs kategorizálva Smoby
- nincs kategorizálva Bikemate
- nincs kategorizálva I-TEC
- nincs kategorizálva Gravity
- nincs kategorizálva Gabor
- nincs kategorizálva Anthro
- nincs kategorizálva Wacom
- nincs kategorizálva MB Quart
- nincs kategorizálva Primus
- nincs kategorizálva Weber
- nincs kategorizálva Havis
- nincs kategorizálva Genie
- nincs kategorizálva H-Tronic
- nincs kategorizálva Legamaster
- nincs kategorizálva Lectrosonics
- nincs kategorizálva Hughes & Kettner
- nincs kategorizálva NovaStar
- nincs kategorizálva Swift
- nincs kategorizálva Victron Energy
- nincs kategorizálva IFi Audio
- nincs kategorizálva AREXX
- nincs kategorizálva ATIKA
- nincs kategorizálva Cleco
- nincs kategorizálva OneConcept
- nincs kategorizálva Haeger
- nincs kategorizálva ILive
- nincs kategorizálva Absco
- nincs kategorizálva Audix
- nincs kategorizálva Neumärker
- nincs kategorizálva NANO Modules
- nincs kategorizálva Flame
- nincs kategorizálva Flaem
- nincs kategorizálva Hensel
- nincs kategorizálva Spear & Jackson
- nincs kategorizálva PCE
- nincs kategorizálva Duracell
- nincs kategorizálva Westland
- nincs kategorizálva Rapoo
- nincs kategorizálva OM SYSTEM
- nincs kategorizálva President
- nincs kategorizálva Lowepro
- nincs kategorizálva IVT
- nincs kategorizálva Edwards
- nincs kategorizálva Gustard
- nincs kategorizálva Vivolink
- nincs kategorizálva AS Schwabe
- nincs kategorizálva Deditec
- nincs kategorizálva WEG
- nincs kategorizálva Bluebird
- nincs kategorizálva Eltako
- nincs kategorizálva Palmako
- nincs kategorizálva Weidmüller
- nincs kategorizálva Dunlop
- nincs kategorizálva Cotek
- nincs kategorizálva Grand Effects
- nincs kategorizálva Tascam
- nincs kategorizálva Finnlo
- nincs kategorizálva Homedics
- nincs kategorizálva Happy Plugs
- nincs kategorizálva Concept2
- nincs kategorizálva Linksys
- nincs kategorizálva Olimpia Splendid
- nincs kategorizálva Teltonika
- nincs kategorizálva Sitecom
- nincs kategorizálva Trixie
- nincs kategorizálva Mistral
- nincs kategorizálva ACTi
- nincs kategorizálva Schwaiger
- nincs kategorizálva Christmas Time
- nincs kategorizálva Stannah
- nincs kategorizálva Multibrackets
- nincs kategorizálva LifeSpan
- nincs kategorizálva Neewer
- nincs kategorizálva FiiO
- nincs kategorizálva Christmaxx
- nincs kategorizálva EasyMaxx
- nincs kategorizálva Maxxmee
- nincs kategorizálva Heitronic
- nincs kategorizálva Elmo
- nincs kategorizálva Comprehensive
- nincs kategorizálva Toro
- nincs kategorizálva Lund
- nincs kategorizálva Ocean Matrix
- nincs kategorizálva MAK
- nincs kategorizálva Life Fitness
- nincs kategorizálva Orava
- nincs kategorizálva Dobot
- nincs kategorizálva Cougar
- nincs kategorizálva Arçelik
- nincs kategorizálva Paxton
- nincs kategorizálva Razor
- nincs kategorizálva Roxio
- nincs kategorizálva Vitek
- nincs kategorizálva SurgeX
- nincs kategorizálva Enhance
- nincs kategorizálva Digitalinx
- nincs kategorizálva Anton/Bauer
- nincs kategorizálva Alfatron
- nincs kategorizálva Bolt
- nincs kategorizálva APA
- nincs kategorizálva Mophie
- nincs kategorizálva Brady
- nincs kategorizálva Eurom
- nincs kategorizálva Govee
- nincs kategorizálva QOMO
- nincs kategorizálva Astro
- nincs kategorizálva Xvive
- nincs kategorizálva Bixolon
- nincs kategorizálva Magic Chef
- nincs kategorizálva Dot Line
- nincs kategorizálva WHD
- nincs kategorizálva Sound Devices
- nincs kategorizálva Match
- nincs kategorizálva Doffler
- nincs kategorizálva Geneva
- nincs kategorizálva Foreo
- nincs kategorizálva Topeak
- nincs kategorizálva Zotac
- nincs kategorizálva TechBite
- nincs kategorizálva Sauber
- nincs kategorizálva Cocraft
- nincs kategorizálva Lupine
- nincs kategorizálva Thorens
- nincs kategorizálva Indiana Line
- nincs kategorizálva Craftsman
- nincs kategorizálva Sumiko
- nincs kategorizálva Blackburn
- nincs kategorizálva Laserliner
- nincs kategorizálva RADEMACHER
- nincs kategorizálva SoundMagic
- nincs kategorizálva Majestic
- nincs kategorizálva Sebo
- nincs kategorizálva Savio
- nincs kategorizálva Maestro
- nincs kategorizálva Kern
- nincs kategorizálva Graphite
- nincs kategorizálva Reflexion
- nincs kategorizálva Enermax
- nincs kategorizálva Smartwares
- nincs kategorizálva Salicru
- nincs kategorizálva Megasat
- nincs kategorizálva Eureka
- nincs kategorizálva Teufel
- nincs kategorizálva Sogo
- nincs kategorizálva Hikmicro
- nincs kategorizálva IGET
- nincs kategorizálva TensCare
- nincs kategorizálva Beautifly
- nincs kategorizálva Crosley
- nincs kategorizálva Aqara
- nincs kategorizálva Ugreen
- nincs kategorizálva Vincent
- nincs kategorizálva Kopp
- nincs kategorizálva DPA
- nincs kategorizálva NuPrime
- nincs kategorizálva REVO
- nincs kategorizálva Maytronics
- nincs kategorizálva Park Tool
- nincs kategorizálva George Foreman
- nincs kategorizálva InLine
- nincs kategorizálva Fluval
- nincs kategorizálva Advance Acoustic
- nincs kategorizálva Nutrichef
- nincs kategorizálva Grundfos
- nincs kategorizálva Cubot
- nincs kategorizálva Kokido
- nincs kategorizálva J5create
- nincs kategorizálva SwitchBot
- nincs kategorizálva MoFi
- nincs kategorizálva Apelson
- nincs kategorizálva Adventuridge
- nincs kategorizálva Casa Deco
- nincs kategorizálva Reloop
- nincs kategorizálva Hazet
- nincs kategorizálva Snow Joe
- nincs kategorizálva Glem Gas
- nincs kategorizálva Primewire
- nincs kategorizálva Euromaid
- nincs kategorizálva 8BitDo
- nincs kategorizálva CSL
- nincs kategorizálva Oreck
- nincs kategorizálva Tepro
- nincs kategorizálva XCell
- nincs kategorizálva Perfect Christmas
- nincs kategorizálva I.safe Mobile
- nincs kategorizálva Newstar
- nincs kategorizálva Artsound
- nincs kategorizálva Vivitar
- nincs kategorizálva Vogel's
- nincs kategorizálva Char-Broil
- nincs kategorizálva BSS Audio
- nincs kategorizálva Chandler
- nincs kategorizálva Flama
- nincs kategorizálva HK Audio
- nincs kategorizálva Sevenoak
- nincs kategorizálva Rittal
- nincs kategorizálva Cherry
- nincs kategorizálva Lasko
- nincs kategorizálva Yellow Garden Line
- nincs kategorizálva SWIT
- nincs kategorizálva Belkin
- nincs kategorizálva Bebob
- nincs kategorizálva Kahayan
- nincs kategorizálva Gen Energy
- nincs kategorizálva Anywhere Cart
- nincs kategorizálva Xcellon
- nincs kategorizálva RGBlink
- nincs kategorizálva Heckler
- nincs kategorizálva Lewitt
- nincs kategorizálva CEDAR
- nincs kategorizálva Kopul
- nincs kategorizálva SmallRig
- nincs kategorizálva Fiilex
- nincs kategorizálva Morley
- nincs kategorizálva KJB Security Products
- nincs kategorizálva Zeiss
- nincs kategorizálva Vertex
- nincs kategorizálva K&M
- nincs kategorizálva Elgato
- nincs kategorizálva Sky-Watcher
- nincs kategorizálva Wimberley
- nincs kategorizálva Sescom
- nincs kategorizálva PTZ Optics
- nincs kategorizálva KanexPro
- nincs kategorizálva Rupert Neve Designs
- nincs kategorizálva ARC
- nincs kategorizálva DEERSYNC
- nincs kategorizálva Key Digital
- nincs kategorizálva Cranborne Audio
- nincs kategorizálva Murideo
- nincs kategorizálva Glide Gear
- nincs kategorizálva Lian Li
- nincs kategorizálva Hosa
- nincs kategorizálva Pawa
- nincs kategorizálva Vortex
- nincs kategorizálva Kramer
- nincs kategorizálva Serpent
- nincs kategorizálva Whirlwind
- nincs kategorizálva Erica Synths
- nincs kategorizálva Arkon
- nincs kategorizálva Analog Way
- nincs kategorizálva Profoto
- nincs kategorizálva ChyTV
- nincs kategorizálva ToughTested
- nincs kategorizálva Robus
- nincs kategorizálva ART
- nincs kategorizálva Intellijel
- nincs kategorizálva BZBGear
- nincs kategorizálva BirdDog
- nincs kategorizálva Manfrotto
- nincs kategorizálva Lemair
- nincs kategorizálva Stamina
- nincs kategorizálva AMX
- nincs kategorizálva Ideal
- nincs kategorizálva Rosco
- nincs kategorizálva Matsui
- nincs kategorizálva Zibro
- nincs kategorizálva Fysic
- nincs kategorizálva Quigg
- nincs kategorizálva Wiko
- nincs kategorizálva A.O. Smith
- nincs kategorizálva Ade
- nincs kategorizálva Aduro
- nincs kategorizálva Allnet
- nincs kategorizálva Airlux
- nincs kategorizálva Aligator
- nincs kategorizálva Ambrogio
- nincs kategorizálva Allied Telesis
- nincs kategorizálva Allibert
- nincs kategorizálva Alienware
- nincs kategorizálva ABC Design
- nincs kategorizálva Amfra
- nincs kategorizálva Ansmann
- nincs kategorizálva Alcon
- nincs kategorizálva Airlive
- nincs kategorizálva A4tech
- nincs kategorizálva Ampeg
- nincs kategorizálva Amplicom
- nincs kategorizálva Amprobe
- nincs kategorizálva Argon
- nincs kategorizálva American Audio
- nincs kategorizálva Aquapur
- nincs kategorizálva Aeris
- nincs kategorizálva Ascom
- nincs kategorizálva Alpen Kreuzer
- nincs kategorizálva Reflecta
- nincs kategorizálva Argus
- nincs kategorizálva ATN
- nincs kategorizálva Ziggo
- nincs kategorizálva Intermatic
- nincs kategorizálva Flamingo
- nincs kategorizálva Toolland
- nincs kategorizálva Icy Box
- nincs kategorizálva Brennenstuhl
- nincs kategorizálva Ferm
- nincs kategorizálva MJX
- nincs kategorizálva Hirschmann
- nincs kategorizálva Kruidvat
- nincs kategorizálva Absima
- nincs kategorizálva Audison
- nincs kategorizálva Salton
- nincs kategorizálva Proteca
- nincs kategorizálva Topmove
- nincs kategorizálva Lexibook
- nincs kategorizálva Body Solid
- nincs kategorizálva Draper
- nincs kategorizálva Tryton
- nincs kategorizálva Arthur Martin
- nincs kategorizálva Oceanic
- nincs kategorizálva Tiger
- nincs kategorizálva Yale
- nincs kategorizálva Meradiso
- nincs kategorizálva Calor
- nincs kategorizálva Waring Commercial
- nincs kategorizálva Kernau
- nincs kategorizálva Miomare
- nincs kategorizálva BH Fitness
- nincs kategorizálva Tevion
- nincs kategorizálva GPO
- nincs kategorizálva Thermador
- nincs kategorizálva Lucide
- nincs kategorizálva Parisot
- nincs kategorizálva Caliber
- nincs kategorizálva Skil
- nincs kategorizálva Eminent
- nincs kategorizálva Pressalit
- nincs kategorizálva SilverStone
- nincs kategorizálva Oster
- nincs kategorizálva Kichler
- nincs kategorizálva VAX
- nincs kategorizálva Trekstor
- nincs kategorizálva Vestel
- nincs kategorizálva Sinbo
- nincs kategorizálva Bushnell
- nincs kategorizálva Jata
- nincs kategorizálva VirtuFit
- nincs kategorizálva Swan
- nincs kategorizálva Fritel
- nincs kategorizálva Ordex
- nincs kategorizálva Itho
- nincs kategorizálva Targus
- nincs kategorizálva Q-CONNECT
- nincs kategorizálva Landmann
- nincs kategorizálva Sicce
- nincs kategorizálva Britax
- nincs kategorizálva Monogram
- nincs kategorizálva Hard Head
- nincs kategorizálva Exibel
- nincs kategorizálva Medela
- nincs kategorizálva Easy Camp
- nincs kategorizálva Anslut
- nincs kategorizálva Meec Tools
- nincs kategorizálva Auto Joe
- nincs kategorizálva Fortinet
- nincs kategorizálva Youin
- nincs kategorizálva Valore
- nincs kategorizálva Accucold
- nincs kategorizálva Sun Joe
- nincs kategorizálva Perfecta
- nincs kategorizálva Jumbo
- nincs kategorizálva Cricut
- nincs kategorizálva Hähnel
- nincs kategorizálva Ferplast
- nincs kategorizálva EWT
- nincs kategorizálva Enduro
- nincs kategorizálva Aukey
- nincs kategorizálva Dremel
- nincs kategorizálva KlikaanKlikuit
- nincs kategorizálva Gemini
- nincs kategorizálva Easypix
- nincs kategorizálva Berg
- nincs kategorizálva Simplified MFG
- nincs kategorizálva Vision
- nincs kategorizálva Axa
- nincs kategorizálva ABB
- nincs kategorizálva Mellerware
- nincs kategorizálva Intergas
- nincs kategorizálva Silva
- nincs kategorizálva Energenie
- nincs kategorizálva Termozeta
- nincs kategorizálva Bella
- nincs kategorizálva Palson
- nincs kategorizálva Eldom
- nincs kategorizálva Valeton
- nincs kategorizálva Jocca
- nincs kategorizálva Nilox
- nincs kategorizálva Vango
- nincs kategorizálva Ventura
- nincs kategorizálva Sonos
- nincs kategorizálva Summit Audio
- nincs kategorizálva SKS
- nincs kategorizálva Musway
- nincs kategorizálva Kensington
- nincs kategorizálva Nautilus
- nincs kategorizálva Byron
- nincs kategorizálva Cresta
- nincs kategorizálva Brigmton
- nincs kategorizálva Sunstech
- nincs kategorizálva Smith & Wesson
- nincs kategorizálva Elektrobock
- nincs kategorizálva Nabo
- nincs kategorizálva Defy
- nincs kategorizálva DeLock
- nincs kategorizálva Avalon
- nincs kategorizálva Plant Craft
- nincs kategorizálva Dubatti
- nincs kategorizálva Bionaire
- nincs kategorizálva Maginon
- nincs kategorizálva Sylvania
- nincs kategorizálva Campomatic
- nincs kategorizálva Patton
- nincs kategorizálva Igloo
- nincs kategorizálva Senco
- nincs kategorizálva Tork
- nincs kategorizálva Techly
- nincs kategorizálva Numatic
- nincs kategorizálva Swissvoice
- nincs kategorizálva Vaude
- nincs kategorizálva Totolink
- nincs kategorizálva Sunny
- nincs kategorizálva BlueBuilt
- nincs kategorizálva Gazelle
- nincs kategorizálva Profile
- nincs kategorizálva Marquant
- nincs kategorizálva Nibe
- nincs kategorizálva Damixa
- nincs kategorizálva Da-Lite
- nincs kategorizálva Ferroli
- nincs kategorizálva First Austria
- nincs kategorizálva Ednet
- nincs kategorizálva Bowflex
- nincs kategorizálva AVerMedia
- nincs kategorizálva Visage
- nincs kategorizálva Celestron
- nincs kategorizálva CaterCool
- nincs kategorizálva Master Lock
- nincs kategorizálva Matrox
- nincs kategorizálva Seiko
- nincs kategorizálva Maktec
- nincs kategorizálva Binatone
- nincs kategorizálva Connect IT
- nincs kategorizálva Steren
- nincs kategorizálva Perel
- nincs kategorizálva Nuna
- nincs kategorizálva Eico
- nincs kategorizálva Polk
- nincs kategorizálva Nero
- nincs kategorizálva Kubo
- nincs kategorizálva Exagerate
- nincs kategorizálva Air King
- nincs kategorizálva Gossen
- nincs kategorizálva Elba
- nincs kategorizálva Flir
- nincs kategorizálva KiddyGuard
- nincs kategorizálva Proline
- nincs kategorizálva Livarno
- nincs kategorizálva Barkan
- nincs kategorizálva Netis
- nincs kategorizálva Coby
- nincs kategorizálva Royal Sovereign
- nincs kategorizálva King
- nincs kategorizálva AcuRite
- nincs kategorizálva Ergobaby
- nincs kategorizálva Envivo
- nincs kategorizálva Petzl
- nincs kategorizálva True
- nincs kategorizálva Galaxy Audio
- nincs kategorizálva Black Diamond
- nincs kategorizálva ESYLUX
- nincs kategorizálva Ventus
- nincs kategorizálva TOTO
- nincs kategorizálva Technoline
- nincs kategorizálva Osann
- nincs kategorizálva Lindam
- nincs kategorizálva Kelvinator
- nincs kategorizálva Goliath
- nincs kategorizálva Yamato
- nincs kategorizálva Vivo
- nincs kategorizálva Belgacom
- nincs kategorizálva SEB
- nincs kategorizálva Malmbergs
- nincs kategorizálva Phoenix
- nincs kategorizálva AV:link
- nincs kategorizálva Power Craft
- nincs kategorizálva Otolift
- nincs kategorizálva GBC
- nincs kategorizálva Prenatal
- nincs kategorizálva Champion
- nincs kategorizálva Tvilum
- nincs kategorizálva Heylo
- nincs kategorizálva TacTic
- nincs kategorizálva Nolte
- nincs kategorizálva G3
- nincs kategorizálva Peach
- nincs kategorizálva Pure
- nincs kategorizálva Lescha
- nincs kategorizálva Buffalo
- nincs kategorizálva Vello
- nincs kategorizálva Jenn-Air
- nincs kategorizálva R-Vent
- nincs kategorizálva Woood
- nincs kategorizálva Audiovox
- nincs kategorizálva Carpigiani
- nincs kategorizálva Davis
- nincs kategorizálva ICU
- nincs kategorizálva Daitsu
- nincs kategorizálva Farberware
- nincs kategorizálva CasaFan
- nincs kategorizálva Milectric
- nincs kategorizálva Vicks
- nincs kategorizálva Walkstool
- nincs kategorizálva Macally
- nincs kategorizálva GeoVision
- nincs kategorizálva Kidde
- nincs kategorizálva Apogee
- nincs kategorizálva Nest
- nincs kategorizálva Grothe
- nincs kategorizálva LevelOne
- nincs kategorizálva Kwantum
- nincs kategorizálva Safescan
- nincs kategorizálva Pyle Pro
- nincs kategorizálva Transcend
- nincs kategorizálva Wehkamp
- nincs kategorizálva Profoon
- nincs kategorizálva Svedbergs
- nincs kategorizálva Osprey
- nincs kategorizálva Bunn
- nincs kategorizálva Ninebot
- nincs kategorizálva Siedle
- nincs kategorizálva Cilio
- nincs kategorizálva LaCie
- nincs kategorizálva Itho-Daalderop
- nincs kategorizálva Maul
- nincs kategorizálva BabyOno
- nincs kategorizálva Karibu
- nincs kategorizálva Pericles
- nincs kategorizálva Troy-Bilt
- nincs kategorizálva Asaklitt
- nincs kategorizálva Rusta
- nincs kategorizálva Samac
- nincs kategorizálva Waterpik
- nincs kategorizálva SMA
- nincs kategorizálva Kayser
- nincs kategorizálva Autotek
- nincs kategorizálva Safety 1st
- nincs kategorizálva Evga
- nincs kategorizálva Hive
- nincs kategorizálva Brabantia
- nincs kategorizálva Fissler
- nincs kategorizálva Kayoba
- nincs kategorizálva Lexmark
- nincs kategorizálva Inkbird
- nincs kategorizálva Valcom
- nincs kategorizálva Goobay
- nincs kategorizálva Switel
- nincs kategorizálva Hager
- nincs kategorizálva Michelin
- nincs kategorizálva Bopita
- nincs kategorizálva Challenge
- nincs kategorizálva Duux
- nincs kategorizálva Imetec
- nincs kategorizálva Salta
- nincs kategorizálva InFocus
- nincs kategorizálva Bigben
- nincs kategorizálva Playseat
- nincs kategorizálva Topcraft
- nincs kategorizálva Kraftwerk
- nincs kategorizálva Naish
- nincs kategorizálva Festo
- nincs kategorizálva Olivetti
- nincs kategorizálva Massive
- nincs kategorizálva Barska
- nincs kategorizálva Weihrauch Sport
- nincs kategorizálva Blaze
- nincs kategorizálva Hombli
- nincs kategorizálva Martha Stewart
- nincs kategorizálva Lümme
- nincs kategorizálva Springfree
- nincs kategorizálva Ansco
- nincs kategorizálva Goodram
- nincs kategorizálva MADE
- nincs kategorizálva Noma
- nincs kategorizálva IDance
- nincs kategorizálva Habitat
- nincs kategorizálva Maxview
- nincs kategorizálva Yongnuo
- nincs kategorizálva Boso
- nincs kategorizálva Gamma
- nincs kategorizálva Elite
- nincs kategorizálva BOHLT
- nincs kategorizálva Handicare
- nincs kategorizálva Primo
- nincs kategorizálva Rocketfish
- nincs kategorizálva Little Tikes
- nincs kategorizálva Laser
- nincs kategorizálva Creda
- nincs kategorizálva Alba
- nincs kategorizálva Clas Ohlson
- nincs kategorizálva Baninni
- nincs kategorizálva Naxa
- nincs kategorizálva Nemef
- nincs kategorizálva RugGear
- nincs kategorizálva Umidigi
- nincs kategorizálva Saro
- nincs kategorizálva Vogue
- nincs kategorizálva Grixx
- nincs kategorizálva SuperFish
- nincs kategorizálva Luvion
- nincs kategorizálva Aqua Joe
- nincs kategorizálva Innovaphone
- nincs kategorizálva Intel
- nincs kategorizálva Zuiver
- nincs kategorizálva Fantec
- nincs kategorizálva Intermec
- nincs kategorizálva Active Era
- nincs kategorizálva Trigano
- nincs kategorizálva Sweex
- nincs kategorizálva Busch And Müller
- nincs kategorizálva Ices
- nincs kategorizálva Reer
- nincs kategorizálva Vizio
- nincs kategorizálva Cello
- nincs kategorizálva RDL
- nincs kategorizálva Austrian Audio
- nincs kategorizálva Vakoss
- nincs kategorizálva Eberspacher
- nincs kategorizálva Kress
- nincs kategorizálva Hobby
- nincs kategorizálva Zehnder
- nincs kategorizálva Laurastar
- nincs kategorizálva Mx Onda
- nincs kategorizálva Zenit
- nincs kategorizálva Wacker Neuson
- nincs kategorizálva Nûby
- nincs kategorizálva EVE
- nincs kategorizálva Xterra
- nincs kategorizálva Fredenstein
- nincs kategorizálva Playmobil
- nincs kategorizálva Invacare
- nincs kategorizálva Napoleon
- nincs kategorizálva Metronic
- nincs kategorizálva Nanni
- nincs kategorizálva Fuji
- nincs kategorizálva Swissonic
- nincs kategorizálva Schütte
- nincs kategorizálva BRIO
- nincs kategorizálva Aruba
- nincs kategorizálva Waeco
- nincs kategorizálva Natec
- nincs kategorizálva RGV
- nincs kategorizálva Ikan
- nincs kategorizálva Elkay
- nincs kategorizálva IHealth
- nincs kategorizálva Hapro
- nincs kategorizálva Tamiya
- nincs kategorizálva Logicom
- nincs kategorizálva Alfen
- nincs kategorizálva Sound Machines
- nincs kategorizálva Team
- nincs kategorizálva Nikkei
- nincs kategorizálva Petsafe
- nincs kategorizálva TranzX
- nincs kategorizálva Aviom
- nincs kategorizálva UPM
- nincs kategorizálva BABY Born
- nincs kategorizálva Duro
- nincs kategorizálva T'nB
- nincs kategorizálva Ematic
- nincs kategorizálva Palm
- nincs kategorizálva QSC
- nincs kategorizálva Phonak
- nincs kategorizálva Emporia
- nincs kategorizálva Faber
- nincs kategorizálva Cardiostrong
- nincs kategorizálva Hartan
- nincs kategorizálva Xavax
- nincs kategorizálva Emmaljunga
- nincs kategorizálva Tracer
- nincs kategorizálva ZAZU
- nincs kategorizálva Crosscall
- nincs kategorizálva Countryman
- nincs kategorizálva Minolta
- nincs kategorizálva Aerial
- nincs kategorizálva Navman
- nincs kategorizálva Prime3
- nincs kategorizálva Silver Cross
- nincs kategorizálva Victor
- nincs kategorizálva Zagg
- nincs kategorizálva ESI
- nincs kategorizálva Blumfeldt
- nincs kategorizálva Edgestar
- nincs kategorizálva Orbis
- nincs kategorizálva ACE
- nincs kategorizálva Maxicool
- nincs kategorizálva For_Q
- nincs kategorizálva Schaudt
- nincs kategorizálva Avocor
- nincs kategorizálva Lanzar
- nincs kategorizálva DoorBird
- nincs kategorizálva KDK
- nincs kategorizálva FoodSaver
- nincs kategorizálva Vroomshoop
- nincs kategorizálva SureFlap
- nincs kategorizálva GVM
- nincs kategorizálva McGregor
- nincs kategorizálva Nvidia
- nincs kategorizálva Irritrol
- nincs kategorizálva Basbau
- nincs kategorizálva Exit
- nincs kategorizálva CaterChef
- nincs kategorizálva Kasda
- nincs kategorizálva Veho
- nincs kategorizálva Kambrook
- nincs kategorizálva Nevadent
- nincs kategorizálva Plum
- nincs kategorizálva Simrad
- nincs kategorizálva Cellular Line
- nincs kategorizálva Puky
- nincs kategorizálva GFI System
- nincs kategorizálva Humax
- nincs kategorizálva Vaddio
- nincs kategorizálva Berner
- nincs kategorizálva Swarovski Optik
- nincs kategorizálva Gira
- nincs kategorizálva Jung
- nincs kategorizálva Sachtler
- nincs kategorizálva Seagate
- nincs kategorizálva Golden Age Project
- nincs kategorizálva Harvia
- nincs kategorizálva Spin Master
- nincs kategorizálva Bravilor Bonamat
- nincs kategorizálva Blue
- nincs kategorizálva Brinsea
- nincs kategorizálva Genexis
- nincs kategorizálva Genelec
- nincs kategorizálva Maxxter
- nincs kategorizálva Inspire
- nincs kategorizálva Apart
- nincs kategorizálva Venta
- nincs kategorizálva Cadac
- nincs kategorizálva Anchor Audio
- nincs kategorizálva 4moms
- nincs kategorizálva Dantherm
- nincs kategorizálva Interlogix
- nincs kategorizálva Dnt
- nincs kategorizálva Eizo
- nincs kategorizálva Krontaler
- nincs kategorizálva Lyman
- nincs kategorizálva Etekcity
- nincs kategorizálva Genaray
- nincs kategorizálva Balance
- nincs kategorizálva Qualcast
- nincs kategorizálva Cablexpert
- nincs kategorizálva Iomega
- nincs kategorizálva Phil And Teds
- nincs kategorizálva Tornado
- nincs kategorizálva Baby Jogger
- nincs kategorizálva Velux
- nincs kategorizálva Stelton
- nincs kategorizálva Mr Handsfree
- nincs kategorizálva Joovy
- nincs kategorizálva Sommer
- nincs kategorizálva Bodum
- nincs kategorizálva Saitek
- nincs kategorizálva DAS Audio
- nincs kategorizálva Vestfrost
- nincs kategorizálva Leen Bakker
- nincs kategorizálva Eventide
- nincs kategorizálva Audio Pro
- nincs kategorizálva OSO
- nincs kategorizálva Vermeiren
- nincs kategorizálva Kunft
- nincs kategorizálva Radial Engineering
- nincs kategorizálva Fito
- nincs kategorizálva Jotul
- nincs kategorizálva Shoprider
- nincs kategorizálva WHALE
- nincs kategorizálva Shuttle
- nincs kategorizálva Furuno
- nincs kategorizálva Max
- nincs kategorizálva Clage
- nincs kategorizálva Tetra
- nincs kategorizálva Noveen
- nincs kategorizálva Dualit
- nincs kategorizálva Cre8audio
- nincs kategorizálva Nanlite
- nincs kategorizálva Kupper
- nincs kategorizálva Bluesound
- nincs kategorizálva Ledger
- nincs kategorizálva Koenig
- nincs kategorizálva Contour
- nincs kategorizálva BakkerElkhuizen
- nincs kategorizálva Lupilu
- nincs kategorizálva Outdoorchef
- nincs kategorizálva Boyo
- nincs kategorizálva IKRA
- nincs kategorizálva Fakir
- nincs kategorizálva IOttie
- nincs kategorizálva Digi
- nincs kategorizálva Verizon
- nincs kategorizálva XPG
- nincs kategorizálva Valco Baby
- nincs kategorizálva Trio Lighting
- nincs kategorizálva Integra
- nincs kategorizálva Upo
- nincs kategorizálva Vitamix
- nincs kategorizálva Blade
- nincs kategorizálva Rio
- nincs kategorizálva Cadel
- nincs kategorizálva ThinkFun
- nincs kategorizálva Revox
- nincs kategorizálva Emtec
- nincs kategorizálva Ranex
- nincs kategorizálva Truper
- nincs kategorizálva ISDT
- nincs kategorizálva Abac
- nincs kategorizálva Celly
- nincs kategorizálva Comica
- nincs kategorizálva Globo
- nincs kategorizálva ZLine
- nincs kategorizálva Fusion
- nincs kategorizálva Audient
- nincs kategorizálva Adesso
- nincs kategorizálva Paradigm
- nincs kategorizálva C3
- nincs kategorizálva EMSA
- nincs kategorizálva Natuzzi
- nincs kategorizálva Grunkel
- nincs kategorizálva Satel
- nincs kategorizálva Bazooka
- nincs kategorizálva PAX
- nincs kategorizálva K&K Sound
- nincs kategorizálva Dutchbone
- nincs kategorizálva Noise Engineering
- nincs kategorizálva PAC
- nincs kategorizálva Beretta
- nincs kategorizálva Wentronic
- nincs kategorizálva Peerless
- nincs kategorizálva RAVPower
- nincs kategorizálva Hooker
- nincs kategorizálva IHome
- nincs kategorizálva Atomos
- nincs kategorizálva Luxman
- nincs kategorizálva Gitzo
- nincs kategorizálva SeaLife
- nincs kategorizálva Nesco
- nincs kategorizálva Wago
- nincs kategorizálva AIC
- nincs kategorizálva Brydge
- nincs kategorizálva Selec
- nincs kategorizálva Aiphone
- nincs kategorizálva Tivoli Audio
- nincs kategorizálva Senal
- nincs kategorizálva JETI
- nincs kategorizálva Waves
- nincs kategorizálva EQ3
- nincs kategorizálva Karlik
- nincs kategorizálva Comark
- nincs kategorizálva Lervia
- nincs kategorizálva Coline
- nincs kategorizálva N8WERK
- nincs kategorizálva Petri
- nincs kategorizálva Calex
- nincs kategorizálva Satechi
- nincs kategorizálva Skullcandy
- nincs kategorizálva Hansgrohe
- nincs kategorizálva Masport
- nincs kategorizálva 4smarts
- nincs kategorizálva Xaoc
- nincs kategorizálva Beyerdynamic
- nincs kategorizálva Qute
- nincs kategorizálva BabyGO
- nincs kategorizálva Schwinn
- nincs kategorizálva Lanberg
- nincs kategorizálva Friedland
- nincs kategorizálva Megableu
- nincs kategorizálva Nexxt
- nincs kategorizálva Coleman
- nincs kategorizálva Bora
- nincs kategorizálva Magic Care
- nincs kategorizálva Raclet
- nincs kategorizálva Butler
- nincs kategorizálva Weishaupt
- nincs kategorizálva Glock
- nincs kategorizálva Linn
- nincs kategorizálva Iluv
- nincs kategorizálva REMKO
- nincs kategorizálva Monoprice
- nincs kategorizálva Ibiza Sound
- nincs kategorizálva Echo
- nincs kategorizálva Croozer
- nincs kategorizálva TELEX
- nincs kategorizálva Dynamic
- nincs kategorizálva Promethean
- nincs kategorizálva HyperIce
- nincs kategorizálva Home Easy
- nincs kategorizálva Basil
- nincs kategorizálva Munchkin
- nincs kategorizálva Vitalmaxx
- nincs kategorizálva Nxg
- nincs kategorizálva AGM
- nincs kategorizálva Bruder Mannesmann
- nincs kategorizálva Autodesk
- nincs kategorizálva Diana
- nincs kategorizálva Tandberg Data
- nincs kategorizálva Fostex
- nincs kategorizálva Viridian
- nincs kategorizálva Plustek
- nincs kategorizálva Prowise
- nincs kategorizálva Mousetrapper
- nincs kategorizálva SKROSS
- nincs kategorizálva Sikkens
- nincs kategorizálva DEXP
- nincs kategorizálva GolfBuddy
- nincs kategorizálva Lynx
- nincs kategorizálva Thermor
- nincs kategorizálva NodOn
- nincs kategorizálva Endorphin.es
- nincs kategorizálva Deutz
- nincs kategorizálva Optimum
- nincs kategorizálva FIMI
- nincs kategorizálva Jilong
- nincs kategorizálva MIPRO
- nincs kategorizálva Bravilor
- nincs kategorizálva Bracketron
- nincs kategorizálva Solid State Logic
- nincs kategorizálva Pointer
- nincs kategorizálva XYZprinting
- nincs kategorizálva Edision
- nincs kategorizálva Carmen
- nincs kategorizálva MTM
- nincs kategorizálva X-Sense
- nincs kategorizálva De Buyer
- nincs kategorizálva Metapace
- nincs kategorizálva Exo-Terra
- nincs kategorizálva Neets
- nincs kategorizálva OutNowTech
- nincs kategorizálva NAV-TV
- nincs kategorizálva Wooden Camera
- nincs kategorizálva Maclaren
- nincs kategorizálva AdHoc
- nincs kategorizálva AudioQuest
- nincs kategorizálva Powerblade
- nincs kategorizálva HiFi ROSE
- nincs kategorizálva Hayter
- nincs kategorizálva Pinolino
- nincs kategorizálva OSD Audio
- nincs kategorizálva WMD
- nincs kategorizálva Andover
- nincs kategorizálva Simpark
- nincs kategorizálva Beafon
- nincs kategorizálva Maruyama
- nincs kategorizálva 3B
- nincs kategorizálva FABER CASTELL
- nincs kategorizálva Ergotron
- nincs kategorizálva Stairville
- nincs kategorizálva Giordani
- nincs kategorizálva RME
- nincs kategorizálva Black Lion Audio
- nincs kategorizálva Cowon
- nincs kategorizálva Soundstream
- nincs kategorizálva Crayola
- nincs kategorizálva Xoro
- nincs kategorizálva Medel
- nincs kategorizálva REVITIVE
- nincs kategorizálva Maze
- nincs kategorizálva CTOUCH
- nincs kategorizálva Adastra
- nincs kategorizálva Meister Craft
- nincs kategorizálva Meade
- nincs kategorizálva Perkins
- nincs kategorizálva Sagemcom
- nincs kategorizálva Yeastar
- nincs kategorizálva Laserworld
- nincs kategorizálva Billow
- nincs kategorizálva Chuango
- nincs kategorizálva Kelty
- nincs kategorizálva West Elm
- nincs kategorizálva Block
- nincs kategorizálva Ozone
- nincs kategorizálva Klavis
- nincs kategorizálva Clearblue
- nincs kategorizálva Garden Lights
- nincs kategorizálva ETiger
- nincs kategorizálva Bison
- nincs kategorizálva Jabsco
- nincs kategorizálva Foxconn
- nincs kategorizálva Icy Dock
- nincs kategorizálva Wasco
- nincs kategorizálva Baby Brezza
- nincs kategorizálva Make Noise
- nincs kategorizálva Telstra
- nincs kategorizálva TeachLogic
- nincs kategorizálva ASSA ABLOY
- nincs kategorizálva Lumag
- nincs kategorizálva Charge Amps
- nincs kategorizálva Berker
- nincs kategorizálva Eufab
- nincs kategorizálva Crucial
- nincs kategorizálva Snom
- nincs kategorizálva RIDGID
- nincs kategorizálva Premier
- nincs kategorizálva Aeon Labs
- nincs kategorizálva Ibm
- nincs kategorizálva Unilux
- nincs kategorizálva Shokz
- nincs kategorizálva Citronic
- nincs kategorizálva TEF
- nincs kategorizálva Cosatto
- nincs kategorizálva Weasy
- nincs kategorizálva Aerotec
- nincs kategorizálva Atlas
- nincs kategorizálva Datacard
- nincs kategorizálva Nordea
- nincs kategorizálva Life Gear
- nincs kategorizálva ZYCOO
- nincs kategorizálva Macrom
- nincs kategorizálva Kontakt Chemie
- nincs kategorizálva Purell
- nincs kategorizálva Riccar
- nincs kategorizálva BabyHome
- nincs kategorizálva Contax
- nincs kategorizálva OpenVox
- nincs kategorizálva Atdec
- nincs kategorizálva Batavia
- nincs kategorizálva Klarfit
- nincs kategorizálva Gutfels
- nincs kategorizálva Bruynzeel
- nincs kategorizálva MSpa
- nincs kategorizálva View Quest
- nincs kategorizálva Drayton
- nincs kategorizálva Formuler
- nincs kategorizálva Sonnet
- nincs kategorizálva Oertli
- nincs kategorizálva UX
- nincs kategorizálva Moog
- nincs kategorizálva Nerf
- nincs kategorizálva KidKraft
- nincs kategorizálva Westfalia
- nincs kategorizálva Metrel
- nincs kategorizálva Solid
- nincs kategorizálva NUK
- nincs kategorizálva Morris
- nincs kategorizálva Ruger
- nincs kategorizálva Hubelino
- nincs kategorizálva Aputure
- nincs kategorizálva Gerni
- nincs kategorizálva Jupio
- nincs kategorizálva MedFolio
- nincs kategorizálva Baby Annabell
- nincs kategorizálva Blaser
- nincs kategorizálva Heatit
- nincs kategorizálva Endress
- nincs kategorizálva ProForm
- nincs kategorizálva UTEPO
- nincs kategorizálva Purpleline
- nincs kategorizálva Lindell Audio
- nincs kategorizálva Max Pro
- nincs kategorizálva Think Tank
- nincs kategorizálva Portech
- nincs kategorizálva Twelve South
- nincs kategorizálva Lec
- nincs kategorizálva Geomag
- nincs kategorizálva LTC
- nincs kategorizálva Koala
- nincs kategorizálva Drawmer
- nincs kategorizálva Audeze
- nincs kategorizálva Blue Sky
- nincs kategorizálva Valeo
- nincs kategorizálva Noxon
- nincs kategorizálva Woonexpress
- nincs kategorizálva IQAir
- nincs kategorizálva Sanus Systems
- nincs kategorizálva BabyDan
- nincs kategorizálva ColorKey
- nincs kategorizálva Tormatic
- nincs kategorizálva After Later Audio
- nincs kategorizálva Verbatim
- nincs kategorizálva 2hp
- nincs kategorizálva Energizer
- nincs kategorizálva IXS
- nincs kategorizálva Samlex
- nincs kategorizálva Navionics
- nincs kategorizálva AirTurn
- nincs kategorizálva Zalman
- nincs kategorizálva Zega
- nincs kategorizálva Leatherman
- nincs kategorizálva CreativeWorKs
- nincs kategorizálva Ultimate Support
- nincs kategorizálva Rösle
- nincs kategorizálva Prince
- nincs kategorizálva AXI
- nincs kategorizálva EMG
- nincs kategorizálva James
- nincs kategorizálva Bicker Elektronik
- nincs kategorizálva Iadea
- nincs kategorizálva Nimble
- nincs kategorizálva Reginox
- nincs kategorizálva BIOS Medical
- nincs kategorizálva Advantech
- nincs kategorizálva PSSO
- nincs kategorizálva Wise
- nincs kategorizálva SIG Sauer
- nincs kategorizálva Merkel
- nincs kategorizálva Patching Panda
- nincs kategorizálva Harley Benton
- nincs kategorizálva Crest Audio
- nincs kategorizálva Globe
- nincs kategorizálva Rossi
- nincs kategorizálva Hercules
- nincs kategorizálva Contour Design
- nincs kategorizálva Propellerhead
- nincs kategorizálva Nanuk
- nincs kategorizálva Digital Watchdog
- nincs kategorizálva Sonifex
- nincs kategorizálva Riviera And Bar
- nincs kategorizálva Kreiling
- nincs kategorizálva Xantech
- nincs kategorizálva Marker
- nincs kategorizálva Kohler
- nincs kategorizálva Safco
- nincs kategorizálva Xunzel
- nincs kategorizálva Oklahoma Sound
- nincs kategorizálva Thames & Kosmos
- nincs kategorizálva Betso
- nincs kategorizálva Fortia
- nincs kategorizálva Moen
- nincs kategorizálva Babysense
- nincs kategorizálva Namco Bandai Games
- nincs kategorizálva Sealy
- nincs kategorizálva Ferguson
- nincs kategorizálva Wet Sounds
- nincs kategorizálva CRU
- nincs kategorizálva Avantone Pro
- nincs kategorizálva Umarex
- nincs kategorizálva Televés
- nincs kategorizálva AbleNet
- nincs kategorizálva Exalux
- nincs kategorizálva IBasso
- nincs kategorizálva Sole Fitness
- nincs kategorizálva Leap Frog
- nincs kategorizálva Sightmark
- nincs kategorizálva Eissound
- nincs kategorizálva Ganz
- nincs kategorizálva Manley
- nincs kategorizálva Micro Matic
- nincs kategorizálva Thermomate
- nincs kategorizálva Steiner
- nincs kategorizálva Acard
- nincs kategorizálva Burigotto
- nincs kategorizálva Redmond
- nincs kategorizálva Sencys
- nincs kategorizálva Norton Clipper
- nincs kategorizálva Extron
- nincs kategorizálva Avocent
- nincs kategorizálva Geze
- nincs kategorizálva RTS
- nincs kategorizálva Ontech
- nincs kategorizálva HyperJuice
- nincs kategorizálva Koss
- nincs kategorizálva Swingline
- nincs kategorizálva Kwikset
- nincs kategorizálva Infomir
- nincs kategorizálva RaySafe
- nincs kategorizálva Di4
- nincs kategorizálva Hohner
- nincs kategorizálva Dahle
- nincs kategorizálva Sanli
- nincs kategorizálva Shelly
- nincs kategorizálva Husky
- nincs kategorizálva Philos
- nincs kategorizálva Siemon
- nincs kategorizálva Block & Block
- nincs kategorizálva Brondell
- nincs kategorizálva NutriBullet
- nincs kategorizálva Four Hands
- nincs kategorizálva Oben
- nincs kategorizálva ASA
- nincs kategorizálva Vantec
- nincs kategorizálva Thronmax
- nincs kategorizálva Axkid
- nincs kategorizálva Botex
- nincs kategorizálva Intellinet
- nincs kategorizálva Maxsa
- nincs kategorizálva Tripp
- nincs kategorizálva TRIUS
- nincs kategorizálva Ankarsrum
- nincs kategorizálva MTD
- nincs kategorizálva Etymotic
- nincs kategorizálva Fine Dine
- nincs kategorizálva ClearOne
- nincs kategorizálva Heidemann
- nincs kategorizálva OneTouch
- nincs kategorizálva Superrollo
- nincs kategorizálva Goldtouch
- nincs kategorizálva Gamewright
- nincs kategorizálva Kerbl
- nincs kategorizálva Braun Phototechnik
- nincs kategorizálva Black Decker
- nincs kategorizálva Muller
- nincs kategorizálva SXT
- nincs kategorizálva Essenza
- nincs kategorizálva Seecode
- nincs kategorizálva Rugged Geek
- nincs kategorizálva Nubert
- nincs kategorizálva Dave Smith
- nincs kategorizálva Skymaster
- nincs kategorizálva Dorr
- nincs kategorizálva Gardol
- nincs kategorizálva Helix
- nincs kategorizálva TFA Dostmann
- nincs kategorizálva Werma
- nincs kategorizálva Durable
- nincs kategorizálva Zenza Bronica
- nincs kategorizálva Spypoint
- nincs kategorizálva Suprema
- nincs kategorizálva Ziehl
- nincs kategorizálva VAIS
- nincs kategorizálva Perma
- nincs kategorizálva Scandes
- nincs kategorizálva Enovate
- nincs kategorizálva Lofrans
- nincs kategorizálva Winegard
- nincs kategorizálva Pigtronix
- nincs kategorizálva ProTeam
- nincs kategorizálva Wagner SprayTech
- nincs kategorizálva Libec
- nincs kategorizálva Pardini
- nincs kategorizálva KWC
- nincs kategorizálva Soul
- nincs kategorizálva Laney
- nincs kategorizálva Compex
- nincs kategorizálva Theragun
- nincs kategorizálva Weil
- nincs kategorizálva Plantiflor
- nincs kategorizálva LAS
- nincs kategorizálva Rosseto
- nincs kategorizálva Redrock Micro
- nincs kategorizálva Motu
- nincs kategorizálva Kata
- nincs kategorizálva Minix
- nincs kategorizálva Lazer
- nincs kategorizálva EarthQuaker Devices
- nincs kategorizálva The Grainfather
- nincs kategorizálva Kessler
- nincs kategorizálva Emga
- nincs kategorizálva Devialet
- nincs kategorizálva Briggs & Stratton
- nincs kategorizálva USAopoly
- nincs kategorizálva Gami
- nincs kategorizálva Igloohome
- nincs kategorizálva Kenko
- nincs kategorizálva Zennio
- nincs kategorizálva Vixen
- nincs kategorizálva B-tech
- nincs kategorizálva Praktica
- nincs kategorizálva Elinchrom
- nincs kategorizálva Boori
- nincs kategorizálva CamRanger
- nincs kategorizálva ETON
- nincs kategorizálva Hasselblad
- nincs kategorizálva Madrix
- nincs kategorizálva Q Acoustics
- nincs kategorizálva Spacedec
- nincs kategorizálva Auray
- nincs kategorizálva Bontempi
- nincs kategorizálva Furman
- nincs kategorizálva Summer Infant
- nincs kategorizálva Cooper & Quint
- nincs kategorizálva Deltex
- nincs kategorizálva Adax
- nincs kategorizálva Xplora
- nincs kategorizálva Buzz Rack
- nincs kategorizálva Cruz
- nincs kategorizálva Eonon
- nincs kategorizálva SMC
- nincs kategorizálva Ibico
- nincs kategorizálva OXO Good Grips
- nincs kategorizálva Exit Toys
- nincs kategorizálva Triton
- nincs kategorizálva Profizelt24
- nincs kategorizálva Helios Preisser
- nincs kategorizálva YSI
- nincs kategorizálva Yeyian
- nincs kategorizálva Paulmann
- nincs kategorizálva Nitek
- nincs kategorizálva Snoes
- nincs kategorizálva Alpatronix
- nincs kategorizálva Labelmate
- nincs kategorizálva Martin Audio
- nincs kategorizálva Schertler
- nincs kategorizálva Teradek
- nincs kategorizálva Sissel
- nincs kategorizálva Kunath
- nincs kategorizálva Penclic
- nincs kategorizálva Escort
- nincs kategorizálva ViewCast
- nincs kategorizálva Crown
- nincs kategorizálva Wolfcraft
- nincs kategorizálva Tennsco
- nincs kategorizálva FireKing
- nincs kategorizálva RAM Mounts
- nincs kategorizálva Novus
- nincs kategorizálva Arebos
- nincs kategorizálva Kreg
- nincs kategorizálva Bentley
- nincs kategorizálva Morningstar
- nincs kategorizálva DMax
- nincs kategorizálva Backyard Discovery
- nincs kategorizálva Minuteman
- nincs kategorizálva Ortofon
- nincs kategorizálva RéVive
- nincs kategorizálva Star Micronics
- nincs kategorizálva Tamron
- nincs kategorizálva Woodland Scenics
- nincs kategorizálva Chapin
- nincs kategorizálva J. Rockett Audio Designs
- nincs kategorizálva Satisfyer
- nincs kategorizálva Hämmerli
- nincs kategorizálva Verto
- nincs kategorizálva Soma
- nincs kategorizálva SRS
- nincs kategorizálva Point 65
- nincs kategorizálva ReTrak
- nincs kategorizálva Avantree
- nincs kategorizálva Akuvox
- nincs kategorizálva LYYT
- nincs kategorizálva Old Blood Noise
- nincs kategorizálva Vulcan
- nincs kategorizálva CradlePoint
- nincs kategorizálva Catalyst
- nincs kategorizálva Antelope Audio
- nincs kategorizálva Brinno
- nincs kategorizálva Venom
- nincs kategorizálva CE Labs
- nincs kategorizálva Legrand
- nincs kategorizálva Z CAM
- nincs kategorizálva Digium
- nincs kategorizálva Giardino
- nincs kategorizálva Mulex
- nincs kategorizálva Socomec
- nincs kategorizálva System Sensor
- nincs kategorizálva San Jamar
- nincs kategorizálva Fiskars
- nincs kategorizálva IPort
- nincs kategorizálva X-Rite
- nincs kategorizálva Wetelux
- nincs kategorizálva Talkaphone
- nincs kategorizálva Merax
- nincs kategorizálva GermGuardian
- nincs kategorizálva R-Go Tools
- nincs kategorizálva Urbanista
- nincs kategorizálva SLV
- nincs kategorizálva Sagitter
- nincs kategorizálva Rainbow
- nincs kategorizálva Riello
- nincs kategorizálva Gagato
- nincs kategorizálva Traeger
- nincs kategorizálva General
- nincs kategorizálva Ooni
- nincs kategorizálva ECTIVE
- nincs kategorizálva Gymform
- nincs kategorizálva Tzumi
- nincs kategorizálva BERTSCHAT
- nincs kategorizálva Schumacher
- nincs kategorizálva Michael Todd Beauty
- nincs kategorizálva Cygnett
- nincs kategorizálva Germania
- nincs kategorizálva Victorio
- nincs kategorizálva Platinum
- nincs kategorizálva Trimble
- nincs kategorizálva Playtive Junior
- nincs kategorizálva Parklands
- nincs kategorizálva Avid
- nincs kategorizálva Vipack
- nincs kategorizálva Helios
- nincs kategorizálva EKO
- nincs kategorizálva BIG
- nincs kategorizálva POGS
- nincs kategorizálva Graflex
- nincs kategorizálva Coolaroo
- nincs kategorizálva Wurth
- nincs kategorizálva Mebus
- nincs kategorizálva Gioteck
- nincs kategorizálva Kenton
- nincs kategorizálva Cypress
- nincs kategorizálva Foliatec
- nincs kategorizálva Mauser
- nincs kategorizálva Silhouette
- nincs kategorizálva South Shore
- nincs kategorizálva Discovery
- nincs kategorizálva T4E
- nincs kategorizálva Speck
- nincs kategorizálva Generation
- nincs kategorizálva Iseki
- nincs kategorizálva MOZA
- nincs kategorizálva Ecler
- nincs kategorizálva Turbosound
- nincs kategorizálva Phase One
- nincs kategorizálva Little Giant
- nincs kategorizálva Röhm
- nincs kategorizálva Ulanzi
- nincs kategorizálva Anova
- nincs kategorizálva Viscount
- nincs kategorizálva Khind
- nincs kategorizálva DAB
- nincs kategorizálva Anex
- nincs kategorizálva LERAN
- nincs kategorizálva Majella
- nincs kategorizálva GMB Audio
- nincs kategorizálva Ashdown Engineering
- nincs kategorizálva Century
- nincs kategorizálva Unger
- nincs kategorizálva Inverto
- nincs kategorizálva Special-T
- nincs kategorizálva Ygnis
- nincs kategorizálva Esotec
- nincs kategorizálva True & Tidy
- nincs kategorizálva Petkit
- nincs kategorizálva Icon
- nincs kategorizálva Fuzzix
- nincs kategorizálva Kitchen Brains
- nincs kategorizálva Best
- nincs kategorizálva NetAlly
- nincs kategorizálva Triax
- nincs kategorizálva Peltor
- nincs kategorizálva JAR Systems
- nincs kategorizálva Moleskine
- nincs kategorizálva Bytecc
- nincs kategorizálva Strex
- nincs kategorizálva Xlyne
- nincs kategorizálva Premier Mounts
- nincs kategorizálva One Stop Systems
- nincs kategorizálva Cool Maker
- nincs kategorizálva Neo
- nincs kategorizálva EVOline
- nincs kategorizálva Mtx Audio
- nincs kategorizálva Ursus Trotter
- nincs kategorizálva DoughXpress
- nincs kategorizálva Aquatic AV
- nincs kategorizálva Parasound
- nincs kategorizálva MSR
- nincs kategorizálva Cabstone
- nincs kategorizálva SPT
- nincs kategorizálva DB Technologies
- nincs kategorizálva T.I.P.
- nincs kategorizálva Promate
- nincs kategorizálva Berger & Schröter
- nincs kategorizálva Tru Components
- nincs kategorizálva Step2
- nincs kategorizálva Dension
- nincs kategorizálva Crystal Quest
- nincs kategorizálva Pit Boss
- nincs kategorizálva Needit
- nincs kategorizálva MiPow
- nincs kategorizálva GoldenEar Technology
- nincs kategorizálva Colt
- nincs kategorizálva Elite Screens
- nincs kategorizálva Quadro
- nincs kategorizálva Ultron
- nincs kategorizálva Choice
- nincs kategorizálva Roswell
- nincs kategorizálva King Craft
- nincs kategorizálva FOX ESS
- nincs kategorizálva Airman
- nincs kategorizálva Cascade Audio Engineering
- nincs kategorizálva B-Speech
- nincs kategorizálva Vanish
- nincs kategorizálva Nostalgia
- nincs kategorizálva Grosfillex
- nincs kategorizálva Beemoo
- nincs kategorizálva Platinet
- nincs kategorizálva Santos
- nincs kategorizálva Entes
- nincs kategorizálva Evoc
- nincs kategorizálva Versare
- nincs kategorizálva Enphase
- nincs kategorizálva SpeakerCraft
- nincs kategorizálva Epcom
- nincs kategorizálva ZeeVee
- nincs kategorizálva Siku
- nincs kategorizálva Viatek
- nincs kategorizálva Simplicity
- nincs kategorizálva Doomoo
- nincs kategorizálva MBZ
- nincs kategorizálva Davey
- nincs kategorizálva Mettler
- nincs kategorizálva Metalux
- nincs kategorizálva Heitech
- nincs kategorizálva Potenza
- nincs kategorizálva LOQED
- nincs kategorizálva Hatco
- nincs kategorizálva KONFTEL
- nincs kategorizálva Canicom
- nincs kategorizálva Mitsai
- nincs kategorizálva Selfsat
- nincs kategorizálva Leef
- nincs kategorizálva Tusa
- nincs kategorizálva Hovicon
- nincs kategorizálva American BioTech Supply
- nincs kategorizálva Noris
- nincs kategorizálva KS Tools
- nincs kategorizálva Koliber
- nincs kategorizálva Schmidt & Bender
- nincs kategorizálva Mesa Boogie
- nincs kategorizálva Improv
- nincs kategorizálva LandRoller
- nincs kategorizálva Wegman
- nincs kategorizálva Lockncharge
- nincs kategorizálva Merlin
- nincs kategorizálva Standard Horizon
- nincs kategorizálva Goal Zero
- nincs kategorizálva HealthPostures
- nincs kategorizálva Dreadbox
- nincs kategorizálva Joranalogue
- nincs kategorizálva CYP
- nincs kategorizálva Heaven Fresh
- nincs kategorizálva Lutec
- nincs kategorizálva Champion Sports
- nincs kategorizálva Molotow
- nincs kategorizálva Herlag
- nincs kategorizálva Dux
- nincs kategorizálva FALLER
- nincs kategorizálva Miditech
- nincs kategorizálva SE Electronics
- nincs kategorizálva TTM
- nincs kategorizálva Paw Patrol
- nincs kategorizálva LELO
- nincs kategorizálva Mermade
- nincs kategorizálva MXR
- nincs kategorizálva SKLZ
- nincs kategorizálva Herma
- nincs kategorizálva BWT
- nincs kategorizálva Syrp
- nincs kategorizálva Ugolini
- nincs kategorizálva Cosina
- nincs kategorizálva Heckler & Koch
- nincs kategorizálva Whistler
- nincs kategorizálva Twisper
- nincs kategorizálva Manitowoc
- nincs kategorizálva Hushmat
- nincs kategorizálva Xigmatek
- nincs kategorizálva Tema
- nincs kategorizálva ALM
- nincs kategorizálva Topaz
- nincs kategorizálva Toddy
- nincs kategorizálva Aicon
- nincs kategorizálva Astell&Kern
- nincs kategorizálva Doepfer
- nincs kategorizálva Fun Generation
- nincs kategorizálva Karma
- nincs kategorizálva TV One
- nincs kategorizálva Berkel
- nincs kategorizálva Hugo Muller
- nincs kategorizálva Vinci
- nincs kategorizálva Jordan
- nincs kategorizálva Duromax
- nincs kategorizálva DataComm
- nincs kategorizálva Powercube
- nincs kategorizálva Kasp
- nincs kategorizálva Dimavery
- nincs kategorizálva Hanwha
- nincs kategorizálva WestBend
- nincs kategorizálva Mr Coffee
- nincs kategorizálva Sherlock
- nincs kategorizálva SEA-PRO
- nincs kategorizálva Omiindustriies
- nincs kategorizálva Weltevree
- nincs kategorizálva Phoenix Contact
- nincs kategorizálva AMS Neve
- nincs kategorizálva LVSUN
- nincs kategorizálva Aston Microphones
- nincs kategorizálva Netsys
- nincs kategorizálva Alfi
- nincs kategorizálva Polarlite
- nincs kategorizálva Companion
- nincs kategorizálva Mr. Beams
- nincs kategorizálva Morphor
- nincs kategorizálva Lapp
- nincs kategorizálva XO
- nincs kategorizálva PcDuino
- nincs kategorizálva LECO
- nincs kategorizálva Maretron
- nincs kategorizálva Hortus
- nincs kategorizálva Razorri
- nincs kategorizálva Fetch
- nincs kategorizálva Zoetis
- nincs kategorizálva Prem-i-air
- nincs kategorizálva NWS
- nincs kategorizálva GAM
- nincs kategorizálva Scale Computing
- nincs kategorizálva Naturn Living
- nincs kategorizálva Aeotec
- nincs kategorizálva Catlink
- nincs kategorizálva FitterFirst
- nincs kategorizálva Raveland
- nincs kategorizálva Mr. Heater
- nincs kategorizálva Welltech
- nincs kategorizálva Trumeter
- nincs kategorizálva Seidio
- nincs kategorizálva Sincreative
- nincs kategorizálva JDC
- nincs kategorizálva Hidrate
- nincs kategorizálva Sonicware
- nincs kategorizálva Nexibo
- nincs kategorizálva Jolin
- nincs kategorizálva MoTip
- nincs kategorizálva Stenda
- nincs kategorizálva Pro-Lift
- nincs kategorizálva HIOAZO
- nincs kategorizálva Malstrom
- nincs kategorizálva Laserluchs
- nincs kategorizálva Powersoft
- nincs kategorizálva Casetastic
- nincs kategorizálva UClear
- nincs kategorizálva BikeLogger
- nincs kategorizálva Tor Rey
- nincs kategorizálva Momo Design
- nincs kategorizálva Esdec
- nincs kategorizálva Ruark Audio
- nincs kategorizálva AJH Synth
- nincs kategorizálva LifeStraw
- nincs kategorizálva Magnavox
- nincs kategorizálva Toolit
- nincs kategorizálva Egnater
- nincs kategorizálva DutchOne
- nincs kategorizálva Feitian
- nincs kategorizálva Ergie
- nincs kategorizálva Reltech
- nincs kategorizálva Armcross
- nincs kategorizálva Focus Electrics
- nincs kategorizálva Huntleigh
- nincs kategorizálva Beeletix
- nincs kategorizálva Gehmann
- nincs kategorizálva Batronix
- nincs kategorizálva Franzis
- nincs kategorizálva Gridbyt
- nincs kategorizálva TDK-Lambda
- nincs kategorizálva LONQ
- nincs kategorizálva Em-Trak
- nincs kategorizálva Wonky Monkey
- nincs kategorizálva Dresden Elektronik
- nincs kategorizálva Atmel
- nincs kategorizálva Flavour Blaster
- nincs kategorizálva Esoteric
- nincs kategorizálva SmartAVI
- nincs kategorizálva EPH Elektronik
- nincs kategorizálva Markbass
- nincs kategorizálva IMG Stage Line
- nincs kategorizálva IMAC
- nincs kategorizálva Metz Connect
- nincs kategorizálva MGL Avionics
- nincs kategorizálva Eikon
- nincs kategorizálva Casablanca
- nincs kategorizálva Nemco
- nincs kategorizálva Wireless Solution
- nincs kategorizálva Beverage-Air
- nincs kategorizálva Sparco
- nincs kategorizálva Barber Tech
- nincs kategorizálva Estella
- nincs kategorizálva EarFun
- nincs kategorizálva Oehlbach
- nincs kategorizálva Minkels
- nincs kategorizálva Kipor
- nincs kategorizálva Lenmar
- nincs kategorizálva HMS Premium
- nincs kategorizálva Arduino
- nincs kategorizálva Ave Six
- nincs kategorizálva Bestar
- nincs kategorizálva Pelco
- nincs kategorizálva Gardigo
- nincs kategorizálva Highpoint
- nincs kategorizálva Puls Dimension
- nincs kategorizálva Studiologic
- nincs kategorizálva Fischer Amps
- nincs kategorizálva CHINT
- nincs kategorizálva Sirus
- nincs kategorizálva Digitech
- nincs kategorizálva Leviton
- nincs kategorizálva Gretsch
- nincs kategorizálva Pentacon
- nincs kategorizálva Winia
- nincs kategorizálva Bolsey
- nincs kategorizálva Louis Tellier
- nincs kategorizálva EtiamPro
- nincs kategorizálva Simeo
- nincs kategorizálva Baracuda
- nincs kategorizálva Kstar
- nincs kategorizálva Air Guard
- nincs kategorizálva MediaMatrix
- nincs kategorizálva ESX
- nincs kategorizálva Tuur
- nincs kategorizálva ONE Smart Control
- nincs kategorizálva Edelkrone
- nincs kategorizálva OBSBOT
- nincs kategorizálva InSinkErator
- nincs kategorizálva Omnires
- nincs kategorizálva Elite Force
- nincs kategorizálva JK Audio
- nincs kategorizálva DEHN
- nincs kategorizálva Lifan
- nincs kategorizálva Jomox
- nincs kategorizálva Pentatech
- nincs kategorizálva Burley
- nincs kategorizálva Lexicon
- nincs kategorizálva Icarus Blue
- nincs kategorizálva Command
- nincs kategorizálva IRIS
- nincs kategorizálva Neno
- nincs kategorizálva Starburst
- nincs kategorizálva AVPro Edge
- nincs kategorizálva Fluance
- nincs kategorizálva PCE Instruments
- nincs kategorizálva Garden Place
- nincs kategorizálva Moldex
- nincs kategorizálva MaximaVida
- nincs kategorizálva Firefriend
- nincs kategorizálva LightZone
- nincs kategorizálva Robinhood
- nincs kategorizálva Bliss Outdoors
- nincs kategorizálva Fontiso
- nincs kategorizálva Varytec
- nincs kategorizálva Altra
- nincs kategorizálva Omnilux
- nincs kategorizálva Socket Mobile
- nincs kategorizálva Quartet
- nincs kategorizálva Shadow
- nincs kategorizálva IP-COM
- nincs kategorizálva Calligaris .com
- nincs kategorizálva Comtek
- nincs kategorizálva Fishman
- nincs kategorizálva Tams Elektronik
- nincs kategorizálva Digital Juice
- nincs kategorizálva Eschenbach
- nincs kategorizálva ASM
- nincs kategorizálva Bretford
- nincs kategorizálva Ltech
- nincs kategorizálva Kiev
- nincs kategorizálva RetroSound
- nincs kategorizálva Caroline
- nincs kategorizálva Zomo
- nincs kategorizálva VAIS Technology
- nincs kategorizálva Synco
- nincs kategorizálva Buchla & TipTop Audio
- nincs kategorizálva Pyramid
- nincs kategorizálva Maico
- nincs kategorizálva On-Q
- nincs kategorizálva SetonixSynth
- nincs kategorizálva Horex
- nincs kategorizálva Inno-Hit
- nincs kategorizálva Sime
- nincs kategorizálva AvaValley
- nincs kategorizálva INTIMINA
- nincs kategorizálva Monzana
- nincs kategorizálva FCC BBQ
- nincs kategorizálva Auto XS
- nincs kategorizálva Toomax
- nincs kategorizálva Aqua Marina
- nincs kategorizálva Hameg
- nincs kategorizálva Greemotion
- nincs kategorizálva Winter Modular
- nincs kategorizálva Salewa
- nincs kategorizálva FED
- nincs kategorizálva Synamodec
- nincs kategorizálva Grotime
- nincs kategorizálva Pico Macom
- nincs kategorizálva RadonTec
- nincs kategorizálva Katrin
- nincs kategorizálva Kendau
- nincs kategorizálva Kisag
- nincs kategorizálva NUX
- nincs kategorizálva Coxreels
- nincs kategorizálva Nous
- nincs kategorizálva Overade
- nincs kategorizálva Liemke
- nincs kategorizálva Copco
- nincs kategorizálva Vanson
- nincs kategorizálva Canyon
- nincs kategorizálva Carcomm
- nincs kategorizálva Style Me Up
- nincs kategorizálva Swedish Posture
- nincs kategorizálva Melnor
- nincs kategorizálva CDVI
- nincs kategorizálva Excalibur
- nincs kategorizálva Holman
- nincs kategorizálva HomePilot
- nincs kategorizálva Leaptel
- nincs kategorizálva Lifenaxx
- nincs kategorizálva Powertec
- nincs kategorizálva Waterbird
- nincs kategorizálva Dreambaby
- nincs kategorizálva AOpen
- nincs kategorizálva Angler
- nincs kategorizálva GP
- nincs kategorizálva Akrobat
- nincs kategorizálva Casaria
- nincs kategorizálva Selleys
- nincs kategorizálva WindFall
- nincs kategorizálva Ameristep
- nincs kategorizálva Rikon
- nincs kategorizálva KM-fit
- nincs kategorizálva X Rocker
- nincs kategorizálva Mircom
- nincs kategorizálva ESUN
- nincs kategorizálva Durex
- nincs kategorizálva AeroCool
- nincs kategorizálva Vantage Point
- nincs kategorizálva Jokari
- nincs kategorizálva BeeSecure
- nincs kategorizálva Unicol
- nincs kategorizálva Fisher Paykel
- nincs kategorizálva Lasita Maja
- nincs kategorizálva Meccano
- nincs kategorizálva Parallels
- nincs kategorizálva Oatey
- nincs kategorizálva QUIO
- nincs kategorizálva Fisher
- nincs kategorizálva Gretsch Guitars
- nincs kategorizálva Banoch
- nincs kategorizálva XP-PEN
- nincs kategorizálva Atmotube
- nincs kategorizálva Sun Pumps
- nincs kategorizálva Electrify
- nincs kategorizálva Leatt
- nincs kategorizálva Bleep Labs
- nincs kategorizálva FontaFit
- nincs kategorizálva Gossmann
- nincs kategorizálva Comatec
- nincs kategorizálva Jonard Tools
- nincs kategorizálva Atech Flash Technology
- nincs kategorizálva AutoParkTime
- nincs kategorizálva Hudora
- nincs kategorizálva Facal
- nincs kategorizálva Planet Audio
- nincs kategorizálva Datacolor
- nincs kategorizálva Silicon Power
- nincs kategorizálva Sabrent
- nincs kategorizálva JAXY
- nincs kategorizálva WARN
- nincs kategorizálva Aarke
- nincs kategorizálva TikkTokk
- nincs kategorizálva Roco
- nincs kategorizálva Flexson
- nincs kategorizálva Camec
- nincs kategorizálva Wibrain
- nincs kategorizálva Rolly Toys
- nincs kategorizálva Level Mount
- nincs kategorizálva Teenage Engineering
- nincs kategorizálva Elipson
- nincs kategorizálva STANDIVARIUS
- nincs kategorizálva CommScope
- nincs kategorizálva Videotec
- nincs kategorizálva Orange
- nincs kategorizálva Extralife Instruments
- nincs kategorizálva Genki Instruments
- nincs kategorizálva Industrial Music Electronics
- nincs kategorizálva Mauser Sitzkultur
- nincs kategorizálva Accezz
- nincs kategorizálva A4 Tech
- nincs kategorizálva Full Boar
- nincs kategorizálva Zedar
- nincs kategorizálva Yli Electronic
- nincs kategorizálva Dals
- nincs kategorizálva Bulman
- nincs kategorizálva TOOLMATE
- nincs kategorizálva SleepPro
- nincs kategorizálva Muama
- nincs kategorizálva Lepu Medical
- nincs kategorizálva Michigan
- nincs kategorizálva Beringer
- nincs kategorizálva Waterdrop
- nincs kategorizálva Revamp
- nincs kategorizálva Phonic
- nincs kategorizálva ZCover
- nincs kategorizálva Vasagle
- nincs kategorizálva Aquatica
- nincs kategorizálva Girmi
- nincs kategorizálva Goaliath
- nincs kategorizálva 909 Outdoor
- nincs kategorizálva Viomi
- nincs kategorizálva Grimm Audio
- nincs kategorizálva Better Life
- nincs kategorizálva Dayclocks
- nincs kategorizálva Testec
- nincs kategorizálva Phidgets
- nincs kategorizálva TK Audio
- nincs kategorizálva Hawk-Woods
- nincs kategorizálva Novo
- nincs kategorizálva Commercial Chef
- nincs kategorizálva Novis
- nincs kategorizálva Dexibell
- nincs kategorizálva IsoAcoustics
- nincs kategorizálva Memphis
- nincs kategorizálva Engel
- nincs kategorizálva Clifford
- nincs kategorizálva Cambo
- nincs kategorizálva Hedbox
- nincs kategorizálva Campart
- nincs kategorizálva Lansinoh
- nincs kategorizálva Adviti
- nincs kategorizálva Maclean
- nincs kategorizálva 9.solutions
- nincs kategorizálva Hotone
- nincs kategorizálva WEN
- nincs kategorizálva Trace Elliot
- nincs kategorizálva Lockwood
- nincs kategorizálva Nexera
- nincs kategorizálva Goodway
- nincs kategorizálva BlueDri
- nincs kategorizálva Seenergy
- nincs kategorizálva Meinl
- nincs kategorizálva Analogis
- nincs kategorizálva BBQ Premium
- nincs kategorizálva Stäubli
- nincs kategorizálva RAB
- nincs kategorizálva Schabus
- nincs kategorizálva Eoslift
- nincs kategorizálva Bron-Coucke
- nincs kategorizálva Steelton
- nincs kategorizálva FeinTech
- nincs kategorizálva BioChef
- nincs kategorizálva Masterbuilt
- nincs kategorizálva Koolatron
- nincs kategorizálva Euro Cuisine
- nincs kategorizálva GFM
- nincs kategorizálva Tot Tutors
- nincs kategorizálva X4 Life
- nincs kategorizálva Tonar
- nincs kategorizálva Peterson
- nincs kategorizálva CFH
- nincs kategorizálva BOB Gear
- nincs kategorizálva Emeril Everyday
- nincs kategorizálva Könner & Söhnen
- nincs kategorizálva Rockboard
- nincs kategorizálva Goodis
- nincs kategorizálva Nivian
- nincs kategorizálva L.R.Baggs
- nincs kategorizálva Millennia
- nincs kategorizálva Vermona Modular
- nincs kategorizálva Adventure Kings
- nincs kategorizálva Drive Medical
- nincs kategorizálva Hitron
- nincs kategorizálva Bliss Hammocks
- nincs kategorizálva Singular Sound
- nincs kategorizálva Maneco Labs
- nincs kategorizálva BISWIND
- nincs kategorizálva ABE Arnhold
- nincs kategorizálva Mermade Hair
- nincs kategorizálva VCM
- nincs kategorizálva BodyCraft
- nincs kategorizálva Auer Signal
- nincs kategorizálva BrightSign
- nincs kategorizálva Mamas & Papas
- nincs kategorizálva Manduca
- nincs kategorizálva HELGI
- nincs kategorizálva Forge Adour
- nincs kategorizálva Eliminator Lighting
- nincs kategorizálva Darkglass
- nincs kategorizálva Blow
- nincs kategorizálva Paasche
- nincs kategorizálva Vistus
- nincs kategorizálva GMW
- nincs kategorizálva AER
- nincs kategorizálva Dynavox
- nincs kategorizálva Columbus
- nincs kategorizálva IWH
- nincs kategorizálva UGo
- nincs kategorizálva Code Mercenaries
- nincs kategorizálva Diamex
- nincs kategorizálva Sunset
- nincs kategorizálva Avital
- nincs kategorizálva Ondis24
- nincs kategorizálva D'Addario
- nincs kategorizálva BBE
- nincs kategorizálva Warwick
- nincs kategorizálva MyAVR
- nincs kategorizálva EBS
- nincs kategorizálva WEICON
- nincs kategorizálva Rotronic
- nincs kategorizálva Edsyn
- nincs kategorizálva Urban Glide
- nincs kategorizálva EISL
- nincs kategorizálva RCS
- nincs kategorizálva Nicai Systems
- nincs kategorizálva IDENTsmart
- nincs kategorizálva Sharper Image
- nincs kategorizálva Altrad
- nincs kategorizálva Revier Manager
- nincs kategorizálva Homak
- nincs kategorizálva Tycon Systems
- nincs kategorizálva Selve
- nincs kategorizálva Lumel
- nincs kategorizálva Paingone
- nincs kategorizálva Howard Leight
- nincs kategorizálva Plugwise
- nincs kategorizálva Martens
- nincs kategorizálva Desview
- nincs kategorizálva ActiveJet
- nincs kategorizálva Global Water
- nincs kategorizálva Allsee
- nincs kategorizálva Softing
- nincs kategorizálva Pulse ShowerSpas
- nincs kategorizálva Alogic
- nincs kategorizálva GFB
- nincs kategorizálva Sonicsmith
- nincs kategorizálva Toraiz
- nincs kategorizálva Ergodyne
- nincs kategorizálva Maturmeat
- nincs kategorizálva D-Jix
- nincs kategorizálva Orbsmart
- nincs kategorizálva Eowave
- nincs kategorizálva Imperia
- nincs kategorizálva Nature2
- nincs kategorizálva Baby Trend
- nincs kategorizálva AMERRY
- nincs kategorizálva Walther
- nincs kategorizálva ShelterLogic
- nincs kategorizálva Varad
- nincs kategorizálva Dr. Browns
- nincs kategorizálva KMA Machines
- nincs kategorizálva Klark Teknik
- nincs kategorizálva Elcom
- nincs kategorizálva Source Audio
- nincs kategorizálva AtomoSynth
- nincs kategorizálva Innr
- nincs kategorizálva Benidub
- nincs kategorizálva Protector
- nincs kategorizálva Winston
- nincs kategorizálva Solidsteel
- nincs kategorizálva Dracast
- nincs kategorizálva Dream
- nincs kategorizálva Malouf
- nincs kategorizálva Roba
- nincs kategorizálva Ravelli
- nincs kategorizálva Piet Boon
- nincs kategorizálva PureTools
- nincs kategorizálva JML
- nincs kategorizálva Reber
- nincs kategorizálva SiriusXM
- nincs kategorizálva Earthwise
- nincs kategorizálva DoubleSight
- nincs kategorizálva Raya
- nincs kategorizálva Artex
- nincs kategorizálva Bobrick
- nincs kategorizálva Verbos Electronics
- nincs kategorizálva Ark
- nincs kategorizálva DLO
- nincs kategorizálva ENS
- nincs kategorizálva Listen
- nincs kategorizálva Oscium
- nincs kategorizálva Benchmark USA
- nincs kategorizálva Python
- nincs kategorizálva Littelfuse
- nincs kategorizálva Game Factor
- nincs kategorizálva NComputing
- nincs kategorizálva Mode Machines
- nincs kategorizálva Legends
- nincs kategorizálva AS Synthesizers
- nincs kategorizálva Itechworld
- nincs kategorizálva Nexcom
- nincs kategorizálva SatKing
- nincs kategorizálva Fulltone
- nincs kategorizálva Advantix
- nincs kategorizálva Wampler
- nincs kategorizálva VAEMI
- nincs kategorizálva Aguilar
- nincs kategorizálva Narva
- nincs kategorizálva DOK
- nincs kategorizálva OzCharge
- nincs kategorizálva MIYO
- nincs kategorizálva Cioks
- nincs kategorizálva Neopower
- nincs kategorizálva AvMap
- nincs kategorizálva Arlec
- nincs kategorizálva Sanwa
- nincs kategorizálva REDARC
- nincs kategorizálva Guardian
- nincs kategorizálva Radio Flyer
- nincs kategorizálva Gaslock
- nincs kategorizálva Gaffgun
- nincs kategorizálva AquaMAX
- nincs kategorizálva DigitSole
- nincs kategorizálva Portsmith
- nincs kategorizálva Rome
- nincs kategorizálva DW
- nincs kategorizálva BEA
- nincs kategorizálva Disty
- nincs kategorizálva OXI Instruments
- nincs kategorizálva AvaTime
- nincs kategorizálva Xhose
- nincs kategorizálva MYVU
- nincs kategorizálva Kopykake
- nincs kategorizálva Konstant Lab
- nincs kategorizálva Turbo Scrub
- nincs kategorizálva Tenderfoot Electronics
- nincs kategorizálva Kask
- nincs kategorizálva Callpod
- nincs kategorizálva Dorman
- nincs kategorizálva 2box
- nincs kategorizálva Enlight
- nincs kategorizálva Franken
- nincs kategorizálva RUBI
- nincs kategorizálva Europa Leisure
- nincs kategorizálva GAMO
- nincs kategorizálva Musser
- nincs kategorizálva Edge Products
- nincs kategorizálva IClever
- nincs kategorizálva HN-Power
- nincs kategorizálva BIONIK
- nincs kategorizálva King Canopy
- nincs kategorizálva HeadRush
- nincs kategorizálva Flover
- nincs kategorizálva Milestone Systems
- nincs kategorizálva Micsig
- nincs kategorizálva Dodow
- nincs kategorizálva Spring
- nincs kategorizálva Red Panda
- nincs kategorizálva OJ ELECTRONICS
- nincs kategorizálva Aquasure
- nincs kategorizálva Banana Pi
- nincs kategorizálva Ilford
- nincs kategorizálva Crazy Tube Circuits
- nincs kategorizálva J.P. Instruments
- nincs kategorizálva GMB Gaming
- nincs kategorizálva Proclip
- nincs kategorizálva SainSmart
- nincs kategorizálva Kaona
- nincs kategorizálva Baja Mobility
- nincs kategorizálva DPW Design
- nincs kategorizálva SinuPulse
- nincs kategorizálva The T.bone
- nincs kategorizálva DIEZEL
- nincs kategorizálva VMB
- nincs kategorizálva Z.Vex
- nincs kategorizálva Seymour Duncan
- nincs kategorizálva BluGuitar
- nincs kategorizálva Lehle
- nincs kategorizálva Bricasti Design
- nincs kategorizálva T.akustik
- nincs kategorizálva Dwarf Connection
- nincs kategorizálva JL Cooper
- nincs kategorizálva StrikeMaster
- nincs kategorizálva ProUser
- nincs kategorizálva Bēm Wireless
- nincs kategorizálva Aqua-Vu
- nincs kategorizálva Millecroquettes
- nincs kategorizálva GR Bass
- nincs kategorizálva WilTec
- nincs kategorizálva Sure-Fi
- nincs kategorizálva Copernicus
- nincs kategorizálva Gumdrop
- nincs kategorizálva Tellur
- nincs kategorizálva Woox
- nincs kategorizálva Gallien-Krueger
- nincs kategorizálva Jetway
- nincs kategorizálva Texsport
- nincs kategorizálva SSV Works
- nincs kategorizálva Terre
- nincs kategorizálva Sanitec
- nincs kategorizálva Pangea Audio
- nincs kategorizálva Hogue
- nincs kategorizálva ATP
- nincs kategorizálva Pfannenberg
- nincs kategorizálva Scytek
- nincs kategorizálva MotorScrubber
- nincs kategorizálva Krone
- nincs kategorizálva Kraftmax
- nincs kategorizálva PCTV Systems
- nincs kategorizálva Cooper Lighting
- nincs kategorizálva Code Corporation
- nincs kategorizálva Now TV
- nincs kategorizálva Beautiful
- nincs kategorizálva Best Fitness
- nincs kategorizálva Voodoo Lab
- nincs kategorizálva Strymon
- nincs kategorizálva Insect Lore
- nincs kategorizálva Faytech
- nincs kategorizálva Chrome-Q
- nincs kategorizálva Kitronik
- nincs kategorizálva Trasman
- nincs kategorizálva Hamlet
- nincs kategorizálva SumUp
- nincs kategorizálva Microlab
- nincs kategorizálva Rotolight
- nincs kategorizálva Mr Gardener
- nincs kategorizálva Paladin
- nincs kategorizálva Lumu
- nincs kategorizálva WAYDOO
- nincs kategorizálva Fimer
- nincs kategorizálva ASIWO
- nincs kategorizálva Vankyo
- nincs kategorizálva OWC
- nincs kategorizálva Lexar
- nincs kategorizálva Vent-Axia
- nincs kategorizálva Firefield
- nincs kategorizálva E-Power
- nincs kategorizálva RectorSeal
- nincs kategorizálva Red Digital Cinema
- nincs kategorizálva Kaiser Nienhaus
- nincs kategorizálva Freeplay
- nincs kategorizálva Roller Grill
- nincs kategorizálva Zaor
- nincs kategorizálva Glorious
- nincs kategorizálva AVTech
- nincs kategorizálva Dataflex
- nincs kategorizálva Bugera
- nincs kategorizálva Handy Lux
- nincs kategorizálva Rossum Electro-Music
- nincs kategorizálva Panta
- nincs kategorizálva Pentel
- nincs kategorizálva Wallas
- nincs kategorizálva Gima
- nincs kategorizálva MagnaPool
- nincs kategorizálva Aquadon
- nincs kategorizálva Raidsonic
- nincs kategorizálva Approx
- nincs kategorizálva Gamesir
- nincs kategorizálva Neunaber
- nincs kategorizálva Leotec
- nincs kategorizálva VOREL
- nincs kategorizálva Ciarra
- nincs kategorizálva Ocean Way Audio
- nincs kategorizálva DayStar Filters
- nincs kategorizálva Flexispot
- nincs kategorizálva OP/TECH
- nincs kategorizálva ETC
- nincs kategorizálva Nuki
- nincs kategorizálva EOTech
- nincs kategorizálva Cinderella
- nincs kategorizálva Bauhn
- nincs kategorizálva Aspen
- nincs kategorizálva Cottons
- nincs kategorizálva TVLogic
- nincs kategorizálva CAD Audio
- nincs kategorizálva Frequency Central
- nincs kategorizálva Sacrament
- nincs kategorizálva The Box
- nincs kategorizálva AudioThing
- nincs kategorizálva Feelworld
- nincs kategorizálva SoundPEATS
- nincs kategorizálva Cambium Networks
- nincs kategorizálva Trident
- nincs kategorizálva Schoeps
- nincs kategorizálva HPI Racing
- nincs kategorizálva Trijicon
- nincs kategorizálva Favini
- nincs kategorizálva Dnipro
- nincs kategorizálva IFootage
- nincs kategorizálva Sonuus
- nincs kategorizálva Cabasse
- nincs kategorizálva Jonsered
- nincs kategorizálva Saint Algue
- nincs kategorizálva Cactus
- nincs kategorizálva Oecolux
- nincs kategorizálva SoundLAB
- nincs kategorizálva ACL
- nincs kategorizálva Mars Gaming
- nincs kategorizálva Radiant
- nincs kategorizálva G.Skill
- nincs kategorizálva Edbak
- nincs kategorizálva Integral LED
- nincs kategorizálva Integral
- nincs kategorizálva Roline
- nincs kategorizálva Virax
- nincs kategorizálva MSW
- nincs kategorizálva Amaran
- nincs kategorizálva Gill
- nincs kategorizálva AMC
- nincs kategorizálva Triangle
- nincs kategorizálva Tumbleweed
- nincs kategorizálva Alutruss
- nincs kategorizálva Sunpentown
- nincs kategorizálva Hamstra
- nincs kategorizálva PVI
- nincs kategorizálva Grendel
- nincs kategorizálva Coravin
- nincs kategorizálva O&O Software
- nincs kategorizálva Wasp
- nincs kategorizálva Chef's Choice
- nincs kategorizálva Ciclo
- nincs kategorizálva Warmup
- nincs kategorizálva Brastemp
- nincs kategorizálva Wavtech
- nincs kategorizálva Satco
- nincs kategorizálva AMT
- nincs kategorizálva Royal Catering
- nincs kategorizálva Artrom
- nincs kategorizálva Lowell
- nincs kategorizálva Adonit
- nincs kategorizálva Point Source Audio
- nincs kategorizálva ANDYCINE
- nincs kategorizálva AmpliVox
- nincs kategorizálva Pippi
- nincs kategorizálva Casalux
- nincs kategorizálva CyberData Systems
- nincs kategorizálva Omnitron Systems
- nincs kategorizálva Stewart Systems
- nincs kategorizálva Qubino
- nincs kategorizálva Eurosound
- nincs kategorizálva WyreStorm
- nincs kategorizálva Williams Sound
- nincs kategorizálva Magewell
- nincs kategorizálva Globalo
- nincs kategorizálva Adam Hall
- nincs kategorizálva SoundTube
- nincs kategorizálva Therabody
- nincs kategorizálva Infortrend
- nincs kategorizálva STI
- nincs kategorizálva Rug Doctor
- nincs kategorizálva Mad Dog
- nincs kategorizálva Raspberry Pi
- nincs kategorizálva Bals
- nincs kategorizálva Balt
- nincs kategorizálva AJ.BA
- nincs kategorizálva ESKA
- nincs kategorizálva Lascar Electronics
- nincs kategorizálva EWON
- nincs kategorizálva Sport-Tronic
- nincs kategorizálva Alga
- nincs kategorizálva WesAudio
- nincs kategorizálva Hamron
- nincs kategorizálva Robust
- nincs kategorizálva Heritage Audio
- nincs kategorizálva Quik Lok
- nincs kategorizálva Tsakalis AudioWorks
- nincs kategorizálva MagTek
- nincs kategorizálva Jupiter
- nincs kategorizálva Sony Optiarc
- nincs kategorizálva Colortone
- nincs kategorizálva Lowel
- nincs kategorizálva Anybus
- nincs kategorizálva Super Rod
- nincs kategorizálva Carnielli
- nincs kategorizálva Luminex
- nincs kategorizálva HiLook
- nincs kategorizálva P3 International
- nincs kategorizálva Idec
- nincs kategorizálva Beckmann & Egle
- nincs kategorizálva Seek Thermal
- nincs kategorizálva VintageView
- nincs kategorizálva Alfresco
- nincs kategorizálva Bintec-elmeg
- nincs kategorizálva Crane Song
- nincs kategorizálva W'eau
- nincs kategorizálva Ixxat
- nincs kategorizálva Belena
- nincs kategorizálva Fanox
- nincs kategorizálva Crouzet
- nincs kategorizálva Megarevo
- nincs kategorizálva Tech 21
- nincs kategorizálva Petmate
- nincs kategorizálva BlendMount
- nincs kategorizálva Perlick
- nincs kategorizálva Sedona
- nincs kategorizálva Tecnoinox
- nincs kategorizálva CaterRacks
- nincs kategorizálva Besco
- nincs kategorizálva Prologue
- nincs kategorizálva Atosa
- nincs kategorizálva Nanoleaf
- nincs kategorizálva Mach Power
- nincs kategorizálva Soltection
- nincs kategorizálva Kool-It
- nincs kategorizálva Cool Head
- nincs kategorizálva KeepOut
- nincs kategorizálva LawnMaster
- nincs kategorizálva Deltronic
- nincs kategorizálva Eligent
- nincs kategorizálva Meris
- nincs kategorizálva Procare
- nincs kategorizálva AmerBox
- nincs kategorizálva Qu-Bit
- nincs kategorizálva Blue Lantern
- nincs kategorizálva CTA Digital
- nincs kategorizálva DivKid
- nincs kategorizálva Uniross
- nincs kategorizálva Panamax
- nincs kategorizálva FaseLunare
- nincs kategorizálva Götze & Jensen
- nincs kategorizálva (Recovery)
- nincs kategorizálva Twinkly
- nincs kategorizálva Acefast
- nincs kategorizálva Squarp Instruments
- nincs kategorizálva EtherWAN
- nincs kategorizálva Econ Connect
- nincs kategorizálva META
- nincs kategorizálva Shimbol
- nincs kategorizálva GC Audio
- nincs kategorizálva Einhell Bavaria
- nincs kategorizálva Motrona
- nincs kategorizálva Thalheimer
- nincs kategorizálva FeiYu-Tech
- nincs kategorizálva Aida
- nincs kategorizálva Apantac
- nincs kategorizálva VisionTek
- nincs kategorizálva Accsoon
- nincs kategorizálva Rothenberger
- nincs kategorizálva FeiyuTech
- nincs kategorizálva Losi
- nincs kategorizálva Bessey
- nincs kategorizálva A3
- nincs kategorizálva Serge
- nincs kategorizálva Gladiator
- nincs kategorizálva Mobli
- nincs kategorizálva Sonoff
- nincs kategorizálva G-Technology
- nincs kategorizálva Caroma
- nincs kategorizálva Sungale
- nincs kategorizálva Befaco
- nincs kategorizálva Waltec
- nincs kategorizálva Eartec
- nincs kategorizálva Portkeys
- nincs kategorizálva Westcott
- nincs kategorizálva EXSYS
- nincs kategorizálva Digiquest
- nincs kategorizálva Gewiss
- nincs kategorizálva Hagor
- nincs kategorizálva Glyph
- nincs kategorizálva Seco-Larm
- nincs kategorizálva Murr Elektronik
- nincs kategorizálva Massoth
- nincs kategorizálva Envitec
- nincs kategorizálva Mimo Monitors
- nincs kategorizálva Alula
- nincs kategorizálva Blebox
- nincs kategorizálva VS Sassoon
- nincs kategorizálva Redsbaby
- nincs kategorizálva Bright Spark
- nincs kategorizálva Algo
- nincs kategorizálva Peloton
- nincs kategorizálva Gentrax
- nincs kategorizálva Brocade
- nincs kategorizálva ICC
- nincs kategorizálva Insteon
- nincs kategorizálva Amer
- nincs kategorizálva Warner Bros
- nincs kategorizálva Vinotemp
- nincs kategorizálva Silent Knight
- nincs kategorizálva Mosconi
- nincs kategorizálva Ditek
- nincs kategorizálva Kingston Technology
- nincs kategorizálva Axxess
- nincs kategorizálva Wilson
- nincs kategorizálva Goki
- nincs kategorizálva CGV
- nincs kategorizálva My Arcade
- nincs kategorizálva Enttec
- nincs kategorizálva Tescoma
- nincs kategorizálva RF Elements
- nincs kategorizálva ALC
- nincs kategorizálva Holland Electronics
- nincs kategorizálva Arista
- nincs kategorizálva Chenbro Micom
- nincs kategorizálva Triumph Sports
- nincs kategorizálva Gasmate
- nincs kategorizálva Novo Nordisk
- nincs kategorizálva Ionmax
- nincs kategorizálva Seville Classics
- nincs kategorizálva TechLogix Networx
- nincs kategorizálva NuTone
- nincs kategorizálva Thermalright
- nincs kategorizálva Meross
- nincs kategorizálva Bxterra
- nincs kategorizálva Renogy
- nincs kategorizálva Babylonia
- nincs kategorizálva HeartSine
- nincs kategorizálva Bullet
- nincs kategorizálva Morrison
- nincs kategorizálva Ordo
- nincs kategorizálva Alphacool
- nincs kategorizálva Asetek
- nincs kategorizálva AZZA
- nincs kategorizálva Audibax
- nincs kategorizálva TechN
- nincs kategorizálva Eversolo
- nincs kategorizálva Davita
- nincs kategorizálva Giga Copper
- nincs kategorizálva Elsner
- nincs kategorizálva Séura
- nincs kategorizálva Cube Controls
- nincs kategorizálva Meridian
- nincs kategorizálva Donexon
- nincs kategorizálva Eve Audio
- nincs kategorizálva Axagon
- nincs kategorizálva Linq
- nincs kategorizálva Wortmann AG
- nincs kategorizálva DiGiGrid
- nincs kategorizálva Sanofi
- nincs kategorizálva Mitzu
- nincs kategorizálva Avteq
- nincs kategorizálva Seaward
- nincs kategorizálva Omega Altise
- nincs kategorizálva Fizzics
- nincs kategorizálva XFX
- nincs kategorizálva Leynew
- nincs kategorizálva Lauten Audio
- nincs kategorizálva Cropico
- nincs kategorizálva Sunwoda
- nincs kategorizálva Schleich
- nincs kategorizálva Unitech
- nincs kategorizálva FXLab
- nincs kategorizálva Middle Atlantic
- nincs kategorizálva Kincrome
- nincs kategorizálva BC Acoustique
- nincs kategorizálva Brockhaus HEUER
- nincs kategorizálva Reishunger
- nincs kategorizálva Ergotec
- nincs kategorizálva Dupla
- nincs kategorizálva APSystems
- nincs kategorizálva IODD
- nincs kategorizálva BYD
- nincs kategorizálva Tektronix
- nincs kategorizálva Aqua Medic
- nincs kategorizálva Gold Note
- nincs kategorizálva Oromed
- nincs kategorizálva Pylontech
- nincs kategorizálva Fire Sense
- nincs kategorizálva Grüniq
- nincs kategorizálva Goodwe
- nincs kategorizálva Moki
- nincs kategorizálva Enertex
- nincs kategorizálva IOTAVX
- nincs kategorizálva Ovation
- nincs kategorizálva InAlto
- nincs kategorizálva Enviroswim
- nincs kategorizálva Dobar
- nincs kategorizálva Vevor
- nincs kategorizálva Ovente
- nincs kategorizálva PowerColor
- nincs kategorizálva ISpring
- nincs kategorizálva WeFix
- nincs kategorizálva BCA
- nincs kategorizálva Saki
- nincs kategorizálva Smart365
- nincs kategorizálva Fosi Audio
- nincs kategorizálva ChargeHub
- nincs kategorizálva Eldat
- nincs kategorizálva NEP
- nincs kategorizálva SoundSwitch
- nincs kategorizálva Sera
- nincs kategorizálva Dostmann Electronic
- nincs kategorizálva JBC
- nincs kategorizálva DV Mark
- nincs kategorizálva MOON
- nincs kategorizálva Cuggl
- nincs kategorizálva HABAU
- nincs kategorizálva CVW
- nincs kategorizálva Earbreeze
- nincs kategorizálva Möhlenhoff
- nincs kategorizálva Taqua
- nincs kategorizálva Brainstorm
- nincs kategorizálva Colonial Elegance
- nincs kategorizálva Overtone Labs
- nincs kategorizálva IBEAM
- nincs kategorizálva Bühnen
- nincs kategorizálva Blukac
- nincs kategorizálva BendixKing
- nincs kategorizálva Tube-Tech
- nincs kategorizálva TCW Technologies
- nincs kategorizálva UNITEK
- nincs kategorizálva CoolerMaster
- nincs kategorizálva Rexing
- nincs kategorizálva The T.mix
- nincs kategorizálva Regula-Werk King
- nincs kategorizálva Inter-M
- nincs kategorizálva MIDI Solutions
- nincs kategorizálva Positive Grid
- nincs kategorizálva Amgrow
- nincs kategorizálva Xaphoon
- nincs kategorizálva Winchester
- nincs kategorizálva Lampa
- nincs kategorizálva Sinus Live
- nincs kategorizálva Sureguard
- nincs kategorizálva QuickCool
- nincs kategorizálva Smit Visual
- nincs kategorizálva NZR
- nincs kategorizálva Toparc
- nincs kategorizálva Oro-Med
- nincs kategorizálva Hex
- nincs kategorizálva Baby Cakes
- nincs kategorizálva Deflecto
- nincs kategorizálva ELMEKO
- nincs kategorizálva Tesseract Modular
- nincs kategorizálva Sport Dog
- nincs kategorizálva Nowsonic
- nincs kategorizálva Hubble Connected
- nincs kategorizálva ELTA Music
- nincs kategorizálva Dragonshock
- nincs kategorizálva We-Vibe
- nincs kategorizálva Budda
- nincs kategorizálva Electronics International
- nincs kategorizálva Lamar
- nincs kategorizálva Atlantis Land
- nincs kategorizálva White Lightning
- nincs kategorizálva GEV
- nincs kategorizálva Frient
- nincs kategorizálva Kaiser Fototechnik
- nincs kategorizálva Vishay
- nincs kategorizálva Rooboost
- nincs kategorizálva Bitspower
- nincs kategorizálva EAT
- nincs kategorizálva Comar
- nincs kategorizálva Freedor
- nincs kategorizálva Start International
- nincs kategorizálva C2G
- nincs kategorizálva AXITEC
- nincs kategorizálva Lingg & Janke
- nincs kategorizálva Auralex
- nincs kategorizálva Pieps
- nincs kategorizálva Innovative
- nincs kategorizálva Lynx Technik
- nincs kategorizálva Yuede
- nincs kategorizálva ClimeMET
- nincs kategorizálva Pliant Technologies
- nincs kategorizálva Prompter People
- nincs kategorizálva Astropet
- nincs kategorizálva Canopia
- nincs kategorizálva Wabeco
- nincs kategorizálva Swingline GBC
- nincs kategorizálva Spelsberg
- nincs kategorizálva Staudte-Hirsch
- nincs kategorizálva Universal Remote Control
- nincs kategorizálva Soundsphere
- nincs kategorizálva Aqua Computer
- nincs kategorizálva HEDD
- nincs kategorizálva Vinpower Digital
- nincs kategorizálva Magivaac
- nincs kategorizálva Lindemann
- nincs kategorizálva Silent Angel
- nincs kategorizálva IOptron
- nincs kategorizálva ZWO
- nincs kategorizálva Bbf
- nincs kategorizálva Club 3D
- nincs kategorizálva Sprolink
- nincs kategorizálva Thermionic Culture
- nincs kategorizálva Watercool
- nincs kategorizálva Moultrie
- nincs kategorizálva Skaarhoj
- nincs kategorizálva Whitestone
- nincs kategorizálva BMB
- nincs kategorizálva Advance
- nincs kategorizálva Arylic
- nincs kategorizálva Cloud
- nincs kategorizálva Sandia Aerospace
- nincs kategorizálva EK Water Blocks
- nincs kategorizálva Lamptron
- nincs kategorizálva PS Audio
- nincs kategorizálva Gudsen
- nincs kategorizálva Zendure
- nincs kategorizálva Envertech
- nincs kategorizálva Prism Sound
- nincs kategorizálva ID-Tech
- nincs kategorizálva FSP/Fortron
- nincs kategorizálva Meopta
- nincs kategorizálva MARTOR
- nincs kategorizálva Lumantek
- nincs kategorizálva SEADA
- nincs kategorizálva Honey-Can-Do
- nincs kategorizálva Promise Technology
- nincs kategorizálva Deity
- nincs kategorizálva Patriot
- nincs kategorizálva Taga Harmony
- nincs kategorizálva B.E.G.
- nincs kategorizálva Fixpoint
- nincs kategorizálva Enerdrive
- nincs kategorizálva Respironics
- nincs kategorizálva ChamSys
- nincs kategorizálva TESLA Electronics
- nincs kategorizálva Intesis
- nincs kategorizálva Nethix
- nincs kategorizálva Pluto
- nincs kategorizálva Laine
- nincs kategorizálva 3Doodler
- nincs kategorizálva Soundskins
- nincs kategorizálva Middle Atlantic Products
- nincs kategorizálva Loctite
- nincs kategorizálva Antelope
- nincs kategorizálva Astera
- nincs kategorizálva Sabco
- nincs kategorizálva Sensative
- nincs kategorizálva Plasma Cloud
- nincs kategorizálva Flo
- nincs kategorizálva Jungle Gym
- nincs kategorizálva Smart Media
- nincs kategorizálva Code
- nincs kategorizálva Mivar
- nincs kategorizálva SolaX Power
- nincs kategorizálva AURALiC
- nincs kategorizálva AkYtec
- nincs kategorizálva Bestgreen
- nincs kategorizálva MyPOS
- nincs kategorizálva Truetone
- nincs kategorizálva Starlink
- nincs kategorizálva Favero
- nincs kategorizálva Durvet
- nincs kategorizálva KNEKT
- nincs kategorizálva Gator Frameworks
- nincs kategorizálva Teia
- nincs kategorizálva The Joy Factory
- nincs kategorizálva Yuer
- nincs kategorizálva OLLO
- nincs kategorizálva Axor
- nincs kategorizálva MEPROLIGHT
- nincs kategorizálva Tactical Fiber Systems
- nincs kategorizálva GVision
- nincs kategorizálva Veber
- nincs kategorizálva SMS
- nincs kategorizálva Richgro
- nincs kategorizálva Varaluz
- nincs kategorizálva MIOPS
- nincs kategorizálva Enbrighten
- nincs kategorizálva Vicoustic
- nincs kategorizálva Albert Heijn
- nincs kategorizálva Yphix
- nincs kategorizálva Magliner
- nincs kategorizálva Magmatic
- nincs kategorizálva Comfortisse
- nincs kategorizálva Videotel Digital
- nincs kategorizálva Zylight
- nincs kategorizálva Smith-Victor
- nincs kategorizálva HuddleCamHD
- nincs kategorizálva MooreCo
- nincs kategorizálva BIOS Living
- nincs kategorizálva Connection
- nincs kategorizálva Blind Spot
- nincs kategorizálva Badiona
- nincs kategorizálva VMV
- nincs kategorizálva Digigram
- nincs kategorizálva Mutec
- nincs kategorizálva Black Hydra
- nincs kategorizálva Expressive E
- nincs kategorizálva Merging
- nincs kategorizálva Bellari
- nincs kategorizálva Altman
- nincs kategorizálva EXO
- nincs kategorizálva Hawke
- nincs kategorizálva Defender
- nincs kategorizálva Betty Bossi
- nincs kategorizálva FoxFury
- nincs kategorizálva Eller
- nincs kategorizálva Rotatrim
- nincs kategorizálva Peak Design
- nincs kategorizálva Uniropa
- nincs kategorizálva Eura
- nincs kategorizálva ESE
- nincs kategorizálva Claypaky
- nincs kategorizálva Hecate
- nincs kategorizálva Jinbei
- nincs kategorizálva Nearity
- nincs kategorizálva Gra-Vue
- nincs kategorizálva On-Stage
- nincs kategorizálva Inverx
- nincs kategorizálva Titanwolf
- nincs kategorizálva Uplink
- nincs kategorizálva Mybeo
- nincs kategorizálva Medicinalis
- nincs kategorizálva Bearware
- nincs kategorizálva Liam&Daan
- nincs kategorizálva Traco Power
- nincs kategorizálva CAME-TV
- nincs kategorizálva Nureva
- nincs kategorizálva Revic
- nincs kategorizálva Galcon
- nincs kategorizálva Creamsource
- nincs kategorizálva Telmax
- nincs kategorizálva Apollo Design
- nincs kategorizálva JoeCo
- nincs kategorizálva Holosun
- nincs kategorizálva Aconatic
- nincs kategorizálva Kluge
- nincs kategorizálva Arovec
- nincs kategorizálva SecureSafe
- nincs kategorizálva CubuSynth
- nincs kategorizálva Exelpet
- nincs kategorizálva Aplic
- nincs kategorizálva Imarflex
- nincs kategorizálva Tempmate
- nincs kategorizálva Stalco
- nincs kategorizálva Carlsbro
- nincs kategorizálva Ventev
- nincs kategorizálva Mobotix
- nincs kategorizálva Steelbody
- nincs kategorizálva PureLink
- nincs kategorizálva UNYKAch
- nincs kategorizálva VAVA
- nincs kategorizálva Mammut
- nincs kategorizálva Modbap Modular
- nincs kategorizálva Bluestork
- nincs kategorizálva INOGENI
- nincs kategorizálva Carry-on
- nincs kategorizálva AddLiving
- nincs kategorizálva IOIO
- nincs kategorizálva Beghelli
- nincs kategorizálva Nimbus
- nincs kategorizálva Coca-Cola
- nincs kategorizálva City Theatrical
- nincs kategorizálva Acros
- nincs kategorizálva Redback Technologies
- nincs kategorizálva Vent-A-Hood
- nincs kategorizálva GoXtreme
- nincs kategorizálva Bome
- nincs kategorizálva One Control
- nincs kategorizálva EQ Acoustics
- nincs kategorizálva AV Tool
- nincs kategorizálva Aquael
- nincs kategorizálva NEXTO DI
- nincs kategorizálva Thermarest
- nincs kategorizálva Fortinge
- nincs kategorizálva RF-Links
- nincs kategorizálva LiveU
- nincs kategorizálva Austral
- nincs kategorizálva HMD
- nincs kategorizálva Luxul
- nincs kategorizálva Cherub
- nincs kategorizálva ProLights
- nincs kategorizálva Xinfrared
- nincs kategorizálva Brizo
- nincs kategorizálva I-PRO
- nincs kategorizálva Europalms
- nincs kategorizálva DuroStar
- nincs kategorizálva Waterstone
- nincs kategorizálva Huslog
- nincs kategorizálva Mr Steam
- nincs kategorizálva DVDO
- nincs kategorizálva A-Designs
- nincs kategorizálva Henry Engineering
- nincs kategorizálva Primacoustic
- nincs kategorizálva HomeCraft
- nincs kategorizálva Heusinkveld
- nincs kategorizálva EnOcean
- nincs kategorizálva Storcube
- nincs kategorizálva Varia
- nincs kategorizálva Gurari
- nincs kategorizálva Fezz
- nincs kategorizálva ASI
- nincs kategorizálva Lexivon
- nincs kategorizálva Graff
- nincs kategorizálva Swiss Eye
- nincs kategorizálva Cane Creek
- nincs kategorizálva EPEVER
- nincs kategorizálva KED
- nincs kategorizálva Caberg
- nincs kategorizálva Exped
- nincs kategorizálva Lawn Star
- nincs kategorizálva Edouard Rousseau
- nincs kategorizálva GameDay
- nincs kategorizálva Sparkle
- nincs kategorizálva Söll
- nincs kategorizálva X-Lite
- nincs kategorizálva AXESS
- nincs kategorizálva Glemm
- nincs kategorizálva Ridem
- nincs kategorizálva StarIink
- nincs kategorizálva Noyafa
- nincs kategorizálva Envertec
- nincs kategorizálva Nordic Winter
- nincs kategorizálva Sensei
- nincs kategorizálva Volcano
- nincs kategorizálva XS Power
- nincs kategorizálva Wire Technologies
- nincs kategorizálva Taco Tuesday
- nincs kategorizálva CEEM
- nincs kategorizálva IMM Photonics
- nincs kategorizálva Field Optics
- nincs kategorizálva Robern
- nincs kategorizálva Signature Hardware
- nincs kategorizálva GRAUGEAR
- nincs kategorizálva Sure Petcare
- nincs kategorizálva Sortimo
- nincs kategorizálva Livall
- nincs kategorizálva Beaphar
- nincs kategorizálva Catit
- nincs kategorizálva WarmlyYours
- nincs kategorizálva Mebby
- nincs kategorizálva TONI&GUY
- nincs kategorizálva Balam Rush
- nincs kategorizálva Roesle
- nincs kategorizálva Oreg
- nincs kategorizálva Karran
- nincs kategorizálva Topex
- nincs kategorizálva OOONO
- nincs kategorizálva CaviLock
- nincs kategorizálva Origin Storage
- nincs kategorizálva Kostal
- nincs kategorizálva Stamos
- nincs kategorizálva Ulsonix
- nincs kategorizálva Stamony
- nincs kategorizálva Uniprodo
- nincs kategorizálva STANDARD
- nincs kategorizálva BigBlue
- nincs kategorizálva RC Allen
- nincs kategorizálva Plastkon
- nincs kategorizálva Triplett
- nincs kategorizálva Wiesenfield
- nincs kategorizálva Tele Vue
- nincs kategorizálva Bulgin
- nincs kategorizálva Pure 100
- nincs kategorizálva Petite Chérie
- nincs kategorizálva Njoy
- nincs kategorizálva Studio Titan
- nincs kategorizálva AstrHori
- nincs kategorizálva Icron
- nincs kategorizálva Pyrex
- nincs kategorizálva Platypus
- nincs kategorizálva Trezor
- nincs kategorizálva Yamazen
- nincs kategorizálva Ferrofish
- nincs kategorizálva HPRC
- nincs kategorizálva Really Right Stuff
- nincs kategorizálva Decimator
- nincs kategorizálva Chimera
- nincs kategorizálva ButtKicker
- nincs kategorizálva Blonder Tongue
- nincs kategorizálva Crystal Video
- nincs kategorizálva Tilta
- nincs kategorizálva Luxli
- nincs kategorizálva PAG
- nincs kategorizálva NeoMounts
- nincs kategorizálva Western Co.
- nincs kategorizálva ProFlo
- nincs kategorizálva Ruggard
- nincs kategorizálva DiversiTech
- nincs kategorizálva Violectric
- nincs kategorizálva Aalberg Audio
- nincs kategorizálva Evooch
- nincs kategorizálva Bolin Technology
- nincs kategorizálva Total Chef
- nincs kategorizálva Total
- nincs kategorizálva PoLabs
- nincs kategorizálva Taiji
- nincs kategorizálva Digi-Pas
- nincs kategorizálva Pfister
- nincs kategorizálva Fellow
- nincs kategorizálva Kolcraft
- nincs kategorizálva Klauke
- nincs kategorizálva Axler
- nincs kategorizálva Symmons
- nincs kategorizálva Gerber
- nincs kategorizálva Royale
- nincs kategorizálva Venicci
- nincs kategorizálva Das Keyboard
- nincs kategorizálva Schaffner
- nincs kategorizálva Vitec
- nincs kategorizálva Nicols
- nincs kategorizálva Physa
- nincs kategorizálva ARNOLD Lichttechnik
- nincs kategorizálva Matterport
- nincs kategorizálva API Audio
- nincs kategorizálva Moomin
- nincs kategorizálva Belulu
- nincs kategorizálva Jedo
- nincs kategorizálva RIX
- nincs kategorizálva Bayco
- nincs kategorizálva Dinstar
- nincs kategorizálva Noordi
- nincs kategorizálva Corona
- nincs kategorizálva Coors Light
- nincs kategorizálva Arco
- nincs kategorizálva KoolScapes
- nincs kategorizálva Netter Vibration
- nincs kategorizálva Califone
- nincs kategorizálva Dynon Avionics
- nincs kategorizálva Uvex
- nincs kategorizálva UAvionix
- nincs kategorizálva LARQ
- nincs kategorizálva ORCA
- nincs kategorizálva YA-MAN
- nincs kategorizálva CRAFT + MAIN
- nincs kategorizálva V-Tone
- nincs kategorizálva Hellberg
- nincs kategorizálva Stelzner
- nincs kategorizálva LightKeeper Pro
- nincs kategorizálva BMAX
- nincs kategorizálva Cressi
- nincs kategorizálva Singercon
- nincs kategorizálva Pivo
- nincs kategorizálva Sharkbite
- nincs kategorizálva CatSynth
- nincs kategorizálva Lantus
- nincs kategorizálva Pitsos
- nincs kategorizálva Lively
- nincs kategorizálva Ember
- nincs kategorizálva Sifflus
- nincs kategorizálva ACOPower
- nincs kategorizálva Nextorage
- nincs kategorizálva SolidDrive
- nincs kategorizálva Mac Tools
- nincs kategorizálva Phase Technology
- nincs kategorizálva Beltronics
- nincs kategorizálva Lahti Pro
- nincs kategorizálva Jan Nowak
- nincs kategorizálva HiRO
- nincs kategorizálva Vantrue
- nincs kategorizálva Elight
- nincs kategorizálva Forodi
- nincs kategorizálva CELLFAST
- nincs kategorizálva MOZOS
- nincs kategorizálva Buxton
- nincs kategorizálva IsoTek
- nincs kategorizálva Miracle Smile
- nincs kategorizálva Zacuto
- nincs kategorizálva VARI-LITE
- nincs kategorizálva Real Cable
- nincs kategorizálva Pengo
- nincs kategorizálva Sophos
- nincs kategorizálva Kica
- nincs kategorizálva Racktime
- nincs kategorizálva Starlight Xpress
- nincs kategorizálva Sightron
- nincs kategorizálva Simmons
- nincs kategorizálva Infosec
- nincs kategorizálva Leba
Legújabb útmutatók nincs kategorizálva

2 Április 2025

2 Április 2025

2 Április 2025

2 Április 2025

2 Április 2025

2 Április 2025

2 Április 2025

2 Április 2025

2 Április 2025

2 Április 2025