Használati útmutató IFM OY446S
IFM
nincs kategorizálva
OY446S
Olvassa el alább 📖 a magyar nyelvű használati útmutatót IFM OY446S (117 oldal) a nincs kategorizálva kategóriában. Ezt az útmutatót 6 ember találta hasznosnak és 2 felhasználó értékelte átlagosan 4.5 csillagra
Oldal 1/117
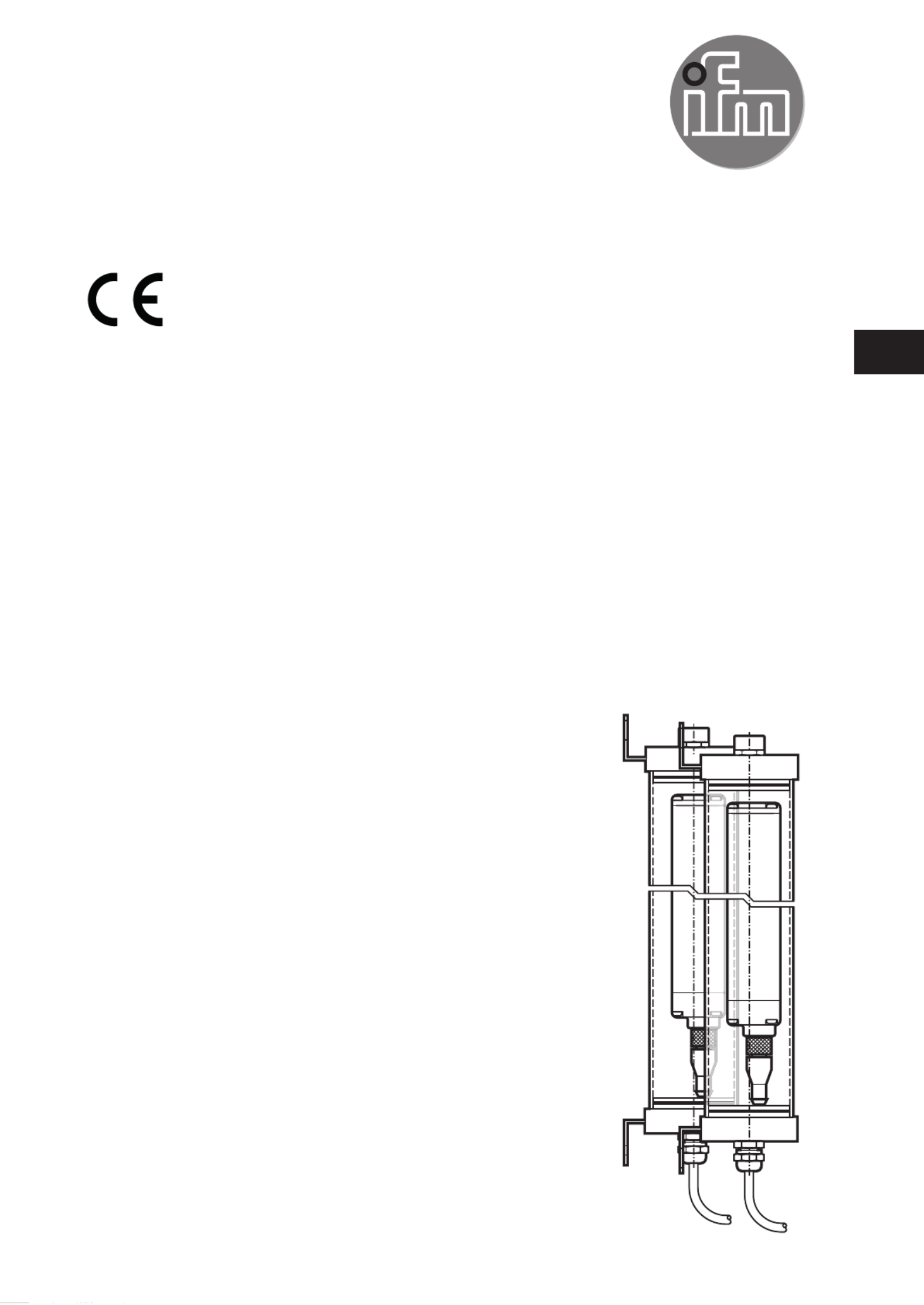
704860 / 04 12 / 2018
Original operating instructions
Photoelectric safety sensors
(safety light curtain / safety light grid)
with IP69K protective tube
Protected area width (range) 0...15 m
OY4xxS
UK
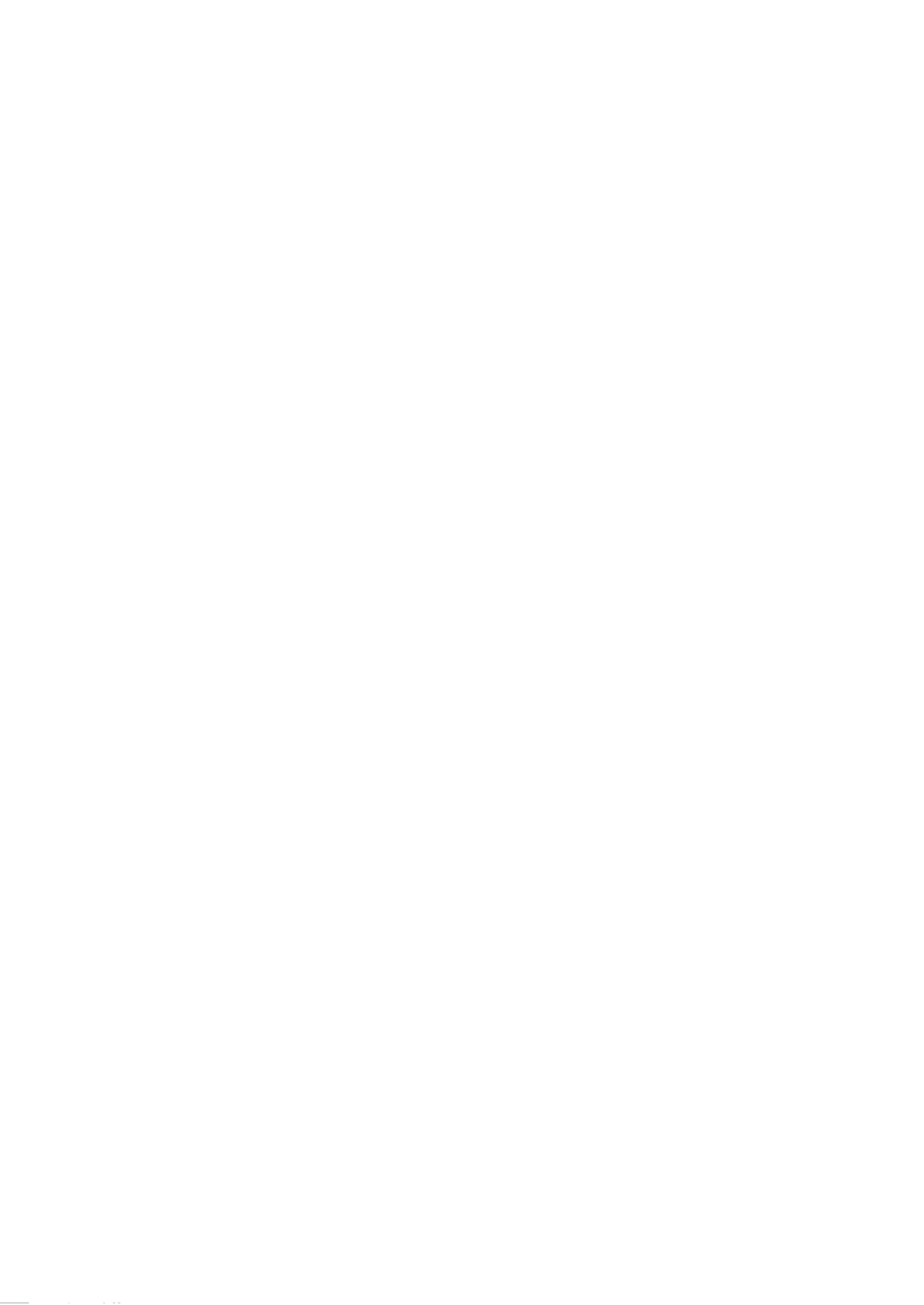
2
Contents
1 Preliminary note 4
...................................................................................................
1.1 Symbols used 4
................................................................................................
1.2 Warning signs used 4
.......................................................................................
2 Safety instructions 5
...............................................................................................
2.1 Safety-related requirements regarding the application 6
..................................
3 Items supplied......................................................................................................7
4 Functions and features 7
........................................................................................
5 Function ...............................................................................................................
8
6 Installation............................................................................................................9
6.1 Installation instructions 9
..................................................................................
6.2 Calculation of the minimum safety distance ................................................
11
6.3 Vertical installation of the safety light curtains / light grids 12
...........................
6.3.1 Safety light curtains: resolution 30 mm 12
...............................................
6.3.2 Safety light grids 2, 3 and 4 beams 13
....................................................
6.4 Horizontal installation of the safety light curtains 13
.........................................
6.5 Fixing and optical alignment 14
........................................................................
6.5.1 Optical alignment 14
................................................................................
6.6 Distance of reflective surfaces 15
.....................................................................
6.7 Multiple systems 17
..........................................................................................
6.8 Use of corner mirrors 18
...................................................................................
7 Electrical connection 19
..........................................................................................
7.1 Wiring diagram transmitter...........................................................................19
7.2 Wiring diagram receiver 20
...............................................................................
8 Operating modes 21
...............................................................................................
8.1 Automatic operation 22
.....................................................................................
8.2 Manual operation 22
.........................................................................................
8.3 Connection of external feedback contacts 23
..................................................
8.4 Test function 23
.................................................................................................
8.4.1 Internal test function 23
...........................................................................
9 Operating and display elements 24
........................................................................
9.1 LED indicators for optical alignment 24
............................................................
9.1.1 Alignment in the automatic mode 24
.......................................................
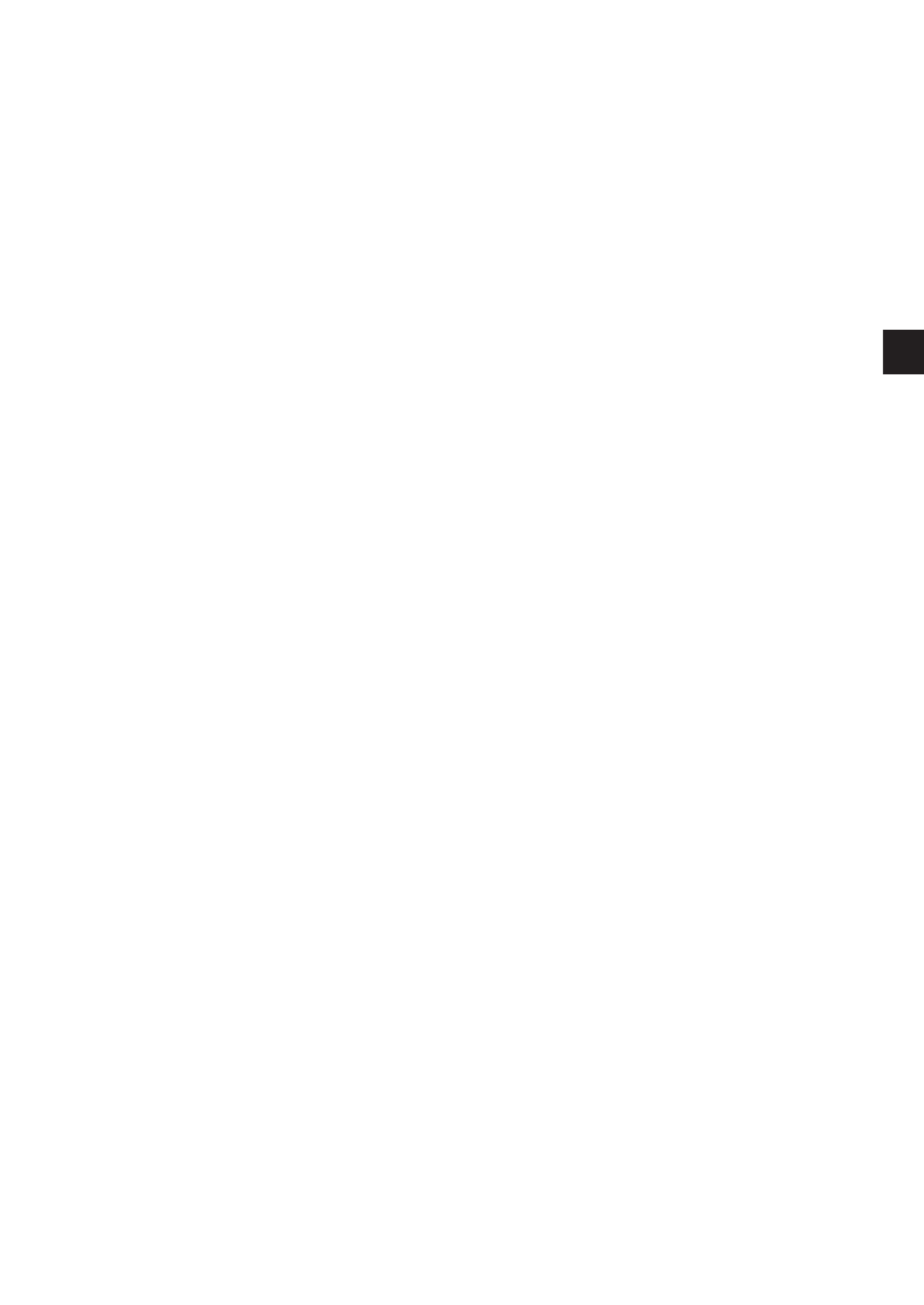
3
UK
9.1.2 Alignment in the manual mode 25
...........................................................
9.2 LED states 26
...................................................................................................
10 Operation .........................................................................................................
27
10.1 Switching state of the outputs 27
....................................................................
10.1.1 The safe state 27
...................................................................................
10.1.2 The switched state 27
............................................................................
10.1.3 Interface classification 27
......................................................................
10.2 Functional test of the safety light curtains 28
.................................................
11 Scale drawing 29
..................................................................................................
11.1 Safety light curtain 29
.....................................................................................
11.2 Safety light grid 30
..........................................................................................
11.2.1 Position of the light beams 31
................................................................
12 Technical Data 32
.................................................................................................
12.1 Heating ......................................................................................................
33
12.2 Safety light curtains: 30 mm resolution 33
......................................................
12.3 Safety light curtains: 40 mm resolution 34
......................................................
12.4 Safety light grids 2, 3 and 4 beams 34
...........................................................
13 Troubleshooting ...............................................................................................
34
13.1 Fault diagnosis transmitter 34
........................................................................
13.2 Fault diagnosis receiver 35
.............................................................................
14 Maintenance, repair and disposal 36
....................................................................
15 Terms and abbreviations 37
..................................................................................
16 Annex ...............................................................................................................
38
16.1 Check list 38
...................................................................................................
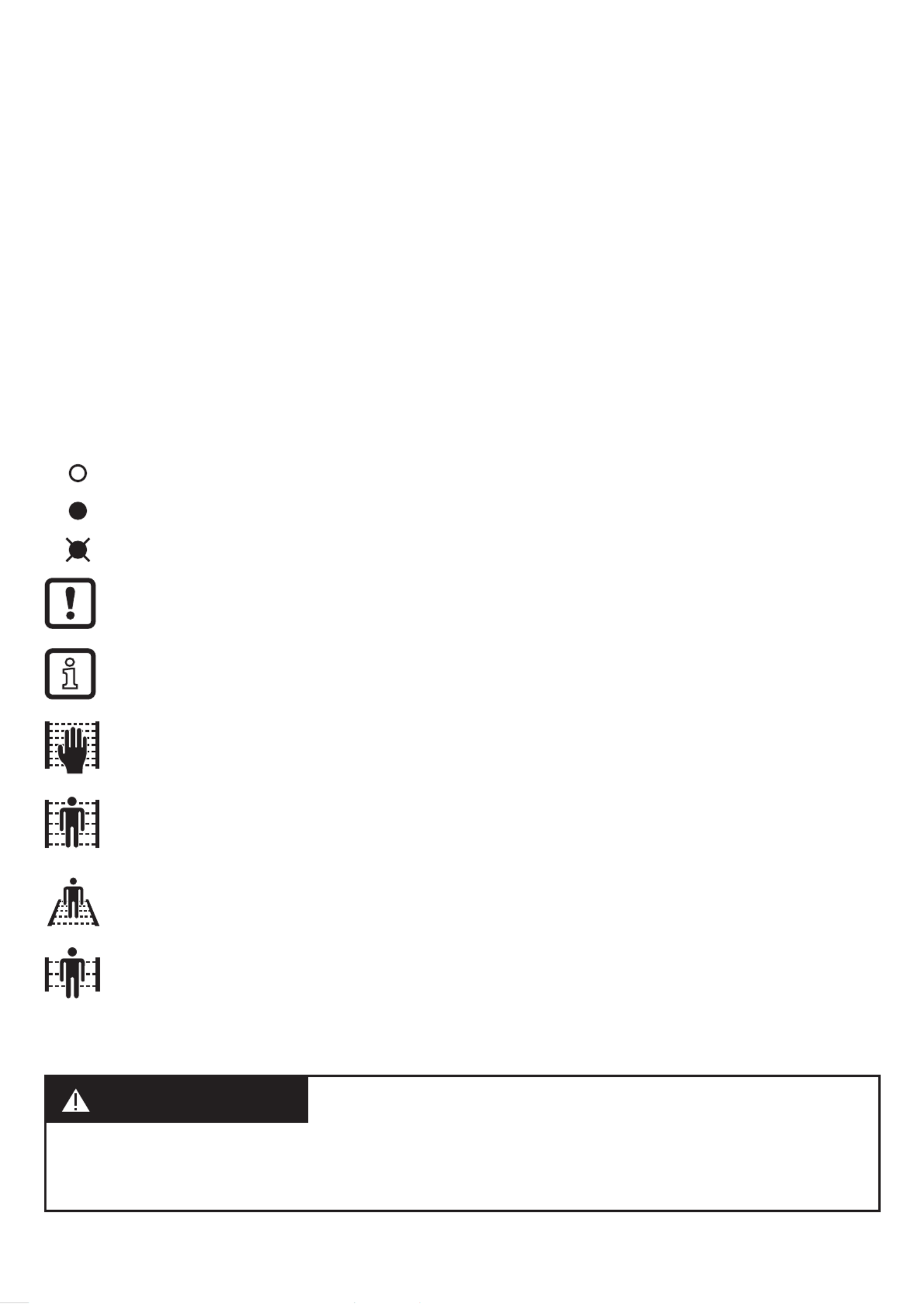
4
1 Preliminary note
The instructions are part of the unit. They are intended for authorised persons
according to the EMC and low voltage directives and safety regulations.
The instructions contain information about the correct handling of the product.
Read the instructions before use to familiarise yourself with operating conditions,
installation and operation.
Adhere to the safety instructions.
1.1 Symbols used
►Instructions
> Reaction, result
→Cross-reference
LED off
LED on
LED flashes
Important note
Non-compliance can result in malfunction or interference.
Information
Supplementary note.
Access prevention hand protection
Access prevention bodies or parts of bodies
Primary guarding bodies or parts of bodies
Access prevention body protection
1.2 Warning signs used
WARNING
Warning of serious personal injury.
Death or serious irreversible injuries may result.
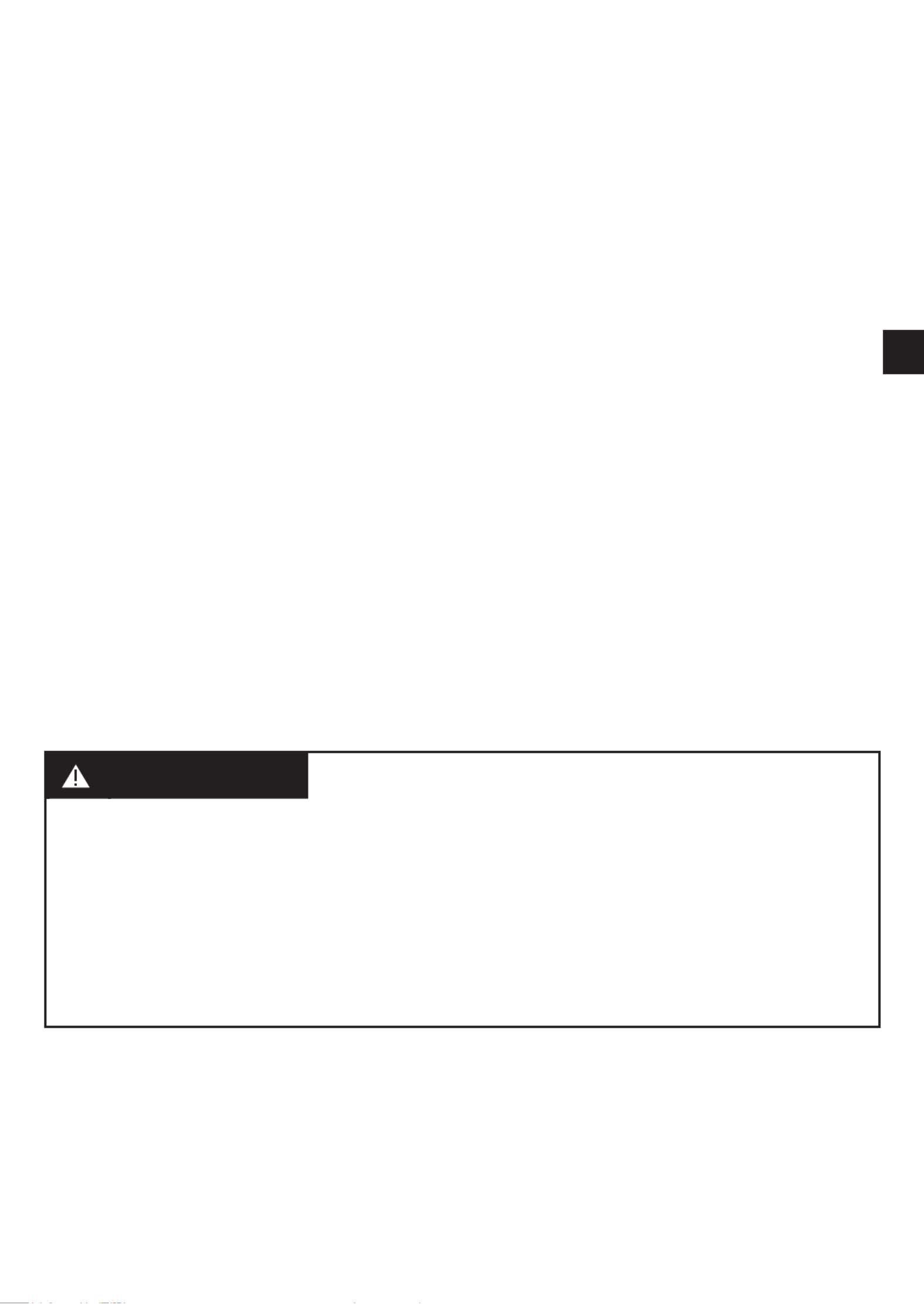
5
UK
2 Safety instructions
• Follow the operating instructions.
• In case of non-observance of notes or standards, specially when tampering
with and / or modifying the unit, any liability and warranty is excluded.
• The unit must be installed, connected and put into operation by a qualified
electrician trained in safety technology.
• The applicable technical standards for the corresponding application must be
complied with.
• For the installation the standards EN 60204, EN 999 and ISO 13855 have to be
observed.
• In case of malfunction of the unit please contact the manufacturer. Tampering
with the unit is not allowed.
• Disconnect the unit externally before handling it. Disconnect all relay load
circuits that are supplied independently.
• After set-up the system has to be subjected to a complete function check.
• Only use the unit under the specified operating conditions (→ 12 Technical
data). In case of special operating conditions please contact the manufacturer.
• In case of any questions concerning safety - if required - contact the safety
expert in charge of your country.
WARNING
In case of improper handling of the product, the safety and physical
integrity of operators and machinery cannot be guaranteed.
Death or serious irreversible injuries may result.
►Observe all notes on installation and handling in these instructions.
►The photoelectric safety sensors must only be used under the specified
operating conditions and in accordance with use as prescribed below.
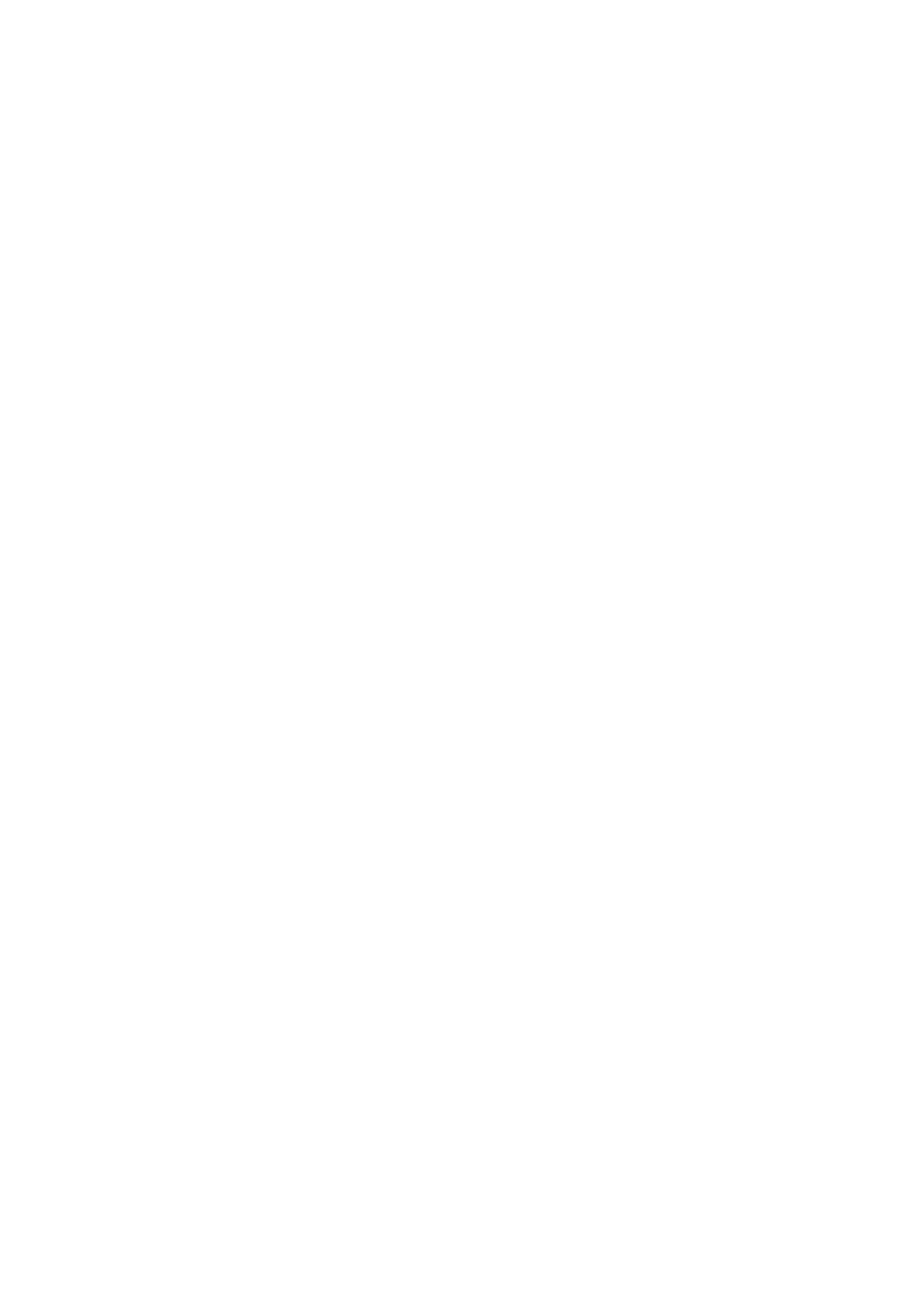
6
2.1 Safety-related requirements regarding the application
It must be ensured that the safety requirements of the respective application
correspond to the requirements stated in these instructions.
Observe the following requirements:
► Adhere to the specified operating conditions (→ 12 Technical data). Use of the
photoelectric safety sensors in the vicinity of ionising radiation is not permitted.
Furthermore, their use in the vicinity of chemically and biologically active media
is to be checked, if necessary.
►Material resistance tests of the photoelectric safety sensors with a protective
tube have been carried out for applications in the food industry. For the tested
chemicals see the respective ECOLAB certificate or contact your ifm branch
office.
►Adhere to the principle of normally closed operation for all external safety
circuits connected to the system.
►If the photoelectric safety sensors go into the state defined as safe due to an
internal fault, measures have to be taken to maintain the safe state when the
installation resumes operation.
►Replace damaged units.
The protective function of the photoelectric safety sensors is only ensured with the
following conditions:
• The machine control can be electrically controlled and the hazardous machine
motion can be stopped immediately at any time of the operation cycle.
• There is no danger for machine operators due to ejection of materials or
machine parts.
• The hazardous area is only accessible via the protected area.
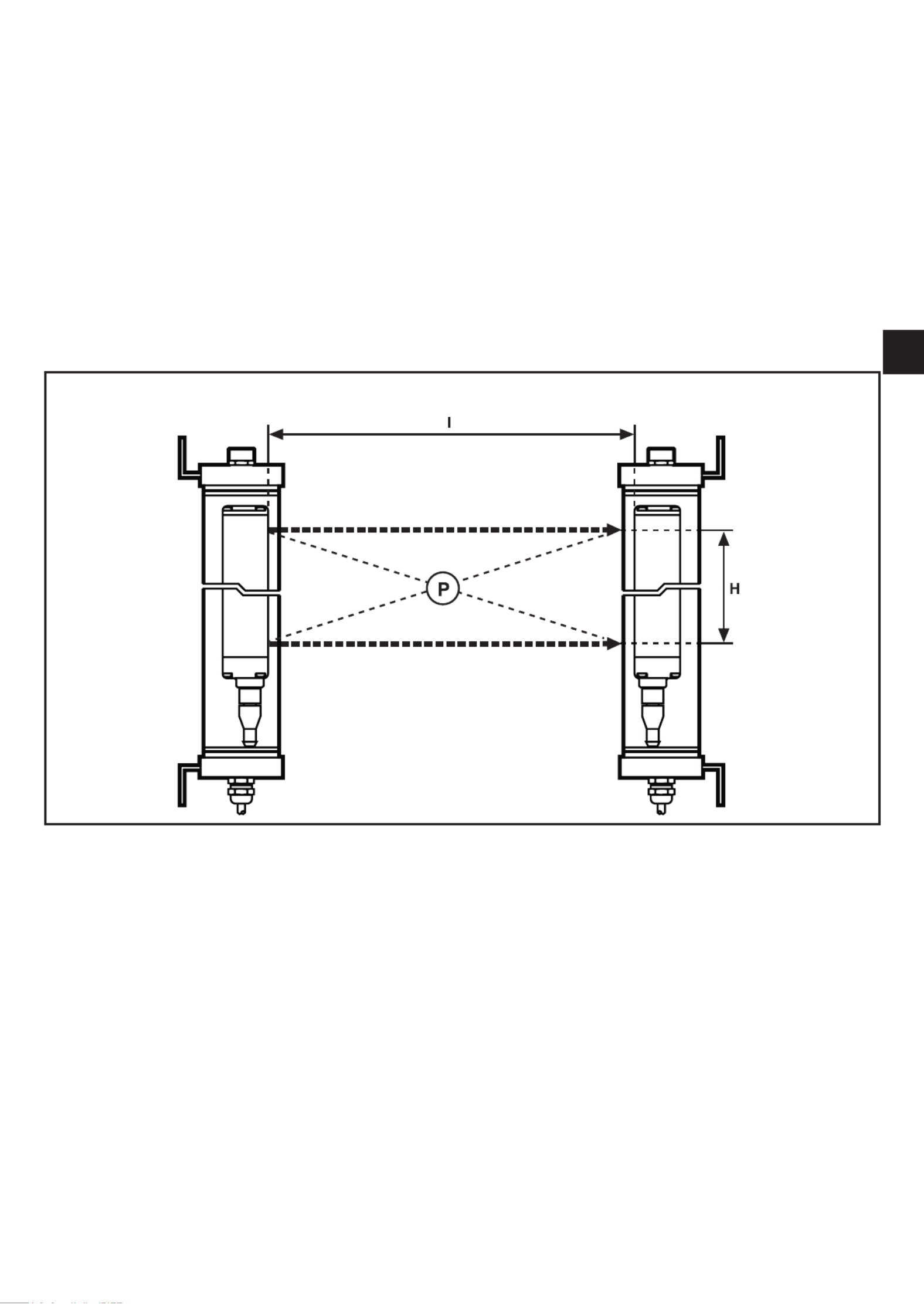
7
UK
3 Items supplied
• 2 photoelectric safety sensors (1 transmitter and 1 receiver) with IP69K
protective tube
• 1 operating instructions photoelectric safety sensors with IP69K protective
tube, reference number 704860
If one of the above-mentioned components is missing or damaged, please contact
one of the ifm branch offices.
4 Functions and features
transmitter (T) receiver (R)
P = protected area; I = protected area width (range) H = protected area height
The OY4xxS safety light curtains / light grids are multi-beam optoelectronic
protective devices to IEC 61496 and consist of one transmitter and one receiver.
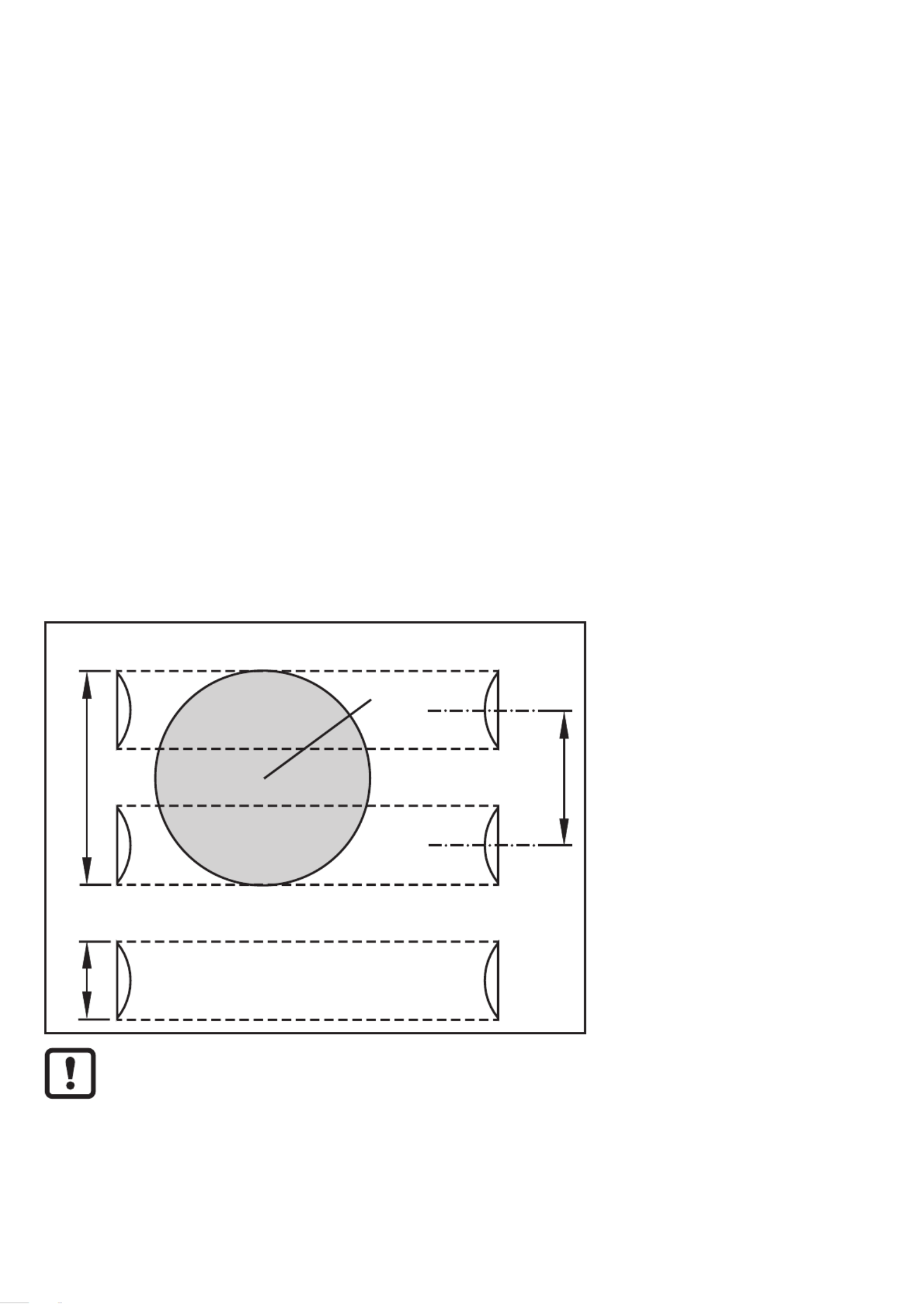
8
5 Function
The protected area (P) is generated between the transmitter and the receiver and
is defined by the protected area height (H) and the protected area width (range)
(I).
The protected area height is the height protected by the safety light curtain / safety
light grid. It depends on the design (→ 12 Technical data).
If the safety light curtains are installed horizontally, this value indicates the depth
of the protected area.
The protected area width (range) is the maximum distance between transmitter
and receiver (→ 12 Technical data).
If the protected area is clear, the two outputs (OSSDs) of the receiver are active.
If an object (O) with a diameter greater than or equal to the resolution (d) enters
the protected area, the outputs are switched off.
The resolution (d) (detection capability) of the safety light curtain depends on the
lens diameter (B) and the lens distance (C) and remains constant at all application
conditions.
transmitter (T) receiver (R)
O = object
C = lens distance
B = lens diameter
d = resolution
To ensure that an object (O) is reliably detected in the protected area the
dimensions of the object (O) must be at least as great as the resolution (d).
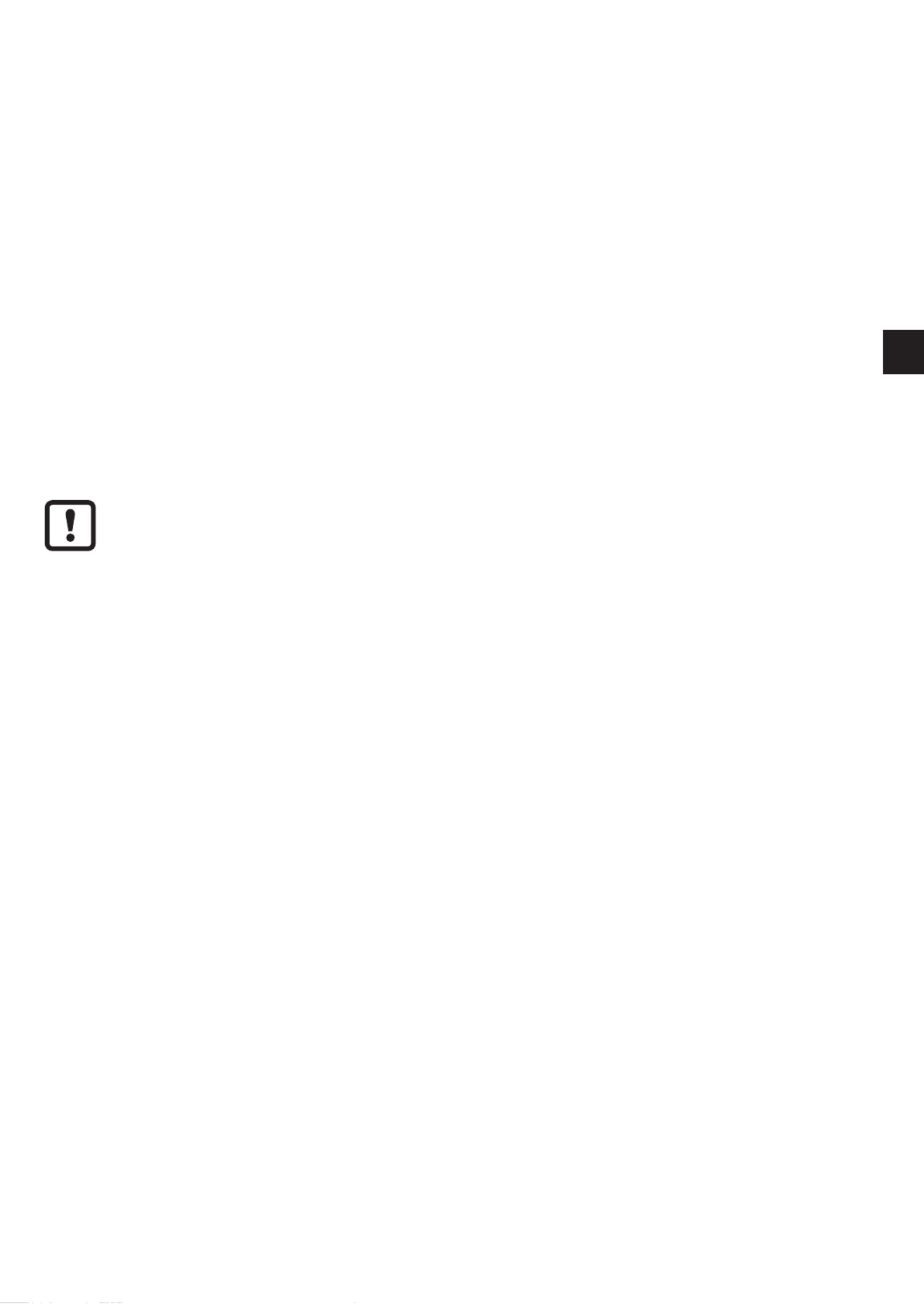
9
UK
6 Installation
6.1 Installation instructions
The following conditions are to be ensured before installation of the photoelectric
safety sensors:
• The degree of protection of the electro-sensitive equipment (ESPE) has to
correspond with the risk assessment of the machine to be monitored.
• The safety system ensures a safety function and is not required for the
operation of a machine.
• It must be possible to stop any hazardous motion of the machine immediately.
In this respect the shutdown delay of the machine has to be determined.
• The object to be detected must be greater than or equal to the resolution of the
photoelectric safety sensor.
Install the photoelectric safety sensors so that the hazardous area can only
be accessed via the protected area. Depending on the application other
mechanical protective equipment may be necessary.
The operating conditions at the mounting location must not affect the functioning
of the photoelectric safety sensors. Please note especially:
• The transmitter and the receiver must not be affected by intensive light sources
(emitters, sunlight etc.).
• The ambient temperature must be within the range indicated (→ 12 Technical
data).
• Fogging of the lenses due to considerable temperature fluctuations can affect
the functioning of the photoelectric safety sensors. Take appropriate measures
to prevent this.
• Certain operating conditions can affect the functioning of the photoelectric
safety sensors. For mounting locations where fog, rain, smoke or dust may
occur, it is recommended to take appropriate measures.
• The standards EN 999 and ISO 13855 must be adhered to.
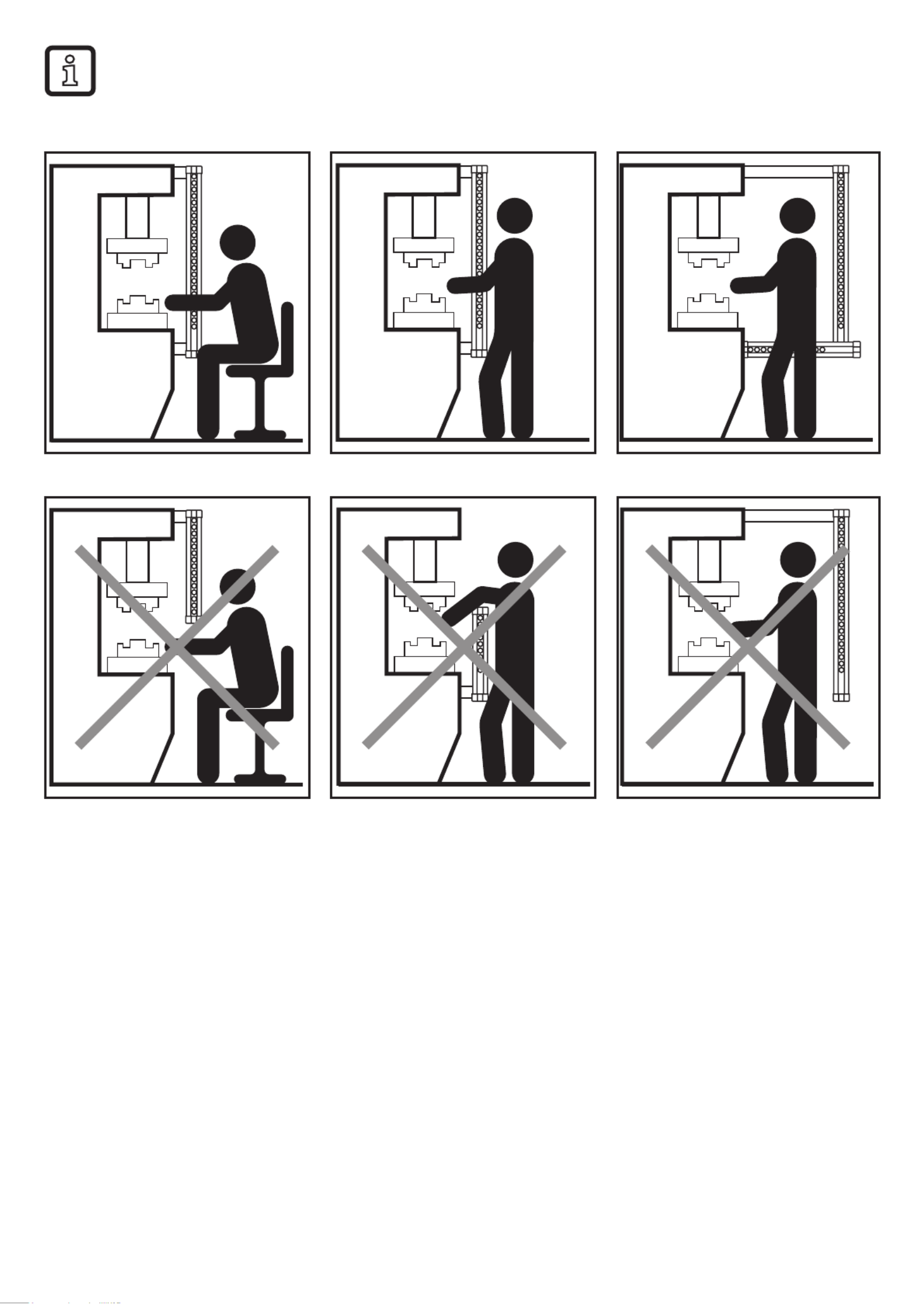
10
Observe the following illustrations for correct installation of the photoelectric
safety sensors.
Correct installation
Wrong installation
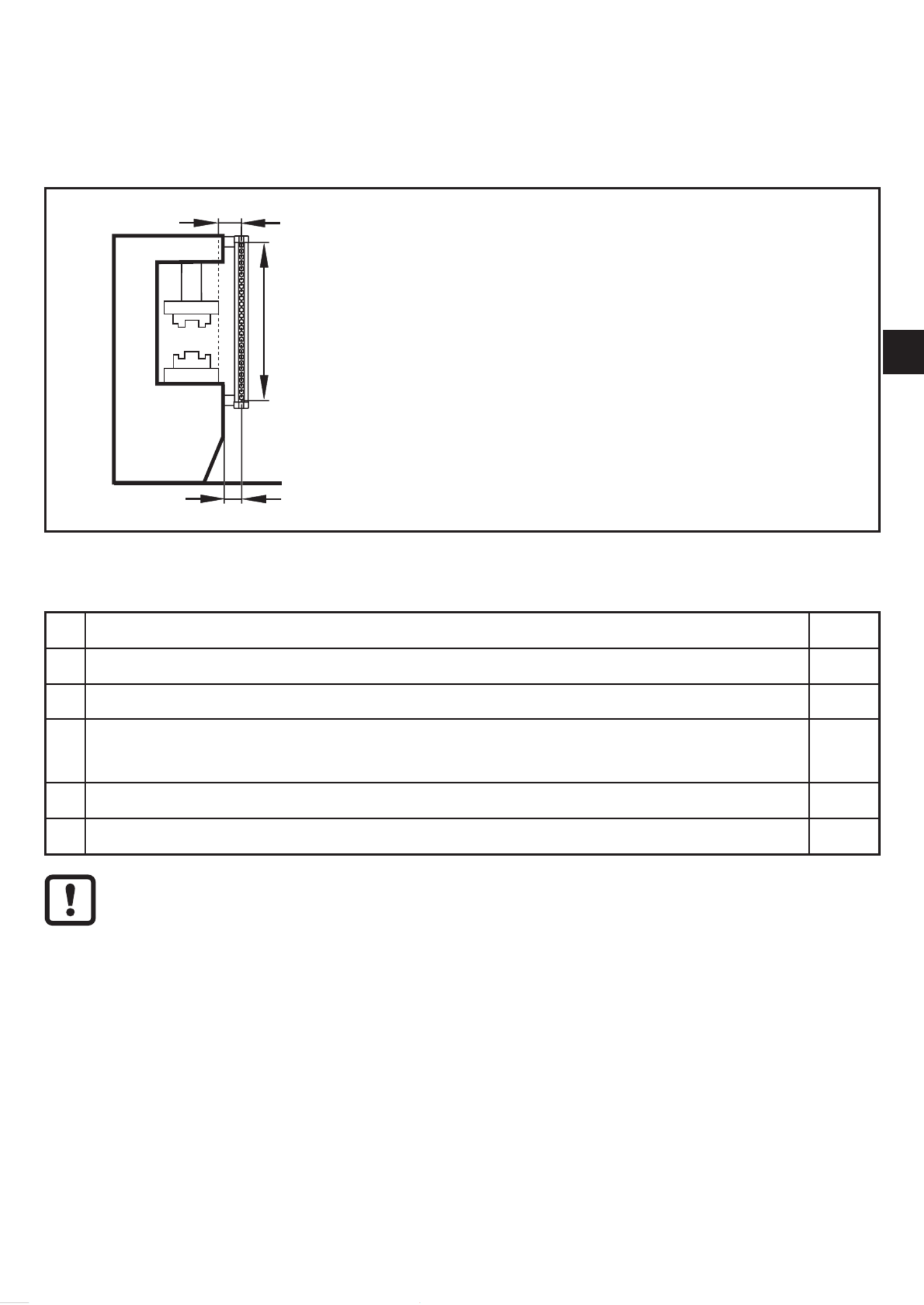
11
UK
6.2 Calculation of the minimum safety distance
There must be a minimum safe distance between the photoelectric safety sensor
and the point of danger. This distance must be ensured so that the point of danger
cannot be accessed before the hazardous state of the machine has been stopped.
►Install the photoelectric safety sensor at a distance
that is greater than or equal to the minimum safety
distance (S) so that the hazardous area (A) can
only be accessed after complete standstill of the
hazardous machine motion.
According to the European Standard EN 999:2008 the
following formula is to be used to calculate the minimum
safety distance (S):
S = K (t1 + t2) + C
C = 8 (d - 14)
A = hazardous area
H = protected area height
S = minimum safety distance
C = additional distance
S
Minimum safety distance mm
K
Speed of approach of the object towards the hazardous area mm/s
t1
Total response time of the protective equipment, from release to switching off s
t2
Total response time of the machine, from the stop signal to switching off or to
passing into the state defined as safe
s
C
Additional distance mm
d
Resolution (detection capacity) mm
Non-compliance with the minimum safety distance may lead to restrictions
to or loss of the safety function.
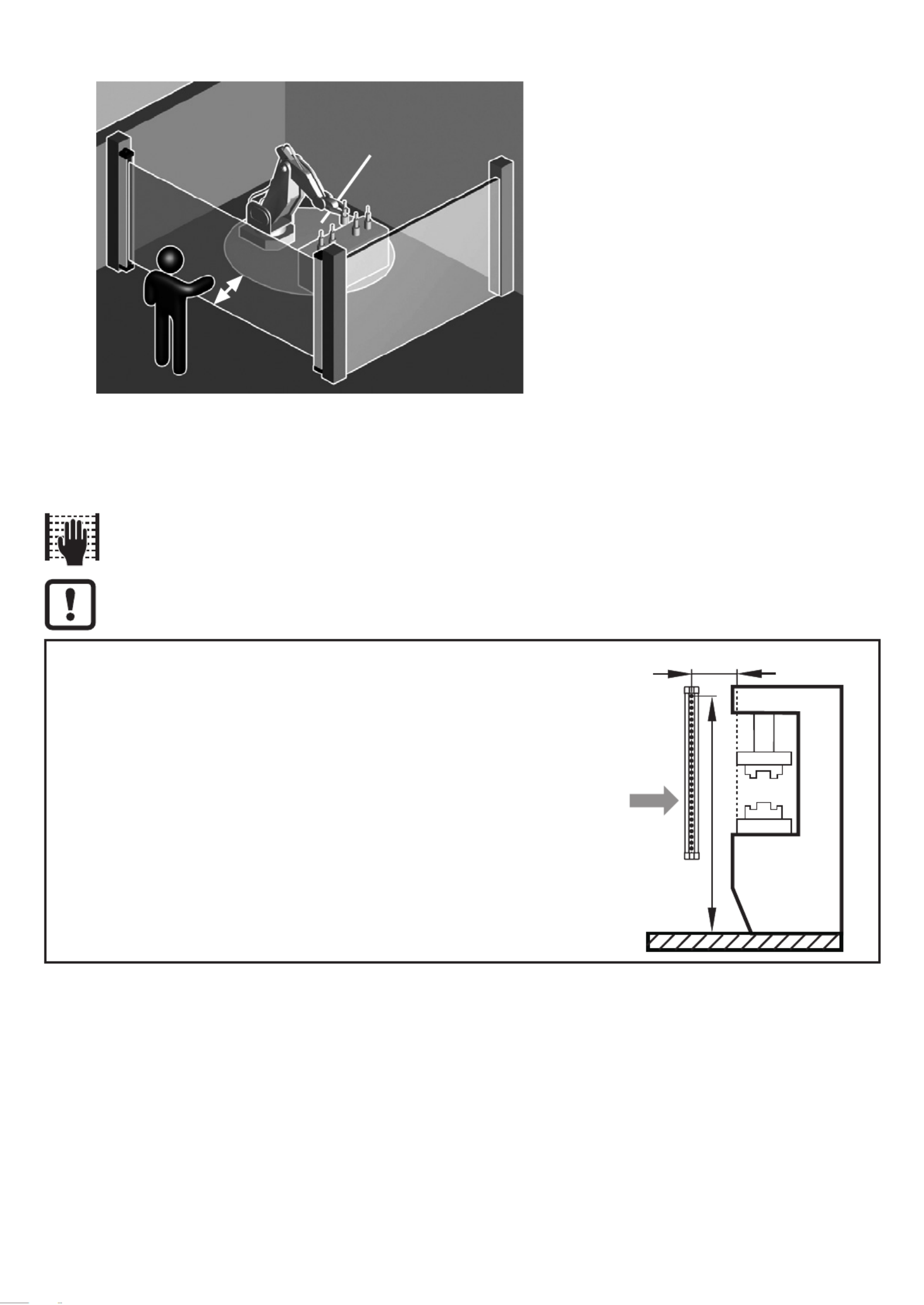
12
Application example:
A = hazardous area
S = min. safety distance
6.3 Vertical installation of the safety light curtains / light grids
6.3.1 Safety light curtains: resolution 30 mm
These designs are suitable for access prevention of hands (hand
protection).
They must not be used for finger protection!
The minimum safety distance (S) is determined using the
following formula:
S = 2000 (t1 + t2) + 8 (d - 14)
This formula applies to minimum safety distances (S)
between 100 and 500 mm. If the calculation shows that S
is greater than 500 mm, the distance can be reduced to a
minimum value of 500 mm by using the following formula:
S = 1600 (t1 + t2) + 8 (d - 14)
A = hazardous area
H = height
S = min. safety distance
G = reference level
If due to the special configuration of the machine it should be possible to reach
the hazardous area from above, the highest light beam of the safety light curtain
should be at a height (H) (measured from the reference level (G)) whose value is
determined to the specifications in ISO 13855.
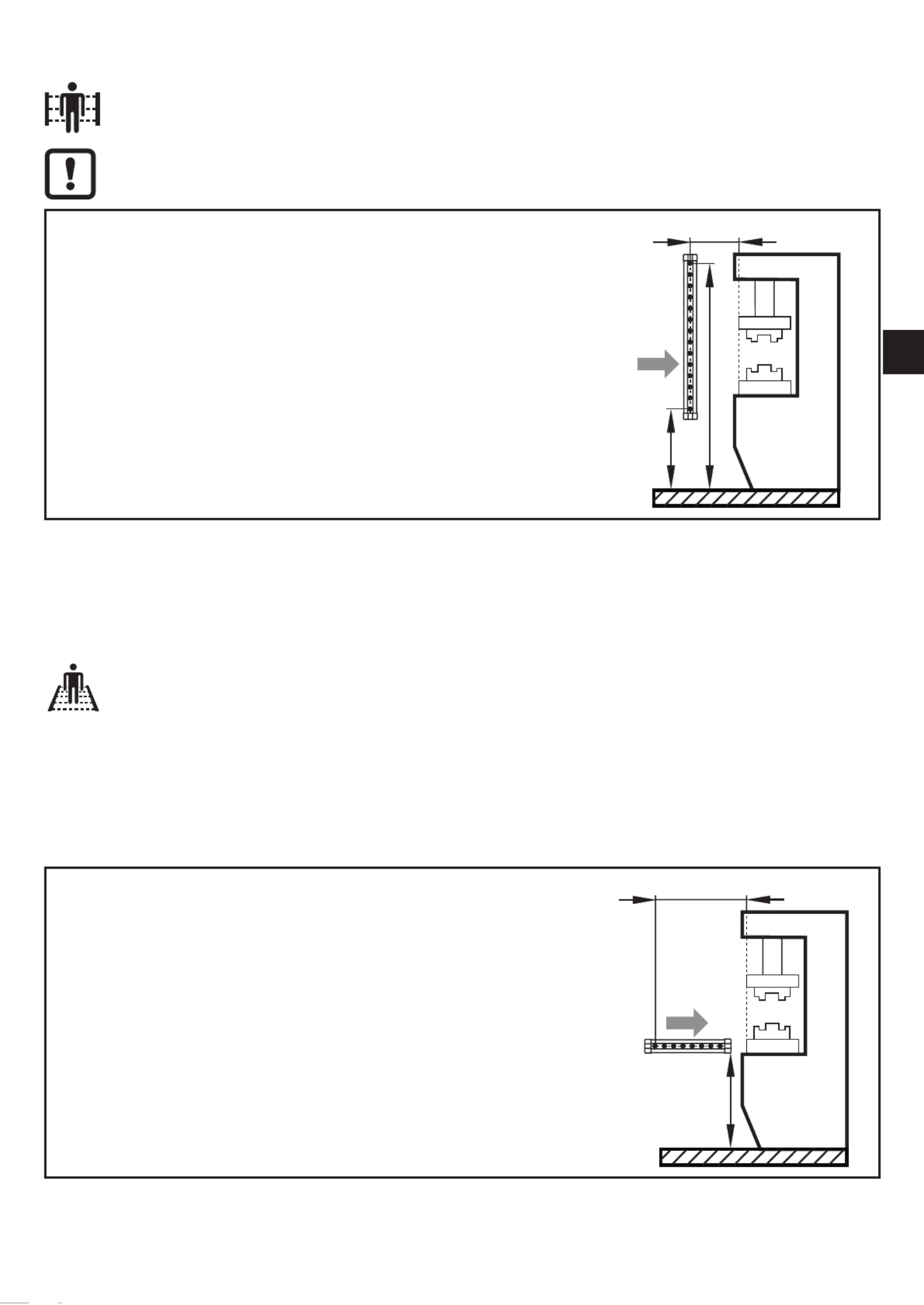
13
UK
6.3.2 Safety light grids 2, 3 and 4 beams
These versions are suitable for access prevention for entire bodies.
They must not be used for the protection of hands or body parts!
The minimum safety distance (S) is determined using the
following formula:
S = 1600 (t1 + t2) + 850
The height (H1) of the upper light beam measured from the
reference level (G) must not be shorter than 900 mm while
the height (H2) of the lowest light beam must not exceed
300 mm (ISO 13855).
A = hazardous area
Hx = height
S = min. safety distance
G = reference level
6.4 Horizontal installation of the safety light curtains
These versions are suitable for primary guarding for bodies or parts of
bodies.
With horizontal installation it has to be noted that the distance between the outer
border of the hazardous area (A) and the outer light beam of the safety light
curtain is greater than or equal to the minimum safety distance (S). It is calculated
as follows:
S = 1600 (t1 + t2) + 1200 – 0.4 H
with H being the height of the protected area of the
reference level (G) of the machine;
H = 15 (d - 50)
In this example the following applies: H < 1 m (to ISO
13855).
A = hazardous area
H = height
S = min. safety distance
G = reference level
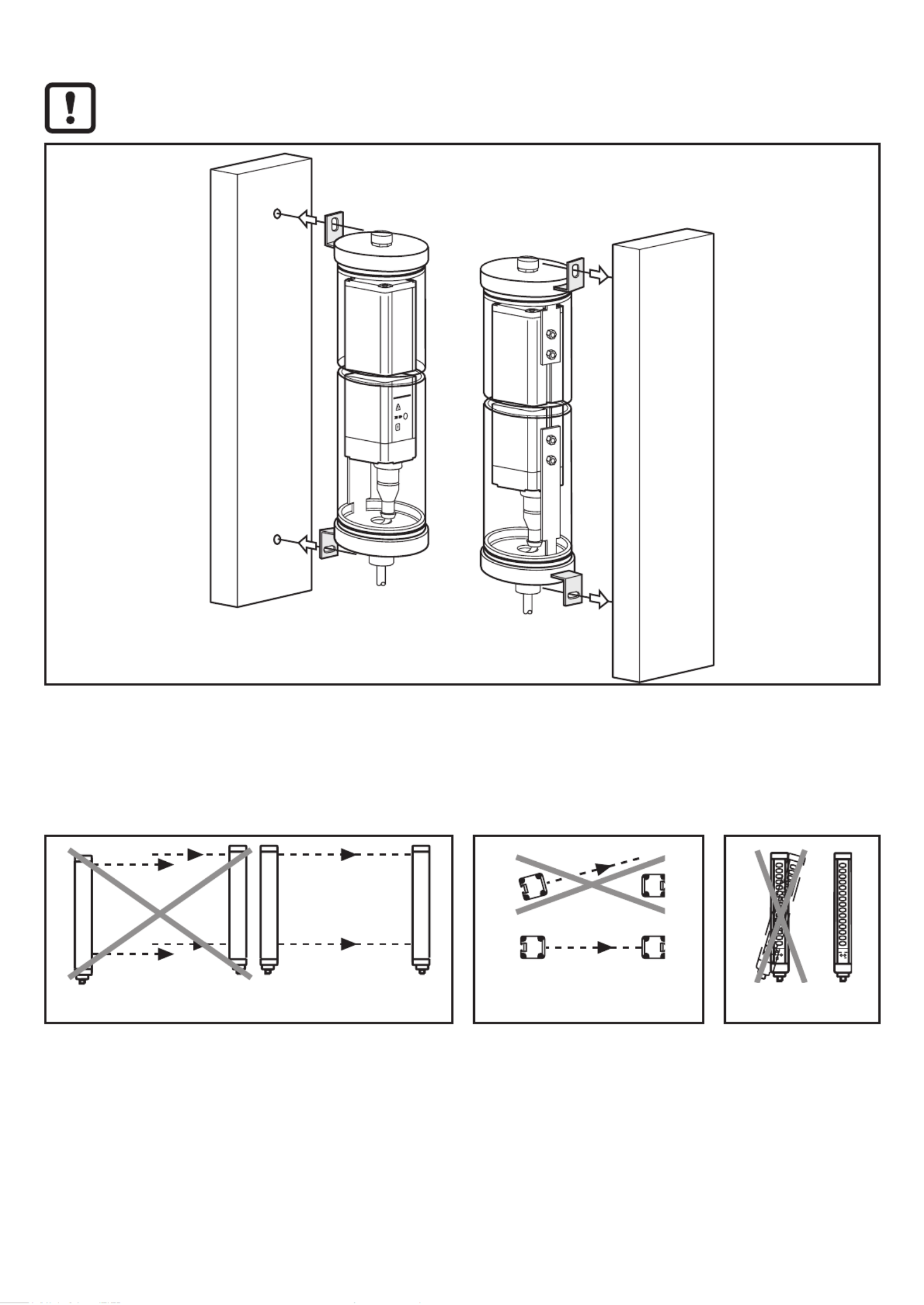
14
6.5 Fixing and optical alignment
Correct alignment of the transmitter and the receiver is decisive for the
proper function of the photoelectric safety sensors.
►Install the transmitter and the receiver so that they are exactly opposite each
other.
6.5.1 Optical alignment
T R T R T R T T
T = transmitter; R = receiver
►Align the transmitter and the receiver so that they are in parallel at the same
height and the cables face the same direction.
►
Fix the transmitter and the receiver.
The indication LEDs of the receiver help to correctly align the photoelectric safety
sensors. (→ 9.1 LED indicators for optical alignment)
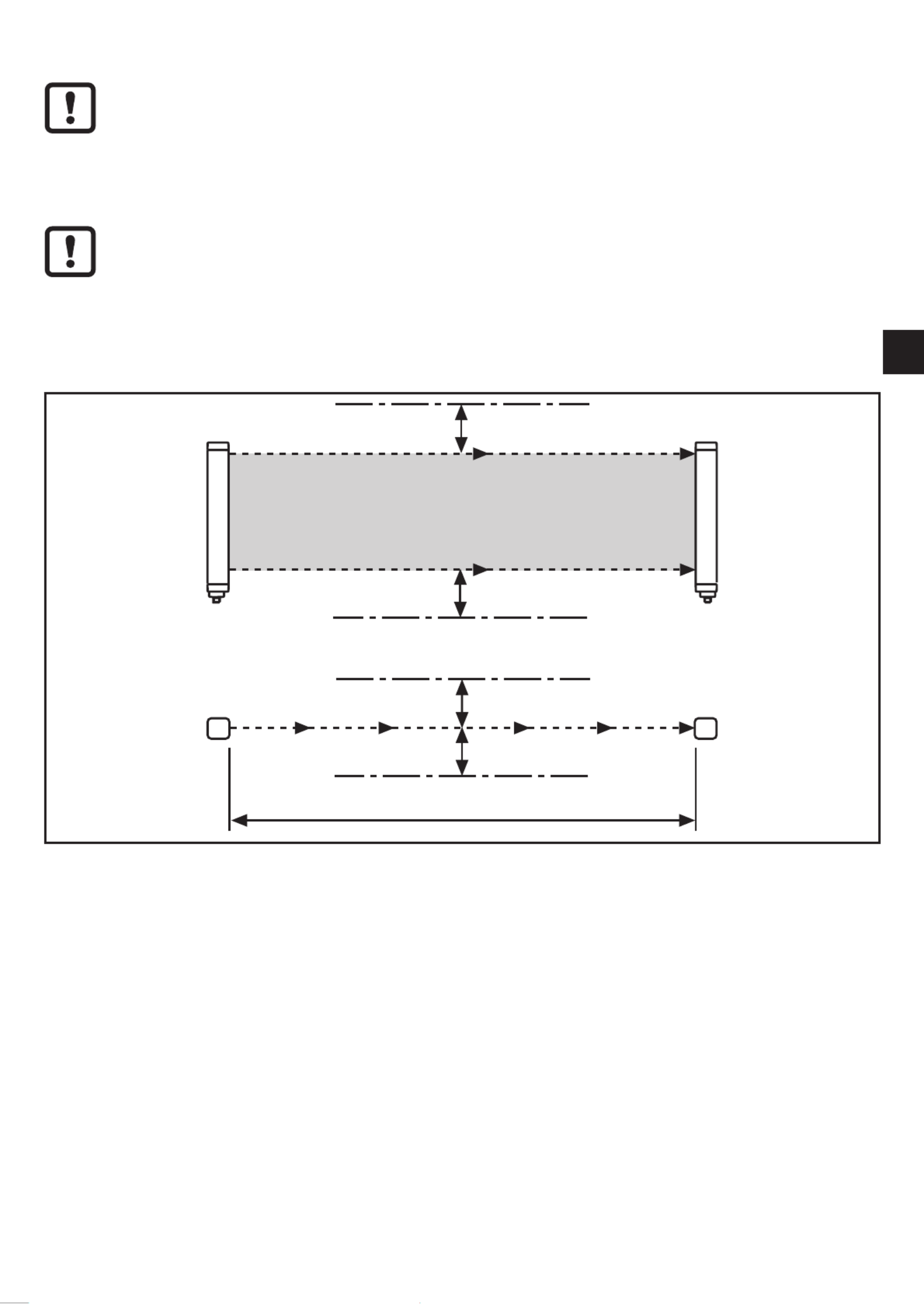
15
UK
6.6 Distance of reflective surfaces
Reflective surfaces close to photoelectric safety sensors can disable the
safety function of the system.
The minimum distance (D) depends on the protected area width (I) taking into
consideration the projection and receiving angles.
The minimum distance (D) between reflective surfaces and the protected
area (P) must be observed. In case of non-compliance an object which
has to be detected cannot be sensed. In case of improper handling of
the product, the safety and physical integrity of operators and machinery
cannot be guaranteed.
transmitter (T) receiver (R)
D = minimum distance; I = protected area width (range); P = protected area
►After installation test by intended interruption of the protected area (P) if
reflective surfaces affect the function of the photoelectric safety sensors.
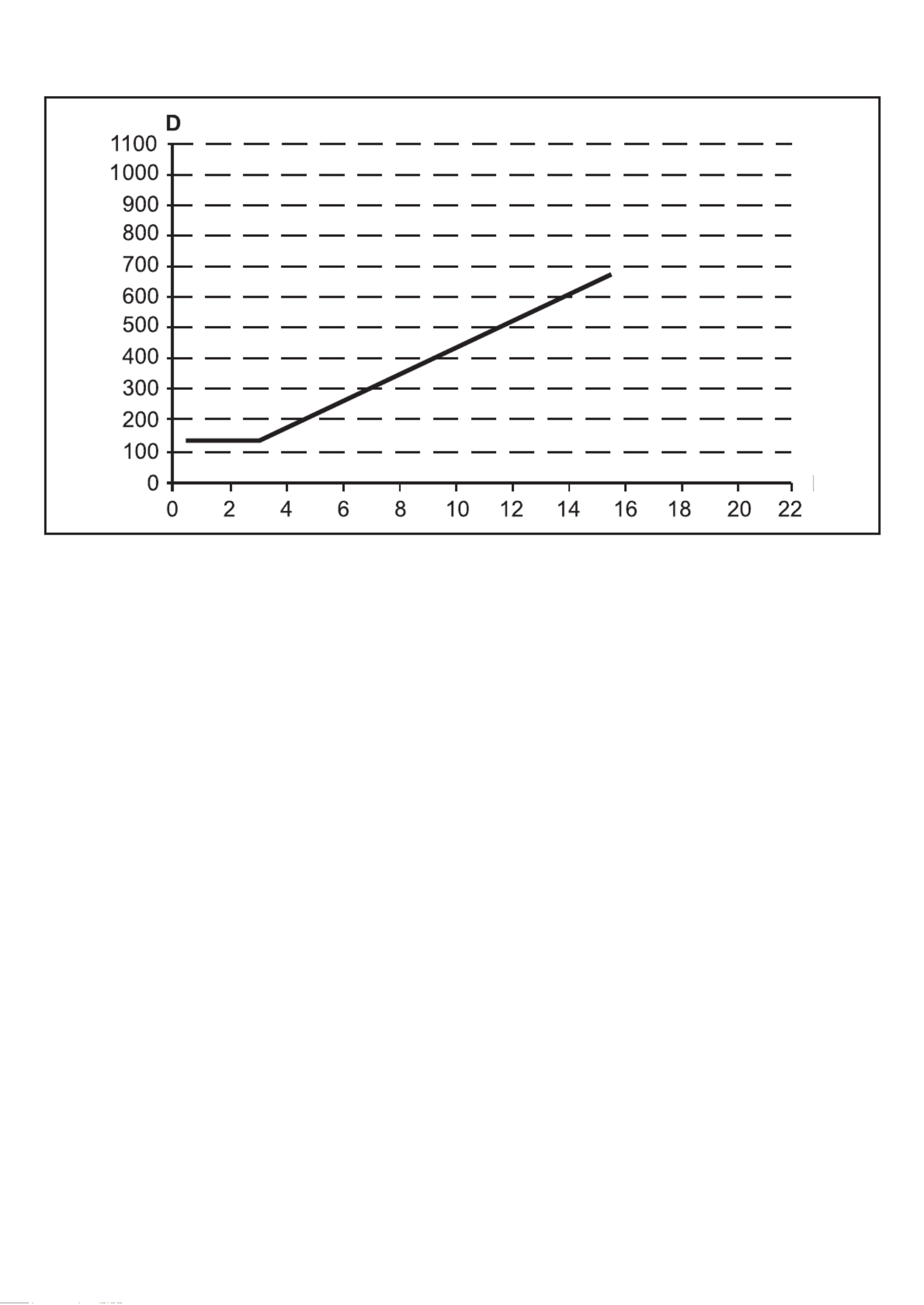
16
Minimum distance to reflective surfaces
D = minimum distance in [mm]; I = protected area width (range) [m]
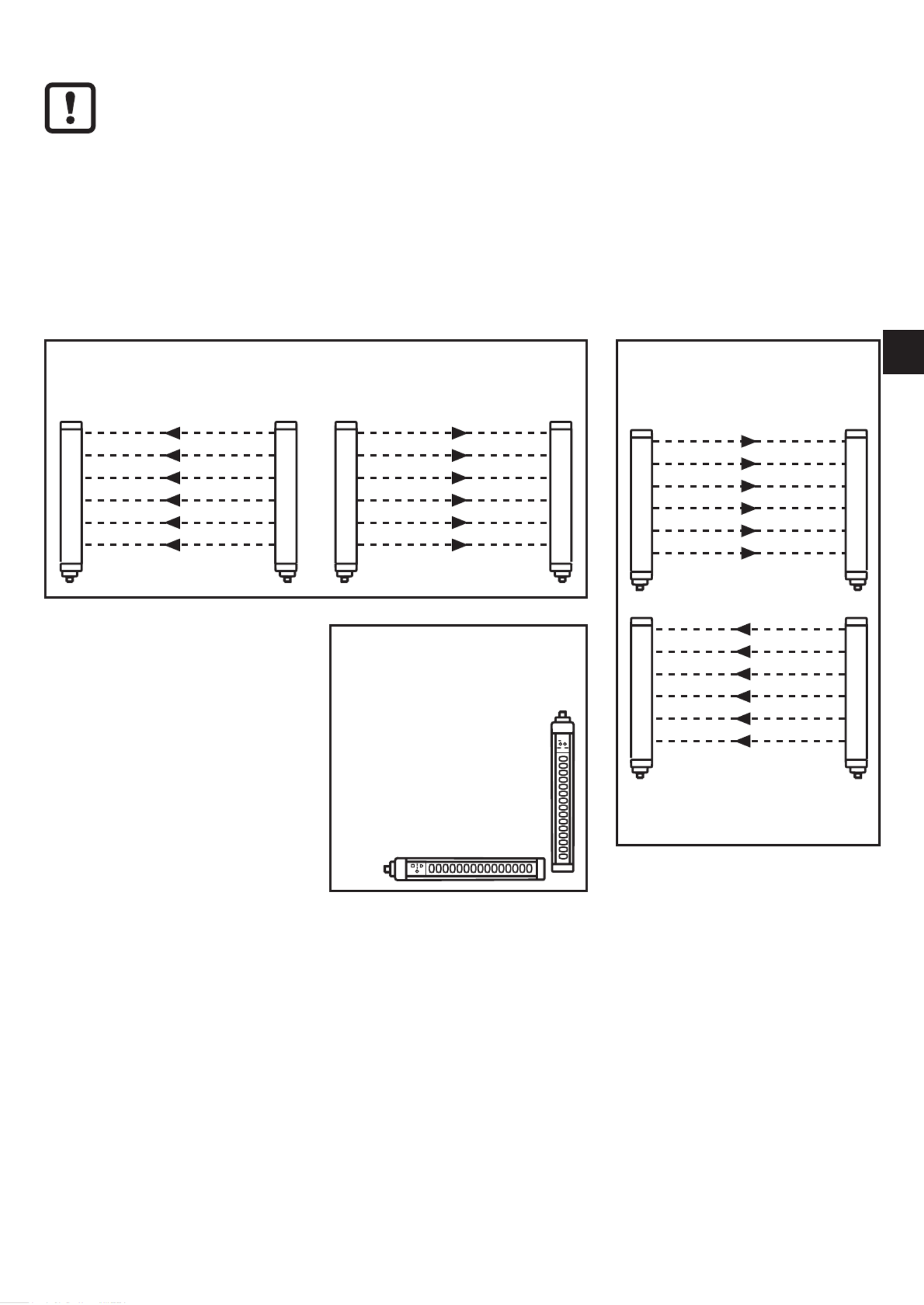
17
UK
6.7 Multiple systems
The use of several safety light curtains / safety light grids can lead to
malfunction and disable the protective function.
The safety light curtains / safety light grids are to be installed so that the beam
sent by the transmitter of a system can only be detected by the respective
receiver.
The following important rules for installation are to be observed to avoid mutual
interference of several systems:
Arrangement A Arrangement B
R1 T1 T2 R2 T1 R1
Possible arrangements:
A: Position of both transmitters
next to each other
B: Position transmitter 1 and
receiver 2 on top of each other
C: Combination in "L" shape
Arrangement C
R1
R2 T2
T2 T = transmitter; R = receiver
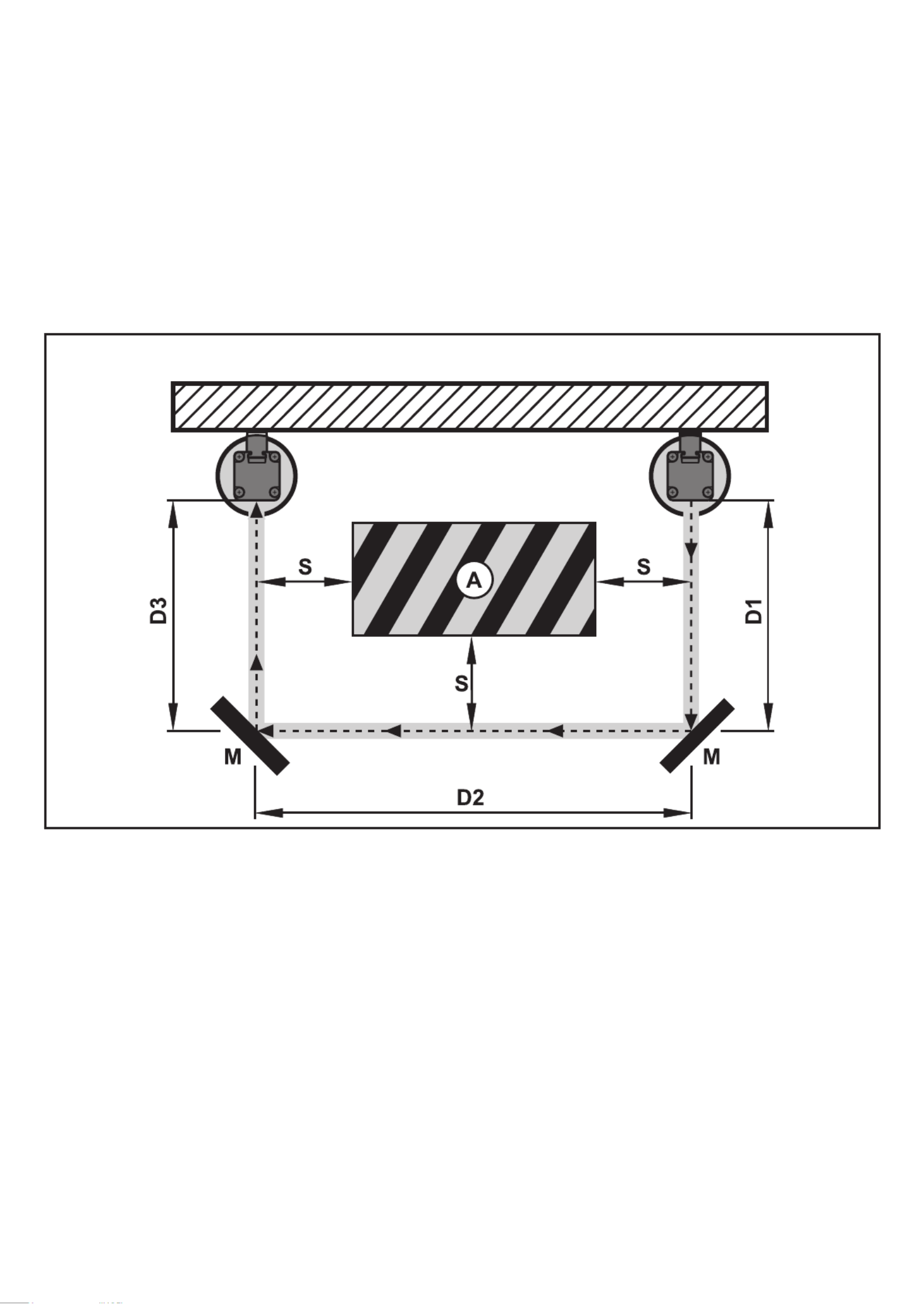
18
6.8 Use of corner mirrors
To protect and monitor hazardous areas with access from several sides one or
several corner mirrors can be used (available as accessory). By using mirrors the
light beam emitted by the transmitter can be sent via several access sides.
►To obtain a reflection angle of 90° the mirrors are to be oriented in an angle of
inclination of 45°.
The following image shows an application where U-shaped access protection is
implemented using two mirrors.
receiver transmitter (R) (T)
A = hazardous area
M = corner mirror
S = minimum safety distance
Dx = side length
►Install the corner mirrors so that the minimum safety distance (S) is adhered to
at each side of the hazardous area.
►During installation make sure that the reflecting area is plane and that no
vibrations affect the safety device.
• The range is the sum of the length of all sides (D1 + D2 + D3) of the access to
the protected area. The maximum range of the photoelectric safety sensors is
reduced by 15% for each mirror.
• Do not use more than three mirrors.
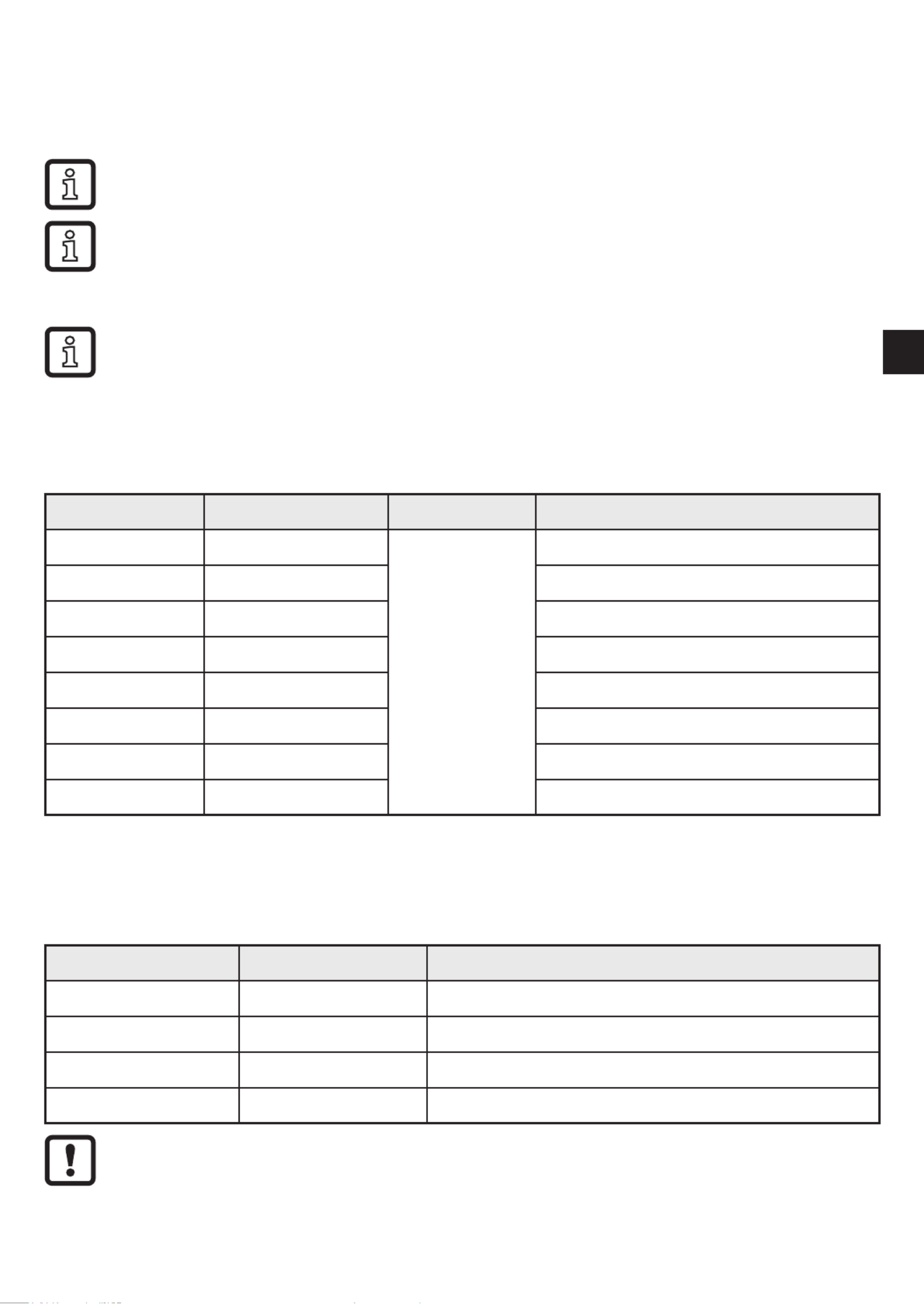
19
UK
7 Electrical connection
►
Disconnect power. Also disconnect any independently supplied relay load
circuits.
The nominal voltage is 24 V DC. This voltage may vary between 19.2 V and
28.8 V.
In case of a single fault the operating voltage must not exceed a maximum
of 28.8 V DC. Therefore a safe separation between current supply and
transformer is necessary.
To guarantee functional reliability an output capacity of min. 2000 µF / A has
to be ensured if a power supply with diode bridge is used.
►Connect the units as indicated in the following tables:
7.1 Wiring diagram transmitter
Core colours Name Type Description
brown L+ (24 V DC)
Input
Operating voltage
white Range 0 Configuration protected area width
blue L- (0 V DC) Operating voltage
green Range 1 Configuration protected area width
grey FE Functional earth
red 24 V AC / DC Heating 24 V AC / DC
yellow 0 V DC Heating 0 V DC
pink n.c. not connected
The protected area width (range) to be used is configured via range 0 and
range 1.
Configuration protected area width (range)
Range 0 Range 1 Description
24 V 0 V Selection range low (0...7 m)
0 V 24 V Selection range high (3...15 m)
0 V 0 V Transmitter in test function (→ 8.4 Test function)
24 V 24 V No function, configuration error
For proper function of the safety light curtains the white and green cores
of the transmitter have to be connected according to the indications in the
above table.
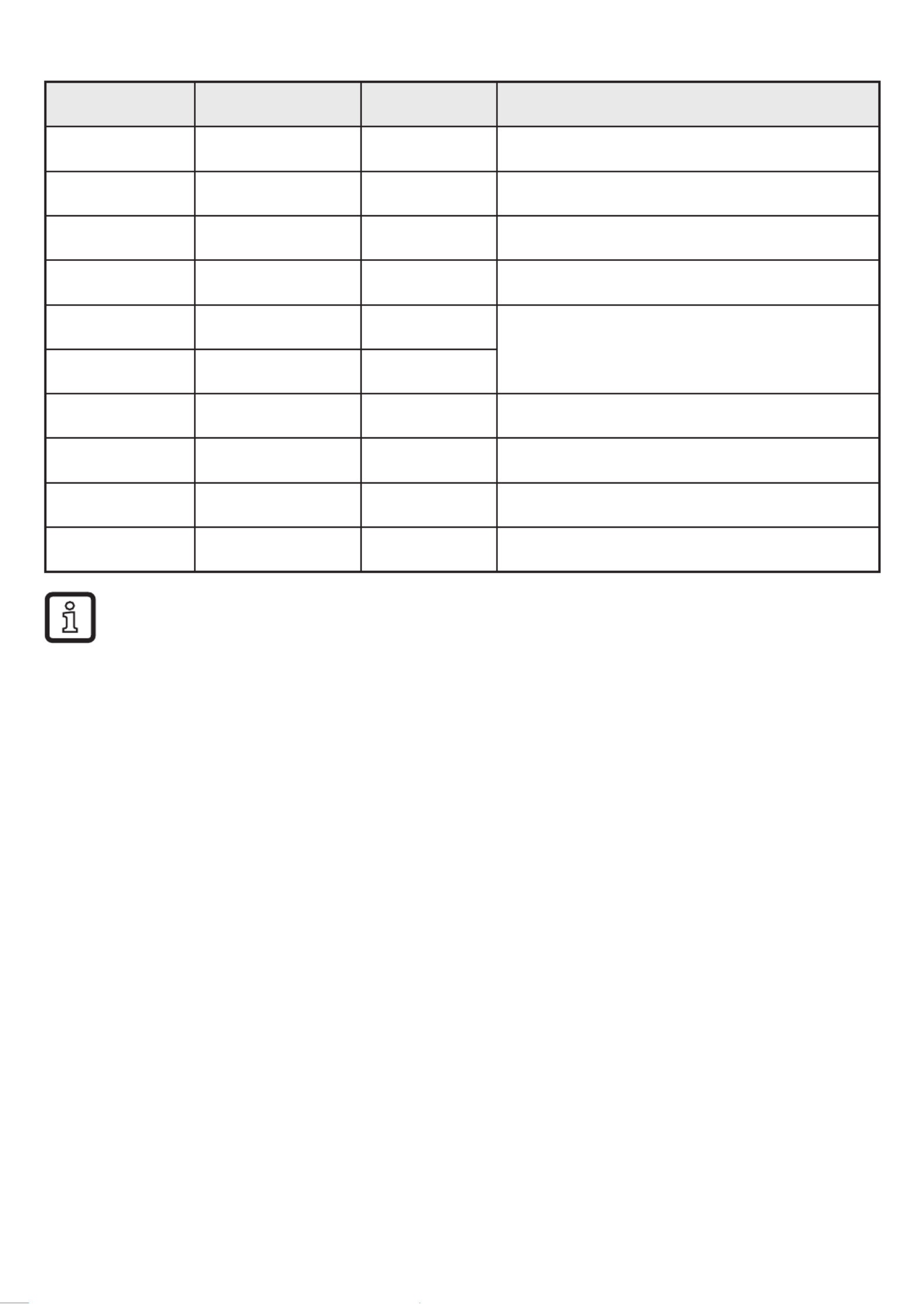
20
7.2 Wiring diagram receiver
Core colours Name Type Description
white OSSD1 Output Static safety-related output 1
brown 24 V DC – Operating voltage 24 V DC
green OSSD2 Output Static safety-related output 2
yellow K1_K2/Restart Input External feedback contacts
grey SEL_A Input Safety light curtains operating mode
pink SEL_B Input
blue 0 V DC – Operating voltage 0 V DC
red FE – Functional earth
violet 24 V AC / DC – Heating 24 V AC / DC
black 0 V DC – Heating 0 V DC
Note: Lay the cables of the photoelectric safety sensors separately from
sources of interference such as power lines.
►Connect the transmitter and the receiver to the functional earth.
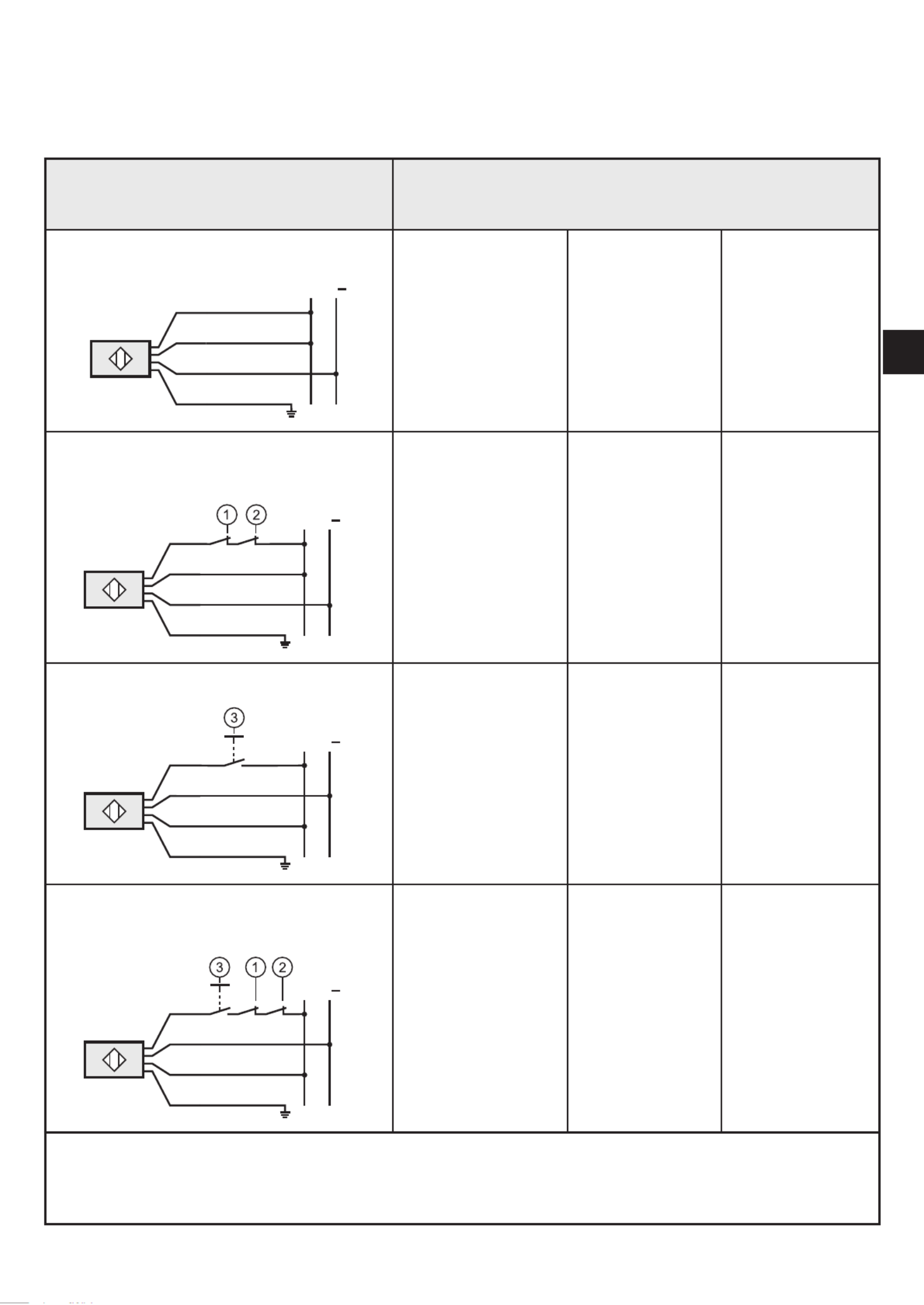
21
UK
8 Operating modes
The different operating modes of the safety light curtains / light grids of the
OY4xxS series can be set via the respective connections to the receiver.
Operating modes Connections
yellow grey pink
AAutomatic K1_K2
Connection to:
L+ (24 V DC)
SEL_A
Connection to:
L+ (24 V DC)
SEL_B
Connection to:
L- (0 V DC)
PK
YE
RD
GY
L+
L
BAutomatic with monitoring of the
feedback contacts
K1_K2
Connection to:
L+ (24 V DC)
(via NC of
the feedback
contacts)
SEL_A
Connection to:
L+ (24 V DC)
SEL_B
Connection to:
L- (0 V DC)
PK
YE
RD
GY
L+
L
CManual K1_K2 /restart
Connection to:
L+ (24 V DC)
(via start button)
SEL_A
Connection to:
L- (0 V DC)
SEL_B
Connection to:
L+ (24 V DC)
GY
YE
RD
PK
L+
L
DManually with monitoring of the
feedback contacts
K1_K2 /restart
Connection to:
L+ (24 V DC)
(via start button
and NC of
the feedback
contacts)
SEL_A
Connection to:
L- (0 V DC)
SEL_B
Connection to:
L+ (24 V DC)
GY
YE
RD
PK
L+
L
1: Feedback contact 1
2: Feedback contact 2
3: Restart
Core colours:
YE (yellow), GY (grey), PK (pink), RD (red)
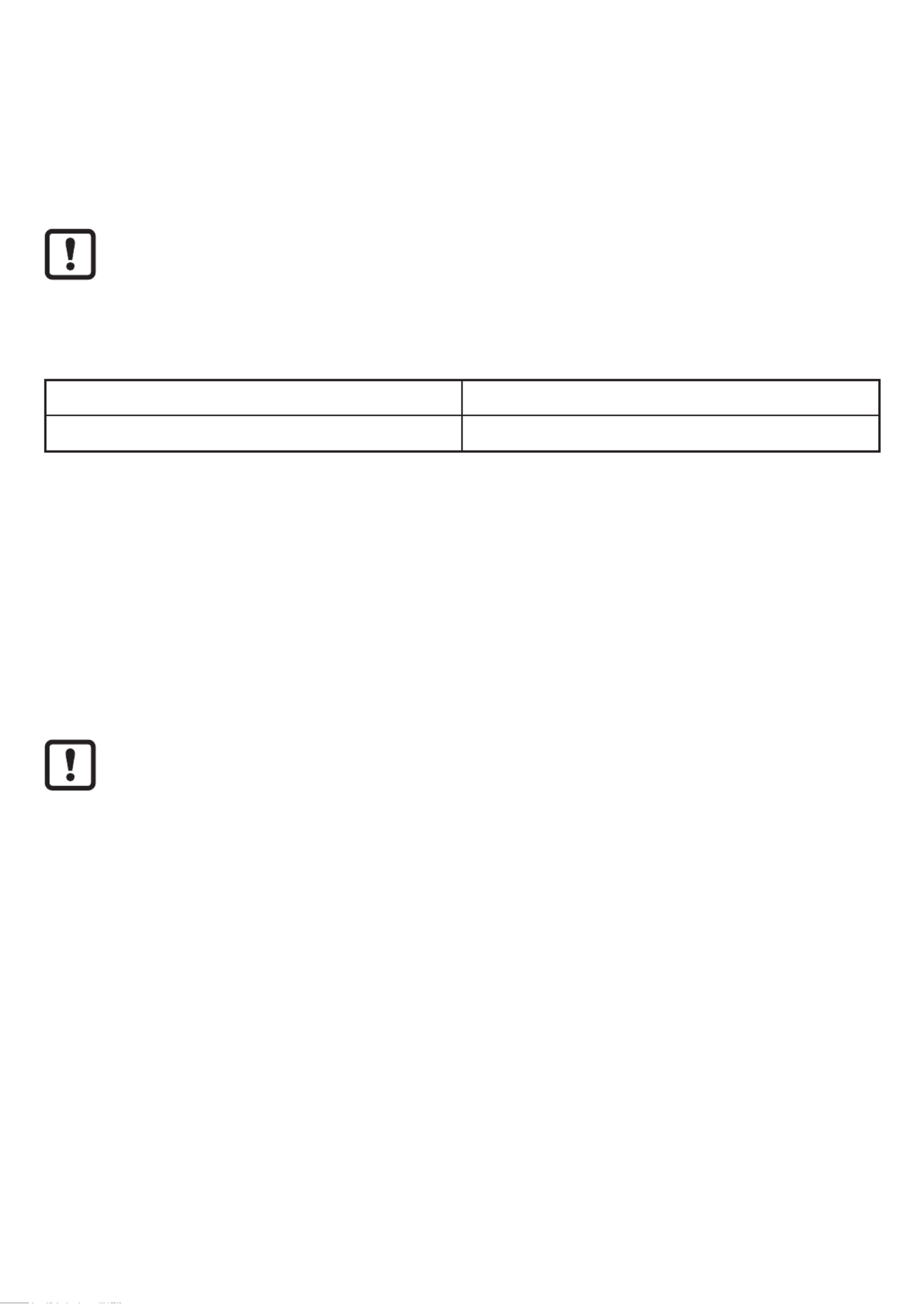
22
8.1 Automatic operation
If the safety light curtains / light grids are used in the automatic mode, monitored
start is not possible.
The safety light curtains / light grids automatically return to operation with clear
protected area, the outputs (OSSDs) are activated.
Verify if this is compatible with the risk analysis of your machine.
In the automatic mode the OSSD1 and OSSD2 outputs follow the status of the
safety light curtains / light grids :
Protected area clear Outputs = active logic "1"
Protected area interrupted Outputs = deactivated logic "0"
8.2 Manual operation
Operation in the manual mode (Start / Restart) is always necessary when passage
to a hazardous area is to be monitored (persons can be present in the hazardous
area after accessing the protected area without being detected).
The start / restart button has to be outside the hazardous area. It has to be
installed so that the hazardous area and access can be clearly seen. It must not
be possible to activate the start / restart button from within the hazardous area.
In the manual mode the safety light curtains / safety light grids comply
with the function as "trip device" to IEC 61496. Non-compliance with this
standard can lead to a hazard for people.
The OSSD1 and OSSD2 safety outputs are activated when the protected area
is clear and the restart command is entered via a start button or via a respective
pulse on the K1_K2/Restart input.
If the safety light curtains / light grids are released by a person or an object, a
restart command (24 V on the K1_K2/Restart input) has to be released. Pulse
duration > 100 ms.
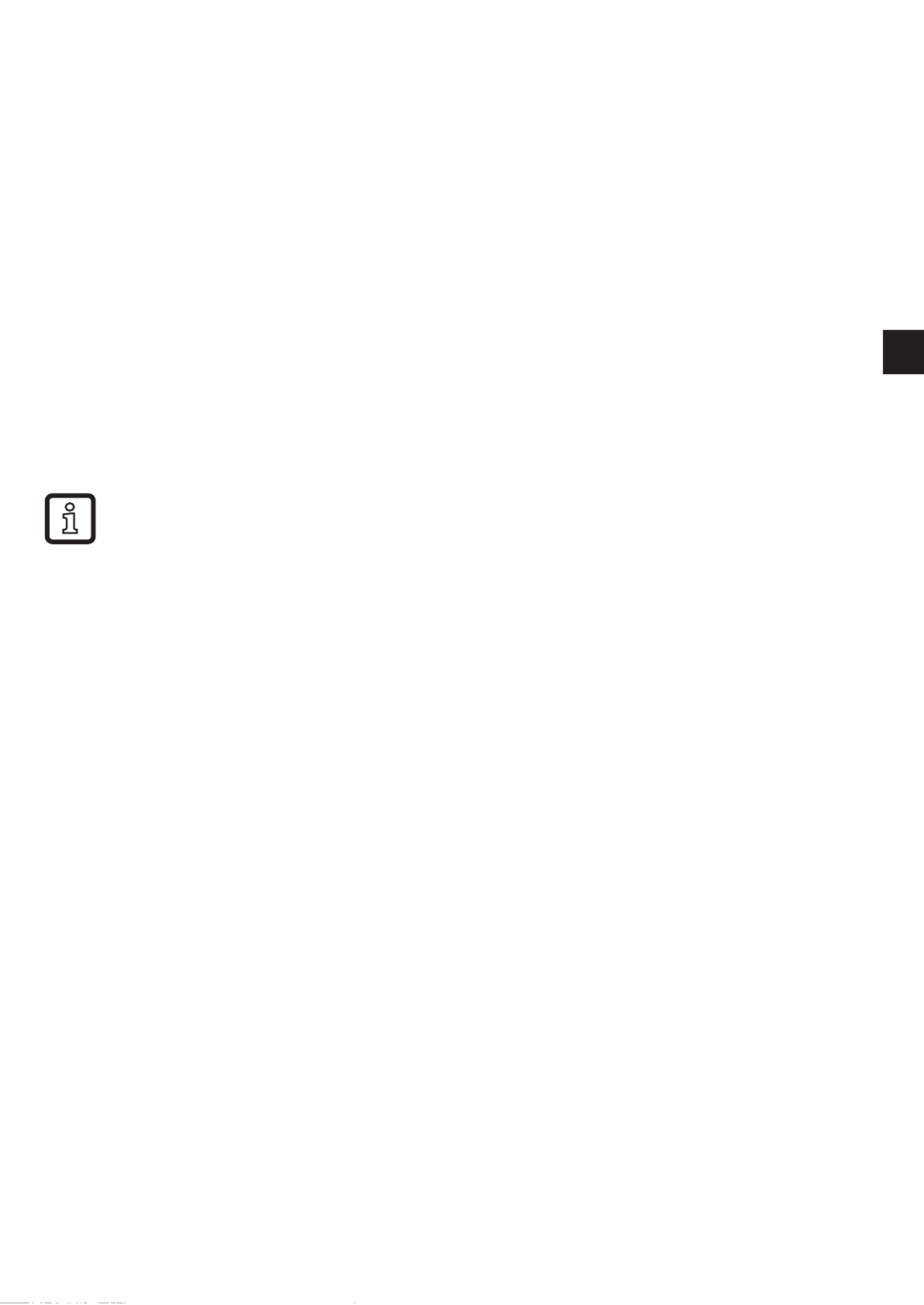
23
UK
8.3 Connection of external feedback contacts
External feedback contacts can be integrated in the automatic or manual
operating mode. The feedback contacts have to be connected in series between
the operating voltage and K1_K2 / Restart (→ 8 Operating modes / table, fig. B).
With manual function a start button has additionally to be switched in series
(→ 8 Operating modes / table, fig. D).
8.4 Test function
For the test function the photoelectric safety sensors can e.g. be tested by a
process control system or a control module (→ 7.1 Table Configuration protected
area width).
The test pulse interrupts the light emission by the transmitter and the outputs carry
a 0 signal (→ 10.1 Switching states of the outputs).
The minimum duration of the test command is 4 ms.
8.4.1 Internal test function
Type 4 safety light curtains / light grids continuously perform internal tests. The
faults are detected within the response time of the respective model leading to
switch-off (response times → 12 Technical data).
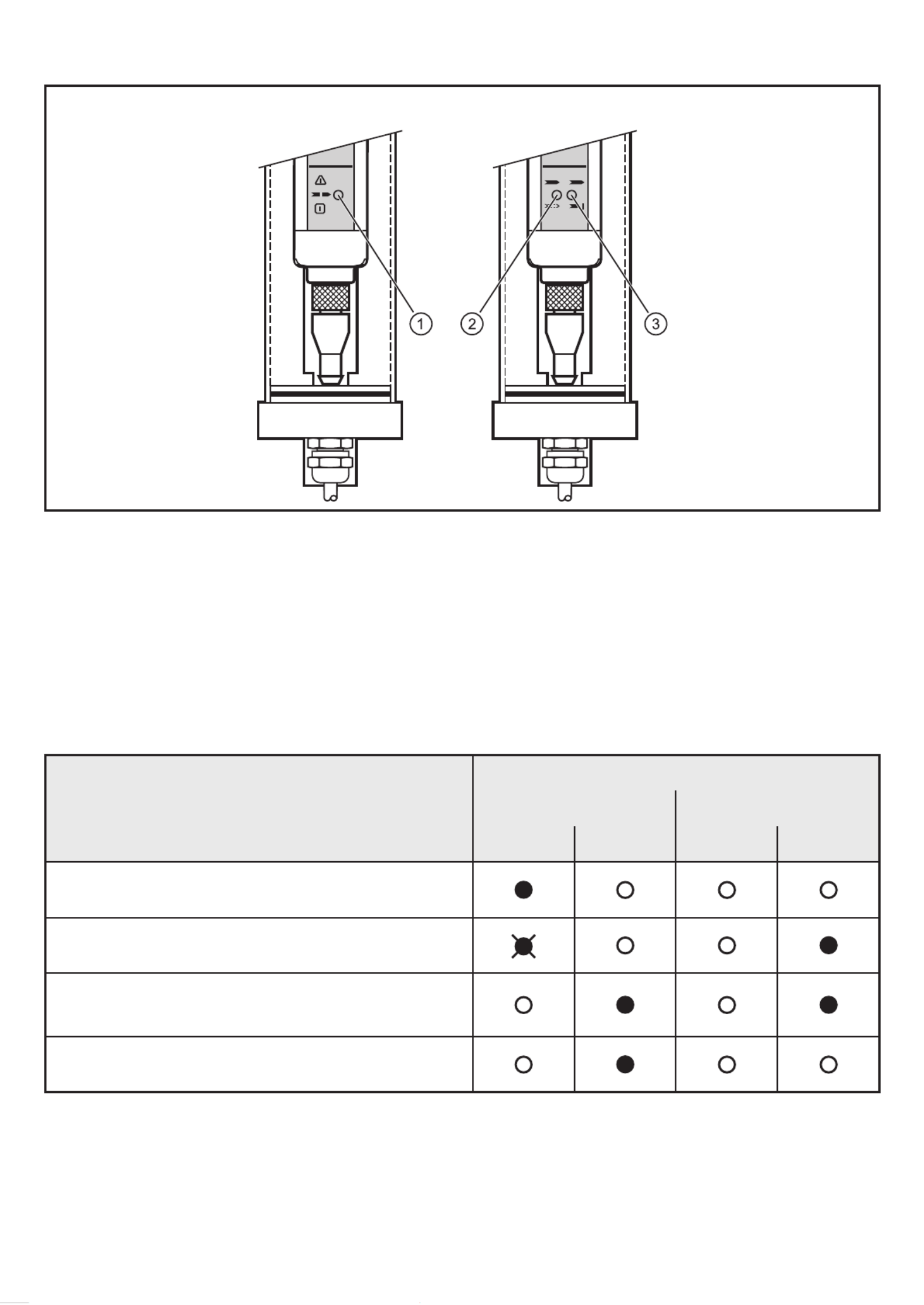
24
9 Operating and display elements
transmitter receiver
1: LED 3 colours (red/green/orange) 2: LED 2 colours (yellow/blue)
3: LED 2 colours (red/green)
9.1 LED indicators for optical alignment
The indication LEDs of the receiver help to correctly align the photoelectric safety
sensors.
9.1.1 Alignment in the automatic mode
Description
Receiver
2-colour LED 2-colour LED
red green yellow blue
Receiver does not detect any light beams
Receiver detects some light beams
Receiver detects all light beams with a weak
signal
Receiver detects all light beams
►Align the transmitter so that the green LED of the receiver lights.
►
Securely fasten the transmitter and the receiver.
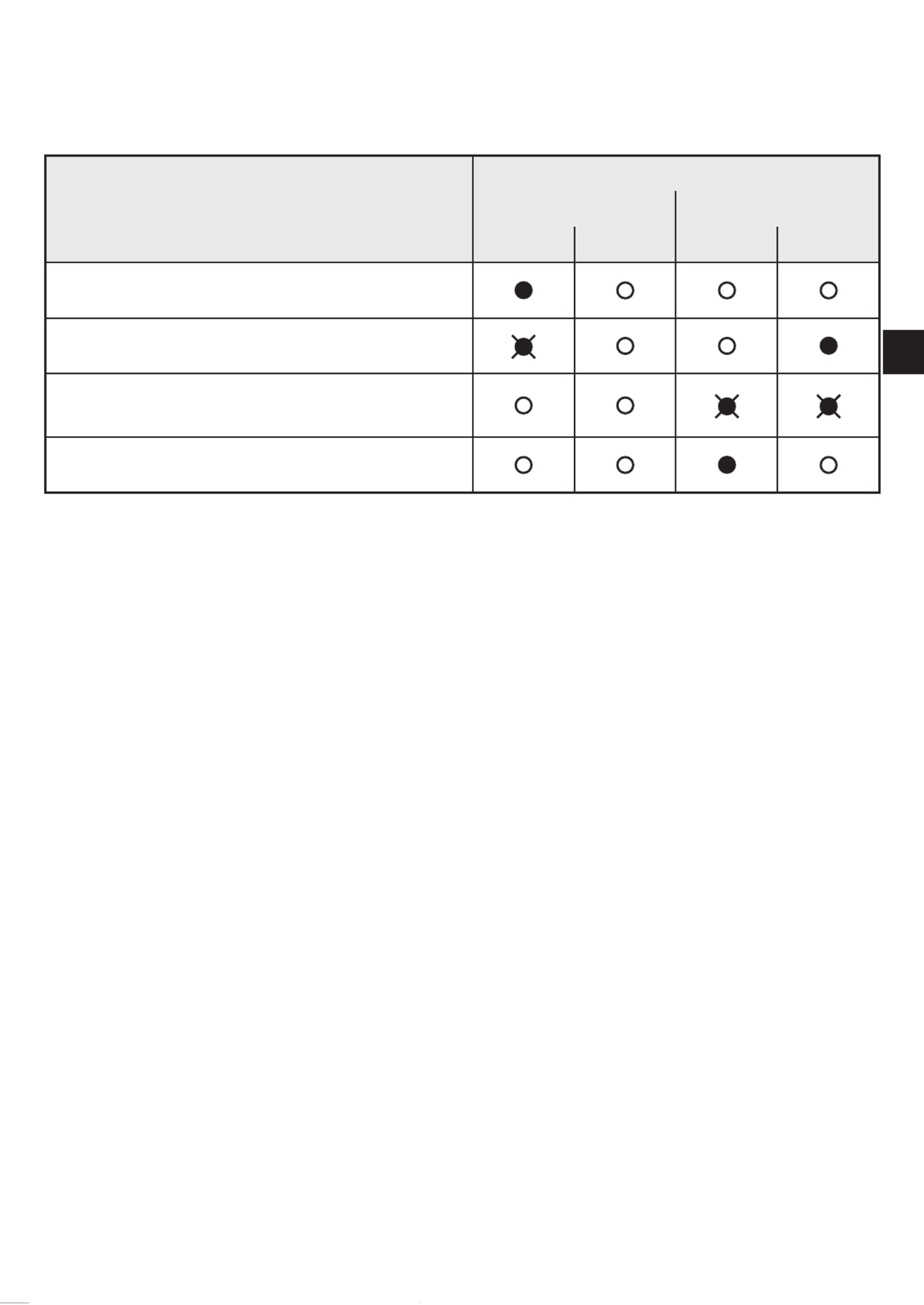
25
UK
9.1.2 Alignment in the manual mode
In the manual operating mode the yellow LED lights instead of the green one. The
light curtain / light grid will then wait for the manual release.
Description
Receiver
2-colour LED 2-colour LED
red green yellow blue
Receiver does not detect any light beams
Receiver detects some light beams
Receiver detects all light beams with a weak
signal
Receiver detects all light beams
►Align the transmitter so that the green LED of the receiver lights.
►
Securely fasten the transmitter and the receiver.
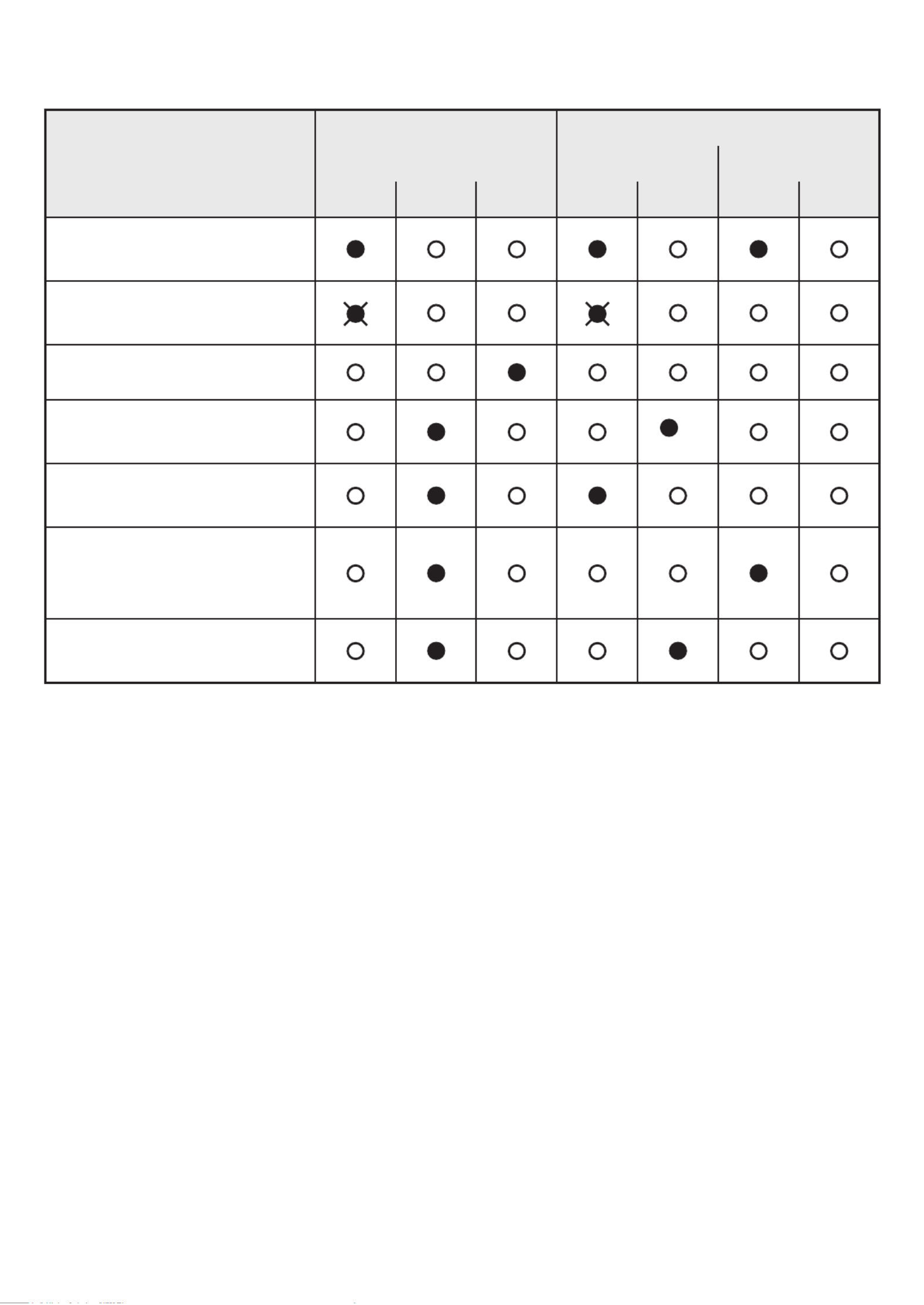
26
9.2 LED states
The blue LED is lit when the signal is weak (→ 9.1).
Description
Transmitter Receiver
LED LED LED
red green
orange
red green yellow blue
Activating the system,
input test
Fault
(→ 13 Troubleshooting)
Test condition
Normal operating
conditions *)
Protected area interrupted,
outputs deactivated
Protected area clear,
outputs deactivated,
waiting for restart
Protected area clear,
outputs activated
*) The green LED flashes twice when the system is switched on if the unit has been
configured with a high range.
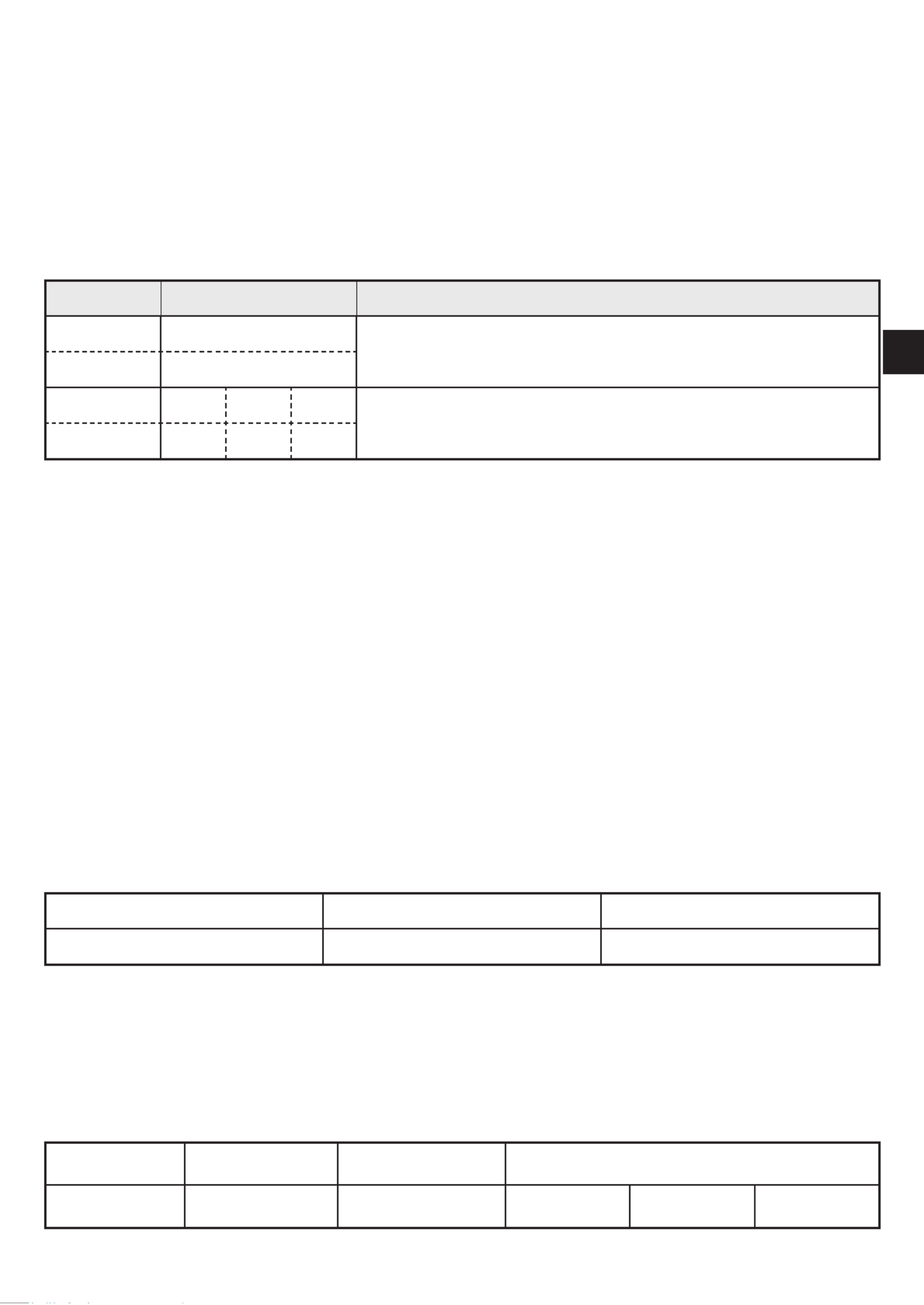
27
UK
10 Operation
10.1 Switching state of the outputs
The safety light curtains / light grids have two outputs (OSSDs) on the receiver;
the status depends on the condition of the protected area.
All short-circuits between the outputs or between an output and the current supply
(24 V DC or 0 V DC) are detected by the safety light curtains / light grids as a fault.
Output Binary states Description
OSSD1 1 Condition
protected area clear.
OSSD2 1
OSSD1 1 0 0 Condition
protected area interrupted or fault detected.
OSSD2 0 1 0
10.1.1 The safe state
The safe state is when the output is switched off (zero-current state: logic "0") of
min. one of the outputs (OSSDs).
If one of the outputs is switched off, the subsequent safety-related logic unit must
bring the complete system into the state defined as safe.
10.1.2 The switched state
In switched state the receiver provides a current of 24 V DC (logic "1") to both
outputs.
Output characteristics
The output characteristics follow the characteristics of the input according to
IEC 61496:
Logic "1" 24 V DC max. 400 mA
Logic "0" < 0.2 mA≤ 1.5 V DC
10.1.3 Interface classification
The interface of the devices complies with interface type C class 3 according to
the ZVEI position paper CB 24I Ed. 2.0
Identification key
Interface type Suitable interface type
Source C3 Receiver C1 C2 C3
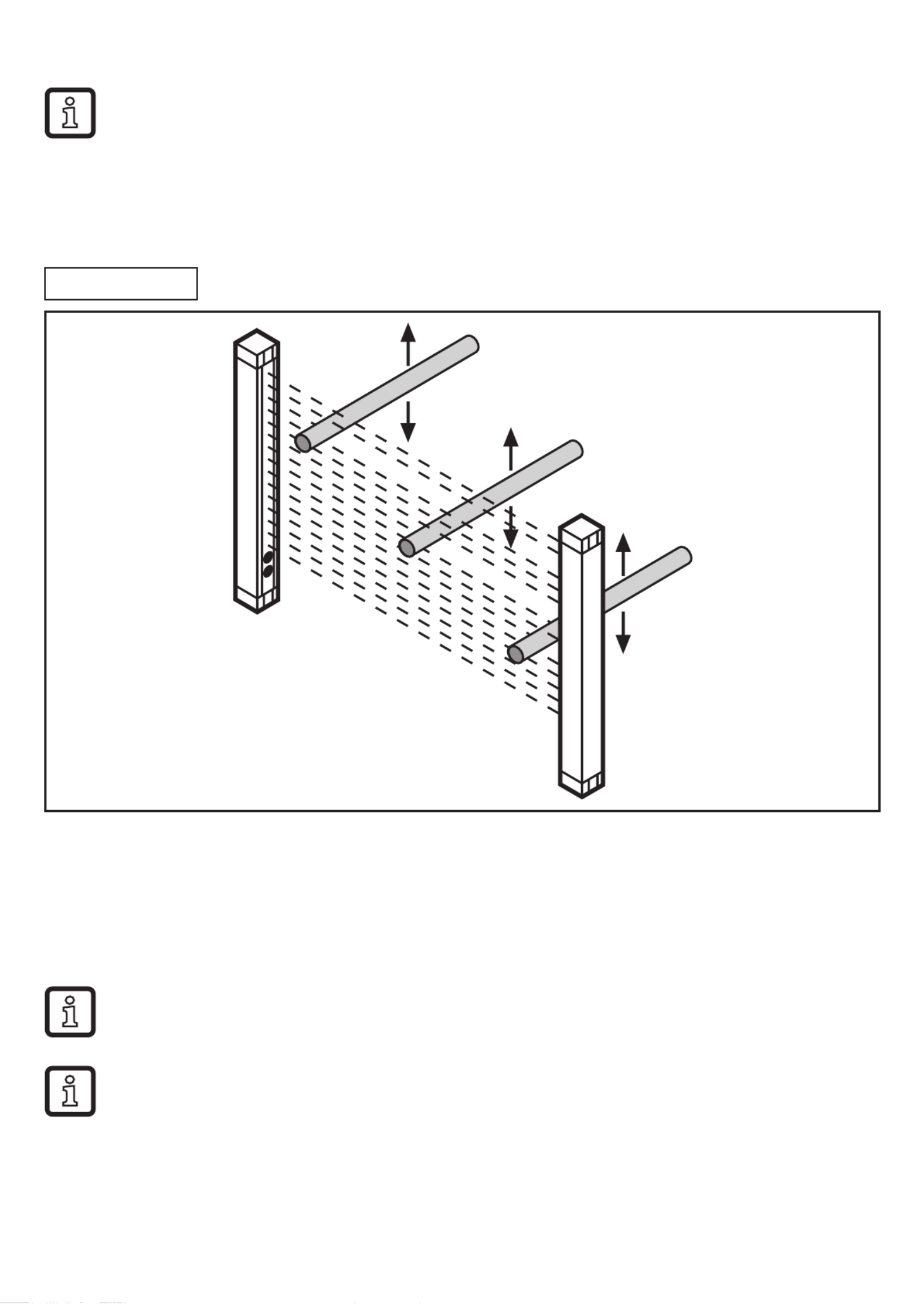
28
10.2 Functional test of the safety light curtains
Check the proper function of the safety light curtains before work starts.
For the functional test a test object in accordance with a resolution of the safety
light curtains has to be used.
For information about available test rods see:
www.ifm.com → Products → Accessories.
►Let the test object enter the protected area and move it slightly downwards.
First of all in the centre and then close to the transmitter and the receiver.
►Make sure that the red LED on the receiver is continuously lit during the
movement in the protected area.
Observe the notes on installation of the safety light curtains → 14
Maintenance, repair and disposal.
Notes on setup → 17.1 Check list.
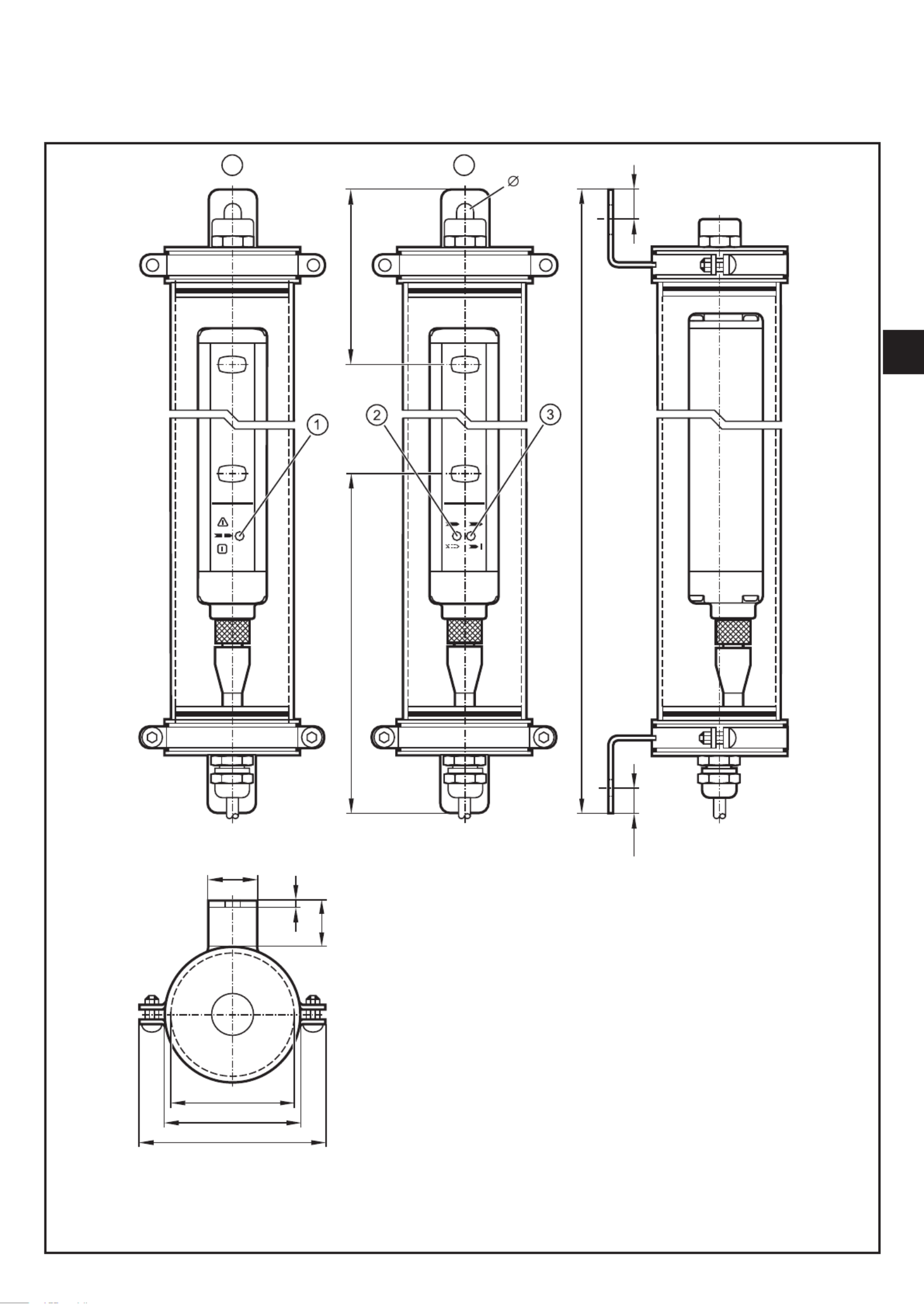
29
UK
11 Scale drawing
11.1 Safety light curtain
R
137 66
7
T
L
10,5 12
50
20
2
18
56
76
T:
R:
L:
transmitter
receiver
total length*
1: LED 3 colours (red/green/orange)
2: LED (yellow)
3: LED 2 colours (red/green)
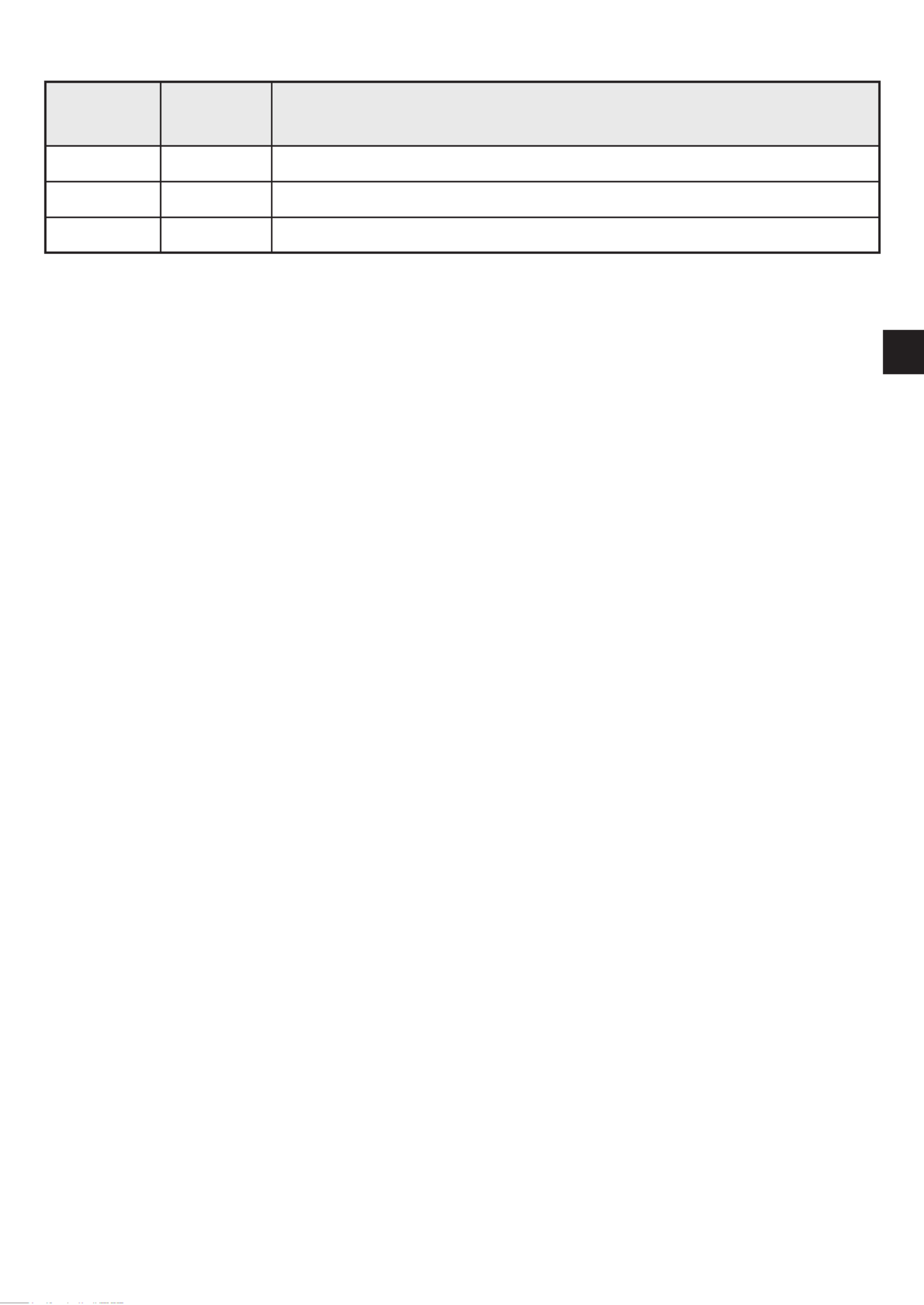
31
UK
11.2.1 Position of the light beams
Model Beams Position of the light beams measured from the lower edge of
the protective tube [mm]
OY421S 2 177 - 677
OY422S 3 177 - 577 - 977
OY423S 4 177 - 477 - 777 - 1077
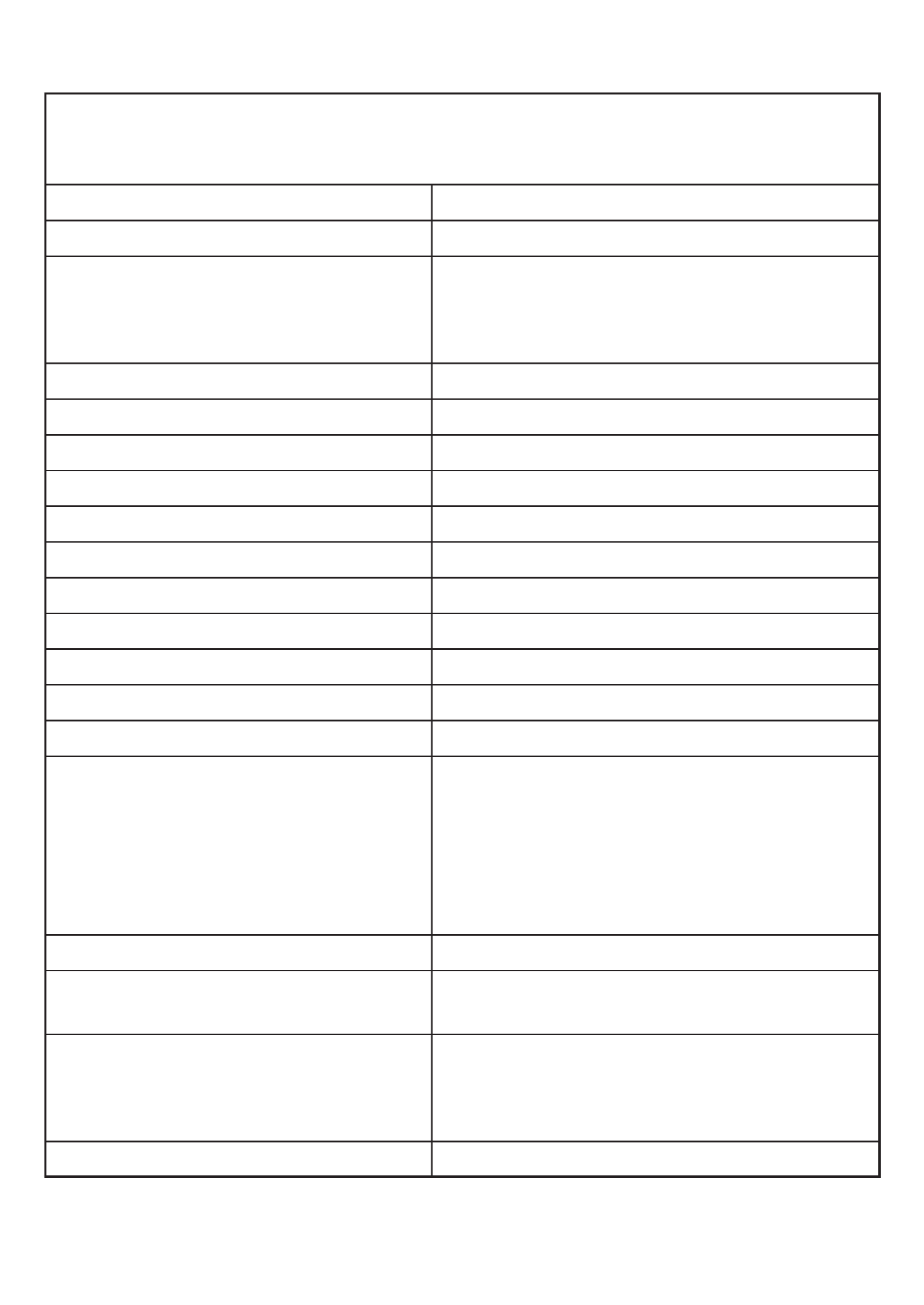
32
12 Technical Data
Conforms to the requirements of:
Type 4 IEC 61496-1, SIL 3 IEC 61508, SILcl 3 IEC 62061,
ISO 13849-1:2015 category 4 PL e
Electrical design DC / PNP
Operating voltage 24 DC (19.2…28.8)
Current consumption
Transmitter [mA] 42
Receiver [mA] 83
Outputs (OSSDs) 2 x PNP
Max. current load per output [mA] 400 (24 V)
Max. capacitive load CL_max [µF] 0.82
Power-on delay time [s] < 2
Mission time TM [h] 175200
EMC IEC 61496-1
Vibration IEC 61496-1
Shock IEC 61496-1
Ambient temperature [°C] -10…55
Max. perm relative air humidity [%] 95
Protection IP 65 / IP 67 / IP 69K / III
Housing material
Transparent protective tube PMMA
Protective cap POM
Clamp High-grade stainless steel (316L/1.4404)
Sealing ring Silicone
Type of light Infrared light 950 nm
Display LED yellow, LED green, LED red, LED blue,
LED orange
Connection
Transmitter PVC cable / 15 m / 8 x 0.34 mm²
Receiver PVC cable / 15 m / 10 x 0.34 mm²
Max. cable length [m] 100 *)
*) for wire cross-section 0.34 mm²
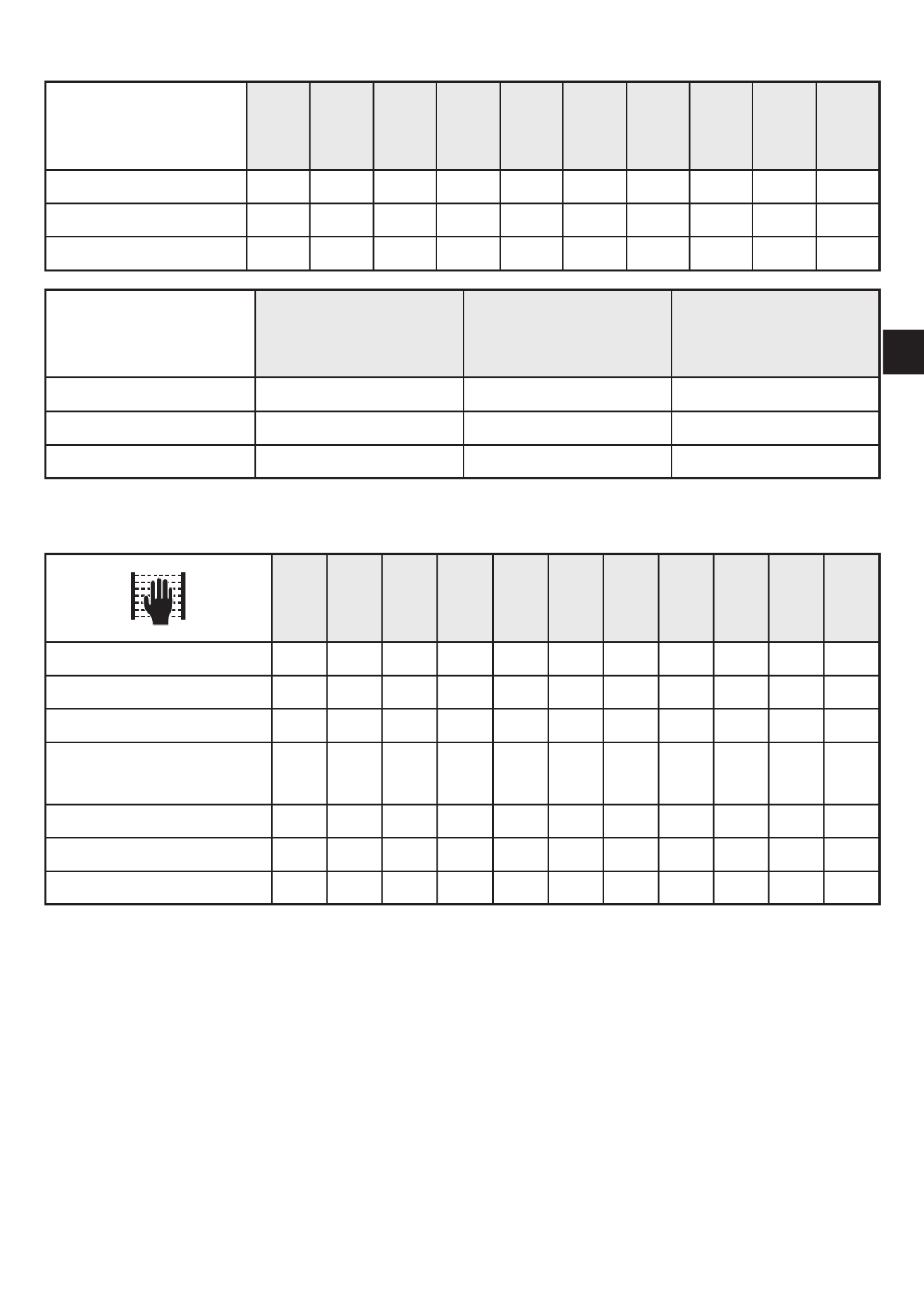
33
UK
12.1 Heating
OY441S
OY442S
OY443S
OY444S
OY445S
OY446S
OY447S
OY448S
OY449S
OY450S
Current consumption
Transmitter [mA] 83 167 250 333 375 417 417 417 417 417
Receiver [mA] 83 167 250 333 375 417 417 417 417 417
OY421S OY422S OY423S
Current consumption
Transmitter [mA] 333 417 417
Receiver [mA] 333 417 417
12.2 Safety light curtains: 30 mm resolution
OY441S
OY442S
OY443S
OY444S
OY445S
OY446S
OY447S
OY448S
OY449S
OY450S
OY452S
Total length L [mm] 342 492 642 792 942 1092 1242 1392 1542 1692 1692
Protected area height [mm] 160 310 460 610 760 910 1060 1210 1360 1510 1510
Response time [ms] 3 4 5 6 6.5 7.5 8.5 9.5 10 11 11
Safety-related reliability
PFHD
[1/h] 9.2-09 1.0-08 1.2-08 1.3-08 1.4-08 1.5-08 1.7-08 1.8-08 1.9-08 2.0-08 2,0-08
Test pulse duration ti
[µs]
80 80 80 80 80 80 80 80 80 80 80
Test pulse interval T
[ms]
3,0 4,0 4,8 5,8 6,6 7,6 8,4 9,4 10,2 11,2 11,2
Ratio ti / T
[%]
2,7 2,0 1,7 1,4 1,2 1,1 1,0 0,9 0,8 0,7 0,7
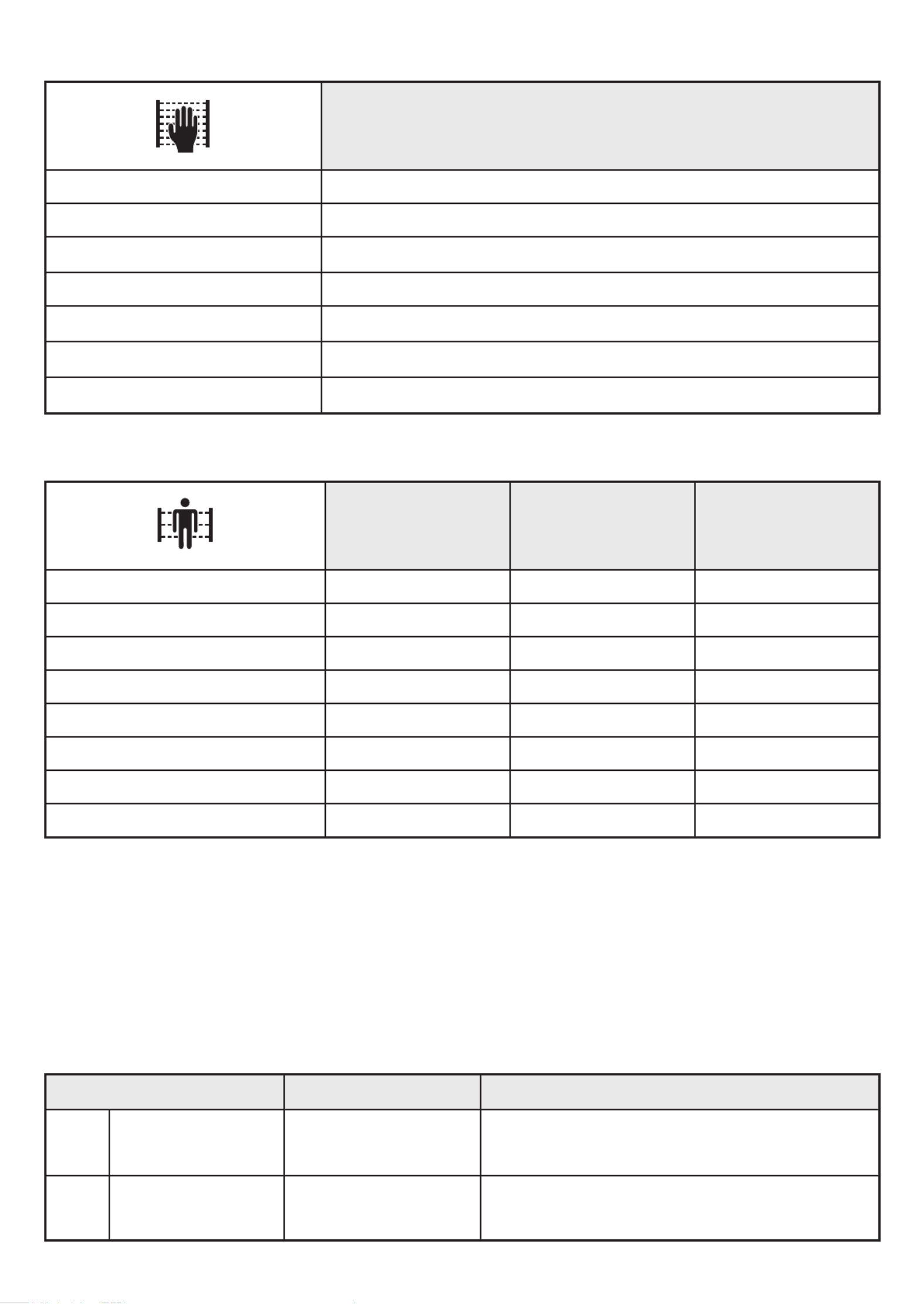
34
12.3 Safety light curtains: 40 mm resolution
OY451S
Total length L [mm] 1842
Protected area height [mm] 1660
Response time [ms] 14
Safety-related reliability
PFHD
[1/h] 1,5-08
Test pulse duration ti
[µs]
80
Test pulse interval T
[ms]
8,8
Ratio ti / T
[%]
0,9
12.4 Safety light grids 2, 3 and 4 beams
OY421S
OY422S
OY423S
Number of beams 2 3 4
Total length L [mm] 782 1082 1182
Protected area height [mm] 510 810 910
Response time [ms] 2.5 2.5 2.5
Safety-related reliability
PFHD
[1/h] 9.2-09 1.0-08 1.1-08
Test pulse duration ti
[µs]
80 80 80
Test pulse interval T
[ms]
2,3 2,4 2,5
Ratio ti / T
[%]
3,5 3,3 3,2
13 Troubleshooting
The LEDs of the transmitter and the receiver indicate faulty operating states
(→ 9 Operating and display elements). For a detailed fault description see the
following tables.
13.1 Fault diagnosis transmitter
LED Possible cause Troubleshooting
red 2 consecutive
pulses
Faulty connection Check the white and green cores.
red 3/4 consecutive
pulses
Internal fault Send device to ifm branch office for repair.
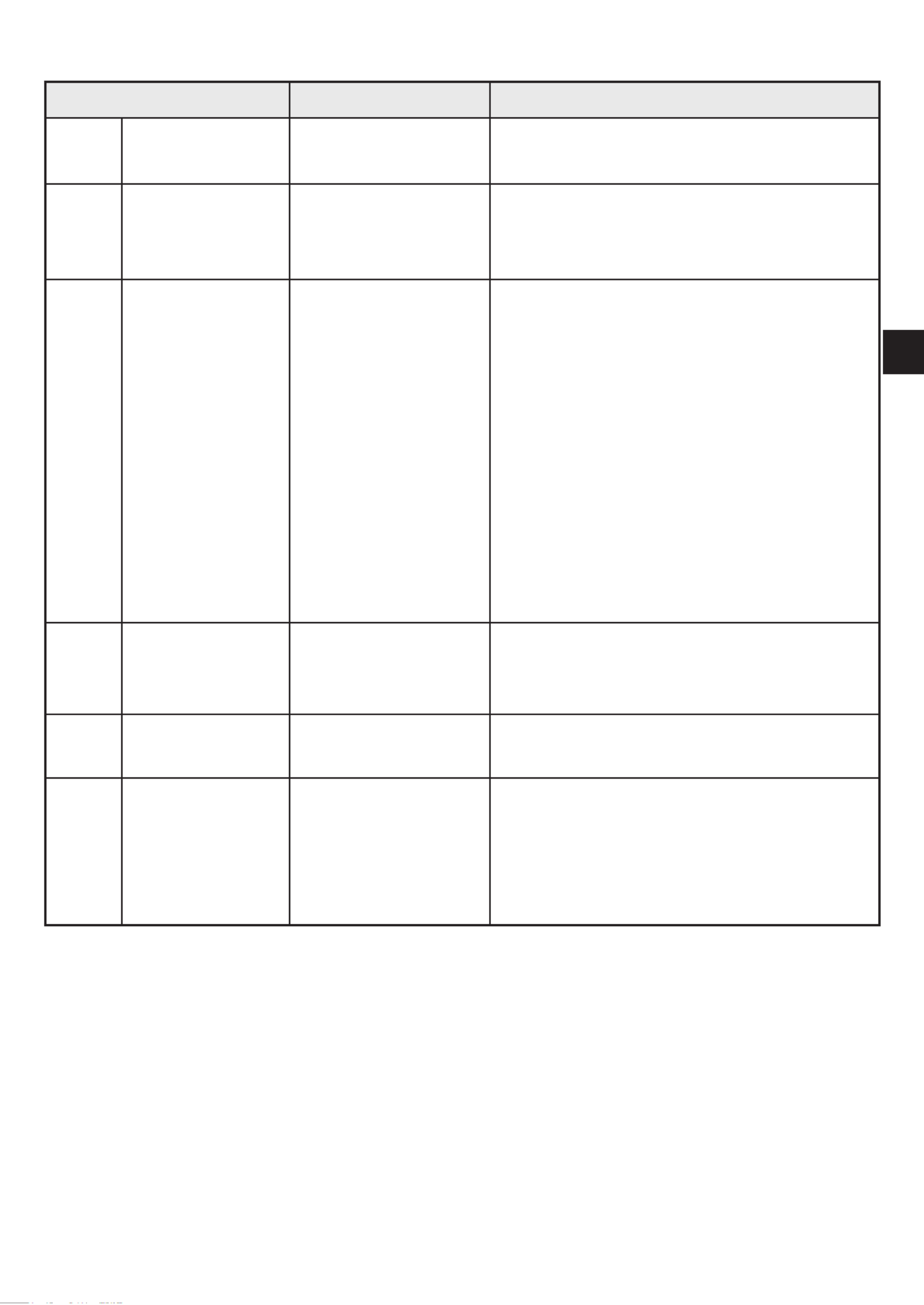
35
UK
13.2 Fault diagnosis receiver
LED Possible cause Troubleshooting
red 2 consecutive
pulses
Wrong configuration Check connections.
red 3 consecutive
pulses
Feedback external
contactor missing
Check the connection to the external
feedback contacts.
red 4 consecutive
pulses
Interfering
transmitter detected
Find interfering transmitter and take one
of the following measures:
- Reduce the range of the interfering
transmitter from high to low.
- Exchange position of transmitter and
receiver.
- Change location of the interfering
transmitter so that the receiver is not
influenced.
- Screen the beams coming from the
interfering transmitter using a mat
protective device.
red 5 consecutive
pulses
Fault
OSSD outputs
Check connections.
If the defect remains, send device to ifm
branch for repair.
red 6/7 consecutive
pulses
Internal fault Send device to ifm branch office for
repair.
yellow Weak signal - Check alignment of transmitter and
receiver.
- Clean protective tube, check range.
- Waiting for restart pulse.
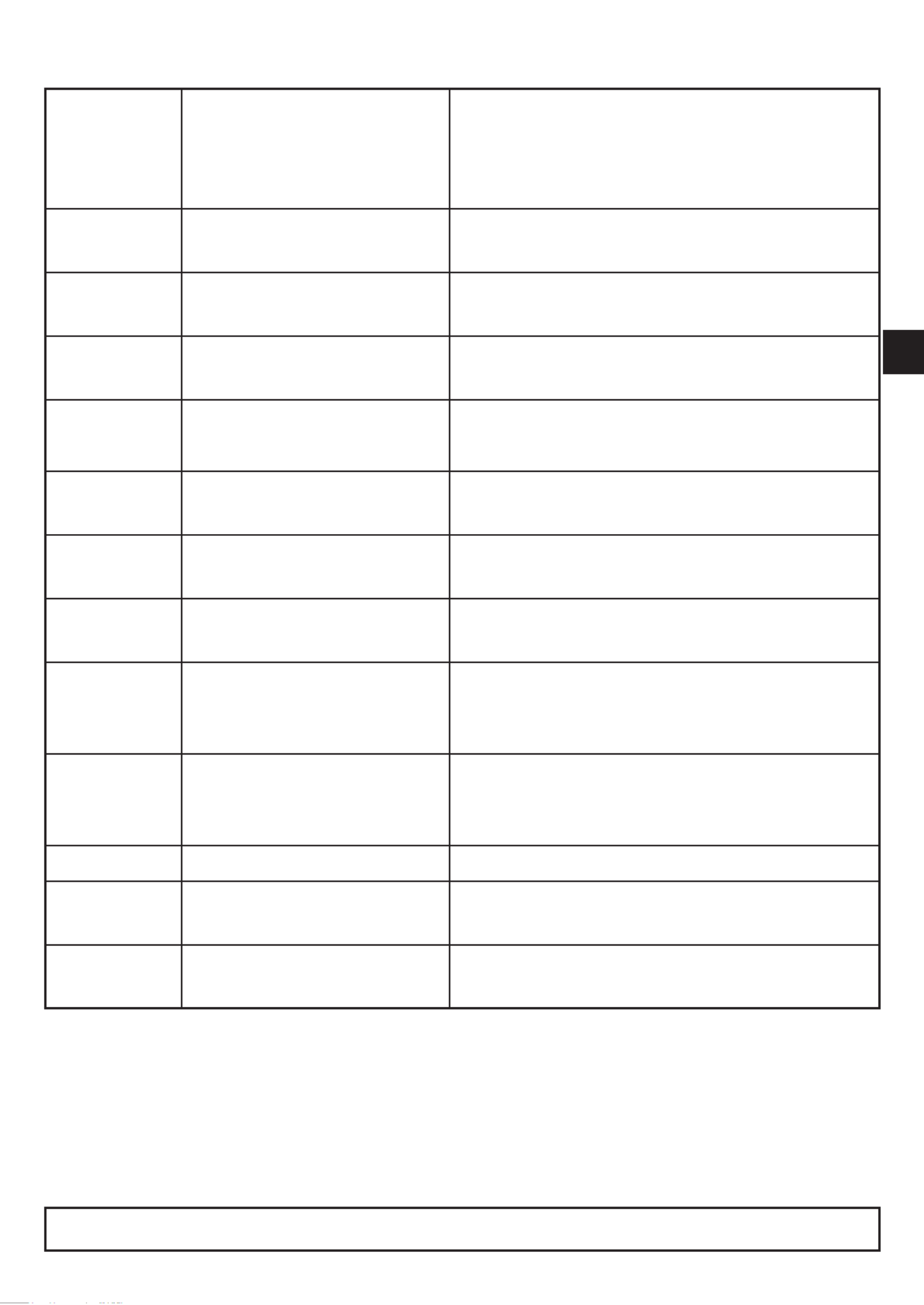
37
UK
15 Terms and abbreviations
Blanking Optional function ensuring that objects are
in the protected area which are larger than
the detection capacity without the OSSDs
switching off.
ESPE Electro-Sensitive Protective
Equipment
CCF Common Cause Failure
DCavg Average Diagnostic
Coverage
Muting Temporary bridging of a safety function by
safety-related parts of the control system.
MTTFdMean Time To Dangerous
Failure
OSSD Output Signal Switching
Device
Static safety-related output.
PFH
(PFHD)
Probability of (dangerous)
Failure per Hour
PL Performance Level Capability of safety-related parts to perform
a safety function at predictable conditions to
fulfil the expected risk reduction.
SIL Safety Integrity Level SIL 1-4 to IEC 61508. The higher the SIL the
lower the probability that a safety function
will fail.
SILcl Safety Integrity Levelclaim limit (to IEC 62061)
TMMission Time
T1 Test Interval
Technical data and further information at www.ifm.com
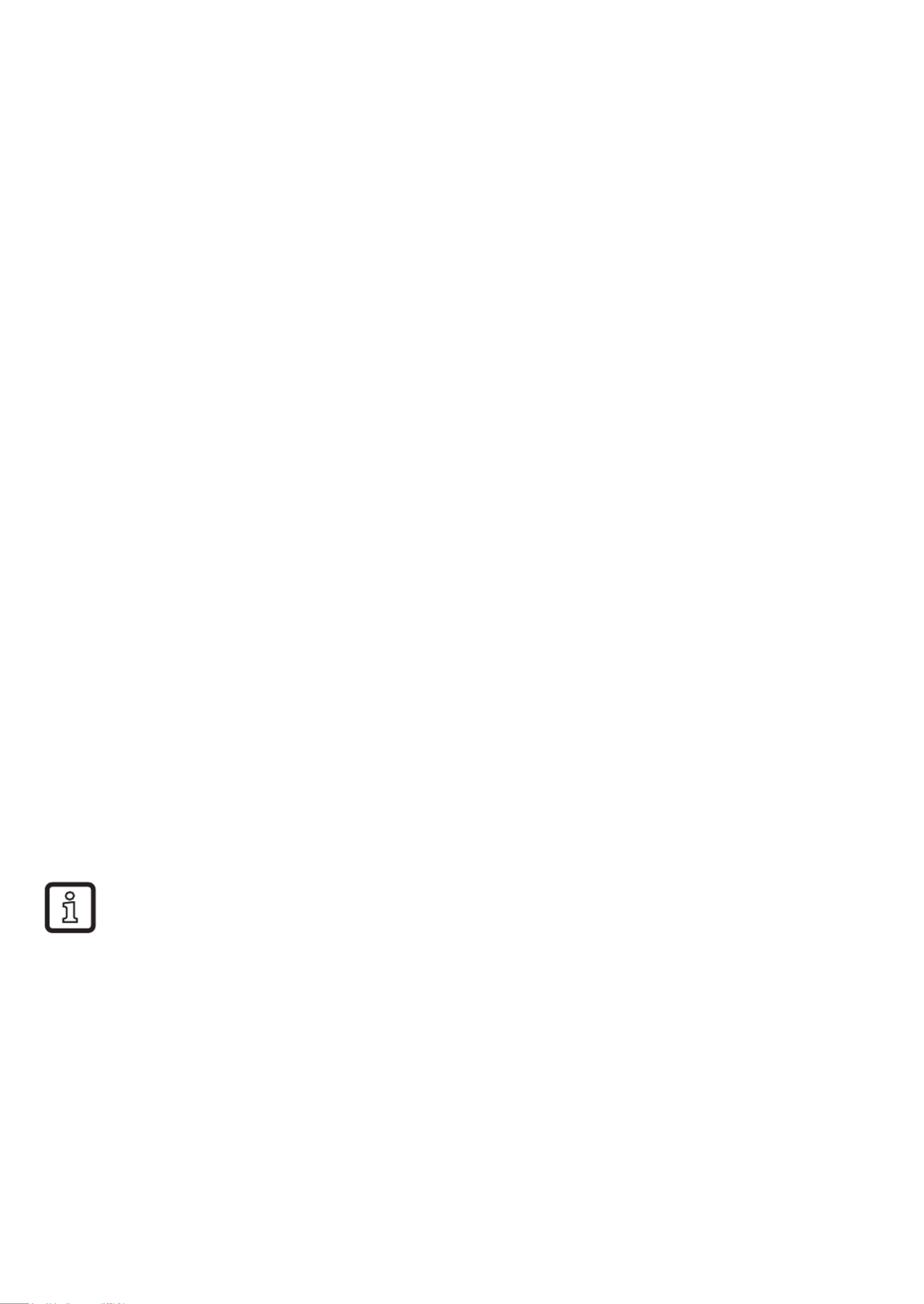
38
16 Annex
16.1 Check list
This check list serves as help for setting up the safety light curtains / light grids.
The requirements in this check list should to be met, however depending on the
application and the directives / standards referred to.
1. Were the directives / standards valid for safety of machinery complied with?
2. Is access prevention / primary guarding of the point of danger only possible
through the protected area of the safety light curtains / light grids?
3. Have steps been taken to prevent reaching under, over or around the light
guards to prevent attempts to defeat them?
4. Has the stop or shutdown delay of the machine been measured and adapted
according to the installation of the safety light curtains / light grids?
5. Have the safety light curtains / light grids been duly fixed and secured against
loosening or movement?
6. Have the safety light curtains / light grids been checked according to the
function and maintenance descriptions in these operating instructions?
7. Has external monitoring (EDM) of the control unit (e.g. contactor, valve etc.)
been used?
8. Is the state defined as safe for switching on / off of the safety light curtains /
light grids initiated?
9. Is /are there any soiling or scratches on the light-emitting surface?
10. Are the installation instructions of these operating instructions adhered to?
This check list does not replace checking or setup by a person trained in
safety matters.
Termékspecifikációk
Márka: | IFM |
Kategória: | nincs kategorizálva |
Modell: | OY446S |
Szüksége van segítségre?
Ha segítségre van szüksége IFM OY446S, tegyen fel kérdést alább, és más felhasználók válaszolnak Önnek
Útmutatók nincs kategorizálva IFM

23 Március 2025

23 Március 2025

18 Március 2025

18 Március 2025

18 Március 2025

18 Március 2025

16 Január 2025

16 Január 2025

16 Január 2025

14 Január 2025
Útmutatók nincs kategorizálva
- nincs kategorizálva Mestic
- nincs kategorizálva Ikea
- nincs kategorizálva Phoenix Gold
- nincs kategorizálva Samsung
- nincs kategorizálva BaByliss
- nincs kategorizálva Grace Design
- nincs kategorizálva PeakTech
- nincs kategorizálva Sony
- nincs kategorizálva August
- nincs kategorizálva Braun
- nincs kategorizálva Yamaha
- nincs kategorizálva National Geographic
- nincs kategorizálva Beko
- nincs kategorizálva Fujitsu
- nincs kategorizálva Hoshizaki
- nincs kategorizálva Microchip
- nincs kategorizálva Dometic
- nincs kategorizálva Electrolux
- nincs kategorizálva Acer
- nincs kategorizálva Moulinex
- nincs kategorizálva Sharkoon
- nincs kategorizálva Whirlpool
- nincs kategorizálva Nedis
- nincs kategorizálva Applico
- nincs kategorizálva Milwaukee
- nincs kategorizálva Amazfit
- nincs kategorizálva LG
- nincs kategorizálva Grundig
- nincs kategorizálva Ariston Thermo
- nincs kategorizálva Husqvarna
- nincs kategorizálva Dolmar
- nincs kategorizálva Realme
- nincs kategorizálva Tommee Tippee
- nincs kategorizálva Parkside
- nincs kategorizálva DeepCool
- nincs kategorizálva Peugeot
- nincs kategorizálva Maglite
- nincs kategorizálva Marantz
- nincs kategorizálva Candy
- nincs kategorizálva Gem Toys
- nincs kategorizálva Worx
- nincs kategorizálva Philips
- nincs kategorizálva Gorenje
- nincs kategorizálva Pioneer
- nincs kategorizálva Kärcher
- nincs kategorizálva Reolink
- nincs kategorizálva Olympus
- nincs kategorizálva Adler
- nincs kategorizálva Princess
- nincs kategorizálva Oregon Scientific
- nincs kategorizálva SilverCrest
- nincs kategorizálva Garmin
- nincs kategorizálva RCF
- nincs kategorizálva Bosch
- nincs kategorizálva Indesit
- nincs kategorizálva Nivona
- nincs kategorizálva TC Electronic
- nincs kategorizálva Singer
- nincs kategorizálva Honda
- nincs kategorizálva Theben
- nincs kategorizálva Panasonic
- nincs kategorizálva Canon
- nincs kategorizálva Zanussi
- nincs kategorizálva JVC
- nincs kategorizálva Lego
- nincs kategorizálva Conair
- nincs kategorizálva MPM
- nincs kategorizálva AEG
- nincs kategorizálva Doepke
- nincs kategorizálva Emerio
- nincs kategorizálva Volvo
- nincs kategorizálva StarTech.com
- nincs kategorizálva Ultimate Speed
- nincs kategorizálva Mega
- nincs kategorizálva Tunturi
- nincs kategorizálva Paidi
- nincs kategorizálva Sharp
- nincs kategorizálva Einhell
- nincs kategorizálva Livarno Lux
- nincs kategorizálva Harman Kardon
- nincs kategorizálva Florabest
- nincs kategorizálva Nokia
- nincs kategorizálva Stihl
- nincs kategorizálva Lenovo
- nincs kategorizálva Teka
- nincs kategorizálva Yard Force
- nincs kategorizálva Hoover
- nincs kategorizálva Evolveo
- nincs kategorizálva Neff
- nincs kategorizálva HyperX
- nincs kategorizálva Casio
- nincs kategorizálva Toshiba
- nincs kategorizálva Sven
- nincs kategorizálva Neumann
- nincs kategorizálva Oppo
- nincs kategorizálva Bluetti
- nincs kategorizálva Ozito
- nincs kategorizálva Omron
- nincs kategorizálva Bartscher
- nincs kategorizálva Gamdias
- nincs kategorizálva Maxwell
- nincs kategorizálva HP
- nincs kategorizálva Makita
- nincs kategorizálva Hyundai
- nincs kategorizálva Hisense
- nincs kategorizálva Gastronoma
- nincs kategorizálva BenQ
- nincs kategorizálva Sandisk
- nincs kategorizálva Scarlett
- nincs kategorizálva Tefal
- nincs kategorizálva Auriol
- nincs kategorizálva Apple
- nincs kategorizálva HQ
- nincs kategorizálva Ubiquiti Networks
- nincs kategorizálva Bestway
- nincs kategorizálva Saramonic
- nincs kategorizálva SunBriteTV
- nincs kategorizálva Siemens
- nincs kategorizálva TP-Link
- nincs kategorizálva Fellowes
- nincs kategorizálva Emos
- nincs kategorizálva Hifonics
- nincs kategorizálva Voltcraft
- nincs kategorizálva Medion
- nincs kategorizálva Onkyo
- nincs kategorizálva MyPhone
- nincs kategorizálva Motorola
- nincs kategorizálva Geemarc
- nincs kategorizálva Vimar
- nincs kategorizálva LogiLink
- nincs kategorizálva Sena
- nincs kategorizálva Exquisit
- nincs kategorizálva Alcatel
- nincs kategorizálva SBS
- nincs kategorizálva Corbero
- nincs kategorizálva Miele
- nincs kategorizálva Technics
- nincs kategorizálva Fuxtec
- nincs kategorizálva Roland
- nincs kategorizálva JBL
- nincs kategorizálva Camry
- nincs kategorizálva Suzuki
- nincs kategorizálva TCL
- nincs kategorizálva DAP-Audio
- nincs kategorizálva Hunter
- nincs kategorizálva Rocstor
- nincs kategorizálva Digitus
- nincs kategorizálva Zebra
- nincs kategorizálva Viessmann
- nincs kategorizálva My Wall
- nincs kategorizálva Xiaomi
- nincs kategorizálva TRENDnet
- nincs kategorizálva V-Zug
- nincs kategorizálva GoGen
- nincs kategorizálva Flex
- nincs kategorizálva Danby
- nincs kategorizálva DeLonghi
- nincs kategorizálva Clean Air Optima
- nincs kategorizálva Mercusys
- nincs kategorizálva AVM
- nincs kategorizálva Futaba
- nincs kategorizálva Enhanced Flight
- nincs kategorizálva Insignia
- nincs kategorizálva Krups
- nincs kategorizálva Vertiv
- nincs kategorizálva Fujifilm
- nincs kategorizálva Hecht
- nincs kategorizálva AL-KO
- nincs kategorizálva Crimson
- nincs kategorizálva Liebherr
- nincs kategorizálva Martin Logan
- nincs kategorizálva EA Elektro Automatik
- nincs kategorizálva Crivit
- nincs kategorizálva LC-Power
- nincs kategorizálva EZVIZ
- nincs kategorizálva Heinner
- nincs kategorizálva Infiniton
- nincs kategorizálva Ford
- nincs kategorizálva Sunbeam
- nincs kategorizálva Dell
- nincs kategorizálva Beurer
- nincs kategorizálva Boss
- nincs kategorizálva Crestron
- nincs kategorizálva Lancom
- nincs kategorizálva Cramer
- nincs kategorizálva ORNO
- nincs kategorizálva Strong
- nincs kategorizálva Ariete
- nincs kategorizálva Wilfa
- nincs kategorizálva Klarstein
- nincs kategorizálva Amica
- nincs kategorizálva Medisana
- nincs kategorizálva Lincoln Electric
- nincs kategorizálva Cyrus
- nincs kategorizálva Keurig
- nincs kategorizálva VOX
- nincs kategorizálva Scheppach
- nincs kategorizálva Dreame
- nincs kategorizálva Instant
- nincs kategorizálva Cybex
- nincs kategorizálva Be Cool
- nincs kategorizálva Gourmetmaxx
- nincs kategorizálva Gigabyte
- nincs kategorizálva Tripp Lite
- nincs kategorizálva Ergotools Pattfield
- nincs kategorizálva Vivax
- nincs kategorizálva Volkswagen
- nincs kategorizálva MEE Audio
- nincs kategorizálva Prixton
- nincs kategorizálva Primera
- nincs kategorizálva Omega
- nincs kategorizálva Conceptronic
- nincs kategorizálva Datalogic
- nincs kategorizálva Allen & Heath
- nincs kategorizálva Thomson
- nincs kategorizálva Intex
- nincs kategorizálva Esperanza
- nincs kategorizálva Juniper
- nincs kategorizálva Smeg
- nincs kategorizálva Polaroid
- nincs kategorizálva Fagor
- nincs kategorizálva BDI
- nincs kategorizálva Unold
- nincs kategorizálva DPM
- nincs kategorizálva Vileda
- nincs kategorizálva SHX
- nincs kategorizálva Jura
- nincs kategorizálva Sage
- nincs kategorizálva Kyocera
- nincs kategorizálva Klipsch
- nincs kategorizálva Hegel
- nincs kategorizálva Melitta
- nincs kategorizálva CMI
- nincs kategorizálva Brentwood
- nincs kategorizálva Bifinett
- nincs kategorizálva Scala
- nincs kategorizálva Technaxx
- nincs kategorizálva Ardes
- nincs kategorizálva Aiwa
- nincs kategorizálva Hammersmith
- nincs kategorizálva Roidmi
- nincs kategorizálva Phanteks
- nincs kategorizálva Cuisinart
- nincs kategorizálva Suevia
- nincs kategorizálva Joie
- nincs kategorizálva GoPro
- nincs kategorizálva Speco Technologies
- nincs kategorizálva Blackmagic Design
- nincs kategorizálva Orima
- nincs kategorizálva Ricoh
- nincs kategorizálva Eden
- nincs kategorizálva GW Instek
- nincs kategorizálva Interphone
- nincs kategorizálva Rommelsbacher
- nincs kategorizálva Hikvision
- nincs kategorizálva United Office
- nincs kategorizálva Rapid
- nincs kategorizálva Kenwood
- nincs kategorizálva Eurolite
- nincs kategorizálva Owon
- nincs kategorizálva Epson
- nincs kategorizálva Cateye
- nincs kategorizálva Cleanmaxx
- nincs kategorizálva WiiM
- nincs kategorizálva Rega
- nincs kategorizálva Vivanco
- nincs kategorizálva Jocel
- nincs kategorizálva Duronic
- nincs kategorizálva Subaru
- nincs kategorizálva Bimar
- nincs kategorizálva Netgear
- nincs kategorizálva Etna
- nincs kategorizálva Solis
- nincs kategorizálva V7
- nincs kategorizálva Huawei
- nincs kategorizálva Dehner
- nincs kategorizálva EGO
- nincs kategorizálva Aim TTi
- nincs kategorizálva Café
- nincs kategorizálva Microsoft
- nincs kategorizálva Asus
- nincs kategorizálva Segway
- nincs kategorizálva Jabra
- nincs kategorizálva Starlyf
- nincs kategorizálva Vtech
- nincs kategorizálva Clatronic
- nincs kategorizálva Arturia
- nincs kategorizálva Rollei
- nincs kategorizálva Rain Bird
- nincs kategorizálva Bomann
- nincs kategorizálva Mafell
- nincs kategorizálva Bauknecht
- nincs kategorizálva Hama
- nincs kategorizálva Amana
- nincs kategorizálva ELAC
- nincs kategorizálva Bugaboo
- nincs kategorizálva Dyson
- nincs kategorizálva JIMMY
- nincs kategorizálva Hauck
- nincs kategorizálva Zoom
- nincs kategorizálva Renkforce
- nincs kategorizálva Korg
- nincs kategorizálva Ambiano
- nincs kategorizálva Toorx
- nincs kategorizálva Kugoo
- nincs kategorizálva Ninja
- nincs kategorizálva Agfa
- nincs kategorizálva Hotpoint
- nincs kategorizálva Midland
- nincs kategorizálva Haier
- nincs kategorizálva Frigidaire
- nincs kategorizálva Mitsubishi
- nincs kategorizálva Gossen Metrawatt
- nincs kategorizálva Cecotec
- nincs kategorizálva Dacor
- nincs kategorizálva Lamax
- nincs kategorizálva Britax-Römer
- nincs kategorizálva Lezyne
- nincs kategorizálva Sanitas
- nincs kategorizálva Synology
- nincs kategorizálva Godex
- nincs kategorizálva Navitel
- nincs kategorizálva Sencor
- nincs kategorizálva Pelgrim
- nincs kategorizálva GPX
- nincs kategorizálva Proaim
- nincs kategorizálva Hori
- nincs kategorizálva Techno Line
- nincs kategorizálva Focusrite
- nincs kategorizálva Knog
- nincs kategorizálva Polsen
- nincs kategorizálva Draytek
- nincs kategorizálva Privileg
- nincs kategorizálva Benavent
- nincs kategorizálva Supermicro
- nincs kategorizálva Baxi
- nincs kategorizálva Küppersbusch
- nincs kategorizálva Pfaff
- nincs kategorizálva CATA
- nincs kategorizálva Genesis
- nincs kategorizálva Innoliving
- nincs kategorizálva Bose
- nincs kategorizálva Avidsen
- nincs kategorizálva M-Audio
- nincs kategorizálva Brother
- nincs kategorizálva Raymarine
- nincs kategorizálva AOC
- nincs kategorizálva Summit
- nincs kategorizálva Thrustmaster
- nincs kategorizálva Lowrance
- nincs kategorizálva Iogear
- nincs kategorizálva Rowenta
- nincs kategorizálva Lastolite
- nincs kategorizálva Polisport
- nincs kategorizálva Westinghouse
- nincs kategorizálva Thomas
- nincs kategorizálva Güde
- nincs kategorizálva Hitachi
- nincs kategorizálva Inventum
- nincs kategorizálva BabyZen
- nincs kategorizálva Xblitz
- nincs kategorizálva BeamZ
- nincs kategorizálva Mercury
- nincs kategorizálva Hasbro
- nincs kategorizálva IRobot
- nincs kategorizálva Wolf Garten
- nincs kategorizálva Kospel
- nincs kategorizálva Peg Perego
- nincs kategorizálva Ctek
- nincs kategorizálva Rexel
- nincs kategorizálva Lagrange
- nincs kategorizálva DSC
- nincs kategorizálva PATLITE
- nincs kategorizálva BLUEPALM
- nincs kategorizálva Reebok
- nincs kategorizálva Continental Edison
- nincs kategorizálva Biostar
- nincs kategorizálva Eta
- nincs kategorizálva Atag
- nincs kategorizálva Izzy
- nincs kategorizálva Remington
- nincs kategorizálva Mikrotik
- nincs kategorizálva Blackstar
- nincs kategorizálva Telefunken
- nincs kategorizálva Asrock
- nincs kategorizálva Nevir
- nincs kategorizálva Microboards
- nincs kategorizálva Kodak
- nincs kategorizálva Sennheiser
- nincs kategorizálva Tractive
- nincs kategorizálva JANDY
- nincs kategorizálva ResMed
- nincs kategorizálva Ring
- nincs kategorizálva V-TAC
- nincs kategorizálva Piko
- nincs kategorizálva Cambridge
- nincs kategorizálva Kanto
- nincs kategorizálva Doro
- nincs kategorizálva Nikon
- nincs kategorizálva Domo
- nincs kategorizálva Russell Hobbs
- nincs kategorizálva Monster
- nincs kategorizálva Alpine
- nincs kategorizálva Acoustic Solutions
- nincs kategorizálva Roadinger
- nincs kategorizálva Silk'n
- nincs kategorizálva Roadstar
- nincs kategorizálva Zepter
- nincs kategorizálva 4ms
- nincs kategorizálva Optoma
- nincs kategorizálva COLBOR
- nincs kategorizálva Thor
- nincs kategorizálva Emilia
- nincs kategorizálva Caso
- nincs kategorizálva Tempo
- nincs kategorizálva Eastron
- nincs kategorizálva Kiloview
- nincs kategorizálva Omnitronic
- nincs kategorizálva Toolcraft
- nincs kategorizálva ZyXEL
- nincs kategorizálva Logitech
- nincs kategorizálva Solac
- nincs kategorizálva Amiko
- nincs kategorizálva Proviel
- nincs kategorizálva SPL
- nincs kategorizálva Bresser
- nincs kategorizálva JennAir
- nincs kategorizálva Bahr
- nincs kategorizálva Pro-Ject
- nincs kategorizálva Coyote
- nincs kategorizálva Smart
- nincs kategorizálva TOA
- nincs kategorizálva Klein Tools
- nincs kategorizálva Parrot
- nincs kategorizálva Chauvin Arnoux
- nincs kategorizálva Carson
- nincs kategorizálva Kindercraft
- nincs kategorizálva Chicco
- nincs kategorizálva Stiebel Eltron
- nincs kategorizálva Create
- nincs kategorizálva Dahua Technology
- nincs kategorizálva Withings
- nincs kategorizálva Edesa
- nincs kategorizálva Viewsonic
- nincs kategorizálva Wagner
- nincs kategorizálva SVS
- nincs kategorizálva Cobra
- nincs kategorizálva Microlife
- nincs kategorizálva Nextbase
- nincs kategorizálva American DJ
- nincs kategorizálva Scosche
- nincs kategorizálva Crane
- nincs kategorizálva Hilti
- nincs kategorizálva Crunch
- nincs kategorizálva NordicTrack
- nincs kategorizálva Denver
- nincs kategorizálva Dynaudio
- nincs kategorizálva Smart-AVI
- nincs kategorizálva Empress Effects
- nincs kategorizálva Naim
- nincs kategorizálva First Alert
- nincs kategorizálva Bush
- nincs kategorizálva Power Dynamics
- nincs kategorizálva Black & Decker
- nincs kategorizálva Workzone
- nincs kategorizálva Fibaro
- nincs kategorizálva G3 Ferrari
- nincs kategorizálva Stages
- nincs kategorizálva Ravensburger
- nincs kategorizálva Zoofari
- nincs kategorizálva IPGARD
- nincs kategorizálva Dynacord
- nincs kategorizálva Minox
- nincs kategorizálva Trevi
- nincs kategorizálva Hoymiles
- nincs kategorizálva Devolo
- nincs kategorizálva Gardena
- nincs kategorizálva EchoMaster
- nincs kategorizálva Memphis Audio
- nincs kategorizálva RCBS
- nincs kategorizálva Hamilton Beach
- nincs kategorizálva Global
- nincs kategorizálva Fitbit
- nincs kategorizálva DiO
- nincs kategorizálva Planet
- nincs kategorizálva Ewent
- nincs kategorizálva Wood's
- nincs kategorizálva Burg Wächter
- nincs kategorizálva Turmix
- nincs kategorizálva Beha-Amprobe
- nincs kategorizálva Evenflo
- nincs kategorizálva Elta
- nincs kategorizálva Ernitec
- nincs kategorizálva Tenda
- nincs kategorizálva Waterco
- nincs kategorizálva Severin
- nincs kategorizálva Vaillant
- nincs kategorizálva Fieldmann
- nincs kategorizálva DJI
- nincs kategorizálva BT
- nincs kategorizálva Bryton
- nincs kategorizálva Albrecht
- nincs kategorizálva X4 Tech
- nincs kategorizálva Lionelo
- nincs kategorizálva Livington
- nincs kategorizálva Black Box
- nincs kategorizálva Mattel
- nincs kategorizálva Ground Zero
- nincs kategorizálva Autel
- nincs kategorizálva EZ Dupe
- nincs kategorizálva Aluratek
- nincs kategorizálva Audio-Technica
- nincs kategorizálva Gustavsberg
- nincs kategorizálva Amazon
- nincs kategorizálva Orbegozo
- nincs kategorizálva NGS
- nincs kategorizálva BRITA
- nincs kategorizálva HDFury
- nincs kategorizálva Hanseatic
- nincs kategorizálva Joy-It
- nincs kategorizálva MSI
- nincs kategorizálva Konig & Meyer
- nincs kategorizálva Daewoo
- nincs kategorizálva Fisher Price
- nincs kategorizálva Lenoxx
- nincs kategorizálva GYS
- nincs kategorizálva Juki
- nincs kategorizálva Dali
- nincs kategorizálva Mount-It!
- nincs kategorizálva Livoo
- nincs kategorizálva Tesla
- nincs kategorizálva Viking
- nincs kategorizálva Kali Audio
- nincs kategorizálva Godox
- nincs kategorizálva SodaStream
- nincs kategorizálva Antec
- nincs kategorizálva Dash
- nincs kategorizálva Eberle
- nincs kategorizálva Gram
- nincs kategorizálva Extech
- nincs kategorizálva Gembird
- nincs kategorizálva Cisco
- nincs kategorizálva Elica
- nincs kategorizálva PowerPlus
- nincs kategorizálva Denon
- nincs kategorizálva Victor Technology
- nincs kategorizálva Body Sculpture
- nincs kategorizálva Balay
- nincs kategorizálva Silverlit
- nincs kategorizálva Sungrow
- nincs kategorizálva Hotpoint Ariston
- nincs kategorizálva ATen
- nincs kategorizálva XGIMI
- nincs kategorizálva Muse
- nincs kategorizálva Energy Sistem
- nincs kategorizálva Native Instruments
- nincs kategorizálva OK
- nincs kategorizálva Horizon Fitness
- nincs kategorizálva GE
- nincs kategorizálva Playtive
- nincs kategorizálva Guzzanti
- nincs kategorizálva Google
- nincs kategorizálva Honor
- nincs kategorizálva Xtorm
- nincs kategorizálva Electro-Voice
- nincs kategorizálva Concept
- nincs kategorizálva DCS
- nincs kategorizálva DEDRA
- nincs kategorizálva SVAN
- nincs kategorizálva Niceboy
- nincs kategorizálva JL Audio
- nincs kategorizálva On Air
- nincs kategorizálva Dymo
- nincs kategorizálva NightStick
- nincs kategorizálva Metabo
- nincs kategorizálva Dorma
- nincs kategorizálva TrueLife
- nincs kategorizálva Turbo Air
- nincs kategorizálva Newline
- nincs kategorizálva SPC
- nincs kategorizálva Sanus
- nincs kategorizálva Bellini
- nincs kategorizálva Maxi-Cosi
- nincs kategorizálva BabyBjörn
- nincs kategorizálva Osram
- nincs kategorizálva Baby Lock
- nincs kategorizálva Maximum
- nincs kategorizálva Bialetti
- nincs kategorizálva Testo
- nincs kategorizálva Ledlenser
- nincs kategorizálva BOYA
- nincs kategorizálva Speed-Link
- nincs kategorizálva Caple
- nincs kategorizálva Kingston
- nincs kategorizálva Hartke
- nincs kategorizálva Weller
- nincs kategorizálva Nobo
- nincs kategorizálva Steelplay
- nincs kategorizálva Auna
- nincs kategorizálva Akasa
- nincs kategorizálva Simpson
- nincs kategorizálva Hitec
- nincs kategorizálva Polti
- nincs kategorizálva Accu-Chek
- nincs kategorizálva Stokke
- nincs kategorizálva CDA
- nincs kategorizálva KitchenAid
- nincs kategorizálva Unify
- nincs kategorizálva Mac Audio
- nincs kategorizálva Asko
- nincs kategorizálva Rosieres
- nincs kategorizálva Consul
- nincs kategorizálva Growatt
- nincs kategorizálva OBH Nordica
- nincs kategorizálva Bissell
- nincs kategorizálva Behringer
- nincs kategorizálva Nexa
- nincs kategorizálva Bea-fon
- nincs kategorizálva Powerfix
- nincs kategorizálva TriStar
- nincs kategorizálva Biltema
- nincs kategorizálva Hoberg
- nincs kategorizálva Zelmer
- nincs kategorizálva Scotsman
- nincs kategorizálva Rocktrail
- nincs kategorizálva Suunto
- nincs kategorizálva Novy
- nincs kategorizálva Mooer
- nincs kategorizálva Suntec
- nincs kategorizálva ZTE
- nincs kategorizálva BaseTech
- nincs kategorizálva Edimax
- nincs kategorizálva Loewe
- nincs kategorizálva REL Acoustics
- nincs kategorizálva Chamberlain
- nincs kategorizálva Chord
- nincs kategorizálva SABO
- nincs kategorizálva Bavaria
- nincs kategorizálva Eufy
- nincs kategorizálva APC
- nincs kategorizálva CyberPower
- nincs kategorizálva Zodiac
- nincs kategorizálva Bogen
- nincs kategorizálva Tanita
- nincs kategorizálva Showtec
- nincs kategorizálva Pulsar
- nincs kategorizálva Jane
- nincs kategorizálva IMC Toys
- nincs kategorizálva RYOBI
- nincs kategorizálva ProfiCare
- nincs kategorizálva Stiga
- nincs kategorizálva Thule
- nincs kategorizálva Rommer
- nincs kategorizálva Atlantic
- nincs kategorizálva KRK
- nincs kategorizálva SolarEdge
- nincs kategorizálva Tower
- nincs kategorizálva Keter
- nincs kategorizálva Futurelight
- nincs kategorizálva ModeCom
- nincs kategorizálva Avaya
- nincs kategorizálva Ei Electronics
- nincs kategorizálva Fantini Cosmi
- nincs kategorizálva ADATA
- nincs kategorizálva Cooler Master
- nincs kategorizálva Babymoov
- nincs kategorizálva Hobart
- nincs kategorizálva Hammer
- nincs kategorizálva Solo
- nincs kategorizálva Terratec
- nincs kategorizálva Carel
- nincs kategorizálva Koenic
- nincs kategorizálva Chauvet
- nincs kategorizálva ICE Watch
- nincs kategorizálva ADDAC System
- nincs kategorizálva Pentair
- nincs kategorizálva DreamGEAR
- nincs kategorizálva Lorelli
- nincs kategorizálva Nodor
- nincs kategorizálva Grohe
- nincs kategorizálva Electro Harmonix
- nincs kategorizálva Syma
- nincs kategorizálva Levenhuk
- nincs kategorizálva Daikin
- nincs kategorizálva Shure
- nincs kategorizálva Renegade
- nincs kategorizálva Konica Minolta
- nincs kategorizálva Aprilia
- nincs kategorizálva PreSonus
- nincs kategorizálva Mamiya
- nincs kategorizálva REV
- nincs kategorizálva Overmax
- nincs kategorizálva Artusi
- nincs kategorizálva SuperTooth
- nincs kategorizálva Midea
- nincs kategorizálva American International
- nincs kategorizálva Hamax
- nincs kategorizálva Adidas
- nincs kategorizálva Steba
- nincs kategorizálva Revel
- nincs kategorizálva OnePlus
- nincs kategorizálva Flycam
- nincs kategorizálva Winix
- nincs kategorizálva Proxxon
- nincs kategorizálva Archos
- nincs kategorizálva HiKOKI
- nincs kategorizálva Deltaco
- nincs kategorizálva Lorex
- nincs kategorizálva Foscam
- nincs kategorizálva Trisa
- nincs kategorizálva Steelseries
- nincs kategorizálva Oliveri
- nincs kategorizálva Polar
- nincs kategorizálva Intertechno
- nincs kategorizálva MaxCom
- nincs kategorizálva SEH
- nincs kategorizálva Heller
- nincs kategorizálva Milan
- nincs kategorizálva Manhattan
- nincs kategorizálva BeSafe
- nincs kategorizálva Spektrum
- nincs kategorizálva Carlo Gavazzi
- nincs kategorizálva Tannoy
- nincs kategorizálva Plantronics
- nincs kategorizálva SkyRC
- nincs kategorizálva Peavey
- nincs kategorizálva BENNING
- nincs kategorizálva Orbit
- nincs kategorizálva PurAthletics
- nincs kategorizálva Blomberg
- nincs kategorizálva Progress
- nincs kategorizálva ISi
- nincs kategorizálva Kogan
- nincs kategorizálva Profilo
- nincs kategorizálva Texas
- nincs kategorizálva Horizon
- nincs kategorizálva Alecto
- nincs kategorizálva Core SWX
- nincs kategorizálva Grizzly
- nincs kategorizálva Festool
- nincs kategorizálva Falmec
- nincs kategorizálva Honeywell
- nincs kategorizálva Truma
- nincs kategorizálva Broan
- nincs kategorizálva Sodapop
- nincs kategorizálva PKM
- nincs kategorizálva EnGenius
- nincs kategorizálva McCulloch
- nincs kategorizálva Fontastic
- nincs kategorizálva Greenworks
- nincs kategorizálva Intenso
- nincs kategorizálva MantelMount
- nincs kategorizálva Stirling
- nincs kategorizálva Adder
- nincs kategorizálva SMART Technologies
- nincs kategorizálva Yato
- nincs kategorizálva Mesko
- nincs kategorizálva Marshall
- nincs kategorizálva Acme
- nincs kategorizálva Levoit
- nincs kategorizálva Sigma
- nincs kategorizálva PowerXL
- nincs kategorizálva Kindermann
- nincs kategorizálva Juwel
- nincs kategorizálva Furrion
- nincs kategorizálva Ultimate
- nincs kategorizálva Gardenline
- nincs kategorizálva Pentax
- nincs kategorizálva Alesis
- nincs kategorizálva Velleman
- nincs kategorizálva Prestigio
- nincs kategorizálva Universal Audio
- nincs kategorizálva Western Digital
- nincs kategorizálva AEA
- nincs kategorizálva Morel
- nincs kategorizálva Geuther
- nincs kategorizálva Terraillon
- nincs kategorizálva Russound
- nincs kategorizálva GLORIA
- nincs kategorizálva Dimplex
- nincs kategorizálva FireAngel
- nincs kategorizálva Grandstream
- nincs kategorizálva Teac
- nincs kategorizálva Master
- nincs kategorizálva D-Link
- nincs kategorizálva Clarion
- nincs kategorizálva Fischer
- nincs kategorizálva Baumr-AG
- nincs kategorizálva Aspes
- nincs kategorizálva Shindaiwa
- nincs kategorizálva Media-Tech
- nincs kategorizálva Avanti
- nincs kategorizálva OKAY
- nincs kategorizálva Scott
- nincs kategorizálva Blustream
- nincs kategorizálva ProfiCook
- nincs kategorizálva E-ast
- nincs kategorizálva Humminbird
- nincs kategorizálva Grillmeister
- nincs kategorizálva TC Helicon
- nincs kategorizálva Saturn
- nincs kategorizálva Milesight
- nincs kategorizálva EQ-3
- nincs kategorizálva Forza
- nincs kategorizálva Fisher & Paykel
- nincs kategorizálva Kenmore
- nincs kategorizálva Metra
- nincs kategorizálva Røde
- nincs kategorizálva TFA
- nincs kategorizálva Monacor
- nincs kategorizálva Cylinda
- nincs kategorizálva Shimano
- nincs kategorizálva Weston
- nincs kategorizálva Huion
- nincs kategorizálva MXL
- nincs kategorizálva Thermex
- nincs kategorizálva IDIS
- nincs kategorizálva Hayward
- nincs kategorizálva Epiphan
- nincs kategorizálva DCG
- nincs kategorizálva Hestan
- nincs kategorizálva Lanaform
- nincs kategorizálva Boneco
- nincs kategorizálva Tesy
- nincs kategorizálva Scanstrut
- nincs kategorizálva TOGU
- nincs kategorizálva S.M.S.L
- nincs kategorizálva Leifheit
- nincs kategorizálva Melissa
- nincs kategorizálva Anthem
- nincs kategorizálva Janitza
- nincs kategorizálva Sheeran Looper
- nincs kategorizálva Zephyr
- nincs kategorizálva One For All
- nincs kategorizálva IK Multimedia
- nincs kategorizálva Zhiyun
- nincs kategorizálva Trotec
- nincs kategorizálva McIntosh
- nincs kategorizálva Sauter
- nincs kategorizálva ION
- nincs kategorizálva Efbe-Schott
- nincs kategorizálva LD Systems
- nincs kategorizálva Nilfisk
- nincs kategorizálva Eurochron
- nincs kategorizálva Manta
- nincs kategorizálva Proel
- nincs kategorizálva Jamo
- nincs kategorizálva Blaupunkt
- nincs kategorizálva U-Line
- nincs kategorizálva Deaf Bonce
- nincs kategorizálva Oricom
- nincs kategorizálva EcoFlow
- nincs kategorizálva NZXT
- nincs kategorizálva Veripart
- nincs kategorizálva NAD
- nincs kategorizálva Ilve
- nincs kategorizálva Viper
- nincs kategorizálva Apricorn
- nincs kategorizálva Gre
- nincs kategorizálva Pancontrol
- nincs kategorizálva Mio
- nincs kategorizálva Witt
- nincs kategorizálva AstralPool
- nincs kategorizálva Easy Home
- nincs kategorizálva Yealink
- nincs kategorizálva TSC
- nincs kategorizálva Korona
- nincs kategorizálva Hozelock
- nincs kategorizálva Chacon
- nincs kategorizálva Stadler Form
- nincs kategorizálva Minn Kota
- nincs kategorizálva Elro
- nincs kategorizálva Crofton
- nincs kategorizálva InfiRay
- nincs kategorizálva Bertazzoni
- nincs kategorizálva Fluke
- nincs kategorizálva Mobicool
- nincs kategorizálva Moxa
- nincs kategorizálva Foster
- nincs kategorizálva Thomann
- nincs kategorizálva DOD
- nincs kategorizálva Datapath
- nincs kategorizálva Sagem
- nincs kategorizálva Hammond
- nincs kategorizálva Princeton Tec
- nincs kategorizálva Pro-User
- nincs kategorizálva Inglesina
- nincs kategorizálva Hansa
- nincs kategorizálva Thetford
- nincs kategorizálva Perixx
- nincs kategorizálva Uni-T
- nincs kategorizálva Razer
- nincs kategorizálva T-Rex
- nincs kategorizálva Taurus
- nincs kategorizálva Comfee
- nincs kategorizálva Cosori
- nincs kategorizálva Samson
- nincs kategorizálva Leitz
- nincs kategorizálva Be Quiet!
- nincs kategorizálva Signature
- nincs kategorizálva Delta
- nincs kategorizálva Zipper
- nincs kategorizálva Cayin
- nincs kategorizálva Bebe Confort
- nincs kategorizálva Gosund
- nincs kategorizálva TomTom
- nincs kategorizálva Jay-Tech
- nincs kategorizálva Busch-Jaeger
- nincs kategorizálva Olympia
- nincs kategorizálva Logik
- nincs kategorizálva Tineco
- nincs kategorizálva NEO Tools
- nincs kategorizálva Domyos
- nincs kategorizálva Millenium
- nincs kategorizálva Bavaria By Einhell
- nincs kategorizálva Mackie
- nincs kategorizálva Soundcraft
- nincs kategorizálva Vonyx
- nincs kategorizálva Rossmax
- nincs kategorizálva Fiap
- nincs kategorizálva Tronic
- nincs kategorizálva Alto
- nincs kategorizálva Metrix
- nincs kategorizálva Delta Dore
- nincs kategorizálva Posiflex
- nincs kategorizálva Hendi
- nincs kategorizálva Peerless-AV
- nincs kategorizálva ZKTeco
- nincs kategorizálva Abus
- nincs kategorizálva Maytag
- nincs kategorizálva La Crosse Technology
- nincs kategorizálva SureFire
- nincs kategorizálva Vivotek
- nincs kategorizálva AG Neovo
- nincs kategorizálva AFK
- nincs kategorizálva Polaris
- nincs kategorizálva KKT Kolbe
- nincs kategorizálva Gree
- nincs kategorizálva Infinity
- nincs kategorizálva Fulgor Milano
- nincs kategorizálva Rovo Kids
- nincs kategorizálva Walrus Audio
- nincs kategorizálva BEEM
- nincs kategorizálva Barazza
- nincs kategorizálva Arlo
- nincs kategorizálva Magnat
- nincs kategorizálva Bang & Olufsen
- nincs kategorizálva Trust
- nincs kategorizálva Herkules
- nincs kategorizálva UDG Gear
- nincs kategorizálva GAO
- nincs kategorizálva Iiyama
- nincs kategorizálva Yukon
- nincs kategorizálva Chief
- nincs kategorizálva AKAI
- nincs kategorizálva Porter-Cable
- nincs kategorizálva Tiptel
- nincs kategorizálva Finder
- nincs kategorizálva Konig
- nincs kategorizálva Marmitek
- nincs kategorizálva H.Koenig
- nincs kategorizálva Stabo
- nincs kategorizálva TechniSat
- nincs kategorizálva Seiki
- nincs kategorizálva Chipolino
- nincs kategorizálva 3M
- nincs kategorizálva ARRI
- nincs kategorizálva Tanaka
- nincs kategorizálva GlobalTronics
- nincs kategorizálva Gtech
- nincs kategorizálva TDE Instruments
- nincs kategorizálva Line 6
- nincs kategorizálva Crelando
- nincs kategorizálva Jensen
- nincs kategorizálva Megger
- nincs kategorizálva Polyend
- nincs kategorizálva Pyle
- nincs kategorizálva Emerson
- nincs kategorizálva Shark
- nincs kategorizálva Computherm
- nincs kategorizálva MuxLab
- nincs kategorizálva Lumens
- nincs kategorizálva Audioengine
- nincs kategorizálva Testboy
- nincs kategorizálva AVer
- nincs kategorizálva Everdure
- nincs kategorizálva Veritas
- nincs kategorizálva Sôlt
- nincs kategorizálva DeWalt
- nincs kategorizálva AVMATRIX
- nincs kategorizálva Kalorik
- nincs kategorizálva Morphy Richards
- nincs kategorizálva Sanyo
- nincs kategorizálva Steinel
- nincs kategorizálva Hacienda
- nincs kategorizálva Kemo
- nincs kategorizálva Constructa
- nincs kategorizálva Rolls
- nincs kategorizálva Frilec
- nincs kategorizálva Laica
- nincs kategorizálva Salora
- nincs kategorizálva Sunding
- nincs kategorizálva Healthy Choice
- nincs kategorizálva Musical Fidelity
- nincs kategorizálva Rangemaster
- nincs kategorizálva DataVideo
- nincs kategorizálva Waldbeck
- nincs kategorizálva Eheim
- nincs kategorizálva Telestar
- nincs kategorizálva A-NeuVideo
- nincs kategorizálva Lenco
- nincs kategorizálva Wachendorff
- nincs kategorizálva Greisinger
- nincs kategorizálva Sonel
- nincs kategorizálva Dangerous Music
- nincs kategorizálva Wiha
- nincs kategorizálva CRUX
- nincs kategorizálva Roccat
- nincs kategorizálva Maxell
- nincs kategorizálva Solplanet
- nincs kategorizálva Junkers
- nincs kategorizálva JMAZ Lighting
- nincs kategorizálva Sanitaire
- nincs kategorizálva Alpina
- nincs kategorizálva Stinger
- nincs kategorizálva GA.MA
- nincs kategorizálva Atlona
- nincs kategorizálva Statron
- nincs kategorizálva Watson
- nincs kategorizálva Corsair
- nincs kategorizálva Schneider
- nincs kategorizálva Corel
- nincs kategorizálva Gastroback
- nincs kategorizálva Kyoritsu
- nincs kategorizálva Bernina
- nincs kategorizálva AJA
- nincs kategorizálva LEDs-ON
- nincs kategorizálva Lindy
- nincs kategorizálva Infantino
- nincs kategorizálva Cudy
- nincs kategorizálva Philco
- nincs kategorizálva JYSK
- nincs kategorizálva Brandson
- nincs kategorizálva ECG
- nincs kategorizálva Foppapedretti
- nincs kategorizálva Audiotec Fischer
- nincs kategorizálva Stanley
- nincs kategorizálva NACON
- nincs kategorizálva Danfoss
- nincs kategorizálva Uniden
- nincs kategorizálva JLab
- nincs kategorizálva Victrola
- nincs kategorizálva Hurricane
- nincs kategorizálva Busch + Müller
- nincs kategorizálva LiftMaster
- nincs kategorizálva Fender
- nincs kategorizálva Vorago
- nincs kategorizálva Gaggenau
- nincs kategorizálva Technika
- nincs kategorizálva Arctic Cooling
- nincs kategorizálva Majority
- nincs kategorizálva Areca
- nincs kategorizálva Rotel
- nincs kategorizálva Hertz
- nincs kategorizálva Impact
- nincs kategorizálva Leica
- nincs kategorizálva Azden
- nincs kategorizálva Bowers & Wilkins
- nincs kategorizálva Barco
- nincs kategorizálva Thinkware
- nincs kategorizálva QNAP
- nincs kategorizálva Franklin
- nincs kategorizálva Quantum
- nincs kategorizálva Mean Well
- nincs kategorizálva FBT
- nincs kategorizálva Vemer
- nincs kategorizálva Zenec
- nincs kategorizálva Vornado
- nincs kategorizálva Emko
- nincs kategorizálva Interstuhl
- nincs kategorizálva KEF
- nincs kategorizálva Newland
- nincs kategorizálva Kaiser
- nincs kategorizálva Burris
- nincs kategorizálva Esatto
- nincs kategorizálva Grässlin
- nincs kategorizálva MDT
- nincs kategorizálva Franke
- nincs kategorizálva NEC
- nincs kategorizálva Audiolab
- nincs kategorizálva Ufesa
- nincs kategorizálva Sekonic
- nincs kategorizálva Meireles
- nincs kategorizálva Capital Sports
- nincs kategorizálva Texas Instruments
- nincs kategorizálva Atlas Sound
- nincs kategorizálva Proctor Silex
- nincs kategorizálva Ernesto
- nincs kategorizálva Silverline
- nincs kategorizálva AKG
- nincs kategorizálva Vonroc
- nincs kategorizálva Marshall Electronics
- nincs kategorizálva Trebs
- nincs kategorizálva Galanz
- nincs kategorizálva Taylor
- nincs kategorizálva Ashly
- nincs kategorizálva AudioControl
- nincs kategorizálva Rigol
- nincs kategorizálva CM Storm
- nincs kategorizálva Graco
- nincs kategorizálva Fanvil
- nincs kategorizálva Scandomestic
- nincs kategorizálva Soundmaster
- nincs kategorizálva New Pol
- nincs kategorizálva Crock-Pot
- nincs kategorizálva Neutrik
- nincs kategorizálva Nitecore
- nincs kategorizálva Audioline
- nincs kategorizálva Monitor Audio
- nincs kategorizálva DMT
- nincs kategorizálva Rinnai
- nincs kategorizálva Steinberg
- nincs kategorizálva Dormakaba
- nincs kategorizálva Cameo
- nincs kategorizálva Cotech
- nincs kategorizálva Audac
- nincs kategorizálva Traxxas
- nincs kategorizálva Fresh 'n Rebel
- nincs kategorizálva Technical Pro
- nincs kategorizálva Martin
- nincs kategorizálva Alphatronics
- nincs kategorizálva AYA
- nincs kategorizálva Siig
- nincs kategorizálva Yorkville
- nincs kategorizálva Stabila
- nincs kategorizálva MBM
- nincs kategorizálva Recaro
- nincs kategorizálva GoClever
- nincs kategorizálva WMF
- nincs kategorizálva Wolf
- nincs kategorizálva Rockford Fosgate
- nincs kategorizálva Sensiplast
- nincs kategorizálva Krüger&Matz
- nincs kategorizálva Salus
- nincs kategorizálva Dual
- nincs kategorizálva Elo
- nincs kategorizálva Inter-Tech
- nincs kategorizálva Ebro
- nincs kategorizálva Getac
- nincs kategorizálva ICOM
- nincs kategorizálva Velbus
- nincs kategorizálva Eaton
- nincs kategorizálva Projecta
- nincs kategorizálva Brandt
- nincs kategorizálva Novation
- nincs kategorizálva Artecta
- nincs kategorizálva Noctua
- nincs kategorizálva Gefen
- nincs kategorizálva Graef
- nincs kategorizálva Ambient Weather
- nincs kategorizálva Warm Audio
- nincs kategorizálva Dirt Devil
- nincs kategorizálva Edilkamin
- nincs kategorizálva Kubota
- nincs kategorizálva Wharfedale
- nincs kategorizálva Edge
- nincs kategorizálva M-e
- nincs kategorizálva Cardo
- nincs kategorizálva Kathrein
- nincs kategorizálva Avenview
- nincs kategorizálva Homematic IP
- nincs kategorizálva IStarUSA
- nincs kategorizálva Oase
- nincs kategorizálva Lantronix
- nincs kategorizálva Adobe
- nincs kategorizálva Yaesu
- nincs kategorizálva WAGAN
- nincs kategorizálva Ketron
- nincs kategorizálva Panduit
- nincs kategorizálva HQ Power
- nincs kategorizálva Elation
- nincs kategorizálva RCA
- nincs kategorizálva Arendo
- nincs kategorizálva Somfy
- nincs kategorizálva Vocopro
- nincs kategorizálva Outwell
- nincs kategorizálva Axis
- nincs kategorizálva Nintendo
- nincs kategorizálva BBB
- nincs kategorizálva SunPower
- nincs kategorizálva Biohort
- nincs kategorizálva Beper
- nincs kategorizálva Insta360
- nincs kategorizálva Optex
- nincs kategorizálva Bestron
- nincs kategorizálva Vacmaster
- nincs kategorizálva HTC
- nincs kategorizálva Breville
- nincs kategorizálva TAURUS Titanium
- nincs kategorizálva Postium
- nincs kategorizálva Magnus
- nincs kategorizálva Thermaltake
- nincs kategorizálva Orion
- nincs kategorizálva Melinera
- nincs kategorizálva Blizzard
- nincs kategorizálva Medeli
- nincs kategorizálva Varta
- nincs kategorizálva Technicolor
- nincs kategorizálva Palmer
- nincs kategorizálva Tiptop Audio
- nincs kategorizálva Antari
- nincs kategorizálva Altronix
- nincs kategorizálva Marvel
- nincs kategorizálva Imperial
- nincs kategorizálva Soler & Palau
- nincs kategorizálva Hover-1
- nincs kategorizálva Kicker
- nincs kategorizálva Alpha Tools
- nincs kategorizálva Creative
- nincs kategorizálva Pattfield
- nincs kategorizálva EverFocus
- nincs kategorizálva Elektron
- nincs kategorizálva SereneLife
- nincs kategorizálva Ravanson
- nincs kategorizálva BLANCO
- nincs kategorizálva Multimetrix
- nincs kategorizálva NOCO
- nincs kategorizálva DBX
- nincs kategorizálva Teesa
- nincs kategorizálva Sangean
- nincs kategorizálva Carrier
- nincs kategorizálva Joby
- nincs kategorizálva Pontec
- nincs kategorizálva Schuberth
- nincs kategorizálva JAYS
- nincs kategorizálva Salter
- nincs kategorizálva Equip
- nincs kategorizálva Deltaco Gaming
- nincs kategorizálva Luxor
- nincs kategorizálva ECS
- nincs kategorizálva Flavel
- nincs kategorizálva Metz
- nincs kategorizálva Deye
- nincs kategorizálva Genius
- nincs kategorizálva Emeril Lagasse
- nincs kategorizálva Camille Bauer
- nincs kategorizálva Ipevo
- nincs kategorizálva Valueline
- nincs kategorizálva Scancool
- nincs kategorizálva Becken
- nincs kategorizálva Swann
- nincs kategorizálva Heckler Design
- nincs kategorizálva Brevi
- nincs kategorizálva Olight
- nincs kategorizálva Best Service
- nincs kategorizálva Kino Flo
- nincs kategorizálva Holzmann
- nincs kategorizálva Fein
- nincs kategorizálva Elvid
- nincs kategorizálva InfaSecure
- nincs kategorizálva PowerBass
- nincs kategorizálva Sirius
- nincs kategorizálva Gamber-Johnson
- nincs kategorizálva Challenge Xtreme
- nincs kategorizálva Arris
- nincs kategorizálva Definitive Technology
- nincs kategorizálva Focal
- nincs kategorizálva Adj
- nincs kategorizálva Revlon
- nincs kategorizálva Anker
- nincs kategorizálva Smoby
- nincs kategorizálva Bikemate
- nincs kategorizálva I-TEC
- nincs kategorizálva Gravity
- nincs kategorizálva Gabor
- nincs kategorizálva Anthro
- nincs kategorizálva Wacom
- nincs kategorizálva MB Quart
- nincs kategorizálva Primus
- nincs kategorizálva Weber
- nincs kategorizálva Havis
- nincs kategorizálva Genie
- nincs kategorizálva H-Tronic
- nincs kategorizálva Legamaster
- nincs kategorizálva Lectrosonics
- nincs kategorizálva Hughes & Kettner
- nincs kategorizálva NovaStar
- nincs kategorizálva Swift
- nincs kategorizálva Victron Energy
- nincs kategorizálva IFi Audio
- nincs kategorizálva AREXX
- nincs kategorizálva ATIKA
- nincs kategorizálva Cleco
- nincs kategorizálva OneConcept
- nincs kategorizálva Haeger
- nincs kategorizálva ILive
- nincs kategorizálva Absco
- nincs kategorizálva Audix
- nincs kategorizálva Neumärker
- nincs kategorizálva NANO Modules
- nincs kategorizálva Flame
- nincs kategorizálva Flaem
- nincs kategorizálva Hensel
- nincs kategorizálva Spear & Jackson
- nincs kategorizálva PCE
- nincs kategorizálva Duracell
- nincs kategorizálva Westland
- nincs kategorizálva Rapoo
- nincs kategorizálva OM SYSTEM
- nincs kategorizálva President
- nincs kategorizálva Lowepro
- nincs kategorizálva IVT
- nincs kategorizálva Edwards
- nincs kategorizálva Gustard
- nincs kategorizálva Vivolink
- nincs kategorizálva AS Schwabe
- nincs kategorizálva Deditec
- nincs kategorizálva WEG
- nincs kategorizálva Bluebird
- nincs kategorizálva Eltako
- nincs kategorizálva Palmako
- nincs kategorizálva Weidmüller
- nincs kategorizálva Dunlop
- nincs kategorizálva Cotek
- nincs kategorizálva Grand Effects
- nincs kategorizálva Tascam
- nincs kategorizálva Finnlo
- nincs kategorizálva Homedics
- nincs kategorizálva Happy Plugs
- nincs kategorizálva Concept2
- nincs kategorizálva Linksys
- nincs kategorizálva Olimpia Splendid
- nincs kategorizálva Teltonika
- nincs kategorizálva Sitecom
- nincs kategorizálva Trixie
- nincs kategorizálva Mistral
- nincs kategorizálva ACTi
- nincs kategorizálva Schwaiger
- nincs kategorizálva Christmas Time
- nincs kategorizálva Stannah
- nincs kategorizálva Multibrackets
- nincs kategorizálva LifeSpan
- nincs kategorizálva Neewer
- nincs kategorizálva FiiO
- nincs kategorizálva Christmaxx
- nincs kategorizálva EasyMaxx
- nincs kategorizálva Maxxmee
- nincs kategorizálva Heitronic
- nincs kategorizálva Elmo
- nincs kategorizálva Comprehensive
- nincs kategorizálva Toro
- nincs kategorizálva Lund
- nincs kategorizálva Ocean Matrix
- nincs kategorizálva MAK
- nincs kategorizálva Life Fitness
- nincs kategorizálva Orava
- nincs kategorizálva Dobot
- nincs kategorizálva Cougar
- nincs kategorizálva Arçelik
- nincs kategorizálva Paxton
- nincs kategorizálva Razor
- nincs kategorizálva Roxio
- nincs kategorizálva Vitek
- nincs kategorizálva SurgeX
- nincs kategorizálva Enhance
- nincs kategorizálva Digitalinx
- nincs kategorizálva Anton/Bauer
- nincs kategorizálva Alfatron
- nincs kategorizálva Bolt
- nincs kategorizálva APA
- nincs kategorizálva Mophie
- nincs kategorizálva Brady
- nincs kategorizálva Eurom
- nincs kategorizálva Govee
- nincs kategorizálva QOMO
- nincs kategorizálva Astro
- nincs kategorizálva Xvive
- nincs kategorizálva Bixolon
- nincs kategorizálva Magic Chef
- nincs kategorizálva Dot Line
- nincs kategorizálva WHD
- nincs kategorizálva Sound Devices
- nincs kategorizálva Match
- nincs kategorizálva Doffler
- nincs kategorizálva Geneva
- nincs kategorizálva Foreo
- nincs kategorizálva Topeak
- nincs kategorizálva Zotac
- nincs kategorizálva TechBite
- nincs kategorizálva Sauber
- nincs kategorizálva Cocraft
- nincs kategorizálva Lupine
- nincs kategorizálva Thorens
- nincs kategorizálva Indiana Line
- nincs kategorizálva Craftsman
- nincs kategorizálva Sumiko
- nincs kategorizálva Blackburn
- nincs kategorizálva Laserliner
- nincs kategorizálva RADEMACHER
- nincs kategorizálva SoundMagic
- nincs kategorizálva Majestic
- nincs kategorizálva Sebo
- nincs kategorizálva Savio
- nincs kategorizálva Maestro
- nincs kategorizálva Kern
- nincs kategorizálva Graphite
- nincs kategorizálva Reflexion
- nincs kategorizálva Enermax
- nincs kategorizálva Smartwares
- nincs kategorizálva Salicru
- nincs kategorizálva Megasat
- nincs kategorizálva Eureka
- nincs kategorizálva Teufel
- nincs kategorizálva Sogo
- nincs kategorizálva Hikmicro
- nincs kategorizálva IGET
- nincs kategorizálva TensCare
- nincs kategorizálva Beautifly
- nincs kategorizálva Crosley
- nincs kategorizálva Aqara
- nincs kategorizálva Ugreen
- nincs kategorizálva Vincent
- nincs kategorizálva Kopp
- nincs kategorizálva DPA
- nincs kategorizálva NuPrime
- nincs kategorizálva REVO
- nincs kategorizálva Maytronics
- nincs kategorizálva Park Tool
- nincs kategorizálva George Foreman
- nincs kategorizálva InLine
- nincs kategorizálva Fluval
- nincs kategorizálva Advance Acoustic
- nincs kategorizálva Nutrichef
- nincs kategorizálva Grundfos
- nincs kategorizálva Cubot
- nincs kategorizálva Kokido
- nincs kategorizálva J5create
- nincs kategorizálva SwitchBot
- nincs kategorizálva MoFi
- nincs kategorizálva Apelson
- nincs kategorizálva Adventuridge
- nincs kategorizálva Casa Deco
- nincs kategorizálva Reloop
- nincs kategorizálva Hazet
- nincs kategorizálva Snow Joe
- nincs kategorizálva Glem Gas
- nincs kategorizálva Primewire
- nincs kategorizálva Euromaid
- nincs kategorizálva 8BitDo
- nincs kategorizálva CSL
- nincs kategorizálva Oreck
- nincs kategorizálva Tepro
- nincs kategorizálva XCell
- nincs kategorizálva Perfect Christmas
- nincs kategorizálva I.safe Mobile
- nincs kategorizálva Newstar
- nincs kategorizálva Artsound
- nincs kategorizálva Vivitar
- nincs kategorizálva Vogel's
- nincs kategorizálva Char-Broil
- nincs kategorizálva BSS Audio
- nincs kategorizálva Chandler
- nincs kategorizálva Flama
- nincs kategorizálva HK Audio
- nincs kategorizálva Sevenoak
- nincs kategorizálva Rittal
- nincs kategorizálva Cherry
- nincs kategorizálva Lasko
- nincs kategorizálva Yellow Garden Line
- nincs kategorizálva SWIT
- nincs kategorizálva Belkin
- nincs kategorizálva Bebob
- nincs kategorizálva Kahayan
- nincs kategorizálva Gen Energy
- nincs kategorizálva Anywhere Cart
- nincs kategorizálva Xcellon
- nincs kategorizálva RGBlink
- nincs kategorizálva Heckler
- nincs kategorizálva Lewitt
- nincs kategorizálva CEDAR
- nincs kategorizálva Kopul
- nincs kategorizálva SmallRig
- nincs kategorizálva Fiilex
- nincs kategorizálva Morley
- nincs kategorizálva KJB Security Products
- nincs kategorizálva Zeiss
- nincs kategorizálva Vertex
- nincs kategorizálva K&M
- nincs kategorizálva Elgato
- nincs kategorizálva Sky-Watcher
- nincs kategorizálva Wimberley
- nincs kategorizálva Sescom
- nincs kategorizálva PTZ Optics
- nincs kategorizálva KanexPro
- nincs kategorizálva Rupert Neve Designs
- nincs kategorizálva ARC
- nincs kategorizálva DEERSYNC
- nincs kategorizálva Key Digital
- nincs kategorizálva Cranborne Audio
- nincs kategorizálva Murideo
- nincs kategorizálva Glide Gear
- nincs kategorizálva Lian Li
- nincs kategorizálva Hosa
- nincs kategorizálva Pawa
- nincs kategorizálva Vortex
- nincs kategorizálva Kramer
- nincs kategorizálva Serpent
- nincs kategorizálva Whirlwind
- nincs kategorizálva Erica Synths
- nincs kategorizálva Arkon
- nincs kategorizálva Analog Way
- nincs kategorizálva Profoto
- nincs kategorizálva ChyTV
- nincs kategorizálva ToughTested
- nincs kategorizálva Robus
- nincs kategorizálva ART
- nincs kategorizálva Intellijel
- nincs kategorizálva BZBGear
- nincs kategorizálva Generac
- nincs kategorizálva BirdDog
- nincs kategorizálva Manfrotto
- nincs kategorizálva Lemair
- nincs kategorizálva Stamina
- nincs kategorizálva AMX
- nincs kategorizálva Ideal
- nincs kategorizálva Rosco
- nincs kategorizálva Matsui
- nincs kategorizálva Zibro
- nincs kategorizálva Fysic
- nincs kategorizálva Quigg
- nincs kategorizálva Wiko
- nincs kategorizálva A.O. Smith
- nincs kategorizálva Ade
- nincs kategorizálva Aduro
- nincs kategorizálva Allnet
- nincs kategorizálva Airlux
- nincs kategorizálva Aligator
- nincs kategorizálva Ambrogio
- nincs kategorizálva Allied Telesis
- nincs kategorizálva Allibert
- nincs kategorizálva Alienware
- nincs kategorizálva ABC Design
- nincs kategorizálva Amfra
- nincs kategorizálva Ansmann
- nincs kategorizálva Alcon
- nincs kategorizálva Airlive
- nincs kategorizálva A4tech
- nincs kategorizálva Ampeg
- nincs kategorizálva Amplicom
- nincs kategorizálva Amprobe
- nincs kategorizálva Argon
- nincs kategorizálva American Audio
- nincs kategorizálva Aquapur
- nincs kategorizálva Aeris
- nincs kategorizálva Ascom
- nincs kategorizálva Act
- nincs kategorizálva Alpen Kreuzer
- nincs kategorizálva Reflecta
- nincs kategorizálva Argus
- nincs kategorizálva ATN
- nincs kategorizálva Ziggo
- nincs kategorizálva Intermatic
- nincs kategorizálva Flamingo
- nincs kategorizálva Toolland
- nincs kategorizálva Icy Box
- nincs kategorizálva Brennenstuhl
- nincs kategorizálva Ferm
- nincs kategorizálva MJX
- nincs kategorizálva Hirschmann
- nincs kategorizálva Kruidvat
- nincs kategorizálva Absima
- nincs kategorizálva Audison
- nincs kategorizálva Salton
- nincs kategorizálva Proteca
- nincs kategorizálva Topmove
- nincs kategorizálva Lexibook
- nincs kategorizálva Body Solid
- nincs kategorizálva Draper
- nincs kategorizálva Tryton
- nincs kategorizálva Arthur Martin
- nincs kategorizálva Oceanic
- nincs kategorizálva Tiger
- nincs kategorizálva Yale
- nincs kategorizálva Meradiso
- nincs kategorizálva Calor
- nincs kategorizálva Waring Commercial
- nincs kategorizálva Kernau
- nincs kategorizálva Miomare
- nincs kategorizálva BH Fitness
- nincs kategorizálva Tevion
- nincs kategorizálva GPO
- nincs kategorizálva Thermador
- nincs kategorizálva Lucide
- nincs kategorizálva Parisot
- nincs kategorizálva Caliber
- nincs kategorizálva Skil
- nincs kategorizálva Eminent
- nincs kategorizálva Pressalit
- nincs kategorizálva SilverStone
- nincs kategorizálva Oster
- nincs kategorizálva Kichler
- nincs kategorizálva VAX
- nincs kategorizálva Trekstor
- nincs kategorizálva Vestel
- nincs kategorizálva Sinbo
- nincs kategorizálva Bushnell
- nincs kategorizálva Jata
- nincs kategorizálva VirtuFit
- nincs kategorizálva Swan
- nincs kategorizálva Fritel
- nincs kategorizálva Ordex
- nincs kategorizálva Itho
- nincs kategorizálva Targus
- nincs kategorizálva Q-CONNECT
- nincs kategorizálva Landmann
- nincs kategorizálva Sicce
- nincs kategorizálva Britax
- nincs kategorizálva Monogram
- nincs kategorizálva Hard Head
- nincs kategorizálva Exibel
- nincs kategorizálva Medela
- nincs kategorizálva Easy Camp
- nincs kategorizálva Anslut
- nincs kategorizálva Meec Tools
- nincs kategorizálva Auto Joe
- nincs kategorizálva Fortinet
- nincs kategorizálva Youin
- nincs kategorizálva Valore
- nincs kategorizálva Accucold
- nincs kategorizálva Sun Joe
- nincs kategorizálva Perfecta
- nincs kategorizálva Jumbo
- nincs kategorizálva Cricut
- nincs kategorizálva Hähnel
- nincs kategorizálva Ferplast
- nincs kategorizálva EWT
- nincs kategorizálva Enduro
- nincs kategorizálva Aukey
- nincs kategorizálva Dremel
- nincs kategorizálva KlikaanKlikuit
- nincs kategorizálva Gemini
- nincs kategorizálva Easypix
- nincs kategorizálva Berg
- nincs kategorizálva Simplified MFG
- nincs kategorizálva Vision
- nincs kategorizálva Axa
- nincs kategorizálva ABB
- nincs kategorizálva Mellerware
- nincs kategorizálva Intergas
- nincs kategorizálva Silva
- nincs kategorizálva Energenie
- nincs kategorizálva Termozeta
- nincs kategorizálva Bella
- nincs kategorizálva Palson
- nincs kategorizálva Eldom
- nincs kategorizálva Valeton
- nincs kategorizálva Jocca
- nincs kategorizálva Nilox
- nincs kategorizálva Vango
- nincs kategorizálva Ventura
- nincs kategorizálva Sonos
- nincs kategorizálva Summit Audio
- nincs kategorizálva SKS
- nincs kategorizálva Musway
- nincs kategorizálva Kensington
- nincs kategorizálva Nautilus
- nincs kategorizálva Byron
- nincs kategorizálva Cresta
- nincs kategorizálva Brigmton
- nincs kategorizálva Sunstech
- nincs kategorizálva Smith & Wesson
- nincs kategorizálva Elektrobock
- nincs kategorizálva Nabo
- nincs kategorizálva Defy
- nincs kategorizálva DeLock
- nincs kategorizálva Avalon
- nincs kategorizálva Plant Craft
- nincs kategorizálva Dubatti
- nincs kategorizálva Bionaire
- nincs kategorizálva Maginon
- nincs kategorizálva Sylvania
- nincs kategorizálva Campomatic
- nincs kategorizálva Patton
- nincs kategorizálva Igloo
- nincs kategorizálva Senco
- nincs kategorizálva Tork
- nincs kategorizálva Techly
- nincs kategorizálva Numatic
- nincs kategorizálva Swissvoice
- nincs kategorizálva Vaude
- nincs kategorizálva Totolink
- nincs kategorizálva Sunny
- nincs kategorizálva BlueBuilt
- nincs kategorizálva Gazelle
- nincs kategorizálva Profile
- nincs kategorizálva Marquant
- nincs kategorizálva Nibe
- nincs kategorizálva Damixa
- nincs kategorizálva Da-Lite
- nincs kategorizálva Ferroli
- nincs kategorizálva First Austria
- nincs kategorizálva Ednet
- nincs kategorizálva Bowflex
- nincs kategorizálva AVerMedia
- nincs kategorizálva Visage
- nincs kategorizálva Celestron
- nincs kategorizálva CaterCool
- nincs kategorizálva Master Lock
- nincs kategorizálva Matrox
- nincs kategorizálva Seiko
- nincs kategorizálva Maktec
- nincs kategorizálva Binatone
- nincs kategorizálva Connect IT
- nincs kategorizálva Steren
- nincs kategorizálva Perel
- nincs kategorizálva Nuna
- nincs kategorizálva Eico
- nincs kategorizálva Polk
- nincs kategorizálva Nero
- nincs kategorizálva Kubo
- nincs kategorizálva Exagerate
- nincs kategorizálva Air King
- nincs kategorizálva Gossen
- nincs kategorizálva Elba
- nincs kategorizálva Flir
- nincs kategorizálva KiddyGuard
- nincs kategorizálva Proline
- nincs kategorizálva Livarno
- nincs kategorizálva Barkan
- nincs kategorizálva Netis
- nincs kategorizálva Coby
- nincs kategorizálva Royal Sovereign
- nincs kategorizálva King
- nincs kategorizálva AcuRite
- nincs kategorizálva Ergobaby
- nincs kategorizálva Envivo
- nincs kategorizálva Petzl
- nincs kategorizálva True
- nincs kategorizálva Galaxy Audio
- nincs kategorizálva Black Diamond
- nincs kategorizálva ESYLUX
- nincs kategorizálva Ventus
- nincs kategorizálva TOTO
- nincs kategorizálva Technoline
- nincs kategorizálva Osann
- nincs kategorizálva Lindam
- nincs kategorizálva Kelvinator
- nincs kategorizálva Goliath
- nincs kategorizálva Yamato
- nincs kategorizálva Vivo
- nincs kategorizálva Belgacom
- nincs kategorizálva SEB
- nincs kategorizálva Malmbergs
- nincs kategorizálva Phoenix
- nincs kategorizálva AV:link
- nincs kategorizálva Power Craft
- nincs kategorizálva Otolift
- nincs kategorizálva GBC
- nincs kategorizálva Prenatal
- nincs kategorizálva Champion
- nincs kategorizálva Tvilum
- nincs kategorizálva Heylo
- nincs kategorizálva TacTic
- nincs kategorizálva Nolte
- nincs kategorizálva G3
- nincs kategorizálva Peach
- nincs kategorizálva Pure
- nincs kategorizálva Lescha
- nincs kategorizálva Buffalo
- nincs kategorizálva Vello
- nincs kategorizálva Jenn-Air
- nincs kategorizálva R-Vent
- nincs kategorizálva Woood
- nincs kategorizálva Audiovox
- nincs kategorizálva Carpigiani
- nincs kategorizálva Davis
- nincs kategorizálva ICU
- nincs kategorizálva Daitsu
- nincs kategorizálva Farberware
- nincs kategorizálva CasaFan
- nincs kategorizálva Milectric
- nincs kategorizálva Vicks
- nincs kategorizálva Walkstool
- nincs kategorizálva Macally
- nincs kategorizálva GeoVision
- nincs kategorizálva Kidde
- nincs kategorizálva Apogee
- nincs kategorizálva Nest
- nincs kategorizálva Grothe
- nincs kategorizálva LevelOne
- nincs kategorizálva Kwantum
- nincs kategorizálva Safescan
- nincs kategorizálva Pyle Pro
- nincs kategorizálva Transcend
- nincs kategorizálva Wehkamp
- nincs kategorizálva Profoon
- nincs kategorizálva Svedbergs
- nincs kategorizálva Osprey
- nincs kategorizálva Bunn
- nincs kategorizálva Ninebot
- nincs kategorizálva Siedle
- nincs kategorizálva Cilio
- nincs kategorizálva LaCie
- nincs kategorizálva Itho-Daalderop
- nincs kategorizálva Maul
- nincs kategorizálva BabyOno
- nincs kategorizálva Karibu
- nincs kategorizálva Pericles
- nincs kategorizálva Troy-Bilt
- nincs kategorizálva Asaklitt
- nincs kategorizálva Rusta
- nincs kategorizálva Samac
- nincs kategorizálva Waterpik
- nincs kategorizálva SMA
- nincs kategorizálva Kayser
- nincs kategorizálva Autotek
- nincs kategorizálva Safety 1st
- nincs kategorizálva Evga
- nincs kategorizálva Hive
- nincs kategorizálva Brabantia
- nincs kategorizálva Fissler
- nincs kategorizálva Kayoba
- nincs kategorizálva Lexmark
- nincs kategorizálva Inkbird
- nincs kategorizálva Valcom
- nincs kategorizálva Goobay
- nincs kategorizálva Switel
- nincs kategorizálva Hager
- nincs kategorizálva Michelin
- nincs kategorizálva Bopita
- nincs kategorizálva Challenge
- nincs kategorizálva Duux
- nincs kategorizálva Imetec
- nincs kategorizálva Salta
- nincs kategorizálva InFocus
- nincs kategorizálva Bigben
- nincs kategorizálva Playseat
- nincs kategorizálva Topcraft
- nincs kategorizálva Kraftwerk
- nincs kategorizálva Naish
- nincs kategorizálva Festo
- nincs kategorizálva Olivetti
- nincs kategorizálva Massive
- nincs kategorizálva Barska
- nincs kategorizálva Weihrauch Sport
- nincs kategorizálva Blaze
- nincs kategorizálva Hombli
- nincs kategorizálva Martha Stewart
- nincs kategorizálva Lümme
- nincs kategorizálva Springfree
- nincs kategorizálva Ansco
- nincs kategorizálva Goodram
- nincs kategorizálva MADE
- nincs kategorizálva Noma
- nincs kategorizálva IDance
- nincs kategorizálva Habitat
- nincs kategorizálva Maxview
- nincs kategorizálva Yongnuo
- nincs kategorizálva Boso
- nincs kategorizálva Gamma
- nincs kategorizálva Elite
- nincs kategorizálva BOHLT
- nincs kategorizálva Handicare
- nincs kategorizálva Primo
- nincs kategorizálva Rocketfish
- nincs kategorizálva Little Tikes
- nincs kategorizálva Laser
- nincs kategorizálva Creda
- nincs kategorizálva Alba
- nincs kategorizálva Clas Ohlson
- nincs kategorizálva Baninni
- nincs kategorizálva Naxa
- nincs kategorizálva Nemef
- nincs kategorizálva RugGear
- nincs kategorizálva Umidigi
- nincs kategorizálva Saro
- nincs kategorizálva Vogue
- nincs kategorizálva Grixx
- nincs kategorizálva SuperFish
- nincs kategorizálva Luvion
- nincs kategorizálva Aqua Joe
- nincs kategorizálva Innovaphone
- nincs kategorizálva Intel
- nincs kategorizálva Zuiver
- nincs kategorizálva Fantec
- nincs kategorizálva Intermec
- nincs kategorizálva Active Era
- nincs kategorizálva Trigano
- nincs kategorizálva Sweex
- nincs kategorizálva Busch And Müller
- nincs kategorizálva Ices
- nincs kategorizálva Reer
- nincs kategorizálva Vizio
- nincs kategorizálva Cello
- nincs kategorizálva RDL
- nincs kategorizálva Austrian Audio
- nincs kategorizálva Vakoss
- nincs kategorizálva Eberspacher
- nincs kategorizálva Kress
- nincs kategorizálva Hobby
- nincs kategorizálva Zehnder
- nincs kategorizálva Laurastar
- nincs kategorizálva Mx Onda
- nincs kategorizálva Zenit
- nincs kategorizálva Wacker Neuson
- nincs kategorizálva Nûby
- nincs kategorizálva EVE
- nincs kategorizálva Xterra
- nincs kategorizálva Fredenstein
- nincs kategorizálva Playmobil
- nincs kategorizálva Invacare
- nincs kategorizálva Napoleon
- nincs kategorizálva Metronic
- nincs kategorizálva Nanni
- nincs kategorizálva Fuji
- nincs kategorizálva Swissonic
- nincs kategorizálva Schütte
- nincs kategorizálva BRIO
- nincs kategorizálva Aruba
- nincs kategorizálva Waeco
- nincs kategorizálva Natec
- nincs kategorizálva RGV
- nincs kategorizálva Ikan
- nincs kategorizálva Elkay
- nincs kategorizálva IHealth
- nincs kategorizálva Hapro
- nincs kategorizálva Tamiya
- nincs kategorizálva Logicom
- nincs kategorizálva Alfen
- nincs kategorizálva Sound Machines
- nincs kategorizálva Team
- nincs kategorizálva Nikkei
- nincs kategorizálva Petsafe
- nincs kategorizálva TranzX
- nincs kategorizálva Aviom
- nincs kategorizálva UPM
- nincs kategorizálva BABY Born
- nincs kategorizálva Duro
- nincs kategorizálva T'nB
- nincs kategorizálva Ematic
- nincs kategorizálva Palm
- nincs kategorizálva QSC
- nincs kategorizálva Phonak
- nincs kategorizálva Emporia
- nincs kategorizálva Faber
- nincs kategorizálva Cardiostrong
- nincs kategorizálva Hartan
- nincs kategorizálva Xavax
- nincs kategorizálva Emmaljunga
- nincs kategorizálva Tracer
- nincs kategorizálva ZAZU
- nincs kategorizálva Crosscall
- nincs kategorizálva Countryman
- nincs kategorizálva Minolta
- nincs kategorizálva Aerial
- nincs kategorizálva Navman
- nincs kategorizálva Prime3
- nincs kategorizálva Silver Cross
- nincs kategorizálva Victor
- nincs kategorizálva Zagg
- nincs kategorizálva ESI
- nincs kategorizálva Blumfeldt
- nincs kategorizálva Edgestar
- nincs kategorizálva Orbis
- nincs kategorizálva ACE
- nincs kategorizálva Maxicool
- nincs kategorizálva For_Q
- nincs kategorizálva Schaudt
- nincs kategorizálva Avocor
- nincs kategorizálva Lanzar
- nincs kategorizálva DoorBird
- nincs kategorizálva KDK
- nincs kategorizálva FoodSaver
- nincs kategorizálva Vroomshoop
- nincs kategorizálva SureFlap
- nincs kategorizálva GVM
- nincs kategorizálva McGregor
- nincs kategorizálva Nvidia
- nincs kategorizálva Irritrol
- nincs kategorizálva Basbau
- nincs kategorizálva Exit
- nincs kategorizálva CaterChef
- nincs kategorizálva Kasda
- nincs kategorizálva Veho
- nincs kategorizálva Kambrook
- nincs kategorizálva Nevadent
- nincs kategorizálva Plum
- nincs kategorizálva Simrad
- nincs kategorizálva Cellular Line
- nincs kategorizálva Puky
- nincs kategorizálva GFI System
- nincs kategorizálva Humax
- nincs kategorizálva Vaddio
- nincs kategorizálva Berner
- nincs kategorizálva Swarovski Optik
- nincs kategorizálva Gira
- nincs kategorizálva Jung
- nincs kategorizálva Sachtler
- nincs kategorizálva Seagate
- nincs kategorizálva Golden Age Project
- nincs kategorizálva Harvia
- nincs kategorizálva Spin Master
- nincs kategorizálva Bravilor Bonamat
- nincs kategorizálva Blue
- nincs kategorizálva Brinsea
- nincs kategorizálva Genexis
- nincs kategorizálva Genelec
- nincs kategorizálva Maxxter
- nincs kategorizálva Inspire
- nincs kategorizálva Apart
- nincs kategorizálva Venta
- nincs kategorizálva Cadac
- nincs kategorizálva Anchor Audio
- nincs kategorizálva 4moms
- nincs kategorizálva Dantherm
- nincs kategorizálva Interlogix
- nincs kategorizálva Dnt
- nincs kategorizálva Eizo
- nincs kategorizálva Krontaler
- nincs kategorizálva Lyman
- nincs kategorizálva Etekcity
- nincs kategorizálva Genaray
- nincs kategorizálva Balance
- nincs kategorizálva Qualcast
- nincs kategorizálva Cablexpert
- nincs kategorizálva Iomega
- nincs kategorizálva Phil And Teds
- nincs kategorizálva Tornado
- nincs kategorizálva Baby Jogger
- nincs kategorizálva Velux
- nincs kategorizálva Stelton
- nincs kategorizálva Mr Handsfree
- nincs kategorizálva Joovy
- nincs kategorizálva Sommer
- nincs kategorizálva Bodum
- nincs kategorizálva Saitek
- nincs kategorizálva DAS Audio
- nincs kategorizálva Vestfrost
- nincs kategorizálva Leen Bakker
- nincs kategorizálva Eventide
- nincs kategorizálva Audio Pro
- nincs kategorizálva OSO
- nincs kategorizálva Vermeiren
- nincs kategorizálva Kunft
- nincs kategorizálva Radial Engineering
- nincs kategorizálva Fito
- nincs kategorizálva Jotul
- nincs kategorizálva Shoprider
- nincs kategorizálva WHALE
- nincs kategorizálva Shuttle
- nincs kategorizálva Furuno
- nincs kategorizálva Max
- nincs kategorizálva Clage
- nincs kategorizálva Tetra
- nincs kategorizálva Noveen
- nincs kategorizálva Dualit
- nincs kategorizálva Cre8audio
- nincs kategorizálva Nanlite
- nincs kategorizálva Kupper
- nincs kategorizálva Bluesound
- nincs kategorizálva Ledger
- nincs kategorizálva Koenig
- nincs kategorizálva Contour
- nincs kategorizálva BakkerElkhuizen
- nincs kategorizálva Lupilu
- nincs kategorizálva Outdoorchef
- nincs kategorizálva Boyo
- nincs kategorizálva IKRA
- nincs kategorizálva Fakir
- nincs kategorizálva IOttie
- nincs kategorizálva Digi
- nincs kategorizálva Verizon
- nincs kategorizálva XPG
- nincs kategorizálva Valco Baby
- nincs kategorizálva Trio Lighting
- nincs kategorizálva Integra
- nincs kategorizálva Upo
- nincs kategorizálva Vitamix
- nincs kategorizálva Blade
- nincs kategorizálva Rio
- nincs kategorizálva Cadel
- nincs kategorizálva ThinkFun
- nincs kategorizálva Revox
- nincs kategorizálva Emtec
- nincs kategorizálva Ranex
- nincs kategorizálva Truper
- nincs kategorizálva ISDT
- nincs kategorizálva Abac
- nincs kategorizálva Celly
- nincs kategorizálva Comica
- nincs kategorizálva Globo
- nincs kategorizálva ZLine
- nincs kategorizálva Fusion
- nincs kategorizálva Audient
- nincs kategorizálva Adesso
- nincs kategorizálva Paradigm
- nincs kategorizálva C3
- nincs kategorizálva EMSA
- nincs kategorizálva Natuzzi
- nincs kategorizálva Grunkel
- nincs kategorizálva Satel
- nincs kategorizálva Bazooka
- nincs kategorizálva PAX
- nincs kategorizálva K&K Sound
- nincs kategorizálva Dutchbone
- nincs kategorizálva Noise Engineering
- nincs kategorizálva PAC
- nincs kategorizálva Beretta
- nincs kategorizálva Wentronic
- nincs kategorizálva Peerless
- nincs kategorizálva RAVPower
- nincs kategorizálva Hooker
- nincs kategorizálva IHome
- nincs kategorizálva Atomos
- nincs kategorizálva Luxman
- nincs kategorizálva Gitzo
- nincs kategorizálva SeaLife
- nincs kategorizálva Nesco
- nincs kategorizálva Wago
- nincs kategorizálva AIC
- nincs kategorizálva Brydge
- nincs kategorizálva Selec
- nincs kategorizálva Aiphone
- nincs kategorizálva Tivoli Audio
- nincs kategorizálva Senal
- nincs kategorizálva JETI
- nincs kategorizálva Waves
- nincs kategorizálva EQ3
- nincs kategorizálva Karlik
- nincs kategorizálva Comark
- nincs kategorizálva Lervia
- nincs kategorizálva Coline
- nincs kategorizálva N8WERK
- nincs kategorizálva Petri
- nincs kategorizálva Calex
- nincs kategorizálva Satechi
- nincs kategorizálva Skullcandy
- nincs kategorizálva Hansgrohe
- nincs kategorizálva Masport
- nincs kategorizálva 4smarts
- nincs kategorizálva Learning Resources
- nincs kategorizálva Xaoc
- nincs kategorizálva Beyerdynamic
- nincs kategorizálva SVAT
- nincs kategorizálva Qute
- nincs kategorizálva BabyGO
- nincs kategorizálva Schwinn
- nincs kategorizálva Lanberg
- nincs kategorizálva Friedland
- nincs kategorizálva Megableu
- nincs kategorizálva Nexxt
- nincs kategorizálva Coleman
- nincs kategorizálva Bora
- nincs kategorizálva Magic Care
- nincs kategorizálva Raclet
- nincs kategorizálva Butler
- nincs kategorizálva Weishaupt
- nincs kategorizálva Glock
- nincs kategorizálva Linn
- nincs kategorizálva Iluv
- nincs kategorizálva REMKO
- nincs kategorizálva Monoprice
- nincs kategorizálva Ibiza Sound
- nincs kategorizálva Echo
- nincs kategorizálva Croozer
- nincs kategorizálva TELEX
- nincs kategorizálva Dynamic
- nincs kategorizálva Promethean
- nincs kategorizálva HyperIce
- nincs kategorizálva Home Easy
- nincs kategorizálva Basil
- nincs kategorizálva Munchkin
- nincs kategorizálva Vitalmaxx
- nincs kategorizálva Nxg
- nincs kategorizálva AGM
- nincs kategorizálva Bruder Mannesmann
- nincs kategorizálva Autodesk
- nincs kategorizálva Diana
- nincs kategorizálva Tandberg Data
- nincs kategorizálva Fostex
- nincs kategorizálva Viridian
- nincs kategorizálva Plustek
- nincs kategorizálva Prowise
- nincs kategorizálva Mousetrapper
- nincs kategorizálva SKROSS
- nincs kategorizálva Sikkens
- nincs kategorizálva DEXP
- nincs kategorizálva GolfBuddy
- nincs kategorizálva Lynx
- nincs kategorizálva Thermor
- nincs kategorizálva NodOn
- nincs kategorizálva Endorphin.es
- nincs kategorizálva Deutz
- nincs kategorizálva Optimum
- nincs kategorizálva FIMI
- nincs kategorizálva Jilong
- nincs kategorizálva MIPRO
- nincs kategorizálva Bravilor
- nincs kategorizálva Bracketron
- nincs kategorizálva Solid State Logic
- nincs kategorizálva Pointer
- nincs kategorizálva XYZprinting
- nincs kategorizálva Edision
- nincs kategorizálva Carmen
- nincs kategorizálva MTM
- nincs kategorizálva X-Sense
- nincs kategorizálva De Buyer
- nincs kategorizálva Metapace
- nincs kategorizálva Exo-Terra
- nincs kategorizálva Neets
- nincs kategorizálva OutNowTech
- nincs kategorizálva NAV-TV
- nincs kategorizálva Wooden Camera
- nincs kategorizálva Maclaren
- nincs kategorizálva AdHoc
- nincs kategorizálva AudioQuest
- nincs kategorizálva Powerblade
- nincs kategorizálva HiFi ROSE
- nincs kategorizálva Hayter
- nincs kategorizálva Pinolino
- nincs kategorizálva OSD Audio
- nincs kategorizálva WMD
- nincs kategorizálva Andover
- nincs kategorizálva Simpark
- nincs kategorizálva Beafon
- nincs kategorizálva Maruyama
- nincs kategorizálva 3B
- nincs kategorizálva FABER CASTELL
- nincs kategorizálva Ergotron
- nincs kategorizálva Stairville
- nincs kategorizálva Giordani
- nincs kategorizálva RME
- nincs kategorizálva Black Lion Audio
- nincs kategorizálva Cowon
- nincs kategorizálva Soundstream
- nincs kategorizálva Crayola
- nincs kategorizálva Xoro
- nincs kategorizálva Medel
- nincs kategorizálva REVITIVE
- nincs kategorizálva Maze
- nincs kategorizálva CTOUCH
- nincs kategorizálva Adastra
- nincs kategorizálva Meister Craft
- nincs kategorizálva Meade
- nincs kategorizálva Perkins
- nincs kategorizálva Sagemcom
- nincs kategorizálva Yeastar
- nincs kategorizálva Laserworld
- nincs kategorizálva Billow
- nincs kategorizálva Chuango
- nincs kategorizálva Kelty
- nincs kategorizálva West Elm
- nincs kategorizálva Block
- nincs kategorizálva Ozone
- nincs kategorizálva Klavis
- nincs kategorizálva Clearblue
- nincs kategorizálva Garden Lights
- nincs kategorizálva ETiger
- nincs kategorizálva Bison
- nincs kategorizálva Jabsco
- nincs kategorizálva Foxconn
- nincs kategorizálva Icy Dock
- nincs kategorizálva Wasco
- nincs kategorizálva Baby Brezza
- nincs kategorizálva Make Noise
- nincs kategorizálva Telstra
- nincs kategorizálva TeachLogic
- nincs kategorizálva ASSA ABLOY
- nincs kategorizálva Lumag
- nincs kategorizálva Charge Amps
- nincs kategorizálva Berker
- nincs kategorizálva Eufab
- nincs kategorizálva Crucial
- nincs kategorizálva Snom
- nincs kategorizálva RIDGID
- nincs kategorizálva Premier
- nincs kategorizálva Aeon Labs
- nincs kategorizálva Ibm
- nincs kategorizálva Unilux
- nincs kategorizálva Shokz
- nincs kategorizálva Citronic
- nincs kategorizálva TEF
- nincs kategorizálva Cosatto
- nincs kategorizálva Weasy
- nincs kategorizálva Aerotec
- nincs kategorizálva Atlas
- nincs kategorizálva Datacard
- nincs kategorizálva Nordea
- nincs kategorizálva Life Gear
- nincs kategorizálva ZYCOO
- nincs kategorizálva Macrom
- nincs kategorizálva Kontakt Chemie
- nincs kategorizálva Purell
- nincs kategorizálva Riccar
- nincs kategorizálva BabyHome
- nincs kategorizálva Contax
- nincs kategorizálva OpenVox
- nincs kategorizálva Atdec
- nincs kategorizálva Batavia
- nincs kategorizálva Klarfit
- nincs kategorizálva Gutfels
- nincs kategorizálva Bruynzeel
- nincs kategorizálva MSpa
- nincs kategorizálva View Quest
- nincs kategorizálva Drayton
- nincs kategorizálva Formuler
- nincs kategorizálva Sonnet
- nincs kategorizálva Oertli
- nincs kategorizálva UX
- nincs kategorizálva Moog
- nincs kategorizálva Nerf
- nincs kategorizálva KidKraft
- nincs kategorizálva Westfalia
- nincs kategorizálva Metrel
- nincs kategorizálva Solid
- nincs kategorizálva NUK
- nincs kategorizálva Morris
- nincs kategorizálva Ruger
- nincs kategorizálva Hubelino
- nincs kategorizálva Aputure
- nincs kategorizálva Gerni
- nincs kategorizálva Jupio
- nincs kategorizálva MedFolio
- nincs kategorizálva Baby Annabell
- nincs kategorizálva Blaser
- nincs kategorizálva Heatit
- nincs kategorizálva Endress
- nincs kategorizálva ProForm
- nincs kategorizálva UTEPO
- nincs kategorizálva Purpleline
- nincs kategorizálva Lindell Audio
- nincs kategorizálva Max Pro
- nincs kategorizálva Think Tank
- nincs kategorizálva Portech
- nincs kategorizálva Twelve South
- nincs kategorizálva Lec
- nincs kategorizálva Geomag
- nincs kategorizálva LTC
- nincs kategorizálva Koala
- nincs kategorizálva Drawmer
- nincs kategorizálva Audeze
- nincs kategorizálva Blue Sky
- nincs kategorizálva Valeo
- nincs kategorizálva Noxon
- nincs kategorizálva Woonexpress
- nincs kategorizálva IQAir
- nincs kategorizálva Sanus Systems
- nincs kategorizálva BabyDan
- nincs kategorizálva ColorKey
- nincs kategorizálva Tormatic
- nincs kategorizálva After Later Audio
- nincs kategorizálva Verbatim
- nincs kategorizálva 2hp
- nincs kategorizálva Energizer
- nincs kategorizálva IXS
- nincs kategorizálva Samlex
- nincs kategorizálva Navionics
- nincs kategorizálva AirTurn
- nincs kategorizálva Zalman
- nincs kategorizálva Zega
- nincs kategorizálva Leatherman
- nincs kategorizálva CreativeWorKs
- nincs kategorizálva Ultimate Support
- nincs kategorizálva Rösle
- nincs kategorizálva Prince
- nincs kategorizálva AXI
- nincs kategorizálva EMG
- nincs kategorizálva James
- nincs kategorizálva Bicker Elektronik
- nincs kategorizálva Iadea
- nincs kategorizálva Nimble
- nincs kategorizálva Reginox
- nincs kategorizálva BIOS Medical
- nincs kategorizálva Advantech
- nincs kategorizálva PSSO
- nincs kategorizálva Wise
- nincs kategorizálva SIG Sauer
- nincs kategorizálva Merkel
- nincs kategorizálva Patching Panda
- nincs kategorizálva Harley Benton
- nincs kategorizálva Crest Audio
- nincs kategorizálva Globe
- nincs kategorizálva Rossi
- nincs kategorizálva Hercules
- nincs kategorizálva Contour Design
- nincs kategorizálva Propellerhead
- nincs kategorizálva Nanuk
- nincs kategorizálva Digital Watchdog
- nincs kategorizálva Sonifex
- nincs kategorizálva Riviera And Bar
- nincs kategorizálva Kreiling
- nincs kategorizálva Xantech
- nincs kategorizálva Marker
- nincs kategorizálva Kohler
- nincs kategorizálva Safco
- nincs kategorizálva Xunzel
- nincs kategorizálva Oklahoma Sound
- nincs kategorizálva Thames & Kosmos
- nincs kategorizálva Betso
- nincs kategorizálva Fortia
- nincs kategorizálva Moen
- nincs kategorizálva Babysense
- nincs kategorizálva Namco Bandai Games
- nincs kategorizálva Sealy
- nincs kategorizálva Ferguson
- nincs kategorizálva Wet Sounds
- nincs kategorizálva CRU
- nincs kategorizálva Avantone Pro
- nincs kategorizálva Umarex
- nincs kategorizálva Televés
- nincs kategorizálva AbleNet
- nincs kategorizálva Exalux
- nincs kategorizálva IBasso
- nincs kategorizálva Sole Fitness
- nincs kategorizálva Leap Frog
- nincs kategorizálva Sightmark
- nincs kategorizálva Eissound
- nincs kategorizálva Ganz
- nincs kategorizálva Manley
- nincs kategorizálva Micro Matic
- nincs kategorizálva Thermomate
- nincs kategorizálva Steiner
- nincs kategorizálva Acard
- nincs kategorizálva Burigotto
- nincs kategorizálva Redmond
- nincs kategorizálva Sencys
- nincs kategorizálva Norton Clipper
- nincs kategorizálva Extron
- nincs kategorizálva Avocent
- nincs kategorizálva Geze
- nincs kategorizálva RTS
- nincs kategorizálva Ontech
- nincs kategorizálva HyperJuice
- nincs kategorizálva Koss
- nincs kategorizálva Swingline
- nincs kategorizálva Kwikset
- nincs kategorizálva Infomir
- nincs kategorizálva RaySafe
- nincs kategorizálva Di4
- nincs kategorizálva Hohner
- nincs kategorizálva Dahle
- nincs kategorizálva Sanli
- nincs kategorizálva Shelly
- nincs kategorizálva Husky
- nincs kategorizálva Philos
- nincs kategorizálva Siemon
- nincs kategorizálva Block & Block
- nincs kategorizálva Brondell
- nincs kategorizálva NutriBullet
- nincs kategorizálva Four Hands
- nincs kategorizálva Oben
- nincs kategorizálva ASA
- nincs kategorizálva Vantec
- nincs kategorizálva Thronmax
- nincs kategorizálva Axkid
- nincs kategorizálva Botex
- nincs kategorizálva Intellinet
- nincs kategorizálva Maxsa
- nincs kategorizálva Tripp
- nincs kategorizálva TRIUS
- nincs kategorizálva Ankarsrum
- nincs kategorizálva MTD
- nincs kategorizálva Etymotic
- nincs kategorizálva Fine Dine
- nincs kategorizálva ClearOne
- nincs kategorizálva Heidemann
- nincs kategorizálva OneTouch
- nincs kategorizálva Superrollo
- nincs kategorizálva Goldtouch
- nincs kategorizálva Gamewright
- nincs kategorizálva Kerbl
- nincs kategorizálva Braun Phototechnik
- nincs kategorizálva Black Decker
- nincs kategorizálva Muller
- nincs kategorizálva SXT
- nincs kategorizálva Essenza
- nincs kategorizálva Seecode
- nincs kategorizálva Rugged Geek
- nincs kategorizálva Nubert
- nincs kategorizálva Dave Smith
- nincs kategorizálva Skymaster
- nincs kategorizálva Dorr
- nincs kategorizálva Gardol
- nincs kategorizálva Helix
- nincs kategorizálva TFA Dostmann
- nincs kategorizálva Werma
- nincs kategorizálva Durable
- nincs kategorizálva Zenza Bronica
- nincs kategorizálva Spypoint
- nincs kategorizálva Suprema
- nincs kategorizálva Ziehl
- nincs kategorizálva VAIS
- nincs kategorizálva Perma
- nincs kategorizálva Scandes
- nincs kategorizálva Enovate
- nincs kategorizálva Lofrans
- nincs kategorizálva Winegard
- nincs kategorizálva Pigtronix
- nincs kategorizálva ProTeam
- nincs kategorizálva Wagner SprayTech
- nincs kategorizálva Libec
- nincs kategorizálva Pardini
- nincs kategorizálva KWC
- nincs kategorizálva Soul
- nincs kategorizálva Laney
- nincs kategorizálva Compex
- nincs kategorizálva Theragun
- nincs kategorizálva Weil
- nincs kategorizálva Plantiflor
- nincs kategorizálva LAS
- nincs kategorizálva Rosseto
- nincs kategorizálva Redrock Micro
- nincs kategorizálva Motu
- nincs kategorizálva Kata
- nincs kategorizálva Minix
- nincs kategorizálva Lazer
- nincs kategorizálva EarthQuaker Devices
- nincs kategorizálva The Grainfather
- nincs kategorizálva Kessler
- nincs kategorizálva Emga
- nincs kategorizálva Devialet
- nincs kategorizálva Briggs & Stratton
- nincs kategorizálva USAopoly
- nincs kategorizálva Gami
- nincs kategorizálva Igloohome
- nincs kategorizálva Kenko
- nincs kategorizálva Zennio
- nincs kategorizálva Vixen
- nincs kategorizálva B-tech
- nincs kategorizálva Praktica
- nincs kategorizálva Elinchrom
- nincs kategorizálva Boori
- nincs kategorizálva CamRanger
- nincs kategorizálva ETON
- nincs kategorizálva Hasselblad
- nincs kategorizálva Madrix
- nincs kategorizálva Q Acoustics
- nincs kategorizálva Spacedec
- nincs kategorizálva Auray
- nincs kategorizálva Bontempi
- nincs kategorizálva Furman
- nincs kategorizálva Summer Infant
- nincs kategorizálva Cooper & Quint
- nincs kategorizálva Deltex
- nincs kategorizálva Adax
- nincs kategorizálva Xplora
- nincs kategorizálva Buzz Rack
- nincs kategorizálva Cruz
- nincs kategorizálva Eonon
- nincs kategorizálva SMC
- nincs kategorizálva Ibico
- nincs kategorizálva OXO Good Grips
- nincs kategorizálva Exit Toys
- nincs kategorizálva Triton
- nincs kategorizálva Profizelt24
- nincs kategorizálva Helios Preisser
- nincs kategorizálva YSI
- nincs kategorizálva Yeyian
- nincs kategorizálva Paulmann
- nincs kategorizálva Nitek
- nincs kategorizálva Snoes
- nincs kategorizálva Alpatronix
- nincs kategorizálva Labelmate
- nincs kategorizálva Martin Audio
- nincs kategorizálva Schertler
- nincs kategorizálva Teradek
- nincs kategorizálva Sissel
- nincs kategorizálva Kunath
- nincs kategorizálva Penclic
- nincs kategorizálva Escort
- nincs kategorizálva ViewCast
- nincs kategorizálva Crown
- nincs kategorizálva Wolfcraft
- nincs kategorizálva Tennsco
- nincs kategorizálva FireKing
- nincs kategorizálva RAM Mounts
- nincs kategorizálva Novus
- nincs kategorizálva Arebos
- nincs kategorizálva Kreg
- nincs kategorizálva Bentley
- nincs kategorizálva Morningstar
- nincs kategorizálva DMax
- nincs kategorizálva Backyard Discovery
- nincs kategorizálva Minuteman
- nincs kategorizálva Ortofon
- nincs kategorizálva RéVive
- nincs kategorizálva Star Micronics
- nincs kategorizálva Tamron
- nincs kategorizálva Woodland Scenics
- nincs kategorizálva Chapin
- nincs kategorizálva J. Rockett Audio Designs
- nincs kategorizálva Satisfyer
- nincs kategorizálva Hämmerli
- nincs kategorizálva Verto
- nincs kategorizálva Soma
- nincs kategorizálva SRS
- nincs kategorizálva Point 65
- nincs kategorizálva ReTrak
- nincs kategorizálva Avantree
- nincs kategorizálva Akuvox
- nincs kategorizálva LYYT
- nincs kategorizálva Old Blood Noise
- nincs kategorizálva Vulcan
- nincs kategorizálva CradlePoint
- nincs kategorizálva Catalyst
- nincs kategorizálva Antelope Audio
- nincs kategorizálva Brinno
- nincs kategorizálva Venom
- nincs kategorizálva CE Labs
- nincs kategorizálva Legrand
- nincs kategorizálva Z CAM
- nincs kategorizálva Digium
- nincs kategorizálva Giardino
- nincs kategorizálva Mulex
- nincs kategorizálva Socomec
- nincs kategorizálva System Sensor
- nincs kategorizálva San Jamar
- nincs kategorizálva Fiskars
- nincs kategorizálva IPort
- nincs kategorizálva X-Rite
- nincs kategorizálva Wetelux
- nincs kategorizálva Talkaphone
- nincs kategorizálva Merax
- nincs kategorizálva GermGuardian
- nincs kategorizálva R-Go Tools
- nincs kategorizálva Urbanista
- nincs kategorizálva SLV
- nincs kategorizálva Sagitter
- nincs kategorizálva Rainbow
- nincs kategorizálva Riello
- nincs kategorizálva Gagato
- nincs kategorizálva Traeger
- nincs kategorizálva General
- nincs kategorizálva Ooni
- nincs kategorizálva ECTIVE
- nincs kategorizálva Gymform
- nincs kategorizálva Tzumi
- nincs kategorizálva BERTSCHAT
- nincs kategorizálva Schumacher
- nincs kategorizálva Michael Todd Beauty
- nincs kategorizálva Cygnett
- nincs kategorizálva Germania
- nincs kategorizálva Victorio
- nincs kategorizálva Platinum
- nincs kategorizálva Trimble
- nincs kategorizálva Playtive Junior
- nincs kategorizálva Parklands
- nincs kategorizálva Avid
- nincs kategorizálva Vipack
- nincs kategorizálva Helios
- nincs kategorizálva EKO
- nincs kategorizálva BIG
- nincs kategorizálva POGS
- nincs kategorizálva Graflex
- nincs kategorizálva Coolaroo
- nincs kategorizálva Wurth
- nincs kategorizálva Mebus
- nincs kategorizálva Gioteck
- nincs kategorizálva Kenton
- nincs kategorizálva Cypress
- nincs kategorizálva Foliatec
- nincs kategorizálva Mauser
- nincs kategorizálva Silhouette
- nincs kategorizálva South Shore
- nincs kategorizálva Discovery
- nincs kategorizálva T4E
- nincs kategorizálva Speck
- nincs kategorizálva Generation
- nincs kategorizálva Iseki
- nincs kategorizálva MOZA
- nincs kategorizálva Ecler
- nincs kategorizálva Turbosound
- nincs kategorizálva Phase One
- nincs kategorizálva Little Giant
- nincs kategorizálva Röhm
- nincs kategorizálva Ulanzi
- nincs kategorizálva Anova
- nincs kategorizálva Viscount
- nincs kategorizálva Khind
- nincs kategorizálva DAB
- nincs kategorizálva Anex
- nincs kategorizálva LERAN
- nincs kategorizálva Majella
- nincs kategorizálva GMB Audio
- nincs kategorizálva Ashdown Engineering
- nincs kategorizálva Century
- nincs kategorizálva Unger
- nincs kategorizálva Inverto
- nincs kategorizálva Special-T
- nincs kategorizálva Ygnis
- nincs kategorizálva Esotec
- nincs kategorizálva True & Tidy
- nincs kategorizálva Petkit
- nincs kategorizálva Icon
- nincs kategorizálva Fuzzix
- nincs kategorizálva Kitchen Brains
- nincs kategorizálva Best
- nincs kategorizálva NetAlly
- nincs kategorizálva Triax
- nincs kategorizálva Peltor
- nincs kategorizálva JAR Systems
- nincs kategorizálva Moleskine
- nincs kategorizálva Bytecc
- nincs kategorizálva Strex
- nincs kategorizálva Xlyne
- nincs kategorizálva Premier Mounts
- nincs kategorizálva One Stop Systems
- nincs kategorizálva Cool Maker
- nincs kategorizálva Neo
- nincs kategorizálva EVOline
- nincs kategorizálva Mtx Audio
- nincs kategorizálva Ursus Trotter
- nincs kategorizálva DoughXpress
- nincs kategorizálva Aquatic AV
- nincs kategorizálva Parasound
- nincs kategorizálva MSR
- nincs kategorizálva Cabstone
- nincs kategorizálva SPT
- nincs kategorizálva DB Technologies
- nincs kategorizálva T.I.P.
- nincs kategorizálva Promate
- nincs kategorizálva Berger & Schröter
- nincs kategorizálva Tru Components
- nincs kategorizálva Step2
- nincs kategorizálva Dension
- nincs kategorizálva Crystal Quest
- nincs kategorizálva Pit Boss
- nincs kategorizálva Needit
- nincs kategorizálva MiPow
- nincs kategorizálva GoldenEar Technology
- nincs kategorizálva Colt
- nincs kategorizálva Elite Screens
- nincs kategorizálva Quadro
- nincs kategorizálva Ultron
- nincs kategorizálva Choice
- nincs kategorizálva Roswell
- nincs kategorizálva King Craft
- nincs kategorizálva FOX ESS
- nincs kategorizálva Airman
- nincs kategorizálva Cascade Audio Engineering
- nincs kategorizálva B-Speech
- nincs kategorizálva Vanish
- nincs kategorizálva Nostalgia
- nincs kategorizálva Grosfillex
- nincs kategorizálva Beemoo
- nincs kategorizálva Platinet
- nincs kategorizálva Santos
- nincs kategorizálva Entes
- nincs kategorizálva Evoc
- nincs kategorizálva Versare
- nincs kategorizálva Enphase
- nincs kategorizálva SpeakerCraft
- nincs kategorizálva Epcom
- nincs kategorizálva ZeeVee
- nincs kategorizálva Siku
- nincs kategorizálva Viatek
- nincs kategorizálva Simplicity
- nincs kategorizálva Doomoo
- nincs kategorizálva MBZ
- nincs kategorizálva Davey
- nincs kategorizálva Mettler
- nincs kategorizálva Metalux
- nincs kategorizálva Heitech
- nincs kategorizálva Potenza
- nincs kategorizálva LOQED
- nincs kategorizálva Hatco
- nincs kategorizálva KONFTEL
- nincs kategorizálva Canicom
- nincs kategorizálva Mitsai
- nincs kategorizálva Selfsat
- nincs kategorizálva Leef
- nincs kategorizálva Tusa
- nincs kategorizálva Hovicon
- nincs kategorizálva American BioTech Supply
- nincs kategorizálva Noris
- nincs kategorizálva KS Tools
- nincs kategorizálva Koliber
- nincs kategorizálva Schmidt & Bender
- nincs kategorizálva Mesa Boogie
- nincs kategorizálva Improv
- nincs kategorizálva LandRoller
- nincs kategorizálva Wegman
- nincs kategorizálva Lockncharge
- nincs kategorizálva Merlin
- nincs kategorizálva Standard Horizon
- nincs kategorizálva Goal Zero
- nincs kategorizálva HealthPostures
- nincs kategorizálva Dreadbox
- nincs kategorizálva Joranalogue
- nincs kategorizálva CYP
- nincs kategorizálva Heaven Fresh
- nincs kategorizálva Lutec
- nincs kategorizálva Champion Sports
- nincs kategorizálva Molotow
- nincs kategorizálva Herlag
- nincs kategorizálva Dux
- nincs kategorizálva FALLER
- nincs kategorizálva Miditech
- nincs kategorizálva SE Electronics
- nincs kategorizálva TTM
- nincs kategorizálva Paw Patrol
- nincs kategorizálva LELO
- nincs kategorizálva Mermade
- nincs kategorizálva MXR
- nincs kategorizálva SKLZ
- nincs kategorizálva Herma
- nincs kategorizálva BWT
- nincs kategorizálva Syrp
- nincs kategorizálva Ugolini
- nincs kategorizálva Cosina
- nincs kategorizálva Heckler & Koch
- nincs kategorizálva Whistler
- nincs kategorizálva Twisper
- nincs kategorizálva Manitowoc
- nincs kategorizálva Hushmat
- nincs kategorizálva Xigmatek
- nincs kategorizálva Tema
- nincs kategorizálva ALM
- nincs kategorizálva Topaz
- nincs kategorizálva Toddy
- nincs kategorizálva Aicon
- nincs kategorizálva Astell&Kern
- nincs kategorizálva Doepfer
- nincs kategorizálva Fun Generation
- nincs kategorizálva Karma
- nincs kategorizálva TV One
- nincs kategorizálva Berkel
- nincs kategorizálva Hugo Muller
- nincs kategorizálva Vinci
- nincs kategorizálva Jordan
- nincs kategorizálva Duromax
- nincs kategorizálva DataComm
- nincs kategorizálva Powercube
- nincs kategorizálva Kasp
- nincs kategorizálva Dimavery
- nincs kategorizálva Hanwha
- nincs kategorizálva WestBend
- nincs kategorizálva Mr Coffee
- nincs kategorizálva Sherlock
- nincs kategorizálva Sloan
- nincs kategorizálva SEA-PRO
- nincs kategorizálva Omiindustriies
- nincs kategorizálva Weltevree
- nincs kategorizálva Phoenix Contact
- nincs kategorizálva AMS Neve
- nincs kategorizálva LVSUN
- nincs kategorizálva Aston Microphones
- nincs kategorizálva Netsys
- nincs kategorizálva Alfi
- nincs kategorizálva Polarlite
- nincs kategorizálva Companion
- nincs kategorizálva Mr. Beams
- nincs kategorizálva Morphor
- nincs kategorizálva Lapp
- nincs kategorizálva XO
- nincs kategorizálva PcDuino
- nincs kategorizálva LECO
- nincs kategorizálva Maretron
- nincs kategorizálva Hortus
- nincs kategorizálva Razorri
- nincs kategorizálva Fetch
- nincs kategorizálva Zoetis
- nincs kategorizálva Prem-i-air
- nincs kategorizálva NWS
- nincs kategorizálva GAM
- nincs kategorizálva Scale Computing
- nincs kategorizálva Naturn Living
- nincs kategorizálva Aeotec
- nincs kategorizálva Catlink
- nincs kategorizálva FitterFirst
- nincs kategorizálva Raveland
- nincs kategorizálva Mr. Heater
- nincs kategorizálva Welltech
- nincs kategorizálva Trumeter
- nincs kategorizálva Seidio
- nincs kategorizálva Sincreative
- nincs kategorizálva JDC
- nincs kategorizálva Hidrate
- nincs kategorizálva Sonicware
- nincs kategorizálva Nexibo
- nincs kategorizálva Jolin
- nincs kategorizálva MoTip
- nincs kategorizálva Stenda
- nincs kategorizálva Pro-Lift
- nincs kategorizálva HIOAZO
- nincs kategorizálva Malstrom
- nincs kategorizálva Laserluchs
- nincs kategorizálva Powersoft
- nincs kategorizálva Casetastic
- nincs kategorizálva UClear
- nincs kategorizálva BikeLogger
- nincs kategorizálva Tor Rey
- nincs kategorizálva Momo Design
- nincs kategorizálva Esdec
- nincs kategorizálva Ruark Audio
- nincs kategorizálva AJH Synth
- nincs kategorizálva LifeStraw
- nincs kategorizálva Magnavox
- nincs kategorizálva Toolit
- nincs kategorizálva Egnater
- nincs kategorizálva DutchOne
- nincs kategorizálva Feitian
- nincs kategorizálva Ergie
- nincs kategorizálva Reltech
- nincs kategorizálva Guide
- nincs kategorizálva Armcross
- nincs kategorizálva Focus Electrics
- nincs kategorizálva Huntleigh
- nincs kategorizálva Beeletix
- nincs kategorizálva Gehmann
- nincs kategorizálva Batronix
- nincs kategorizálva Franzis
- nincs kategorizálva Gridbyt
- nincs kategorizálva TDK-Lambda
- nincs kategorizálva LONQ
- nincs kategorizálva Em-Trak
- nincs kategorizálva Wonky Monkey
- nincs kategorizálva Dresden Elektronik
- nincs kategorizálva Atmel
- nincs kategorizálva Flavour Blaster
- nincs kategorizálva Esoteric
- nincs kategorizálva SmartAVI
- nincs kategorizálva EPH Elektronik
- nincs kategorizálva Markbass
- nincs kategorizálva IMG Stage Line
- nincs kategorizálva IMAC
- nincs kategorizálva Metz Connect
- nincs kategorizálva MGL Avionics
- nincs kategorizálva Eikon
- nincs kategorizálva Casablanca
- nincs kategorizálva Nemco
- nincs kategorizálva Wireless Solution
- nincs kategorizálva Beverage-Air
- nincs kategorizálva Sparco
- nincs kategorizálva Barber Tech
- nincs kategorizálva Estella
- nincs kategorizálva EarFun
- nincs kategorizálva Oehlbach
- nincs kategorizálva Minkels
- nincs kategorizálva Kipor
- nincs kategorizálva Lenmar
- nincs kategorizálva HMS Premium
- nincs kategorizálva Arduino
- nincs kategorizálva Ave Six
- nincs kategorizálva Bestar
- nincs kategorizálva Pelco
- nincs kategorizálva Gardigo
- nincs kategorizálva Highpoint
- nincs kategorizálva Puls Dimension
- nincs kategorizálva Studiologic
- nincs kategorizálva Fischer Amps
- nincs kategorizálva CHINT
- nincs kategorizálva Sirus
- nincs kategorizálva Digitech
- nincs kategorizálva Leviton
- nincs kategorizálva Gretsch
- nincs kategorizálva Pentacon
- nincs kategorizálva Winia
- nincs kategorizálva Bolsey
- nincs kategorizálva Louis Tellier
- nincs kategorizálva EtiamPro
- nincs kategorizálva Simeo
- nincs kategorizálva Baracuda
- nincs kategorizálva Kstar
- nincs kategorizálva Air Guard
- nincs kategorizálva MediaMatrix
- nincs kategorizálva ESX
- nincs kategorizálva Tuur
- nincs kategorizálva ONE Smart Control
- nincs kategorizálva Edelkrone
- nincs kategorizálva OBSBOT
- nincs kategorizálva InSinkErator
- nincs kategorizálva Omnires
- nincs kategorizálva Elite Force
- nincs kategorizálva JK Audio
- nincs kategorizálva DEHN
- nincs kategorizálva Lifan
- nincs kategorizálva Jomox
- nincs kategorizálva Pentatech
- nincs kategorizálva Burley
- nincs kategorizálva Lexicon
- nincs kategorizálva Icarus Blue
- nincs kategorizálva Command
- nincs kategorizálva IRIS
- nincs kategorizálva Neno
- nincs kategorizálva Starburst
- nincs kategorizálva AVPro Edge
- nincs kategorizálva Fluance
- nincs kategorizálva PCE Instruments
- nincs kategorizálva Garden Place
- nincs kategorizálva Moldex
- nincs kategorizálva MaximaVida
- nincs kategorizálva Firefriend
- nincs kategorizálva LightZone
- nincs kategorizálva Robinhood
- nincs kategorizálva Bliss Outdoors
- nincs kategorizálva Fontiso
- nincs kategorizálva Varytec
- nincs kategorizálva Altra
- nincs kategorizálva Omnilux
- nincs kategorizálva Socket Mobile
- nincs kategorizálva Quartet
- nincs kategorizálva Shadow
- nincs kategorizálva IP-COM
- nincs kategorizálva Calligaris .com
- nincs kategorizálva Comtek
- nincs kategorizálva Fishman
- nincs kategorizálva Tams Elektronik
- nincs kategorizálva Digital Juice
- nincs kategorizálva Eschenbach
- nincs kategorizálva ASM
- nincs kategorizálva Bretford
- nincs kategorizálva Ltech
- nincs kategorizálva Kiev
- nincs kategorizálva RetroSound
- nincs kategorizálva Caroline
- nincs kategorizálva Zomo
- nincs kategorizálva VAIS Technology
- nincs kategorizálva Synco
- nincs kategorizálva Buchla & TipTop Audio
- nincs kategorizálva Pyramid
- nincs kategorizálva Maico
- nincs kategorizálva On-Q
- nincs kategorizálva SetonixSynth
- nincs kategorizálva Horex
- nincs kategorizálva Inno-Hit
- nincs kategorizálva Sime
- nincs kategorizálva AvaValley
- nincs kategorizálva INTIMINA
- nincs kategorizálva Monzana
- nincs kategorizálva FCC BBQ
- nincs kategorizálva Auto XS
- nincs kategorizálva Toomax
- nincs kategorizálva Aqua Marina
- nincs kategorizálva Hameg
- nincs kategorizálva Greemotion
- nincs kategorizálva Winter Modular
- nincs kategorizálva Salewa
- nincs kategorizálva FED
- nincs kategorizálva Synamodec
- nincs kategorizálva Grotime
- nincs kategorizálva Pico Macom
- nincs kategorizálva RadonTec
- nincs kategorizálva Katrin
- nincs kategorizálva Kendau
- nincs kategorizálva Kisag
- nincs kategorizálva NUX
- nincs kategorizálva Coxreels
- nincs kategorizálva Nous
- nincs kategorizálva Overade
- nincs kategorizálva Liemke
- nincs kategorizálva Copco
- nincs kategorizálva Vanson
- nincs kategorizálva Canyon
- nincs kategorizálva Carcomm
- nincs kategorizálva Style Me Up
- nincs kategorizálva Swedish Posture
- nincs kategorizálva Melnor
- nincs kategorizálva CDVI
- nincs kategorizálva Excalibur
- nincs kategorizálva Holman
- nincs kategorizálva HomePilot
- nincs kategorizálva Leaptel
- nincs kategorizálva Lifenaxx
- nincs kategorizálva Powertec
- nincs kategorizálva Waterbird
- nincs kategorizálva Dreambaby
- nincs kategorizálva AOpen
- nincs kategorizálva Angler
- nincs kategorizálva GP
- nincs kategorizálva Akrobat
- nincs kategorizálva Casaria
- nincs kategorizálva Selleys
- nincs kategorizálva WindFall
- nincs kategorizálva Ameristep
- nincs kategorizálva Rikon
- nincs kategorizálva KM-fit
- nincs kategorizálva X Rocker
- nincs kategorizálva Mircom
- nincs kategorizálva ESUN
- nincs kategorizálva Durex
- nincs kategorizálva AeroCool
- nincs kategorizálva Vantage Point
- nincs kategorizálva Jokari
- nincs kategorizálva BeeSecure
- nincs kategorizálva Unicol
- nincs kategorizálva Fisher Paykel
- nincs kategorizálva Lasita Maja
- nincs kategorizálva Meccano
- nincs kategorizálva Parallels
- nincs kategorizálva Oatey
- nincs kategorizálva QUIO
- nincs kategorizálva Fisher
- nincs kategorizálva Gretsch Guitars
- nincs kategorizálva Banoch
- nincs kategorizálva XP-PEN
- nincs kategorizálva Atmotube
- nincs kategorizálva Sun Pumps
- nincs kategorizálva Electrify
- nincs kategorizálva Leatt
- nincs kategorizálva Bleep Labs
- nincs kategorizálva FontaFit
- nincs kategorizálva Gossmann
- nincs kategorizálva Comatec
- nincs kategorizálva Jonard Tools
- nincs kategorizálva Atech Flash Technology
- nincs kategorizálva AutoParkTime
- nincs kategorizálva Hudora
- nincs kategorizálva Facal
- nincs kategorizálva Planet Audio
- nincs kategorizálva Datacolor
- nincs kategorizálva Silicon Power
- nincs kategorizálva Sabrent
- nincs kategorizálva JAXY
- nincs kategorizálva WARN
- nincs kategorizálva Aarke
- nincs kategorizálva TikkTokk
- nincs kategorizálva Roco
- nincs kategorizálva Flexson
- nincs kategorizálva Camec
- nincs kategorizálva Wibrain
- nincs kategorizálva Rolly Toys
- nincs kategorizálva Level Mount
- nincs kategorizálva Teenage Engineering
- nincs kategorizálva Elipson
- nincs kategorizálva STANDIVARIUS
- nincs kategorizálva CommScope
- nincs kategorizálva Videotec
- nincs kategorizálva Orange
- nincs kategorizálva Extralife Instruments
- nincs kategorizálva Genki Instruments
- nincs kategorizálva Industrial Music Electronics
- nincs kategorizálva Mauser Sitzkultur
- nincs kategorizálva Accezz
- nincs kategorizálva A4 Tech
- nincs kategorizálva Full Boar
- nincs kategorizálva Zedar
- nincs kategorizálva Yli Electronic
- nincs kategorizálva Dals
- nincs kategorizálva Bulman
- nincs kategorizálva TOOLMATE
- nincs kategorizálva SleepPro
- nincs kategorizálva Muama
- nincs kategorizálva Lepu Medical
- nincs kategorizálva Michigan
- nincs kategorizálva Beringer
- nincs kategorizálva Waterdrop
- nincs kategorizálva Revamp
- nincs kategorizálva Phonic
- nincs kategorizálva ZCover
- nincs kategorizálva Vasagle
- nincs kategorizálva Aquatica
- nincs kategorizálva Girmi
- nincs kategorizálva Goaliath
- nincs kategorizálva 909 Outdoor
- nincs kategorizálva Viomi
- nincs kategorizálva Grimm Audio
- nincs kategorizálva Better Life
- nincs kategorizálva Dayclocks
- nincs kategorizálva Testec
- nincs kategorizálva Phidgets
- nincs kategorizálva TK Audio
- nincs kategorizálva Hawk-Woods
- nincs kategorizálva Novo
- nincs kategorizálva Commercial Chef
- nincs kategorizálva Novis
- nincs kategorizálva Dexibell
- nincs kategorizálva IsoAcoustics
- nincs kategorizálva Memphis
- nincs kategorizálva Engel
- nincs kategorizálva Clifford
- nincs kategorizálva Cambo
- nincs kategorizálva Hedbox
- nincs kategorizálva Campart
- nincs kategorizálva Lansinoh
- nincs kategorizálva Adviti
- nincs kategorizálva Maclean
- nincs kategorizálva 9.solutions
- nincs kategorizálva Hotone
- nincs kategorizálva WEN
- nincs kategorizálva Trace Elliot
- nincs kategorizálva Lockwood
- nincs kategorizálva Nexera
- nincs kategorizálva Goodway
- nincs kategorizálva BlueDri
- nincs kategorizálva Seenergy
- nincs kategorizálva Meinl
- nincs kategorizálva Analogis
- nincs kategorizálva BBQ Premium
- nincs kategorizálva Stäubli
- nincs kategorizálva RAB
- nincs kategorizálva Schabus
- nincs kategorizálva Eoslift
- nincs kategorizálva Bron-Coucke
- nincs kategorizálva Steelton
- nincs kategorizálva FeinTech
- nincs kategorizálva BioChef
- nincs kategorizálva Masterbuilt
- nincs kategorizálva Koolatron
- nincs kategorizálva Euro Cuisine
- nincs kategorizálva GFM
- nincs kategorizálva Tot Tutors
- nincs kategorizálva X4 Life
- nincs kategorizálva Tonar
- nincs kategorizálva Peterson
- nincs kategorizálva CFH
- nincs kategorizálva BOB Gear
- nincs kategorizálva Emeril Everyday
- nincs kategorizálva Könner & Söhnen
- nincs kategorizálva Rockboard
- nincs kategorizálva Goodis
- nincs kategorizálva Nivian
- nincs kategorizálva L.R.Baggs
- nincs kategorizálva Millennia
- nincs kategorizálva Vermona Modular
- nincs kategorizálva Adventure Kings
- nincs kategorizálva Drive Medical
- nincs kategorizálva Hitron
- nincs kategorizálva Bliss Hammocks
- nincs kategorizálva Singular Sound
- nincs kategorizálva Maneco Labs
- nincs kategorizálva BISWIND
- nincs kategorizálva ABE Arnhold
- nincs kategorizálva Mermade Hair
- nincs kategorizálva VCM
- nincs kategorizálva BodyCraft
- nincs kategorizálva Auer Signal
- nincs kategorizálva BrightSign
- nincs kategorizálva Mamas & Papas
- nincs kategorizálva Manduca
- nincs kategorizálva HELGI
- nincs kategorizálva Forge Adour
- nincs kategorizálva Eliminator Lighting
- nincs kategorizálva Darkglass
- nincs kategorizálva Blow
- nincs kategorizálva Paasche
- nincs kategorizálva Vistus
- nincs kategorizálva GMW
- nincs kategorizálva AER
- nincs kategorizálva Dynavox
- nincs kategorizálva Columbus
- nincs kategorizálva IWH
- nincs kategorizálva UGo
- nincs kategorizálva Code Mercenaries
- nincs kategorizálva Diamex
- nincs kategorizálva Sunset
- nincs kategorizálva Avital
- nincs kategorizálva Ondis24
- nincs kategorizálva D'Addario
- nincs kategorizálva BBE
- nincs kategorizálva Warwick
- nincs kategorizálva MyAVR
- nincs kategorizálva EBS
- nincs kategorizálva WEICON
- nincs kategorizálva Rotronic
- nincs kategorizálva Edsyn
- nincs kategorizálva Urban Glide
- nincs kategorizálva EISL
- nincs kategorizálva RCS
- nincs kategorizálva Nicai Systems
- nincs kategorizálva IDENTsmart
- nincs kategorizálva Sharper Image
- nincs kategorizálva Altrad
- nincs kategorizálva Revier Manager
- nincs kategorizálva Homak
- nincs kategorizálva Tycon Systems
- nincs kategorizálva Selve
- nincs kategorizálva Lumel
- nincs kategorizálva Paingone
- nincs kategorizálva Howard Leight
- nincs kategorizálva Plugwise
- nincs kategorizálva Martens
- nincs kategorizálva Desview
- nincs kategorizálva ActiveJet
- nincs kategorizálva Global Water
- nincs kategorizálva Allsee
- nincs kategorizálva Softing
- nincs kategorizálva Pulse ShowerSpas
- nincs kategorizálva Alogic
- nincs kategorizálva GFB
- nincs kategorizálva Sonicsmith
- nincs kategorizálva Toraiz
- nincs kategorizálva Ergodyne
- nincs kategorizálva Maturmeat
- nincs kategorizálva D-Jix
- nincs kategorizálva Orbsmart
- nincs kategorizálva Eowave
- nincs kategorizálva Imperia
- nincs kategorizálva Nature2
- nincs kategorizálva Baby Trend
- nincs kategorizálva AMERRY
- nincs kategorizálva Walther
- nincs kategorizálva ShelterLogic
- nincs kategorizálva Varad
- nincs kategorizálva Dr. Browns
- nincs kategorizálva KMA Machines
- nincs kategorizálva Klark Teknik
- nincs kategorizálva Elcom
- nincs kategorizálva Source Audio
- nincs kategorizálva AtomoSynth
- nincs kategorizálva Innr
- nincs kategorizálva Benidub
- nincs kategorizálva Protector
- nincs kategorizálva Winston
- nincs kategorizálva Solidsteel
- nincs kategorizálva Dracast
- nincs kategorizálva Dream
- nincs kategorizálva Malouf
- nincs kategorizálva Roba
- nincs kategorizálva Ravelli
- nincs kategorizálva Piet Boon
- nincs kategorizálva PureTools
- nincs kategorizálva JML
- nincs kategorizálva Reber
- nincs kategorizálva SiriusXM
- nincs kategorizálva Earthwise
- nincs kategorizálva DoubleSight
- nincs kategorizálva Raya
- nincs kategorizálva Artex
- nincs kategorizálva Bobrick
- nincs kategorizálva Verbos Electronics
- nincs kategorizálva Ark
- nincs kategorizálva DLO
- nincs kategorizálva ENS
- nincs kategorizálva Listen
- nincs kategorizálva Oscium
- nincs kategorizálva Benchmark USA
- nincs kategorizálva Python
- nincs kategorizálva Littelfuse
- nincs kategorizálva Game Factor
- nincs kategorizálva NComputing
- nincs kategorizálva Mode Machines
- nincs kategorizálva Legends
- nincs kategorizálva AS Synthesizers
- nincs kategorizálva Itechworld
- nincs kategorizálva Nexcom
- nincs kategorizálva SatKing
- nincs kategorizálva Fulltone
- nincs kategorizálva Advantix
- nincs kategorizálva Wampler
- nincs kategorizálva VAEMI
- nincs kategorizálva Aguilar
- nincs kategorizálva Narva
- nincs kategorizálva DOK
- nincs kategorizálva OzCharge
- nincs kategorizálva MIYO
- nincs kategorizálva Cioks
- nincs kategorizálva Neopower
- nincs kategorizálva AvMap
- nincs kategorizálva Arlec
- nincs kategorizálva Sanwa
- nincs kategorizálva REDARC
- nincs kategorizálva Guardian
- nincs kategorizálva Radio Flyer
- nincs kategorizálva Gaslock
- nincs kategorizálva Gaffgun
- nincs kategorizálva AquaMAX
- nincs kategorizálva DigitSole
- nincs kategorizálva Portsmith
- nincs kategorizálva Rome
- nincs kategorizálva DW
- nincs kategorizálva BEA
- nincs kategorizálva Disty
- nincs kategorizálva OXI Instruments
- nincs kategorizálva AvaTime
- nincs kategorizálva Xhose
- nincs kategorizálva MYVU
- nincs kategorizálva Kopykake
- nincs kategorizálva Konstant Lab
- nincs kategorizálva Turbo Scrub
- nincs kategorizálva Tenderfoot Electronics
- nincs kategorizálva Kask
- nincs kategorizálva Callpod
- nincs kategorizálva Dorman
- nincs kategorizálva 2box
- nincs kategorizálva Enlight
- nincs kategorizálva Franken
- nincs kategorizálva RUBI
- nincs kategorizálva Europa Leisure
- nincs kategorizálva GAMO
- nincs kategorizálva Musser
- nincs kategorizálva Edge Products
- nincs kategorizálva IClever
- nincs kategorizálva HN-Power
- nincs kategorizálva BIONIK
- nincs kategorizálva King Canopy
- nincs kategorizálva HeadRush
- nincs kategorizálva Flover
- nincs kategorizálva Milestone Systems
- nincs kategorizálva Micsig
- nincs kategorizálva Dodow
- nincs kategorizálva Spring
- nincs kategorizálva Red Panda
- nincs kategorizálva OJ ELECTRONICS
- nincs kategorizálva Aquasure
- nincs kategorizálva Banana Pi
- nincs kategorizálva Ilford
- nincs kategorizálva Crazy Tube Circuits
- nincs kategorizálva J.P. Instruments
- nincs kategorizálva GMB Gaming
- nincs kategorizálva Proclip
- nincs kategorizálva SainSmart
- nincs kategorizálva Kaona
- nincs kategorizálva Baja Mobility
- nincs kategorizálva DPW Design
- nincs kategorizálva SinuPulse
- nincs kategorizálva The T.bone
- nincs kategorizálva DIEZEL
- nincs kategorizálva VMB
- nincs kategorizálva Z.Vex
- nincs kategorizálva Seymour Duncan
- nincs kategorizálva BluGuitar
- nincs kategorizálva Lehle
- nincs kategorizálva Bricasti Design
- nincs kategorizálva T.akustik
- nincs kategorizálva Dwarf Connection
- nincs kategorizálva JL Cooper
- nincs kategorizálva StrikeMaster
- nincs kategorizálva ProUser
- nincs kategorizálva Bēm Wireless
- nincs kategorizálva Aqua-Vu
- nincs kategorizálva Millecroquettes
- nincs kategorizálva GR Bass
- nincs kategorizálva WilTec
- nincs kategorizálva Sure-Fi
- nincs kategorizálva Copernicus
- nincs kategorizálva Gumdrop
- nincs kategorizálva Tellur
- nincs kategorizálva Woox
- nincs kategorizálva Gallien-Krueger
- nincs kategorizálva Jetway
- nincs kategorizálva Texsport
- nincs kategorizálva SSV Works
- nincs kategorizálva Terre
- nincs kategorizálva Sanitec
- nincs kategorizálva Pangea Audio
- nincs kategorizálva Hogue
- nincs kategorizálva ATP
- nincs kategorizálva Pfannenberg
- nincs kategorizálva Scytek
- nincs kategorizálva MotorScrubber
- nincs kategorizálva Krone
- nincs kategorizálva Kraftmax
- nincs kategorizálva PCTV Systems
- nincs kategorizálva Cooper Lighting
- nincs kategorizálva Code Corporation
- nincs kategorizálva Now TV
- nincs kategorizálva Beautiful
- nincs kategorizálva Best Fitness
- nincs kategorizálva Voodoo Lab
- nincs kategorizálva Strymon
- nincs kategorizálva Insect Lore
- nincs kategorizálva Faytech
- nincs kategorizálva Chrome-Q
- nincs kategorizálva Kitronik
- nincs kategorizálva Trasman
- nincs kategorizálva Hamlet
- nincs kategorizálva SumUp
- nincs kategorizálva Microlab
- nincs kategorizálva Rotolight
- nincs kategorizálva Mr Gardener
- nincs kategorizálva Paladin
- nincs kategorizálva Lumu
- nincs kategorizálva WAYDOO
- nincs kategorizálva Fimer
- nincs kategorizálva ASIWO
- nincs kategorizálva Vankyo
- nincs kategorizálva OWC
- nincs kategorizálva Lexar
- nincs kategorizálva Vent-Axia
- nincs kategorizálva Firefield
- nincs kategorizálva E-Power
- nincs kategorizálva RectorSeal
- nincs kategorizálva Red Digital Cinema
- nincs kategorizálva Kaiser Nienhaus
- nincs kategorizálva Freeplay
- nincs kategorizálva Roller Grill
- nincs kategorizálva Zaor
- nincs kategorizálva Glorious
- nincs kategorizálva AVTech
- nincs kategorizálva Dataflex
- nincs kategorizálva Bugera
- nincs kategorizálva Handy Lux
- nincs kategorizálva Rossum Electro-Music
- nincs kategorizálva Panta
- nincs kategorizálva Pentel
- nincs kategorizálva Wallas
- nincs kategorizálva Gima
- nincs kategorizálva MagnaPool
- nincs kategorizálva Aquadon
- nincs kategorizálva Raidsonic
- nincs kategorizálva Approx
- nincs kategorizálva Gamesir
- nincs kategorizálva Neunaber
- nincs kategorizálva Leotec
- nincs kategorizálva VOREL
- nincs kategorizálva Ciarra
- nincs kategorizálva Ocean Way Audio
- nincs kategorizálva DayStar Filters
- nincs kategorizálva Flexispot
- nincs kategorizálva OP/TECH
- nincs kategorizálva ETC
- nincs kategorizálva Nuki
- nincs kategorizálva EOTech
- nincs kategorizálva Cinderella
- nincs kategorizálva Bauhn
- nincs kategorizálva Aspen
- nincs kategorizálva Cottons
- nincs kategorizálva TVLogic
- nincs kategorizálva CAD Audio
- nincs kategorizálva Frequency Central
- nincs kategorizálva Sacrament
- nincs kategorizálva The Box
- nincs kategorizálva AudioThing
- nincs kategorizálva Feelworld
- nincs kategorizálva SoundPEATS
- nincs kategorizálva Cambium Networks
- nincs kategorizálva Trident
- nincs kategorizálva Schoeps
- nincs kategorizálva HPI Racing
- nincs kategorizálva Trijicon
- nincs kategorizálva Favini
- nincs kategorizálva Dnipro
- nincs kategorizálva IFootage
- nincs kategorizálva Sonuus
- nincs kategorizálva Cabasse
- nincs kategorizálva Jonsered
- nincs kategorizálva Saint Algue
- nincs kategorizálva Cactus
- nincs kategorizálva Oecolux
- nincs kategorizálva SoundLAB
- nincs kategorizálva ACL
- nincs kategorizálva Mars Gaming
- nincs kategorizálva Radiant
- nincs kategorizálva G.Skill
- nincs kategorizálva Edbak
- nincs kategorizálva Integral LED
- nincs kategorizálva Integral
- nincs kategorizálva Roline
- nincs kategorizálva Virax
- nincs kategorizálva MSW
- nincs kategorizálva Amaran
- nincs kategorizálva Gill
- nincs kategorizálva AMC
- nincs kategorizálva Triangle
- nincs kategorizálva Tumbleweed
- nincs kategorizálva Alutruss
- nincs kategorizálva Sunpentown
- nincs kategorizálva Hamstra
- nincs kategorizálva PVI
- nincs kategorizálva Grendel
- nincs kategorizálva Coravin
- nincs kategorizálva O&O Software
- nincs kategorizálva Wasp
- nincs kategorizálva Chef's Choice
- nincs kategorizálva Ciclo
- nincs kategorizálva Warmup
- nincs kategorizálva Brastemp
- nincs kategorizálva Wavtech
- nincs kategorizálva Satco
- nincs kategorizálva AMT
- nincs kategorizálva Royal Catering
- nincs kategorizálva Artrom
- nincs kategorizálva Lowell
- nincs kategorizálva Adonit
- nincs kategorizálva Point Source Audio
- nincs kategorizálva ANDYCINE
- nincs kategorizálva AmpliVox
- nincs kategorizálva Pippi
- nincs kategorizálva Casalux
- nincs kategorizálva CyberData Systems
- nincs kategorizálva Omnitron Systems
- nincs kategorizálva Stewart Systems
- nincs kategorizálva Qubino
- nincs kategorizálva Eurosound
- nincs kategorizálva WyreStorm
- nincs kategorizálva Williams Sound
- nincs kategorizálva Magewell
- nincs kategorizálva Globalo
- nincs kategorizálva Adam Hall
- nincs kategorizálva SoundTube
- nincs kategorizálva Therabody
- nincs kategorizálva Infortrend
- nincs kategorizálva STI
- nincs kategorizálva Rug Doctor
- nincs kategorizálva Mad Dog
- nincs kategorizálva Raspberry Pi
- nincs kategorizálva Bals
- nincs kategorizálva Balt
- nincs kategorizálva AJ.BA
- nincs kategorizálva ESKA
- nincs kategorizálva Lascar Electronics
- nincs kategorizálva EWON
- nincs kategorizálva Sport-Tronic
- nincs kategorizálva Alga
- nincs kategorizálva WesAudio
- nincs kategorizálva Hamron
- nincs kategorizálva Robust
- nincs kategorizálva Heritage Audio
- nincs kategorizálva Quik Lok
- nincs kategorizálva Tsakalis AudioWorks
- nincs kategorizálva MagTek
- nincs kategorizálva Jupiter
- nincs kategorizálva Sony Optiarc
- nincs kategorizálva Colortone
- nincs kategorizálva Lowel
- nincs kategorizálva Anybus
- nincs kategorizálva Super Rod
- nincs kategorizálva Carnielli
- nincs kategorizálva Luminex
- nincs kategorizálva HiLook
- nincs kategorizálva P3 International
- nincs kategorizálva Idec
- nincs kategorizálva Beckmann & Egle
- nincs kategorizálva Seek Thermal
- nincs kategorizálva VintageView
- nincs kategorizálva Alfresco
- nincs kategorizálva Bintec-elmeg
- nincs kategorizálva Crane Song
- nincs kategorizálva W'eau
- nincs kategorizálva Ixxat
- nincs kategorizálva Belena
- nincs kategorizálva Fanox
- nincs kategorizálva Crouzet
- nincs kategorizálva Megarevo
- nincs kategorizálva Tech 21
- nincs kategorizálva Petmate
- nincs kategorizálva BlendMount
- nincs kategorizálva Perlick
- nincs kategorizálva Sedona
- nincs kategorizálva Tecnoinox
- nincs kategorizálva CaterRacks
- nincs kategorizálva Besco
- nincs kategorizálva Prologue
- nincs kategorizálva Atosa
- nincs kategorizálva Nanoleaf
- nincs kategorizálva Mach Power
- nincs kategorizálva Soltection
- nincs kategorizálva Kool-It
- nincs kategorizálva Cool Head
- nincs kategorizálva KeepOut
- nincs kategorizálva LawnMaster
- nincs kategorizálva Deltronic
- nincs kategorizálva Eligent
- nincs kategorizálva Meris
- nincs kategorizálva Procare
- nincs kategorizálva AmerBox
- nincs kategorizálva Qu-Bit
- nincs kategorizálva Blue Lantern
- nincs kategorizálva CTA Digital
- nincs kategorizálva DivKid
- nincs kategorizálva Uniross
- nincs kategorizálva Panamax
- nincs kategorizálva FaseLunare
- nincs kategorizálva Götze & Jensen
- nincs kategorizálva (Recovery)
- nincs kategorizálva Twinkly
- nincs kategorizálva Acefast
- nincs kategorizálva Squarp Instruments
- nincs kategorizálva EtherWAN
- nincs kategorizálva Econ Connect
- nincs kategorizálva META
- nincs kategorizálva Shimbol
- nincs kategorizálva GC Audio
- nincs kategorizálva Einhell Bavaria
- nincs kategorizálva Motrona
- nincs kategorizálva Thalheimer
- nincs kategorizálva FeiYu-Tech
- nincs kategorizálva Aida
- nincs kategorizálva Apantac
- nincs kategorizálva VisionTek
- nincs kategorizálva Accsoon
- nincs kategorizálva Rothenberger
- nincs kategorizálva FeiyuTech
- nincs kategorizálva Losi
- nincs kategorizálva Bessey
- nincs kategorizálva A3
- nincs kategorizálva Serge
- nincs kategorizálva Gladiator
- nincs kategorizálva Mobli
- nincs kategorizálva Sonoff
- nincs kategorizálva G-Technology
- nincs kategorizálva Caroma
- nincs kategorizálva Sungale
- nincs kategorizálva Befaco
- nincs kategorizálva Waltec
- nincs kategorizálva Eartec
- nincs kategorizálva Portkeys
- nincs kategorizálva Westcott
- nincs kategorizálva EXSYS
- nincs kategorizálva Digiquest
- nincs kategorizálva Gewiss
- nincs kategorizálva Hagor
- nincs kategorizálva Glyph
- nincs kategorizálva Seco-Larm
- nincs kategorizálva Murr Elektronik
- nincs kategorizálva Massoth
- nincs kategorizálva Envitec
- nincs kategorizálva Mimo Monitors
- nincs kategorizálva Alula
- nincs kategorizálva Blebox
- nincs kategorizálva VS Sassoon
- nincs kategorizálva Redsbaby
- nincs kategorizálva Bright Spark
- nincs kategorizálva Algo
- nincs kategorizálva Peloton
- nincs kategorizálva Gentrax
- nincs kategorizálva Brocade
- nincs kategorizálva ICC
- nincs kategorizálva Insteon
- nincs kategorizálva Amer
- nincs kategorizálva Warner Bros
- nincs kategorizálva Vinotemp
- nincs kategorizálva Silent Knight
- nincs kategorizálva Mosconi
- nincs kategorizálva Ditek
- nincs kategorizálva Kingston Technology
- nincs kategorizálva Axxess
- nincs kategorizálva Wilson
- nincs kategorizálva Goki
- nincs kategorizálva CGV
- nincs kategorizálva My Arcade
- nincs kategorizálva Enttec
- nincs kategorizálva Tescoma
- nincs kategorizálva RF Elements
- nincs kategorizálva ALC
- nincs kategorizálva Holland Electronics
- nincs kategorizálva Arista
- nincs kategorizálva Chenbro Micom
- nincs kategorizálva Triumph Sports
- nincs kategorizálva Gasmate
- nincs kategorizálva Novo Nordisk
- nincs kategorizálva Ionmax
- nincs kategorizálva Seville Classics
- nincs kategorizálva TechLogix Networx
- nincs kategorizálva NuTone
- nincs kategorizálva Thermalright
- nincs kategorizálva Meross
- nincs kategorizálva Bxterra
- nincs kategorizálva Renogy
- nincs kategorizálva Babylonia
- nincs kategorizálva HeartSine
- nincs kategorizálva Bullet
- nincs kategorizálva Morrison
- nincs kategorizálva Ordo
- nincs kategorizálva Alphacool
- nincs kategorizálva Asetek
- nincs kategorizálva AZZA
- nincs kategorizálva Audibax
- nincs kategorizálva TechN
- nincs kategorizálva Eversolo
- nincs kategorizálva Davita
- nincs kategorizálva Giga Copper
- nincs kategorizálva Elsner
- nincs kategorizálva Séura
- nincs kategorizálva Cube Controls
- nincs kategorizálva Meridian
- nincs kategorizálva Donexon
- nincs kategorizálva Eve Audio
- nincs kategorizálva Axagon
- nincs kategorizálva Linq
- nincs kategorizálva Wortmann AG
- nincs kategorizálva DiGiGrid
- nincs kategorizálva Sanofi
- nincs kategorizálva Mitzu
- nincs kategorizálva Avteq
- nincs kategorizálva Seaward
- nincs kategorizálva Omega Altise
- nincs kategorizálva Fizzics
- nincs kategorizálva XFX
- nincs kategorizálva Leynew
- nincs kategorizálva Lauten Audio
- nincs kategorizálva Cropico
- nincs kategorizálva Sunwoda
- nincs kategorizálva Schleich
- nincs kategorizálva Unitech
- nincs kategorizálva FXLab
- nincs kategorizálva Middle Atlantic
- nincs kategorizálva Kincrome
- nincs kategorizálva BC Acoustique
- nincs kategorizálva Brockhaus HEUER
- nincs kategorizálva Reishunger
- nincs kategorizálva Ergotec
- nincs kategorizálva Dupla
- nincs kategorizálva APSystems
- nincs kategorizálva IODD
- nincs kategorizálva BYD
- nincs kategorizálva Tektronix
- nincs kategorizálva Aqua Medic
- nincs kategorizálva Gold Note
- nincs kategorizálva Oromed
- nincs kategorizálva Pylontech
- nincs kategorizálva Fire Sense
- nincs kategorizálva Grüniq
- nincs kategorizálva Goodwe
- nincs kategorizálva Moki
- nincs kategorizálva Enertex
- nincs kategorizálva IOTAVX
- nincs kategorizálva Ovation
- nincs kategorizálva InAlto
- nincs kategorizálva Enviroswim
- nincs kategorizálva Dobar
- nincs kategorizálva Vevor
- nincs kategorizálva Ovente
- nincs kategorizálva PowerColor
- nincs kategorizálva ISpring
- nincs kategorizálva WeFix
- nincs kategorizálva BCA
- nincs kategorizálva Saki
- nincs kategorizálva Smart365
- nincs kategorizálva Fosi Audio
- nincs kategorizálva ChargeHub
- nincs kategorizálva Eldat
- nincs kategorizálva NEP
- nincs kategorizálva SoundSwitch
- nincs kategorizálva Sera
- nincs kategorizálva Dostmann Electronic
- nincs kategorizálva JBC
- nincs kategorizálva DV Mark
- nincs kategorizálva MOON
- nincs kategorizálva Cuggl
- nincs kategorizálva HABAU
- nincs kategorizálva CVW
- nincs kategorizálva Earbreeze
- nincs kategorizálva Möhlenhoff
- nincs kategorizálva Taqua
- nincs kategorizálva Brainstorm
- nincs kategorizálva Colonial Elegance
- nincs kategorizálva Overtone Labs
- nincs kategorizálva IBEAM
- nincs kategorizálva Bühnen
- nincs kategorizálva Blukac
- nincs kategorizálva BendixKing
- nincs kategorizálva Tube-Tech
- nincs kategorizálva TCW Technologies
- nincs kategorizálva UNITEK
- nincs kategorizálva CoolerMaster
- nincs kategorizálva Rexing
- nincs kategorizálva The T.mix
- nincs kategorizálva Regula-Werk King
- nincs kategorizálva Inter-M
- nincs kategorizálva MIDI Solutions
- nincs kategorizálva Positive Grid
- nincs kategorizálva Amgrow
- nincs kategorizálva Xaphoon
- nincs kategorizálva Winchester
- nincs kategorizálva Lampa
- nincs kategorizálva Sinus Live
- nincs kategorizálva Sureguard
- nincs kategorizálva QuickCool
- nincs kategorizálva Smit Visual
- nincs kategorizálva NZR
- nincs kategorizálva Toparc
- nincs kategorizálva Oro-Med
- nincs kategorizálva Hex
- nincs kategorizálva Baby Cakes
- nincs kategorizálva Deflecto
- nincs kategorizálva ELMEKO
- nincs kategorizálva Tesseract Modular
- nincs kategorizálva Sport Dog
- nincs kategorizálva Nowsonic
- nincs kategorizálva Hubble Connected
- nincs kategorizálva ELTA Music
- nincs kategorizálva Dragonshock
- nincs kategorizálva We-Vibe
- nincs kategorizálva Budda
- nincs kategorizálva Electronics International
- nincs kategorizálva Lamar
- nincs kategorizálva Atlantis Land
- nincs kategorizálva White Lightning
- nincs kategorizálva GEV
- nincs kategorizálva Frient
- nincs kategorizálva Kaiser Fototechnik
- nincs kategorizálva Vishay
- nincs kategorizálva Rooboost
- nincs kategorizálva Bitspower
- nincs kategorizálva EAT
- nincs kategorizálva Comar
- nincs kategorizálva Freedor
- nincs kategorizálva Start International
- nincs kategorizálva C2G
- nincs kategorizálva AXITEC
- nincs kategorizálva Lingg & Janke
- nincs kategorizálva Auralex
- nincs kategorizálva Pieps
- nincs kategorizálva Innovative
- nincs kategorizálva Lynx Technik
- nincs kategorizálva Yuede
- nincs kategorizálva ClimeMET
- nincs kategorizálva Pliant Technologies
- nincs kategorizálva Prompter People
- nincs kategorizálva Astropet
- nincs kategorizálva Canopia
- nincs kategorizálva Wabeco
- nincs kategorizálva Swingline GBC
- nincs kategorizálva Spelsberg
- nincs kategorizálva Staudte-Hirsch
- nincs kategorizálva Universal Remote Control
- nincs kategorizálva Soundsphere
- nincs kategorizálva Aqua Computer
- nincs kategorizálva HEDD
- nincs kategorizálva Vinpower Digital
- nincs kategorizálva Magivaac
- nincs kategorizálva Lindemann
- nincs kategorizálva Silent Angel
- nincs kategorizálva IOptron
- nincs kategorizálva ZWO
- nincs kategorizálva Bbf
- nincs kategorizálva Club 3D
- nincs kategorizálva Sprolink
- nincs kategorizálva Thermionic Culture
- nincs kategorizálva Watercool
- nincs kategorizálva Moultrie
- nincs kategorizálva Skaarhoj
- nincs kategorizálva Whitestone
- nincs kategorizálva BMB
- nincs kategorizálva Advance
- nincs kategorizálva Arylic
- nincs kategorizálva Cloud
- nincs kategorizálva Sandia Aerospace
- nincs kategorizálva EK Water Blocks
- nincs kategorizálva Lamptron
- nincs kategorizálva PS Audio
- nincs kategorizálva Gudsen
- nincs kategorizálva Zendure
- nincs kategorizálva Envertech
- nincs kategorizálva Prism Sound
- nincs kategorizálva ID-Tech
- nincs kategorizálva FSP/Fortron
- nincs kategorizálva Meopta
- nincs kategorizálva MARTOR
- nincs kategorizálva Lumantek
- nincs kategorizálva SEADA
- nincs kategorizálva Honey-Can-Do
- nincs kategorizálva Promise Technology
- nincs kategorizálva Deity
- nincs kategorizálva Patriot
- nincs kategorizálva Taga Harmony
- nincs kategorizálva B.E.G.
- nincs kategorizálva Fixpoint
- nincs kategorizálva Enerdrive
- nincs kategorizálva Respironics
- nincs kategorizálva ChamSys
- nincs kategorizálva TESLA Electronics
- nincs kategorizálva Intesis
- nincs kategorizálva Nethix
- nincs kategorizálva Pluto
- nincs kategorizálva Laine
- nincs kategorizálva 3Doodler
- nincs kategorizálva Soundskins
- nincs kategorizálva Middle Atlantic Products
- nincs kategorizálva Loctite
- nincs kategorizálva Antelope
- nincs kategorizálva Astera
- nincs kategorizálva Sabco
- nincs kategorizálva Sensative
- nincs kategorizálva Plasma Cloud
- nincs kategorizálva Flo
- nincs kategorizálva Jungle Gym
- nincs kategorizálva Smart Media
- nincs kategorizálva Code
- nincs kategorizálva Mivar
- nincs kategorizálva SolaX Power
- nincs kategorizálva AURALiC
- nincs kategorizálva AkYtec
- nincs kategorizálva Bestgreen
- nincs kategorizálva MyPOS
- nincs kategorizálva Truetone
- nincs kategorizálva Starlink
- nincs kategorizálva Favero
- nincs kategorizálva Durvet
- nincs kategorizálva KNEKT
- nincs kategorizálva Gator Frameworks
- nincs kategorizálva Teia
- nincs kategorizálva The Joy Factory
- nincs kategorizálva Yuer
- nincs kategorizálva OLLO
- nincs kategorizálva Axor
- nincs kategorizálva MEPROLIGHT
- nincs kategorizálva Tactical Fiber Systems
- nincs kategorizálva GVision
- nincs kategorizálva Veber
- nincs kategorizálva SMS
- nincs kategorizálva Richgro
- nincs kategorizálva Varaluz
- nincs kategorizálva MIOPS
- nincs kategorizálva Enbrighten
- nincs kategorizálva Vicoustic
- nincs kategorizálva Albert Heijn
- nincs kategorizálva Yphix
- nincs kategorizálva Magliner
- nincs kategorizálva Magmatic
- nincs kategorizálva Comfortisse
- nincs kategorizálva Videotel Digital
- nincs kategorizálva Zylight
- nincs kategorizálva Smith-Victor
- nincs kategorizálva HuddleCamHD
- nincs kategorizálva MooreCo
- nincs kategorizálva BIOS Living
- nincs kategorizálva Connection
- nincs kategorizálva Blind Spot
- nincs kategorizálva Badiona
- nincs kategorizálva VMV
- nincs kategorizálva Digigram
- nincs kategorizálva Mutec
- nincs kategorizálva Black Hydra
- nincs kategorizálva Expressive E
- nincs kategorizálva Merging
- nincs kategorizálva Bellari
- nincs kategorizálva Altman
- nincs kategorizálva EXO
- nincs kategorizálva Hawke
- nincs kategorizálva Defender
- nincs kategorizálva Betty Bossi
- nincs kategorizálva FoxFury
- nincs kategorizálva Eller
- nincs kategorizálva Rotatrim
- nincs kategorizálva Peak Design
- nincs kategorizálva Uniropa
- nincs kategorizálva Eura
- nincs kategorizálva ESE
- nincs kategorizálva Claypaky
- nincs kategorizálva Hecate
- nincs kategorizálva Jinbei
- nincs kategorizálva Nearity
- nincs kategorizálva Gra-Vue
- nincs kategorizálva On-Stage
- nincs kategorizálva Inverx
- nincs kategorizálva Titanwolf
- nincs kategorizálva Uplink
- nincs kategorizálva Mybeo
- nincs kategorizálva Medicinalis
- nincs kategorizálva Bearware
- nincs kategorizálva Liam&Daan
- nincs kategorizálva Traco Power
- nincs kategorizálva CAME-TV
- nincs kategorizálva Nureva
- nincs kategorizálva Revic
- nincs kategorizálva Galcon
- nincs kategorizálva Creamsource
- nincs kategorizálva Telmax
- nincs kategorizálva Apollo Design
- nincs kategorizálva JoeCo
- nincs kategorizálva Holosun
- nincs kategorizálva Aconatic
- nincs kategorizálva Kluge
- nincs kategorizálva Arovec
- nincs kategorizálva SecureSafe
- nincs kategorizálva CubuSynth
- nincs kategorizálva Exelpet
- nincs kategorizálva Aplic
- nincs kategorizálva Imarflex
- nincs kategorizálva Tempmate
- nincs kategorizálva Stalco
- nincs kategorizálva Carlsbro
- nincs kategorizálva Ventev
- nincs kategorizálva Mobotix
- nincs kategorizálva Steelbody
- nincs kategorizálva PureLink
- nincs kategorizálva UNYKAch
- nincs kategorizálva VAVA
- nincs kategorizálva Mammut
- nincs kategorizálva Modbap Modular
- nincs kategorizálva Bluestork
- nincs kategorizálva INOGENI
- nincs kategorizálva Linhof
- nincs kategorizálva Carry-on
- nincs kategorizálva AddLiving
- nincs kategorizálva IOIO
- nincs kategorizálva Beghelli
- nincs kategorizálva Nimbus
- nincs kategorizálva Coca-Cola
- nincs kategorizálva City Theatrical
- nincs kategorizálva Acros
- nincs kategorizálva Redback Technologies
- nincs kategorizálva Vent-A-Hood
- nincs kategorizálva GoXtreme
- nincs kategorizálva Bome
- nincs kategorizálva One Control
- nincs kategorizálva EQ Acoustics
- nincs kategorizálva AV Tool
- nincs kategorizálva Aquael
- nincs kategorizálva NEXTO DI
- nincs kategorizálva Thermarest
- nincs kategorizálva Fortinge
- nincs kategorizálva RF-Links
- nincs kategorizálva LiveU
- nincs kategorizálva Austral
- nincs kategorizálva HMD
- nincs kategorizálva Luxul
- nincs kategorizálva Cherub
- nincs kategorizálva ProLights
- nincs kategorizálva Xinfrared
- nincs kategorizálva Brizo
- nincs kategorizálva I-PRO
- nincs kategorizálva Europalms
- nincs kategorizálva DuroStar
- nincs kategorizálva Waterstone
- nincs kategorizálva Huslog
- nincs kategorizálva Mr Steam
- nincs kategorizálva DVDO
- nincs kategorizálva A-Designs
- nincs kategorizálva Henry Engineering
- nincs kategorizálva Primacoustic
- nincs kategorizálva HomeCraft
- nincs kategorizálva Heusinkveld
- nincs kategorizálva EnOcean
- nincs kategorizálva Storcube
- nincs kategorizálva Varia
- nincs kategorizálva Gurari
- nincs kategorizálva Fezz
- nincs kategorizálva ASI
- nincs kategorizálva Lexivon
- nincs kategorizálva Graff
- nincs kategorizálva Swiss Eye
- nincs kategorizálva Cane Creek
- nincs kategorizálva EPEVER
- nincs kategorizálva KED
- nincs kategorizálva Caberg
- nincs kategorizálva Exped
- nincs kategorizálva Lawn Star
- nincs kategorizálva Edouard Rousseau
- nincs kategorizálva GameDay
- nincs kategorizálva Sparkle
- nincs kategorizálva Söll
- nincs kategorizálva X-Lite
- nincs kategorizálva AXESS
- nincs kategorizálva Glemm
- nincs kategorizálva Ridem
- nincs kategorizálva StarIink
- nincs kategorizálva Noyafa
- nincs kategorizálva Envertec
- nincs kategorizálva Nordic Winter
- nincs kategorizálva Sensei
- nincs kategorizálva Volcano
- nincs kategorizálva XS Power
- nincs kategorizálva Wire Technologies
- nincs kategorizálva Taco Tuesday
- nincs kategorizálva CEEM
- nincs kategorizálva IMM Photonics
- nincs kategorizálva Field Optics
- nincs kategorizálva Robern
- nincs kategorizálva Signature Hardware
- nincs kategorizálva GRAUGEAR
- nincs kategorizálva Sure Petcare
- nincs kategorizálva Sortimo
- nincs kategorizálva Livall
- nincs kategorizálva Beaphar
- nincs kategorizálva Catit
- nincs kategorizálva WarmlyYours
- nincs kategorizálva Mebby
- nincs kategorizálva TONI&GUY
- nincs kategorizálva Balam Rush
- nincs kategorizálva Roesle
- nincs kategorizálva Oreg
- nincs kategorizálva Karran
- nincs kategorizálva Topex
- nincs kategorizálva OOONO
- nincs kategorizálva CaviLock
- nincs kategorizálva Origin Storage
- nincs kategorizálva Kostal
- nincs kategorizálva Stamos
- nincs kategorizálva Ulsonix
- nincs kategorizálva Stamony
- nincs kategorizálva Uniprodo
- nincs kategorizálva STANDARD
- nincs kategorizálva BigBlue
- nincs kategorizálva RC Allen
- nincs kategorizálva Plastkon
- nincs kategorizálva Triplett
- nincs kategorizálva Wiesenfield
- nincs kategorizálva Tele Vue
- nincs kategorizálva Bulgin
- nincs kategorizálva Pure 100
- nincs kategorizálva Petite Chérie
- nincs kategorizálva Njoy
- nincs kategorizálva Studio Titan
- nincs kategorizálva AstrHori
- nincs kategorizálva Icron
- nincs kategorizálva Pyrex
- nincs kategorizálva Platypus
- nincs kategorizálva Trezor
- nincs kategorizálva Yamazen
- nincs kategorizálva Ferrofish
- nincs kategorizálva HPRC
- nincs kategorizálva Really Right Stuff
- nincs kategorizálva Decimator
- nincs kategorizálva Chimera
- nincs kategorizálva ButtKicker
- nincs kategorizálva Blonder Tongue
- nincs kategorizálva Crystal Video
- nincs kategorizálva Tilta
- nincs kategorizálva Luxli
- nincs kategorizálva PAG
- nincs kategorizálva NeoMounts
- nincs kategorizálva Western Co.
- nincs kategorizálva ProFlo
- nincs kategorizálva Ruggard
- nincs kategorizálva DiversiTech
- nincs kategorizálva Violectric
- nincs kategorizálva Aalberg Audio
- nincs kategorizálva Evooch
- nincs kategorizálva Bolin Technology
- nincs kategorizálva Total Chef
- nincs kategorizálva Total
- nincs kategorizálva PoLabs
- nincs kategorizálva Taiji
- nincs kategorizálva Digi-Pas
- nincs kategorizálva Pfister
- nincs kategorizálva Fellow
- nincs kategorizálva Kolcraft
- nincs kategorizálva Klauke
- nincs kategorizálva Axler
- nincs kategorizálva Symmons
- nincs kategorizálva Gerber
- nincs kategorizálva Royale
- nincs kategorizálva Venicci
- nincs kategorizálva Das Keyboard
- nincs kategorizálva Schaffner
- nincs kategorizálva Vitec
- nincs kategorizálva Nicols
- nincs kategorizálva Physa
- nincs kategorizálva ARNOLD Lichttechnik
- nincs kategorizálva Matterport
- nincs kategorizálva API Audio
- nincs kategorizálva Moomin
- nincs kategorizálva Belulu
- nincs kategorizálva Jedo
- nincs kategorizálva RIX
- nincs kategorizálva Bayco
- nincs kategorizálva Dinstar
- nincs kategorizálva Noordi
- nincs kategorizálva Corona
- nincs kategorizálva Coors Light
- nincs kategorizálva Arco
- nincs kategorizálva KoolScapes
- nincs kategorizálva Netter Vibration
- nincs kategorizálva Califone
- nincs kategorizálva Dynon Avionics
- nincs kategorizálva Uvex
- nincs kategorizálva UAvionix
- nincs kategorizálva LARQ
- nincs kategorizálva ORCA
- nincs kategorizálva YA-MAN
- nincs kategorizálva CRAFT + MAIN
- nincs kategorizálva V-Tone
- nincs kategorizálva Hellberg
- nincs kategorizálva Stelzner
- nincs kategorizálva LightKeeper Pro
- nincs kategorizálva BMAX
- nincs kategorizálva Cressi
- nincs kategorizálva Singercon
- nincs kategorizálva Pivo
- nincs kategorizálva Sharkbite
- nincs kategorizálva CatSynth
- nincs kategorizálva Lantus
- nincs kategorizálva Pitsos
- nincs kategorizálva Lively
- nincs kategorizálva Ember
- nincs kategorizálva Sifflus
- nincs kategorizálva ACOPower
- nincs kategorizálva Advanced Network Devices
- nincs kategorizálva Nextorage
- nincs kategorizálva XTRARM
- nincs kategorizálva SolidDrive
- nincs kategorizálva Mac Tools
- nincs kategorizálva Phase Technology
- nincs kategorizálva Beltronics
- nincs kategorizálva Lahti Pro
- nincs kategorizálva Jan Nowak
- nincs kategorizálva HiRO
- nincs kategorizálva Vantrue
- nincs kategorizálva Elight
- nincs kategorizálva Forodi
- nincs kategorizálva CELLFAST
- nincs kategorizálva MOZOS
- nincs kategorizálva Buxton
- nincs kategorizálva ViewZ
- nincs kategorizálva IsoTek
- nincs kategorizálva Miracle Smile
- nincs kategorizálva Zacuto
- nincs kategorizálva VARI-LITE
- nincs kategorizálva Real Cable
- nincs kategorizálva Pengo
- nincs kategorizálva Sophos
- nincs kategorizálva Kica
- nincs kategorizálva Racktime
- nincs kategorizálva Kendall Howard
- nincs kategorizálva Starlight Xpress
- nincs kategorizálva Sightron
- nincs kategorizálva Simmons
- nincs kategorizálva Infosec
- nincs kategorizálva Leba
Legújabb útmutatók nincs kategorizálva

3 Április 2025

3 Április 2025

3 Április 2025

3 Április 2025

3 Április 2025

3 Április 2025

3 Április 2025

3 Április 2025

3 Április 2025

3 Április 2025